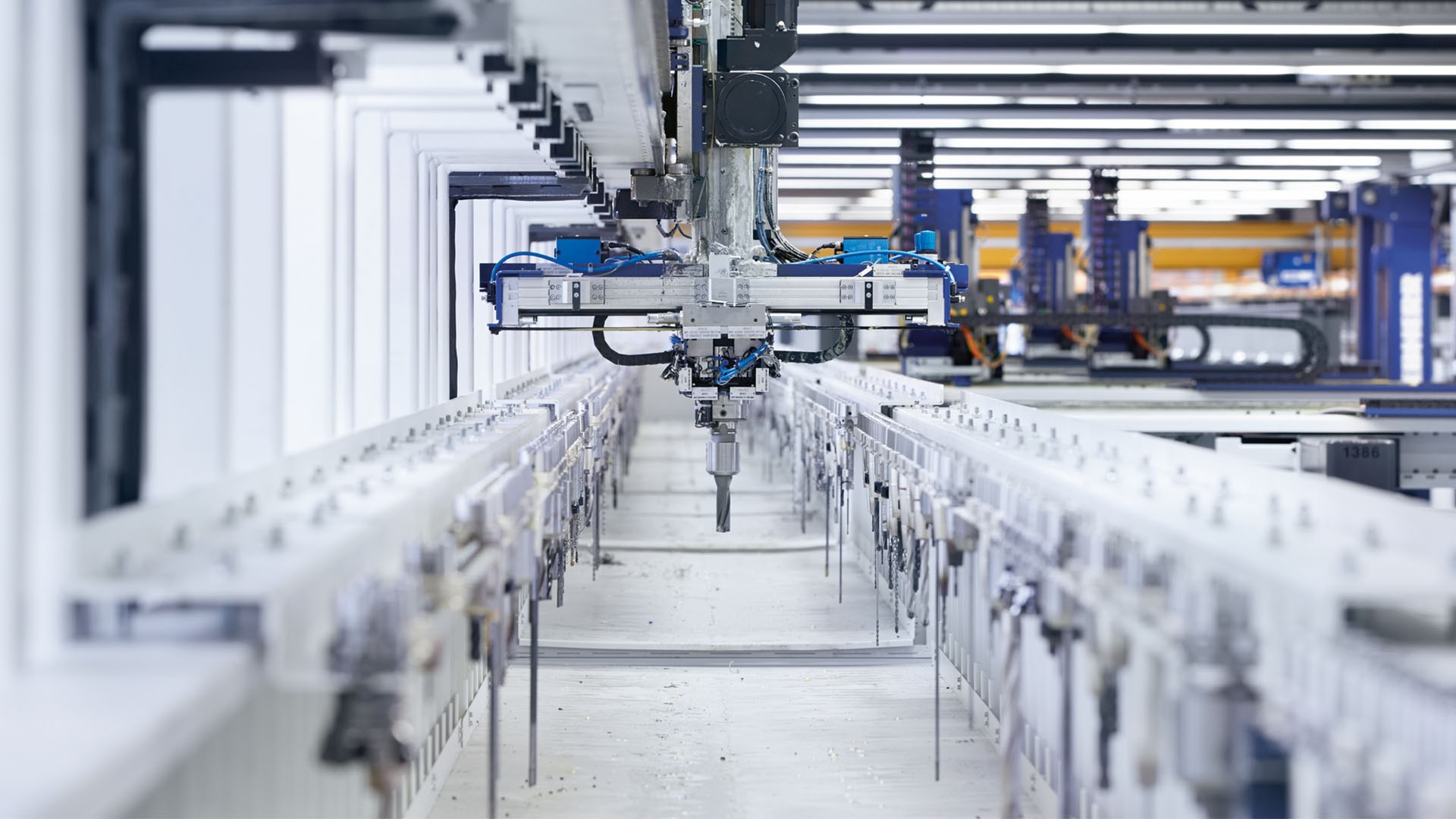
Tool handling system
Liebherr automates the handling and storage of tools in sophisticated systems perfect for production environments with multiple machining centers or high tool demand.
Increasing the degree of automation: from automatic workpiece to tool management
In industries with high tool throughput, such as aerospace or tool and mold making, automated tool handling solves key problems. In such cases, it makes sense to add tool automation to automatic machine loading in linked systems.
Holistic tool management with Liebherr system competence
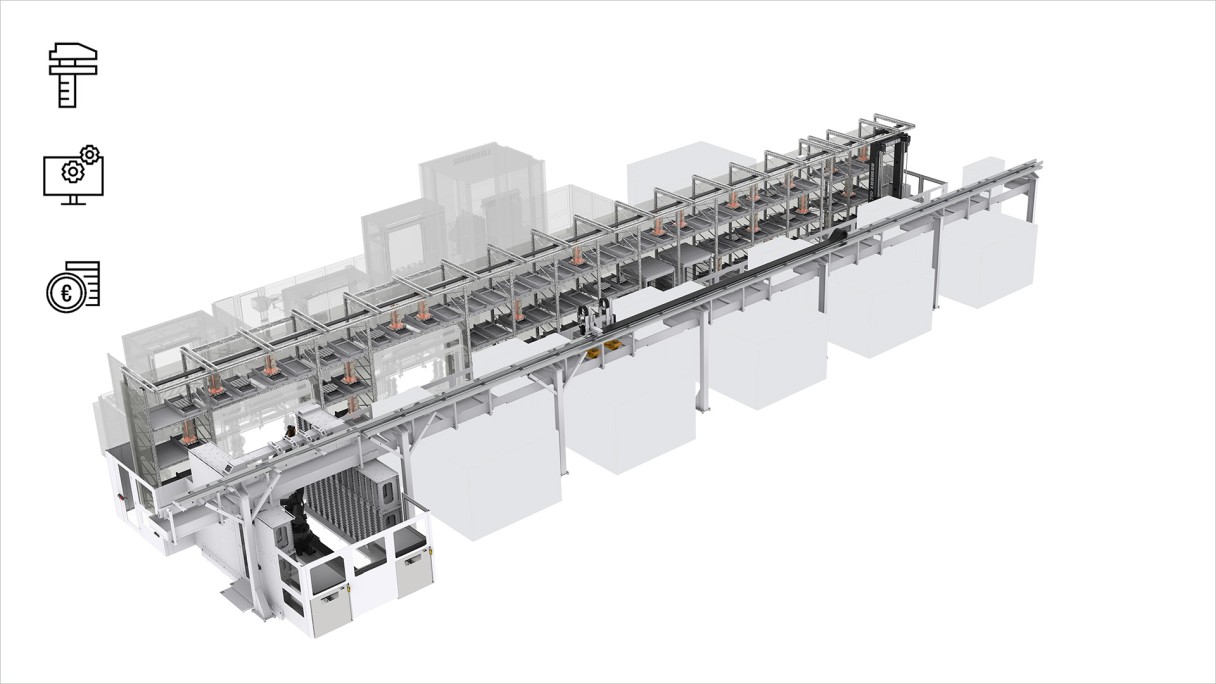
Complementary products
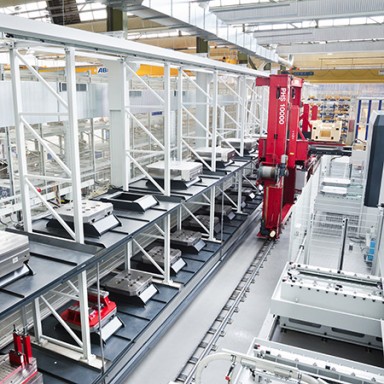
PHS pallet handling systems
Perfectly suited for variant manufacturing, the Liebherr pallet handling system offers large workpiece storage units and thus long autonomy times in low-manpower or even unmanned manufacturing. Intelligent cell control helps to manage resources and reduce the complexity of high mix/low volume manufacturing.
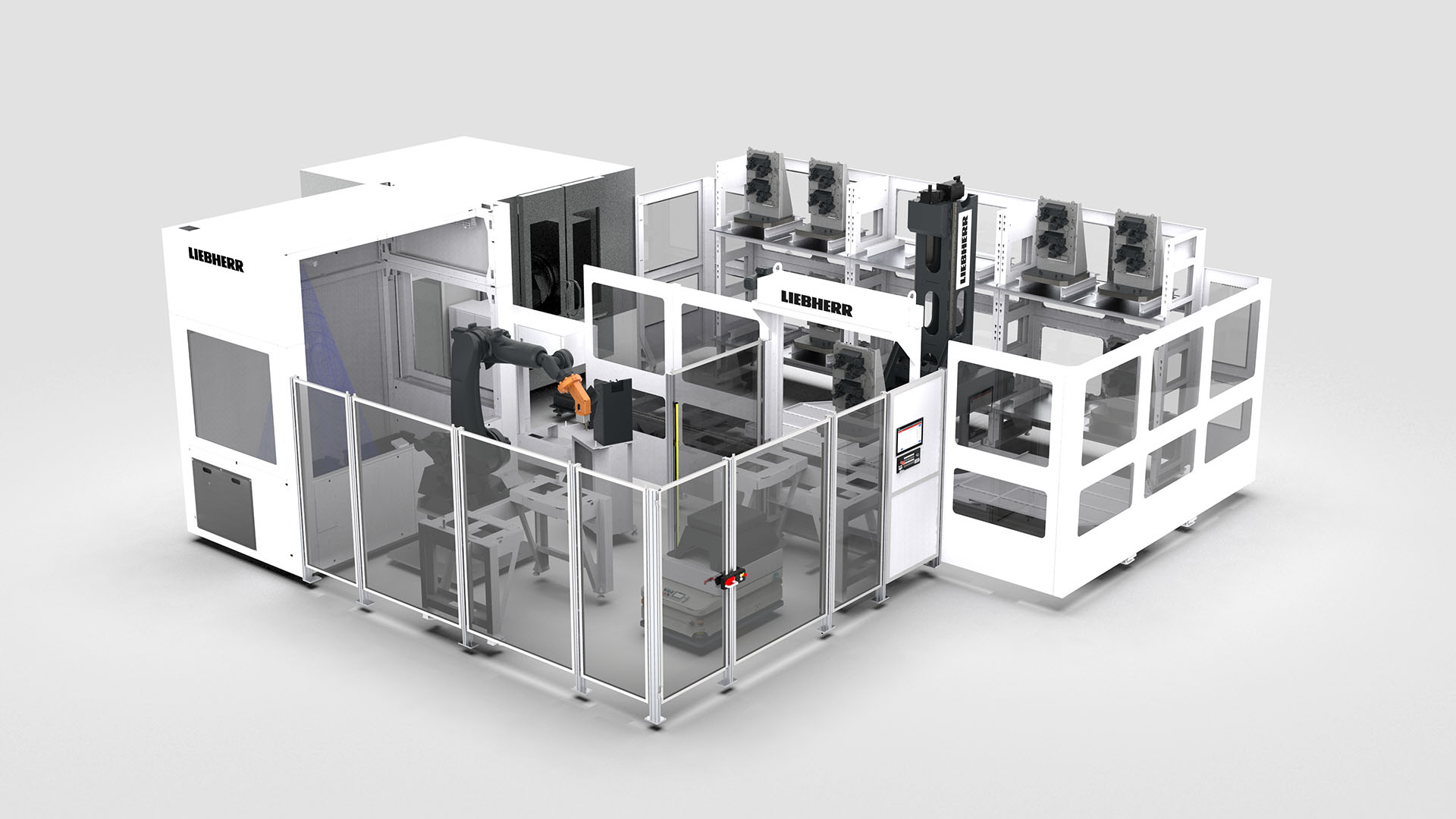
Flexible robot cells
From machine to part nest loading, Liebherr utilizes the full potential of your production with the help of robots.