Press releases | 2025/01/22
Liebherr presents intelligent assistance systems for bottom-slewing cranes
- Sway-free lifting of the load without diagonal pull increases safety for people and sensitive components
- Maximum ease of use with semi-automated lifting
- Assistance systems are available for current K and L cranes
Liebherr sets new standards in the tower crane world: Five intelligent assistance systems for bottom-slewing cranes simplify everyday work on site and make life easier for crane operators. The assistance systems independently carry out semi-automated, simultaneous movements and enable sway-free lifting.
Vehicle assistance systems are becoming ever more common in both the automotive and construction machinery industry. The Liebherr Group is already successfully using assistance systems to increase safety and efficiency on site. Wheel loaders are equipped with an active person detection system for the machine’s rear as well as a linked brake assistant to recognise the presence of people in the manoeuvring area as early as possible and avoid accidents. Liebherr earthmoving and deep foundation engineering machines are equipped with assistance systems that make operation on site easier, more convenient and more efficient.
As of now, intelligent assistance systems are also available for Liebherr tower cranes. They help to make construction sites safer for both people and materials, as well as ensuring more convenient and efficient crane operation. It only takes the push of a button to switch them on or off as required. There are five intelligent assistance systems available for the current Liebherr K and L series bottom-slewing cranes. Sway Control is included as standard with all cranes. The other four, Sway Control Plus, Guided Hook, Vertical Line Finder and Positioning Pilot are all optional.
Sway Control Plus – Sway-free operation
The assistance system supports the crane operator with sway-free operation by actively correcting hook block sway in both slewing and trolley directions. A sensor system also recognises sway that already exists before the system is activated or is caused by external influences e.g. wind. This assistant is particularly beneficial for occasional crane operators who have sufficient space, and for new crane operators as less training is needed.
Guided Hook – moving the load hook by hand
The Guided Hook assistance system allows an operator on the ground to easily move the load hook by hand and thereby guide it to the load themselves. The hook can be moved in slewing and trolley directions. Constant communication between the crane operator and ground operative is therefore no longer necessary. This reduces the likelihood of errors and misunderstandings, which increases efficiency and safety on site.
Vertical Line Finder – lifting without diagonal pull
Vertical Line Finder supports the crane operator with the lifting of loads by preventing diagonal pull, and therefore sway, when lifting. The crane automatically controls the slewing gear and trolley to ensure that the load hook is always optimally positioned above the load’s centre of gravity. As a result, the load is always lifted vertically, without any sway, which increases safety for people and sensitive components on site.
Positioning Pilot – navigating plotted routes and saved points
The Positioning Pilot assistance system makes it possible to move to saved points semi-automatically and to follow predefined routes. Up to three hook positions can be repeatedly and accurately accessed as required and two individually mapped routes can be navigated. The routes can be travelled forwards and backwards, and stopping in between is also an option. This makes Positioning Pilot ideal for repetitive, monotonous lifting tasks like concreting work and truck unloading processes that require several lifts. These semi-automated movements are carried out without sway.
Operator assistants based on new control and operating systems
The new assistance systems are based on Liebherr’s Control 5 control system and Tower Crane Operating System 2. The control system’s high processing power enables all assistance algorithms to be processed in real time. A battery-powered IMU (Inertial Measurement Unit) sensor system measures hook inclination and angular velocity, while a sensor system on the tower detects the inclination of the tower.
Further Information
Video
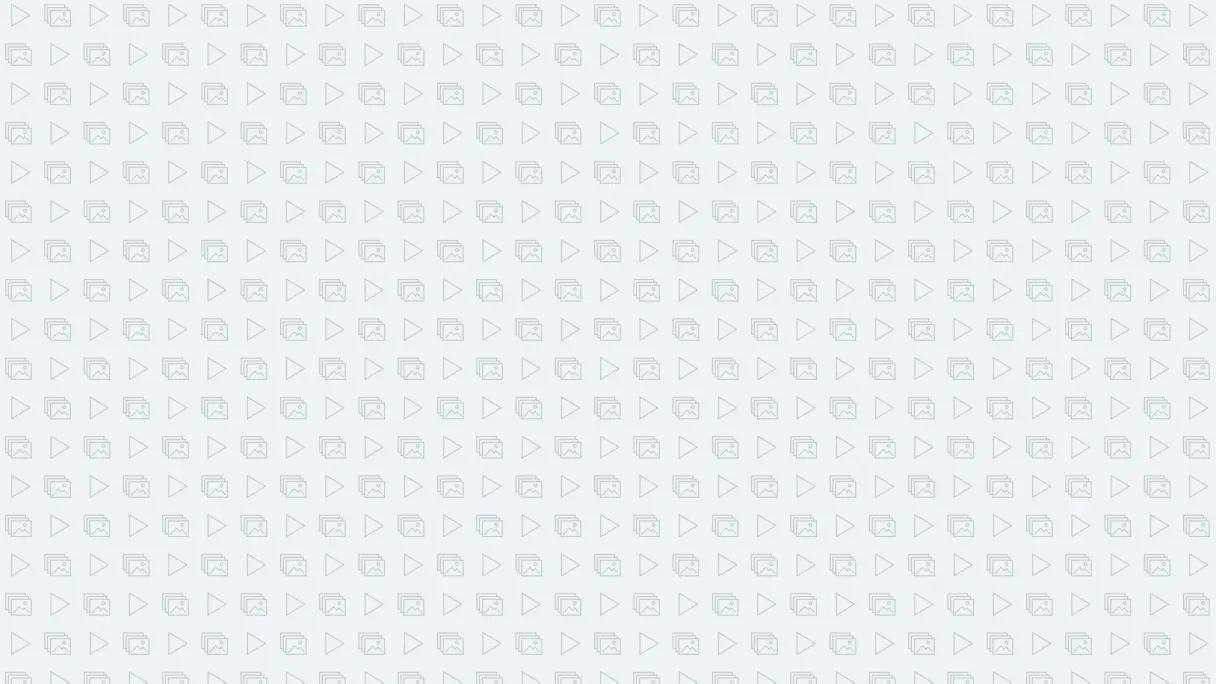
この動画は Google* によって提供されています。この動画を読み込むと、IP アドレスを含むお客様のデータが Google に送信され、Googleによって欧州および欧州経済地域外、したがって第三国、特に米国内で同社独自の目的のためにも保存および処理される可能性があります**。Google のデータ処理に関して、弊社は影響を及ぼすことはできません。
「同意する」をクリックすることで、一般データ保護規則の第6条1項(a)に従い、この動画に関連して Google へのデータ送信に同意したものとみなされます。各 YouTube 動画に個別に同意することを希望せず、このブロッカーなしで動画を読み込むことができるようにしたい場合は、「YouTube 動画を常に許可する」を選択し、今後弊社のウェブサイトで開く他のすべての YouTube 動画について、Google への関連データの送信に同意することもできます。
お客様は、設定の「その他のサービス(オプション)」(後に弊社ウェブサイトのフッターにある「データ保護設定」からもアクセス可能)で当該サービスの選択を解除することにより、いつでも有効な同意を撤回し、以降のお客様のデータの送信を停止することができます。
詳細については、弊社のデータ保護宣言および Google のプライバシーポリシーをご覧ください。*Google Ireland Limited, Gordon House, Barrow Street, Dublin 4, Ireland; 親会社:Google LLC, 1600 Amphitheatre Parkway, Mountain View, CA 94043, USA** 注記:Google へのデータ送信に伴う米国へのデータ転送は、2023 年 7 月 10 日の欧州委員会による妥当性決定(EU-米国データプライバシーフレームワーク)に基づいて行われます。