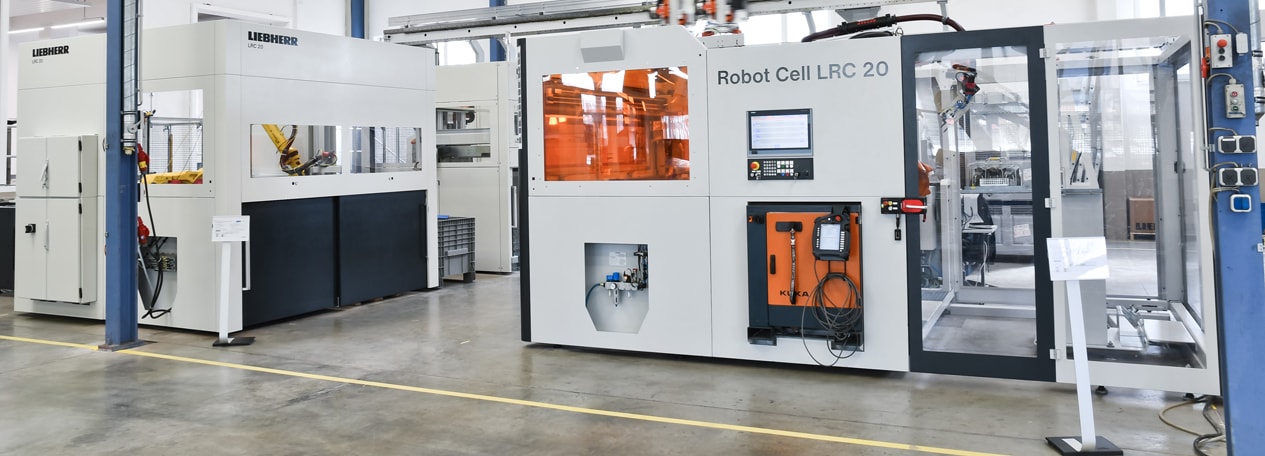
Liebherr Tech-Center: Experience new developments in automation systems
Liebherr opened a new test hall for automation systems in Kempten. Prototype solutions are tested and the systems are “put to the test” here. This new facility allows the customers to experience the tests “live” and gives them the opportunity to conduct virtual tests themselves.
A few minutes by car from the main plant in Kempten is the new test hall for automation systems by Liebherr-Verzahntechnik GmbH: the “Liebherr Tech-Center”. Originally rented as a testing ground for projects, Liebherr also quickly recognized the added value of the area as a place to interact with customers and decided to move the test systems entirely into the Tech-Center.
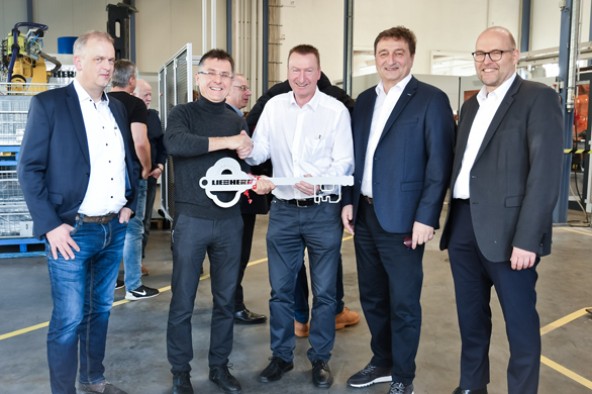
Opening of the Tech-Center in February 2020 (from left to right): Michael Messer, Managing Director Production, Wilfried Fischer, Production Manager Assembly Automation Systems, Thomas Mattern, Head of Automation Systems Development, Dr. Christian Lang, Managing Director Sales / Marketing; Dr. Hans Gronbach, Managing Director Construction / Development
Diverse testing possibilities in the test hall
Over an area of approximately 700 square meters, customers now receive an insight into the world of high-quality automation systems by Liebherr. Systems are tested and demonstrated to current and potential customers. Whether tests on prototypes or new products, feasibility analyses or simulations: “The testing possibilities in our new Tech-Center are diverse. In addition to our pallet handling system, we have also set up two test cells for Bin Picking. We are also testing a flexible manufacturing cell with an automated guided vehicle and our LP 100 linear robot,” says Thomas Mattern, Head of Automation Systems Development, explaining the layout of the test hall.
Two test technicians are permanently on site to commission the test systems, carry out prototype or customer tests and document the results. Other employees such as assembly workers, installers, software developers and computer scientists are deployed as required. Before the system receives sales approval, relevant components and drives are tested here for wear under real conditions, and tests are conducted under maximum load and with a maximum stroke.
Focus on optimized Bin Picking
Bin Picking is also continuously refined here. Gripper and load tests for the removal, placement, and fine-positioning of geometrically complex parts are refined to optimize workflows. “This automation solution enhances process reliability and increases productivity. With the two Bin Picking test cells, our Tech-Center is another factor in a modern manufacturing site,” continues Thomas Mattern. Tests on the automation of systems for the e-mobility market are being planned.
We are talking about a win-win situation for both parties: our customers and Liebherr. While we can effectively carry out tests and test series with new products in terms of development, our customers receive professional support.
Customer area as a place of innovation
A particular highlight of the test department is the customer area. Slightly raised and with a view of the hall, customers can follow the tests “live” in a pleasant atmosphere. At a Bin Picking workstation, they can experience the Bin Picking system and process as a 3D visualization or even simulate it themselves. The top floor has an office and meeting area which offers space for undisturbed project meetings and technological discussion, while being close to the systems at the same time. “We are talking about a win-win situation for both parties: our customers and Liebherr. While we can effectively carry out tests and test series with new products in terms of development, our customers receive professional support. We are convinced that we have created a place of innovation in the Tech-Center,” concludes Thomas Mattern.