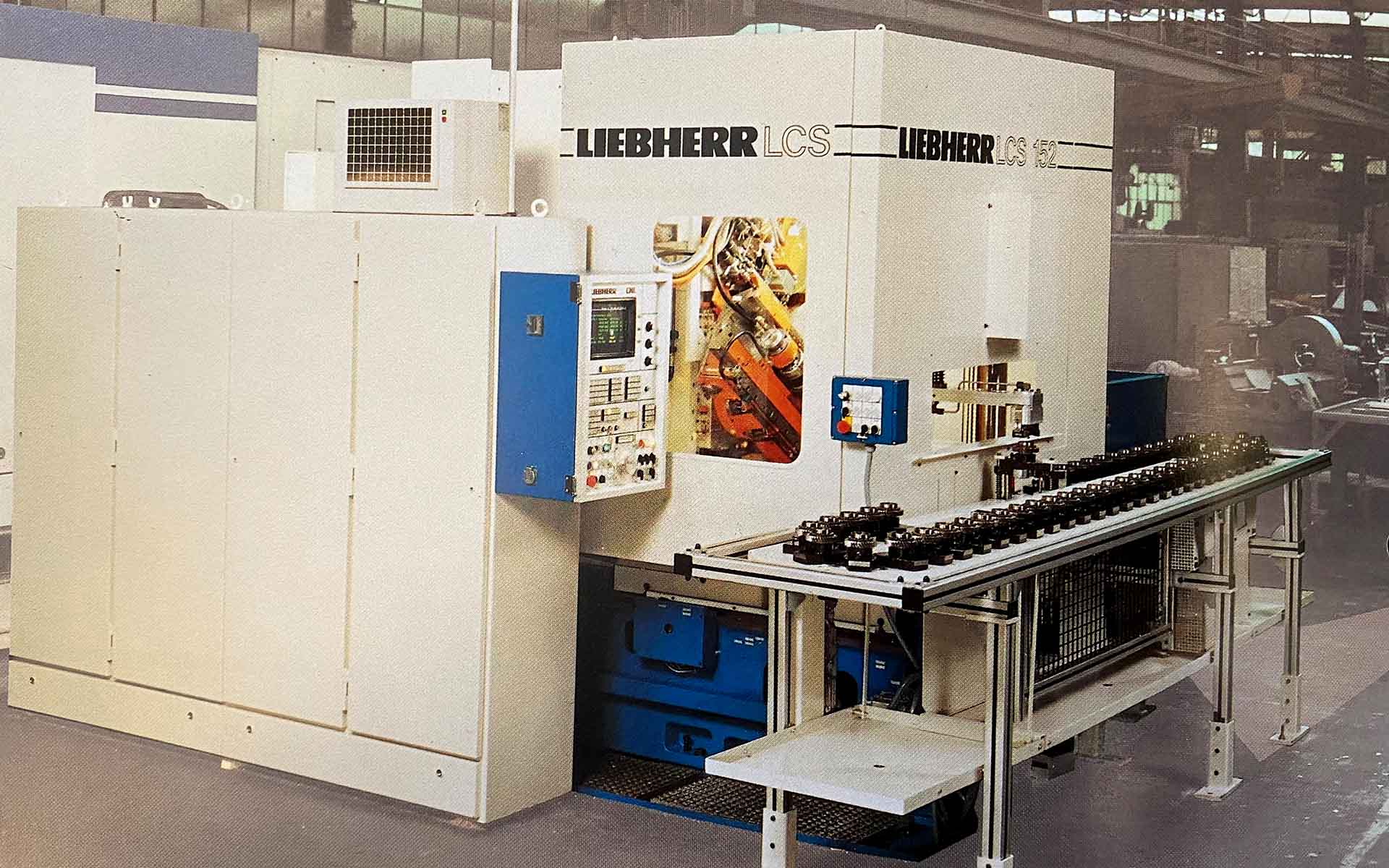
30 years and still going strong
More than 30 years ago, Liebherr-Verzahntechnik GmbH introduced the LCS, an innovative gear grinding machine that was the first in the world to allow generating grinding with dressing-free CBN grinding worms. Since then, Liebherr has continued to develop this robust machine through each generation and maintained its position as an international pioneer in gear grinding. This is the story of the continuous development of an innovative product, and it’s far from over.
1st generation 1988-1998
Introducing CBN generating grinding
Until the late 1980s, the market for grinding machines was dominated by two technologies: users could choose between generating grinding with dressable corundum worms and profile grinding with non dressable CBN discs. In 1988, Liebherr introduced a groundbreaking innovation: the combination of high-speed, continuous generation grinding with dressing-free CBN worms. To do this, the company had developed a metal worm base body coated with the extremely hard cutting material CBN (cubic crystalline boron nitride).
Rapid, twist-free generating grinding
The first generation of the LCS series was born. It achieved cutting speeds of 60 meters per second, which meant it could reduce hard-fine machining times by up to 70 %. However, the high-precision tools were complex to manufacture. To be economical in use, they had to be durable enough to ensure acceptable tool cost per workpiece. This is why Liebherr still offers a reconditioning service for used tools.
Liebherr had already applied for a patent for twist-free generating grinding in 1987. This corrects twists – profile distortions caused by the process during continuous generating grinding of gears with lead modifications. Another patent was for generating grinding followed by polishing on a gear grinding machine. This idea is currently experiencing an impressive revival for low-noise, low-friction e-drive gearboxes.
2nd generation 1998-2004
Directly driven machine table
At EMO 1998 in Hanover, Liebherr presented the second generation of the LCS. In addition to an optimized design, it was one of the first gear grinding machines in the world to have a direct drive for the machine table. This was a quantum leap for gear quality: the higher pitch quality of the gears made it possible to pair generated ground gears in gearboxes and thus significantly reduce noise in vehicle transmissions.
Profile grinding and CBN combination grinding
The new generation of machines was also able to perform CBN profile grinding with up to four tools on one arbor. The new technology of CBN combination grinding, which involves roughing with a worm and finishing with a disc, allowed economical and precise production of all large-module truck components on one machine. This made the LCS a worthwhile investment for many commercial vehicle manufacturers.
3rd generation 2005-2020
Now with corundum generating grinding
The efforts of a Korean automobile manufacturer to develop more powerful passenger car transmissions was the impulse for yet another innovation: the LCS machines now featured dressing technology in order to offer corundum generating grinding around the world.
Corundum profile grinding, gear checking
More upgrades were to come: first, Liebherr implemented corundum profile grinding, and later gear checking directly on the machine. This made the LCS one of the first machines that could be used for both generating and profile grinding, and with CBN and corundum technology or a combination of the two cutting materials at the same time. This technological flexibility and versatility extended its potential uses in a many different industrial sectors, including manufacturers of construction and agricultural machinery, job shops and all kinds of industrial gear manufacturers.
LCS – flexible, robust and durable
The strengths of the LCS series have always been flexibility and versatility. In addition, the machines are so robust and durable that some of them have been in use for 20 to 25 years. With more than 800 installed machines, the LCS is one of Liebherr’s most successful gear cutting machines. “Quite a few machines from the early generations are still going today. There are even machines that have been completely overhauled and equipped with the latest control technology as part of Liebherr’s Reman program, giving them a second lease of life, so to speak,” says Thomas Breith, Head of Product Management for gear cutting machines at Liebherr. Due to the robust automation, which can handle workpieces weighing up to 100 kilograms and up to 800 millimeters in length, he jokingly calls the LCS 500 the “bodybuilder” in its class.
The LCS 1200 fits perfectly into our production, as it can be flexibly used for generating grinding in mass production and for profile grinding of large components in small batches.
Jiangsu New Yinye Transmission Electrochemical Co., Ltd.
Sector:
Industry/wind power
Company size:
approx. 120 employees
Founded:
1993
Company headquarters:
Wuxi, Provinz Jiangsu (China)
Website:
www.wxxinyinye.com
LCS 1200 in use for high-precision special gears
One of the LCS “heavyweights” is in use at Chinese gear manufacturer Jiangsu New Yinye Transmission Electrochemical Co., Ltd., where the LCS 1200, equipped with Liebherr’s largest and most powerful grinding head, grinds special components with diameters of up to 1,200 millimeters. The company is located near Shanghai and specializes in manufacturing high-precision gears which are used in many different sectors, including wind power and materials handling, mining, refueling facilities, food and feed machinery, and other industries. Mr. Xu Yi, General Manager at Jiangsu New Yinye explains, “The LCS 1200 fits perfectly into our production, as it can be flexibly used for generating grinding in mass production and for profile grinding of large components in small batches.”
The latest generation since 2020
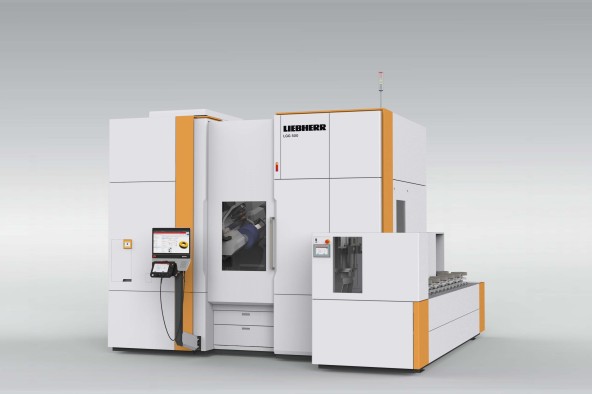
LGG with internal grinding
The LGG, the compact successor machine of the latest generation, has the full range of grinding technologies of its predecessor while offering even more flexibility: the machining options have been expanded to include internal grinding, and three different external grinding heads in different specifications are also available. With an integrated centrifugal device for chips and cooling lubricant that operates during machining, the LGG meets all the requirements for environmentally friendly, clean factory production. Together with the LHOpenConnect data exchange platform, which allows a measuring machine to be directly connected, for example, it’s all set for Industry 4.0.