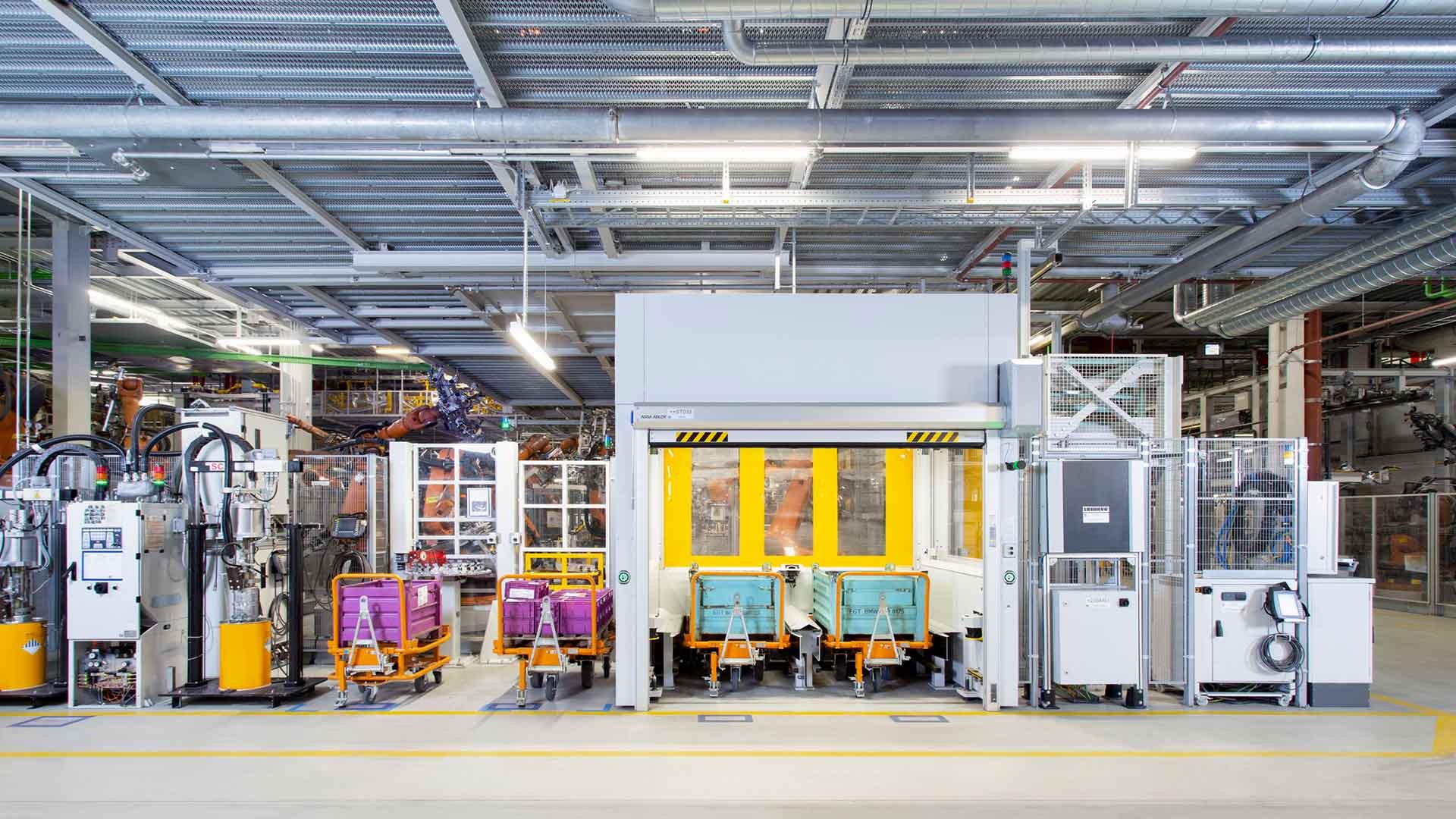
„Griff in die Kiste“ für Zuführung von Karosseriebauteilen
Für den Linieneingang einer Karosseriebauanlage im Dingolfinger Werk der BMW Group lieferte die Liebherr-Verzahntechnik GmbH eine komplette Roboterzelle für die automatisierte, flexible Teilezuführung als Bin Picking-Lösung. Die Aufgabe des Roboters ist es, die Karosseriebauteile zu greifen und sie der Punktschweißanlage zuzuführen – inklusive Doppelbauteil-Erkennung und hochpräziser Zwischenablage in einem Klinkenspeicher.
Das BMW Group Werk in Dingolfing ist einer von 31 Produktionsstandorten der BMW Group weltweit und die größte europäische Fertigungsstätte des Konzerns. Rund 18.000 Mitarbeitende sorgen dafür, dass im Werk täglich rund 1.500 Automobile vom Band laufen. Eines der Modelle ist das Cabrio der 4er-Baureihe, für dessen Fertigung die BMW Group 2020 eine neue Karosseriebauanlage installierte.
Komplettpaket für den Linieneingang
Die Teilezuführung für die Fertigungslinie, in der Seitenrahmenbleche zur Verstärkung der B-Säule verschweißt werden, sollte mit einer Bin Picking-Lösung flexibel automatisiert werden. Dabei konnte die Liebherr-Verzahntechnik GmbH mit einer Komplettlösung für einen kollisionsfreien Griff in die Kiste zur Entnahme der dünnwandigen Bauteile punkten: Die Roboterzelle am Linieneingang beinhaltet das Zuführmodul mit zwei Schnelllauftoren, einen Greifroboter mit Dreipunkt-Sauggreifer, einen Klinkenspeicher für die Zwischenablage, die bedienungsfreundliche Liebherr-Software LHRobotics.Vision sowie Kamerasysteme für die Positionskontrolle der Bauteile und die Doppelbauteil-Erkennung.
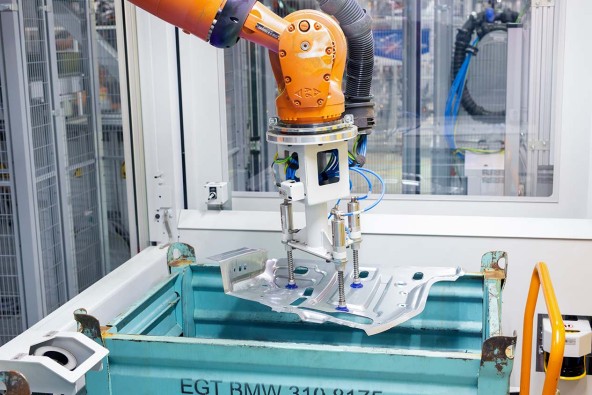
Kollisionsfreie Entnahme der Bleche mit Sauggreifer
Herausforderungen bei der Auslegung
Der automatisierte Linieneingang ist seit 2020 in Betrieb. Der gesamte Fertigungsbereich für das 4er-Cabrio wurde von der BMW Group neu aufgebaut und sollte voll automatisiert und zuverlässig laufen. Dabei waren die Anforderungen genau definiert: Die Teilezuführung musste über einen sogenannten Routenzug erfolgen, ein Flurförderfahrzeug, das die Bauteile anliefert. Aufgabe der Software war es, bei der Logistik rechtzeitig neue Bauteile anzufordern, um den ungehinderten Ablauf der Produktion sicherzustellen.
Das Layout sollte kompakt sein und auf relativ engem Raum sowie innerhalb eines kleinen Zeitfensters realisiert werden. Kundenvorschriften wie die Schnittstelle zum Fertigungsleitsystem der BMW Group mussten beachtet werden. Weitere Herausforderungen waren die kollisionsfreie Entnahme der dünnwandigen Karosseriebauteile aus der Kiste, sowie die Erkennung eines zusätzlich entnommenen Bauteils (des sogenannten „blinden Passagiers“) und die Integration eines Klinkenspeichers als Zwischenpuffer für das taktzeitparallele Beladen neuer Kisten.
Alles aus einer Hand
Ausschlaggebend für die Auftragserteilung war die Tatsache, dass Liebherr mit industriellem Anwendungs-Know-how und Softwarekompetenz den gesamten Anlagenaufbau aus einer Hand anbieten und realisieren konnte – von der Erstauslegung über die Konstruktion bis hin zum Aufbau vor Ort. Die Komplettlösung enthielt Machbarkeitsanalysen, die Greiferkonstruktion und -logik, die Einbindung in die unternehmensspezifische Anlagensteuerung, Aufbau und Inbetriebnahme sowie die Schulung des Bedienpersonals. Im Paket mit der leistungsfähigen, bedienungsfreundlichen Software LHRobotics.Vision machte die Liebherr-Lösung damit das Rennen im Benchmark. „Im Gegensatz zu reinen Visionssystem-Anbietern, die die konkrete Anwendung oft nicht im Blick haben, konnten wir die Machbarkeit absichern. Das ist am Markt relativ selten“, erklärt Eduard Lorenz, für das Projekt zuständiger Angebotsingenieur bei Liebherr.
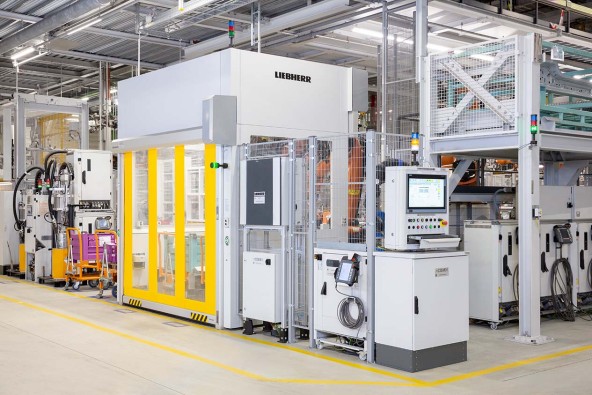
Liebherr automatisiert die Teilezuführung für Karosseriebleche
Automatisierte Teilezuführung
Die Bauteile, die die BMW Group im eigenen Presswerk herstellt, werden per Routenzug in großen Metallladungsträgern grob positioniert. Dort scannt das 3D-Visionssystem zunächst von oben die Position der Kiste sowie die genaue Lage der Karosseriebauteile im Ladungsträger. Auf Basis dieses Scans entnimmt der Roboter das Bauteil mit einem flexiblen Dreipunkt-Sauggreifer aus dem Ladungsträger und positioniert es millimetergenau im Klinkenspeicher, der als Zwischenpuffer dient.
Vorteile der Automation
Von dort aus führt der Roboter das Bauteil der Linie zu. Der Griff in die Kiste erfolgt immer wechselweise, jeweils für das linke und rechte Bauteil. Falls erforderlich, ist der Roboter auch in der Lage, das Bauteil aus dem Ladungsträger direkt in der Übergabestation der Fertigungslinie abzulegen. Der gesamte Vorgang zur Zuführung eines Bauteils von der Quelle bis zur Senke dauert etwas mehr als 20 Sekunden.
Vorteil der Automation ist eine konstante Taktzeit, die durch die Entkopplung von Linientakt und Prozesszeit des Bin Picking-Vorgangs erzielt wird. Und: Sie entlastet das Bedienpersonal der Anlage von monotonen, unergonomischen Tätigkeiten und beugt der Verletzungsgefahr durch scharfkantige Bauteile vor.
Installation in Rekordzeit
Eine besondere Herausforderung war das kurze Zeitfenster für den Aufbau und die Installation der Anlage zwischen zwei Bauphasen der gesamten Fertigungslinie. „Um das leisten zu können, haben wir im Vorfeld eine detaillierte Machbarkeitsanalyse und umfangreiche Testreihen durchgeführt. Vor allem die Genauigkeit bei der Ablage im Klinkenspeicher war ein Thema“, berichtet Lorenz. „Nachdem wir die Zelle vorab bei uns in Kempten einmal komplett aufgebaut und ausgiebig durchgetestet hatten, konnten wir sie innerhalb von nur drei Tagen im Werk der BMW Group aufstellen und in Betrieb nehmen.“
Auch die Integration der spezifischen Anlagensteuerung der BMW Group war keine Standardaufgabe. „Aber genau darin liegt unsere Stärke: Dass wir dank unserer Expertise und den individuellen Versuchen auch solche Herausforderungen erfolgreich meistern“, erklärt Lorenz die Herangehensweise von Liebherr nicht ohne Stolz.
Gute Zusammenarbeit
In der Projektphase erwies sich die Zusammenarbeit zwischen Liebherr und der BMW Group als reibungslos und lösungsorientiert. Für Herausforderungen wie die Integration in die Steuerungsumgebung, die interne Dokumentation der BMW Group oder auch die erschwerten Bedingungen während des Lockdowns fand Liebherr durchdachte Lösungen. „Beide Seiten haben ihren Job gemacht“, resümiert Lorenz und hebt hervor: „Was auch nicht überall selbstverständlich ist: Das Projektteam beim Kunden hat uns immer gut unterstützt.“
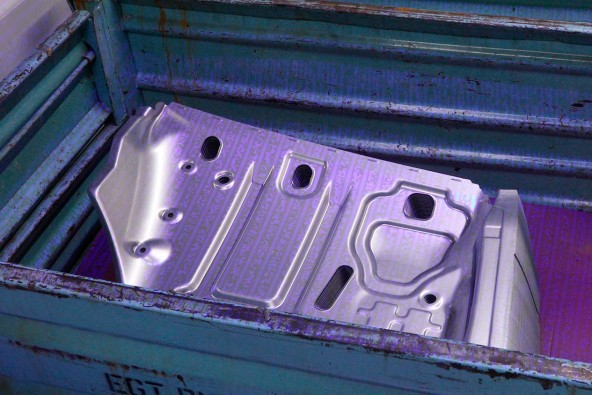
Kamerascan zur Lagebestimmung der Bleche mit 3D-Visionssystem
Partner mit Pioniergeist
Gerade weil man in diesem Fall gemeinsam Neuland betrat, konnte Liebherr die BMW Group erfolgreich unterstützen. Eduard Lorenz beschreibt es so: „Hier war Pioniergeist gefragt, um die Bin-Picking-Technologie in die Standards der BMW Group zu integrieren und die Schnittstellen perfekt aufeinander abzustimmen – und zwar so lange, bis alles funktionierte.“ Auch die räumliche Nähe ist ein Pluspunkt, der gerade in solch innovativen Projekten zum Tragen kommt. Alles in allem keine schlechten Voraussetzungen für weitere gemeinsame Projekte.