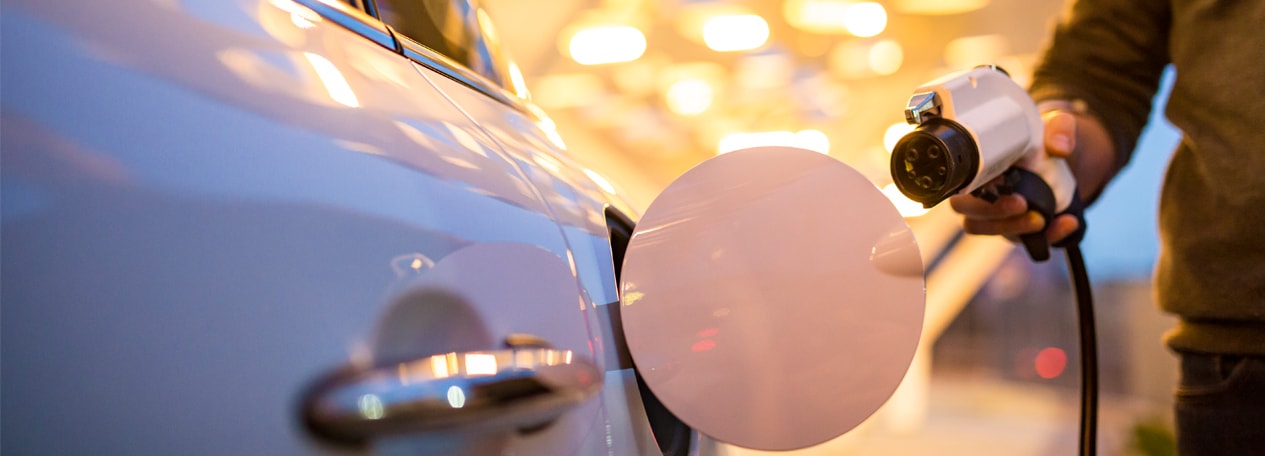
A flexible automation system for battery pack assembly
Liebherr is embracing technological change towards alternative drives and has developed a modular automation system solution for the assembly of battery packs for electric cars – from small batch manufacturing to fully automated mass production. Advantages: Liebherr automation is system-compatible and offers process reliability, fast cycle times and flexibility.
Alternative drives have been an important topic for some time at Liebherr. Many of the company’s products, from concrete mixers to mobile cranes, already feature electric drives (you can find more information at the end of this text). In view of predicted future developments in the field of e-mobility, it was a logical step to take a closer look at Liebherr’s automation systems portfolio with regard to the requirements associated with electrification in the automotive industry.
A development project with scientific support from KIT Campus Transfer GmbH, a spin-off of the Karlsruhe Institute of Technology (KIT), and PEM Motion GmbH, a spin-off of RWTH Aachen University, came to the conclusion that Liebherr is the perfect partner when it comes to the automated assembly of battery packs for vehicles with electric drives. Up to now, the majority of the production is done manually or is only semi-automated. However, increasing demand and the resulting orders can only be fulfilled with more extensive automation solutions. In terms of serial production of components for combustion engines, automated assembly has long been the core business of Liebherr automation systems.
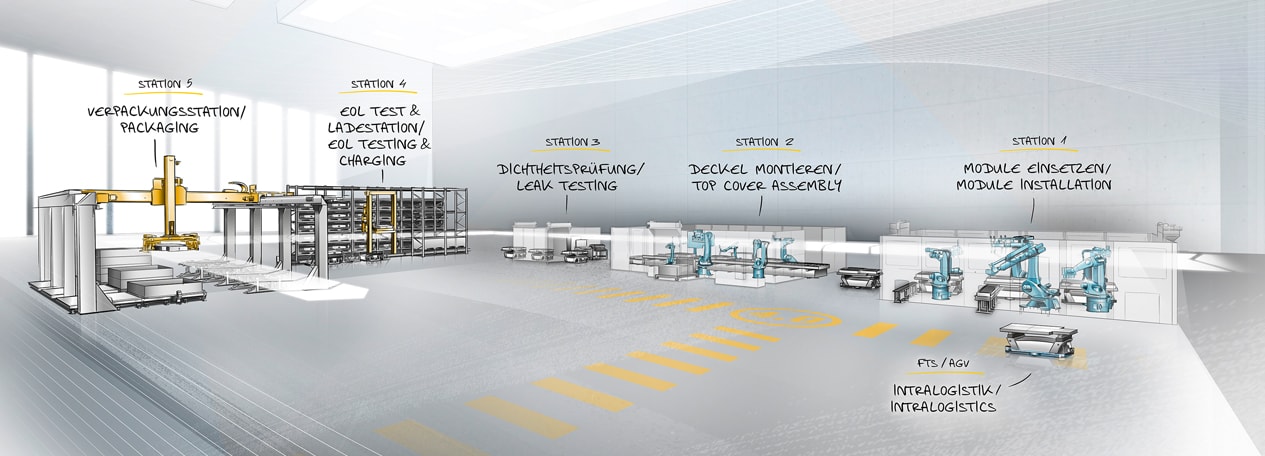
Challenges in battery pack assembly
The conditions that prevail in the assembly of combustion engines cannot be transferred one-to-one to the assembly of battery packs. One of the challenges in handling battery packs is the weight; a fully assembled pack weighs up to 800 kilograms in the automotive sector. Liebherr’s handling systems are ideally suited to this weight class.
Another challenge is the safety-relevant properties of battery parts. Strict customer requirements and safety regulations in system design are, however, already a matter of course for Liebherr. Thomas Mattern, Head of Development in Automation Systems, explains, “We can draw on existing experience, especially in production lines for the automotive industry. The big difference is that this is a workpiece that is subject to different assembly and technological processes. In addition, special requirements arise due to specific properties the workpiece should possess, such as the ability to contain hazardous substances, the degree of flammability and the electrical charge. But it is precisely such challenges that offer certain incentives for which we are well equipped.” Here Liebherr excels with its system capability and expertise in process integration. Product-specific process stations such as metering units, screwing stations or leak testing, which are not part of Liebherr’s core competences, are solved together with suitable partners and suppliers and integrated into the overall process.
Highlights at a glance
Flexibility: turnkey solutions from small batch manufacturing to mass production
Scalable product kits: heavy-duty handling systems, linear gantries, industrial robotics, storage solutions, intralogistics, control system
System capability: integration of product-specific processes
Process reliability: fast cycle times, minimum footprint
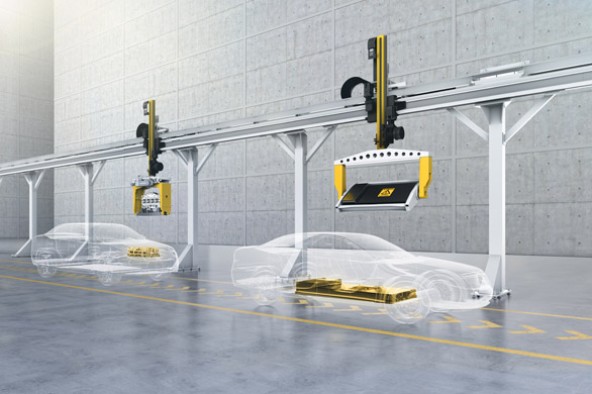
Flexible solution with modular product kits: the Lego principle
Liebherr attaches great importance to modular design, scalability and networking of components. The user has an entire product kit at their disposal: handling systems specifically for heavy transport loads, linear gantries for fast cycle speeds, industrial robotics for complex tasks, storage solutions, intralogistics and the corresponding control systems. Thomas Mattern draws a vivid comparison: “It’s like a Lego building set, the skill is in assembling the individual modules together. Our systems have universal interfaces like the nubs of Lego bricks. From this, we configure a completely individual system according to our customer’s requirements”. This unique capability of Liebherr automated systems allows for semi-automated systems for small quantities or fully automated lines for large serial production can be designed in a scalable way. Liebherr is an experienced partner when it comes to issues such as interfaces, parallel processes, reproducibility, emergency strategies, and availability and tracking of parts. “For battery pack assembly, we can supply everything from a single source to individual process stations that can be combined to a complete turnkey system. Not many can do that,” says Jan Pollmann, Development Engineer for Automation Systems, summing up the scope of possibilities.
Such a flexible system ensures maximum automation density with minimum footprint. Space-saving linear gantries, which are suitable for easy handling of heavy weights, can be specifically combined with industrial robotics that take over more complex handling and process tasks. Further flexible solutions such as automated guided vehicles (AGV) can also be integrated. Thomas Mattern is optimistic about the future: “We have brought the ‘old’ and the ‘new’ world together and are well prepared for alternative drive systems.”
E-mobility at Liebherr:
In order to be prepared for future developments, alternative drive systems are a major topic at the Liebherr Group, and are considered across all divisions. Liebherr is not only a supplier of production systems for e-mobility, but also a manufacturer of construction machinery and mining products with innovative drive concepts:
Concrete technology
Concrete mixer ETM 905
Stationary concrete electric pump 70E
Handling equipment
Material handling machines LH 26 electric industry and LH 110 C gantry port
Mining
Mining excavator R 9200 E
Special underground engineering
Heavy-duty drilling rig LB 16 unplugged (battery operated)
Mobile and crawler crane
Mobile construction crane MK 88-4.1
Maritime cranes
Liebherr portal crane LPS 420E