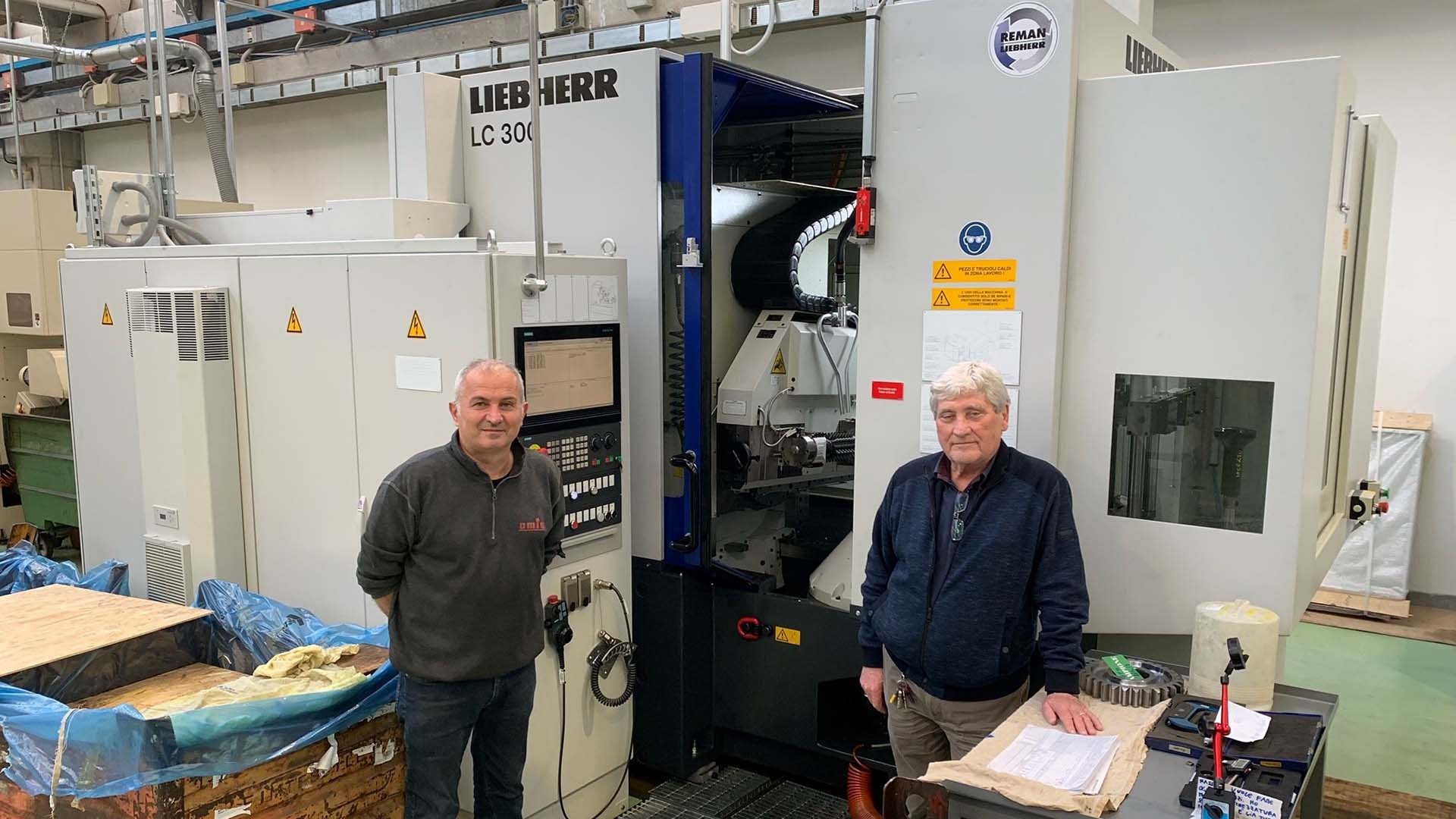
A second life for high-quality machines
In times of resource scarcity and supply bottlenecks, the Reman used machine program from Liebherr-Verzahntechnik GmbH can provide a real alternative to purchasing a new machine. The Kempten company now offers the general overhaul of used machines at three sites worldwide.
Liebherr repairs and overhauls older hobbing, shaping or gear grinding machines, replaces worn or damaged components and assemblies and offers fully overhauled, used machines for purchase. Equipped with new control software and adjusted interfaces, the Reman machines are even Industry 4.0-compatible. Liebherr is breathing new life into these – at attractive conditions, with short delivery times and a new warranty. This means that if a company decides to defer the acquisition of a new machine for cost, time or sustainability reasons, a machine from Liebherr’s Reman program can be a worthwhile alternative – as demonstrated by various examples from the industry.
Second life for gear grinding machine LCS 600
In 2021, Liebherr overhauled an LCS 600 – a gear grinding machine built in 2008 – for a large US manufacturer of transmissions for commercial vehicles. The machine was ready for acceptance by the customer in Kempten after only six months. “In order to keep the downtimes as low as possible, we prepare the assemblies and components beforehand as far as possible. This considerably reduces the actual work on the machine,” explains Ralf Glatzeder, Head of the Reman department at Liebherr. “If necessary, we can provide a machine for rent in the meantime.”
Because of the narrow manufacturing tolerances in finish machining, which are in the micrometer range, the overhaul of a gear grinding machine requires special expertise. “But we were able to demonstrate to the customer that the Reman machine is equal in terms of accuracy,” Glatzeder continues. A particularly impressive feature was that, with the current, user-friendly Liebherr control system LH 90, the machine is even Industry 4.0-compatible. “After our general overhaul, you can expect the same operating life as from a new machine,” he states.
Two hobbing machines before and after the general overhaul
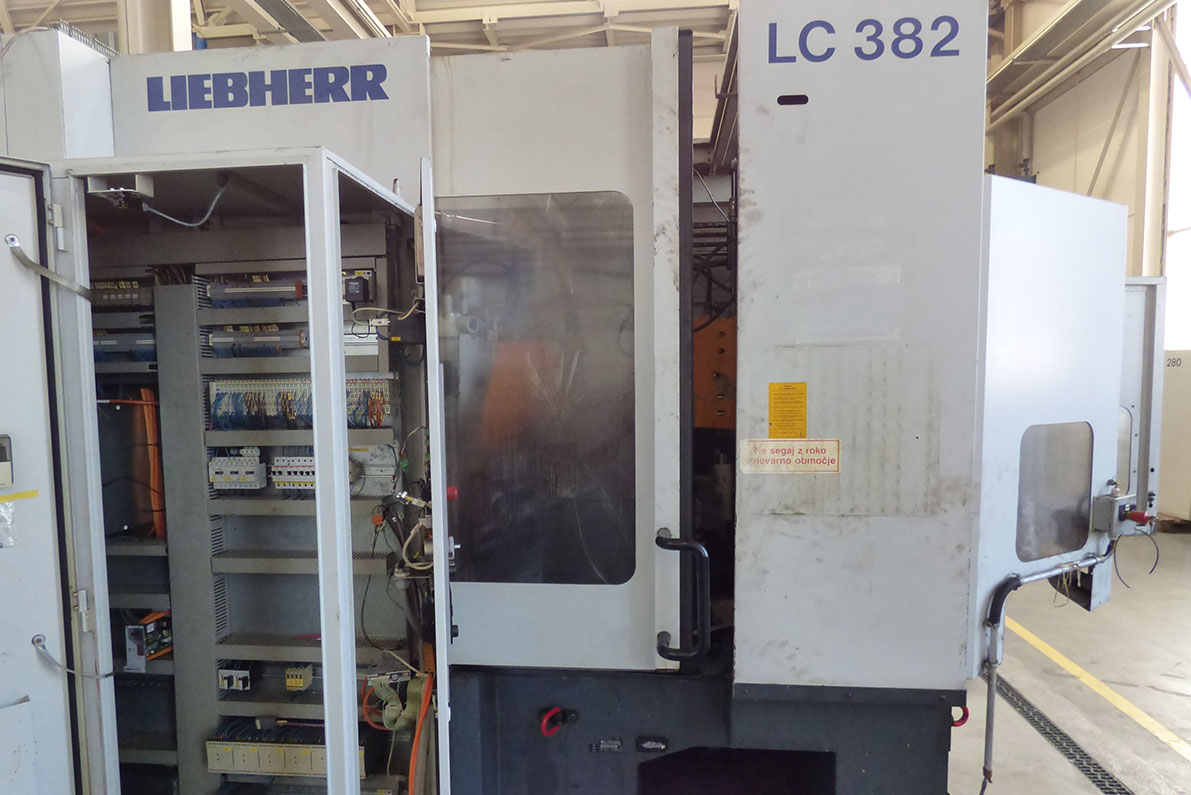
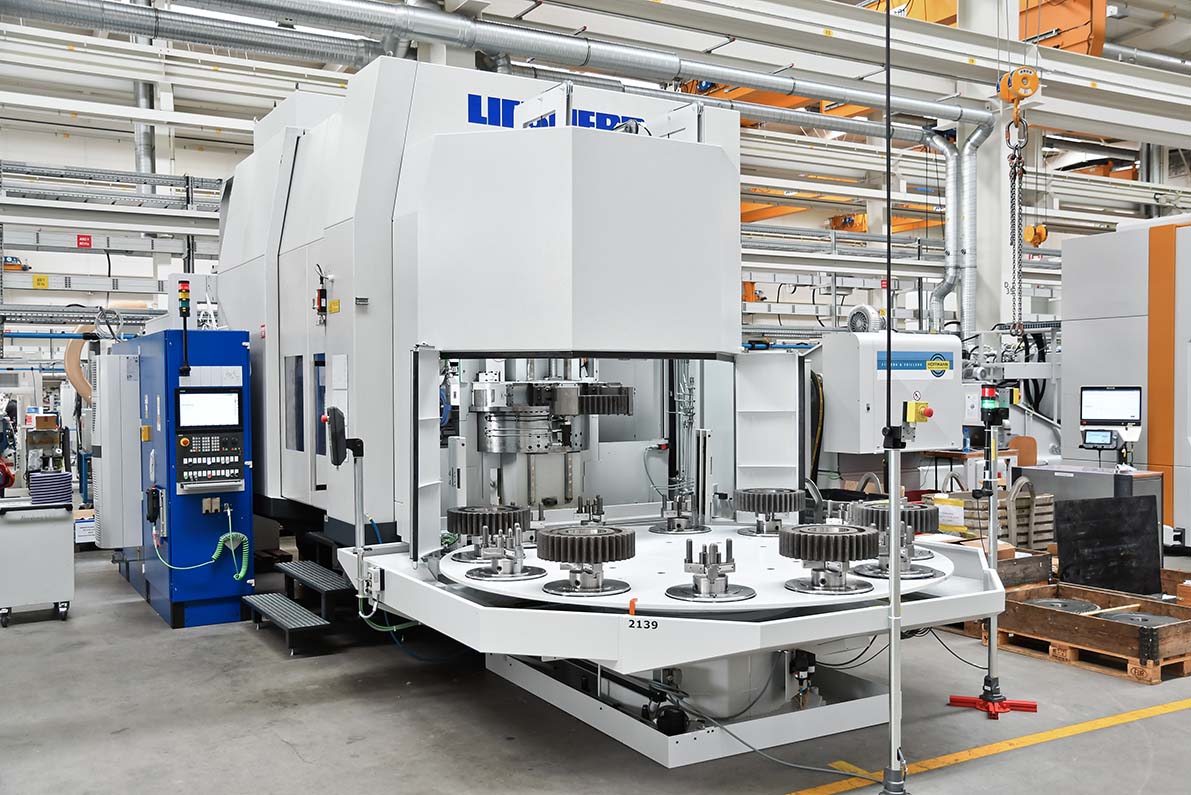
Reman gear cutting machine bridges capacity bottleneck at short notice
The Italian family company OMIG Ingranaggi SRL manufactures, among other things, chamfered cylindrical gears using an LC 380 from Liebherr. Due to capacity bottlenecks, a second, identical machine was required at very short notice to handle the order volume.
In this case, Liebherr was able to supply an already fully overhauled Reman machine. With minor adjustments to the interfaces, the “twin” was available within just three months and has been running in the manufacturing at OMIG since November 2021 – this is also equipped with an LH 90 control system and is therefore capable of data exchange.
“The Reman machine saved us. This was the only way we could obtain a second machine in such a short time,” recalls Ivano Cocchi, CEO of OMIG. “The familiar control unit and the same interfaces meant that setup, operation and connection with our company network were entirely straightforward and presented no problems,” he stresses.
Reman international
Liebherr now offers the Reman program at three locations worldwide: at the company headquarters in Kempten, in Saline, Michigan (USA), and in Guaratinguetá (Brazil). In Brazil, the first used machine was delivered to a transmission manufacturer in May 2022. A further LC 300 gear cutting machine is currently being overhauled at the Guaratinguetá site. Due to high demand, there are already considerations to expand the Reman network into Asia in order to avoid time losses due to customs formalities when transporting the machines.
The machines from the Reman program are as good as new and guarantee the highest accuracy at a low investment cost.
Sustainability
Sustainability due to efficient use of energy and conservation of resources is another important aspect. The general overhaul of used machines requires fewer new components and materials than new production, since only the wear parts are replaced. For example, the Slovenian automotive supplier KLS Ljubno d.o.o. is already using several Reman machines from Liebherr. This is because the company also places great emphasis on environmental aspects in terms of its suppliers. “The Reman range by Liebherr is perfect for us. Not only is it environmentally friendly but also economical,” applauds Georg Halužan, Technical Head of KLS.
“The machines from the Reman program are as good as new and guarantee the highest accuracy at a low investment cost.” As a member of the VDMA initiative Blue Competence, Liebherr is committed to sustainability. “Reman machines cannot replace new machines, but they are a very good addition in some cases. They show that sustainability can also be economical,” summarizes Glatzeder.