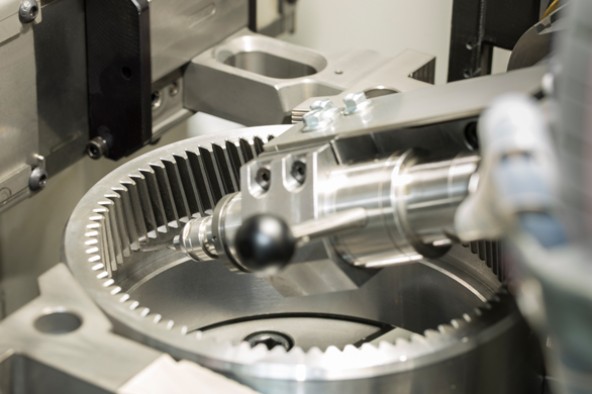
Highlights
- Compact footprint
- Short machining times
- Integrated workpiece automation
- High-performance spindle with internal cooling lubricant return
- Fast tool change
Options
- Tool changer
- For roughing and finishing tools
- For additional functions such as turning, drilling, milling and measuring
- Chamfering during the machining process
- Drawing-compliant chamfer geometries possible
- Maximum reproductive accuracy and precision