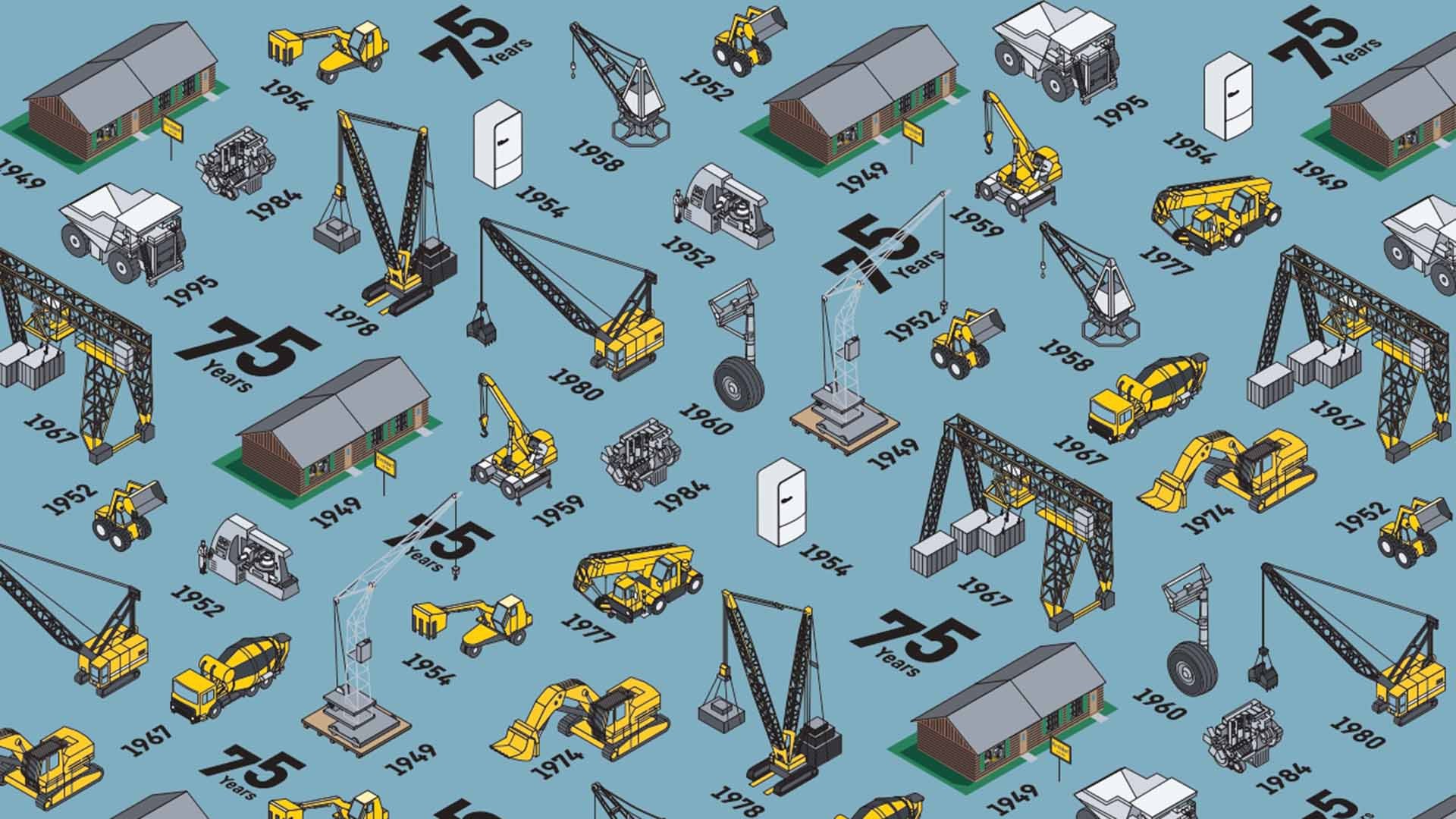
Evotion 2024 | Customer Magazine
Evotion 2024 | Customer Magazine
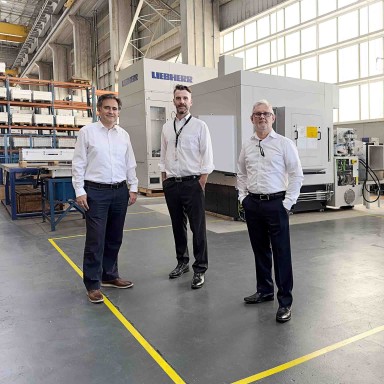
Synergies for the whole of South America
Liebherr Brasil Ltda is celebrating its 50th anniversary in 2024. Excavators, cranes, truck mixers and slewing bearings are just some of the products manufactured for the South American market at the site in Guaratinguetá, Brazil. The sales and service activities of the group are also gathered together here. Liebherr-Verzahntechnik GmbH also has 15 employees at the site.
01
AI supported image processing in bin picking
Liebherr-Verzahntechnik GmbH is taking the plunge into artificial intelligence (AI) with its latest version of LHRobotics.Vision bin picking software. Filtering out irrelevant image data enables faster and more accurate detection of unsorted workpieces when removing them from containers.
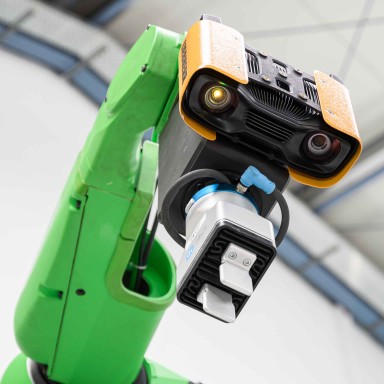
02
Inline process monitoring with LHProcessMonitoring
In electric vehicles, the meshing of the gears can cause disruptive gearbox noise excitations. It is therefore becoming increasingly important for automotive manufacturers and suppliers of electric motors to identify and eliminate the causes of unwanted noise at an early stage. With the LHProcessMonitoring software, Liebherr-Verzahntechnik GmbH has developed a tool that detects deviations during gear production. This saves costs and reduces rejects – and is therefore also of interest to manufacturers of conventional gearboxes.
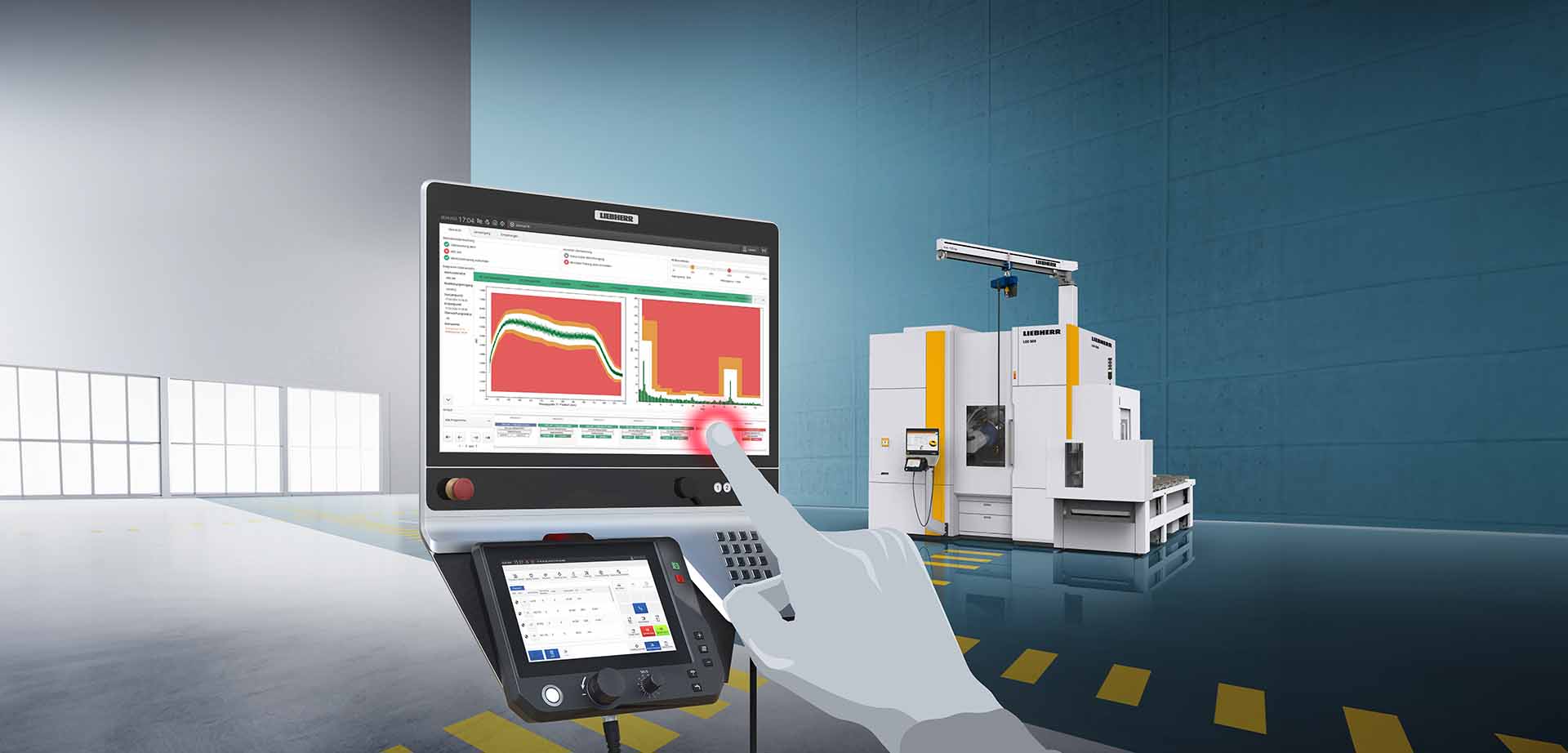
03
LHRobotics.Vision goes to Asia
Pongi Gear Experts Co., Ltd. has represented Liebherr-Verzahntechnik GmbH in Taiwan for many years. In 2022, it incorporated the Kempten company‘s bin picking software into its portfolio and set up its own demonstration and training facility for intelligent automation. Potential customers can evaluate the smart and intuitive system on a fully equipped cell with a camera, robot and simulation tool.
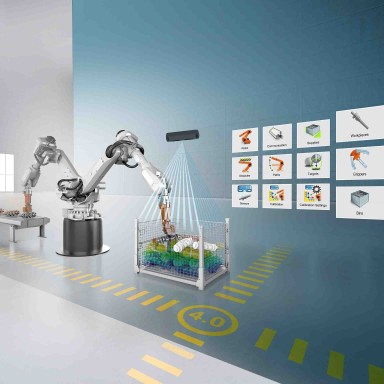
04
Non-destructive disassembly of battery packs
Sustainability goals and increasing raw material prices are making the recycling of batteries from electric vehicles an increasingly pressing issue for the automotive industry. To recover the valuable raw materials and components from the battery packs, they must be disassembled and sorted at the end of their service life. Automated processes provide a basis for economic dismantling while minimizing the hazards to employees from high-voltage equipment. Liebherr-Verzahntechnik GmbH uses its tried and tested automation technology for this and is working with research and industry to develop scalable, flexible solutions for the automotive and recycling sectors.
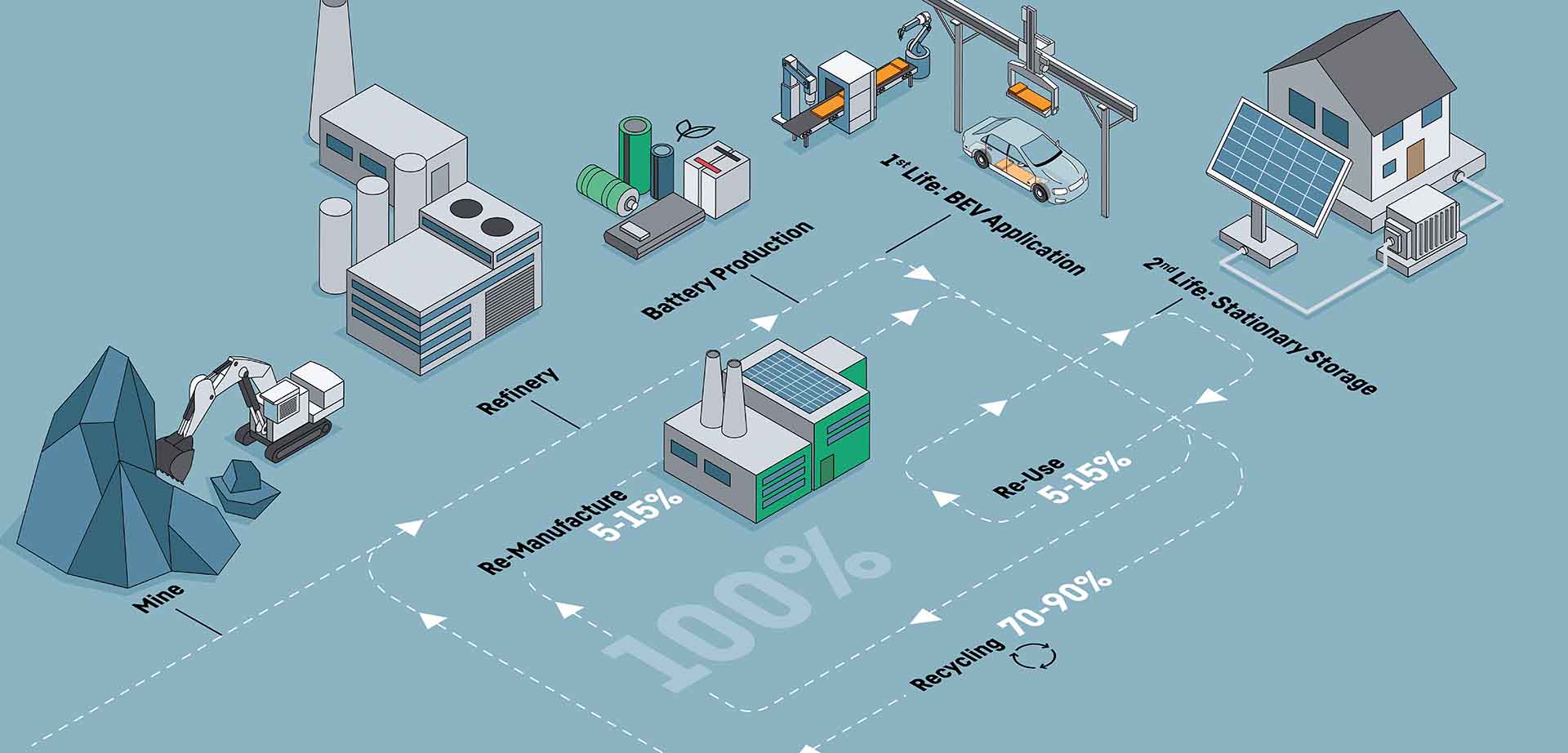
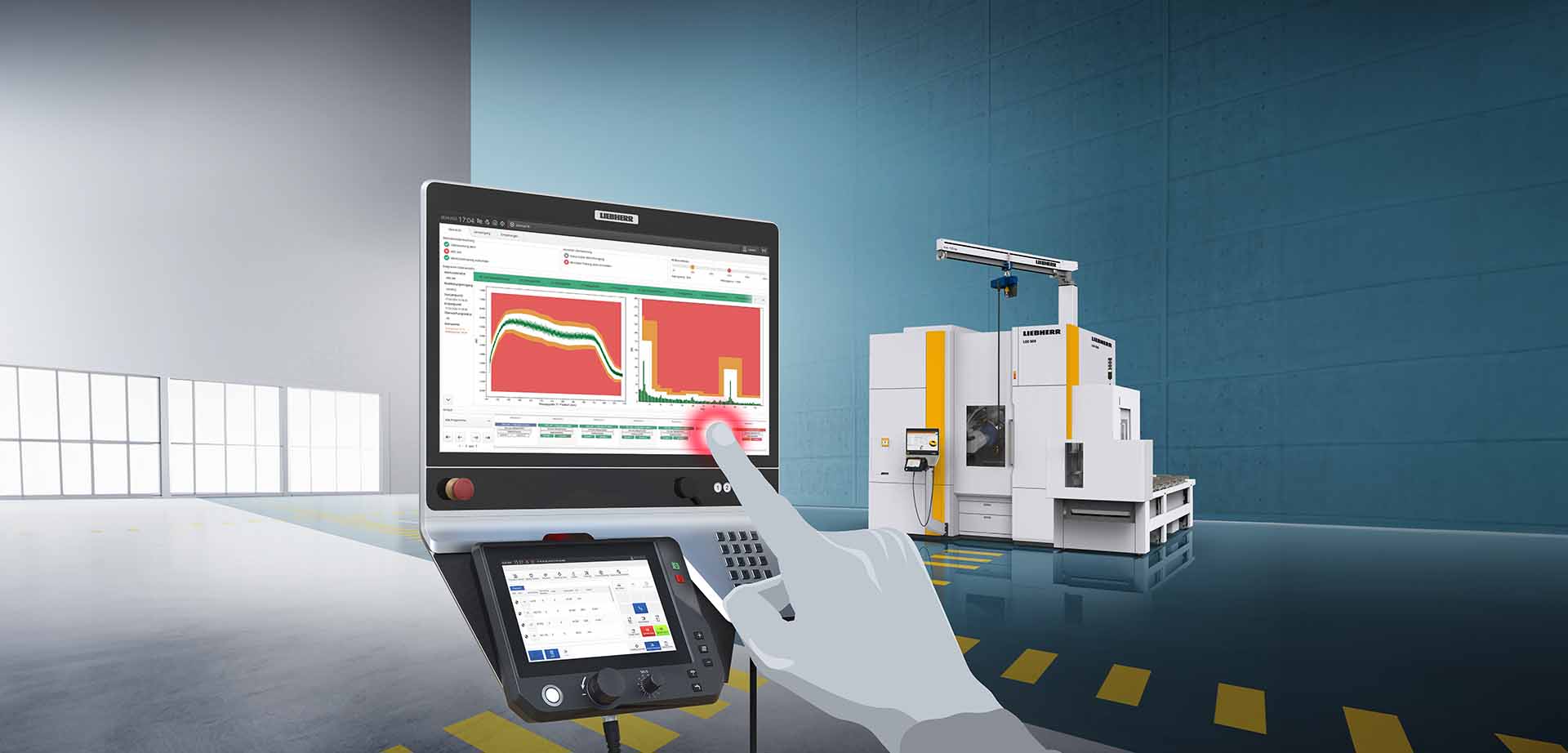
Detecting micro-deviations on gear geometries at an early stage to eliminate increased noise emissions
Inline process monitoring with LHProcessMonitoring
In electric vehicles, the meshing of the gears can cause disruptive gearbox noise excitations. It is therefore becoming increasingly important for automotive manufacturers and suppliers of electric motors to identify and eliminate the causes of unwanted noise at an early stage. With the LHProcessMonitoring software, Liebherr-Verzahntechnik GmbH has developed a tool that detects deviations during gear production. This saves costs and reduces rejects – and is therefore also of interest to manufacturers of conventional gearboxes.
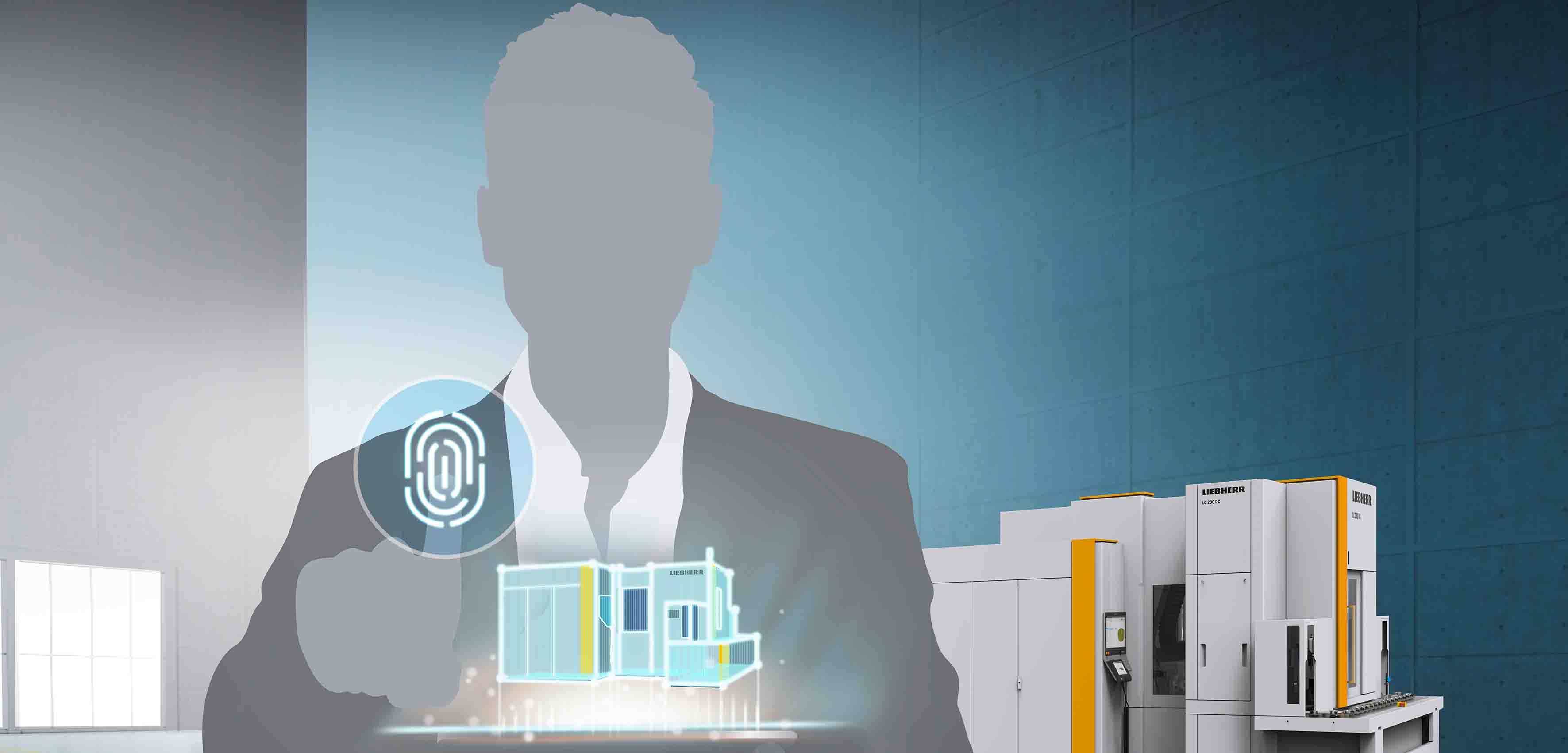
Avoid unplanned downtime and reduce maintenance costs
Condition monitoring with a "digital fingerprint"
Liebherr-Verzahntechnik GmbH now provides its customers with the most important drive and actuator data from a machine – its "digital fingerprint” – as a service to simplify and accelerate machine diagnostics. This makes condition monitoring easier and reduces maintenance costs.
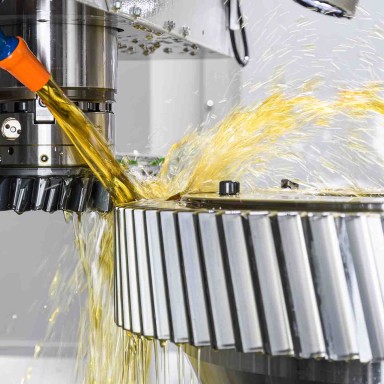
The revised Liebherr gear shaping machine with new features
Robust and even more versatile: the LS 500 E
Gear shaping is a robust and universal process for manufacturing gears – due to the geometries of some gears, no other machining methods are capable of producing the teeth. In order to offer even more versatility in this area, Liebherr-Verzahntechnik GmbH has fundamentally revised and developed its LS 500 E gear shaping machine. A shaping head featuring an electronic helical guide and an interface for an optional chamfering device are now included as standard.
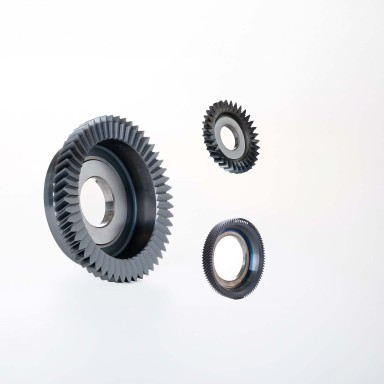
Gear skiving for series and contract manufacturing with the Skiving³ technology package
From “Plug & Pray” to “Plug & Play”
Gear skiving used to be a gear cutting method that was difficult to control due to its complex kinematics, but it now offers a genuine alternative to shaping or broaching. The synergy between machines, tools and processes provided by Liebherr-Verzahntechnik GmbH’s Skiving³ technology package makes it possible to efficiently and flexibly machine an extremely wide variety of workpieces, including in small batch sizes. Skiving³ therefore crucially boosts productivity, quality and cost-effectiveness levels not just in series production, but in contract gear manufacturing as well.
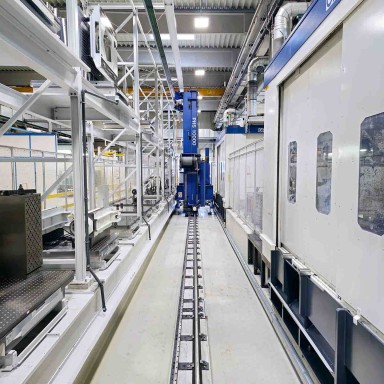
PHS 10000 Pro automates production of large parts at machine manufacturer GROB-WERKE GmbH & Co. KG
Standard, yet individual
With the PHS 10000 Pro pallet handling system from Liebherr-Verzahntechnik GmbH, the machine tool manufacturer GROB in Mindelheim has automated its in-house production of machine components on two 4-axis machining centers and thus increased productivity by around 45%. The challenge here was not only to manage large parts weighing tons, but also a series of additional constraints that required highly individual solutions, as well as project planning where not a single day‘s work could be delayed.
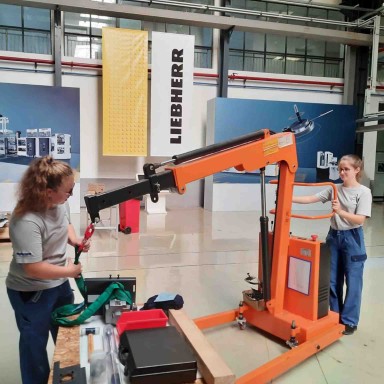
Two Liebherr trainees on assignment abroad in China
“It was such a great experience!”
Julia Stachel and Laura Scheiber completed their training as industrial mechanics at Liebherr-Verzahntechnik GmbH at the beginning of 2024. During their training period, they spent four weeks at the Liebherr plant in Yongchuan, China in August 2023. Here they explain what made them choose China, their experience there and what it is like to suddenly have lots of people wanting to take a photo with you!
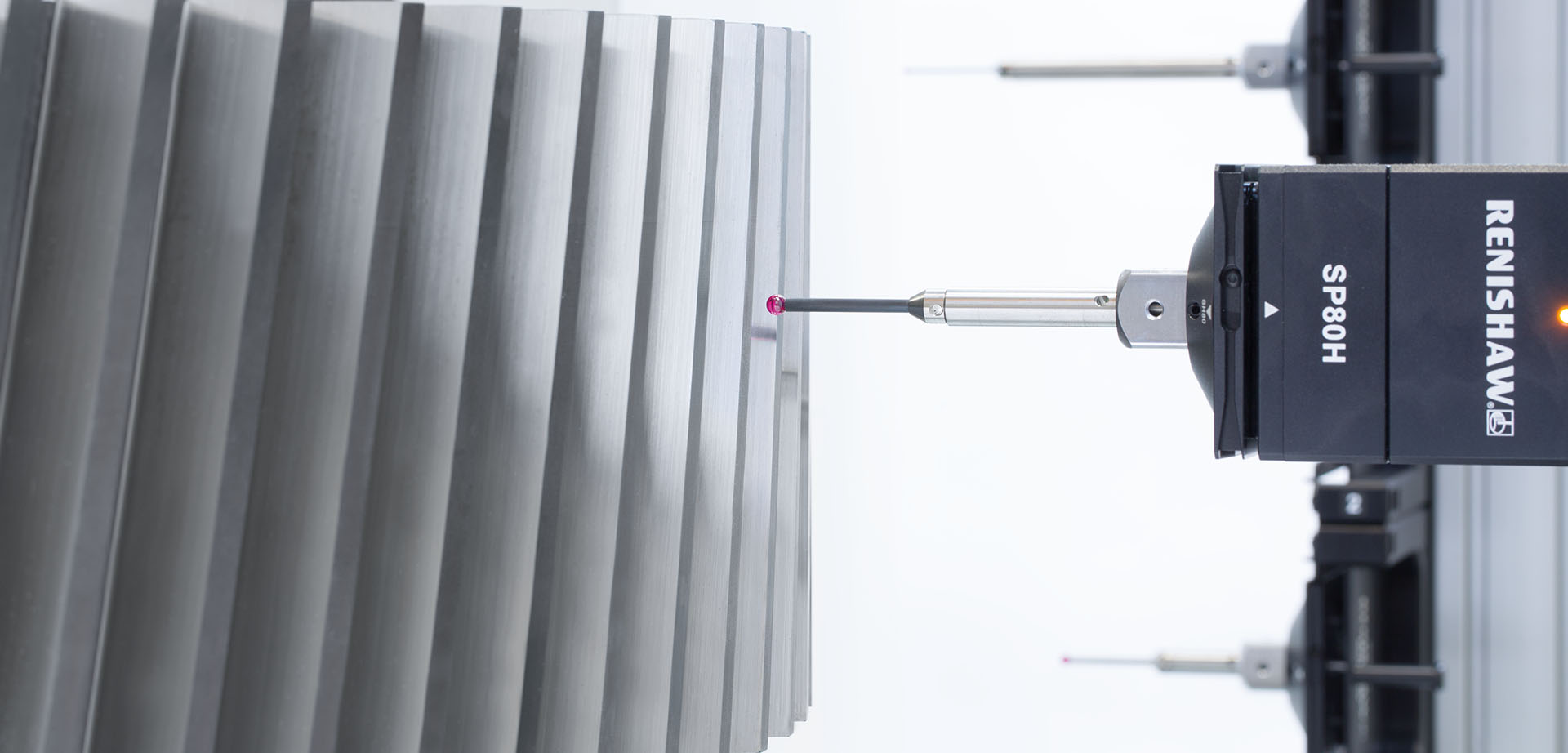
High-precision measuring machines for small and large gears
WGT 1200 optimized for automatic loading of large workpieces
The Liebherr WGT series of gear measuring machines are used in gear manufacturing for a wide range of industries: from the smallest aerospace applications to large gearbox components for wind turbines, tower cranes or commercial vehicles, where some of the gears weigh tons. With the optimized WGT 1200, Liebherr-Verzahntechnik GmbH provides high-precision measurement even for huge workpieces up to a diameter of 1400 mm and a weight of 5 tons.
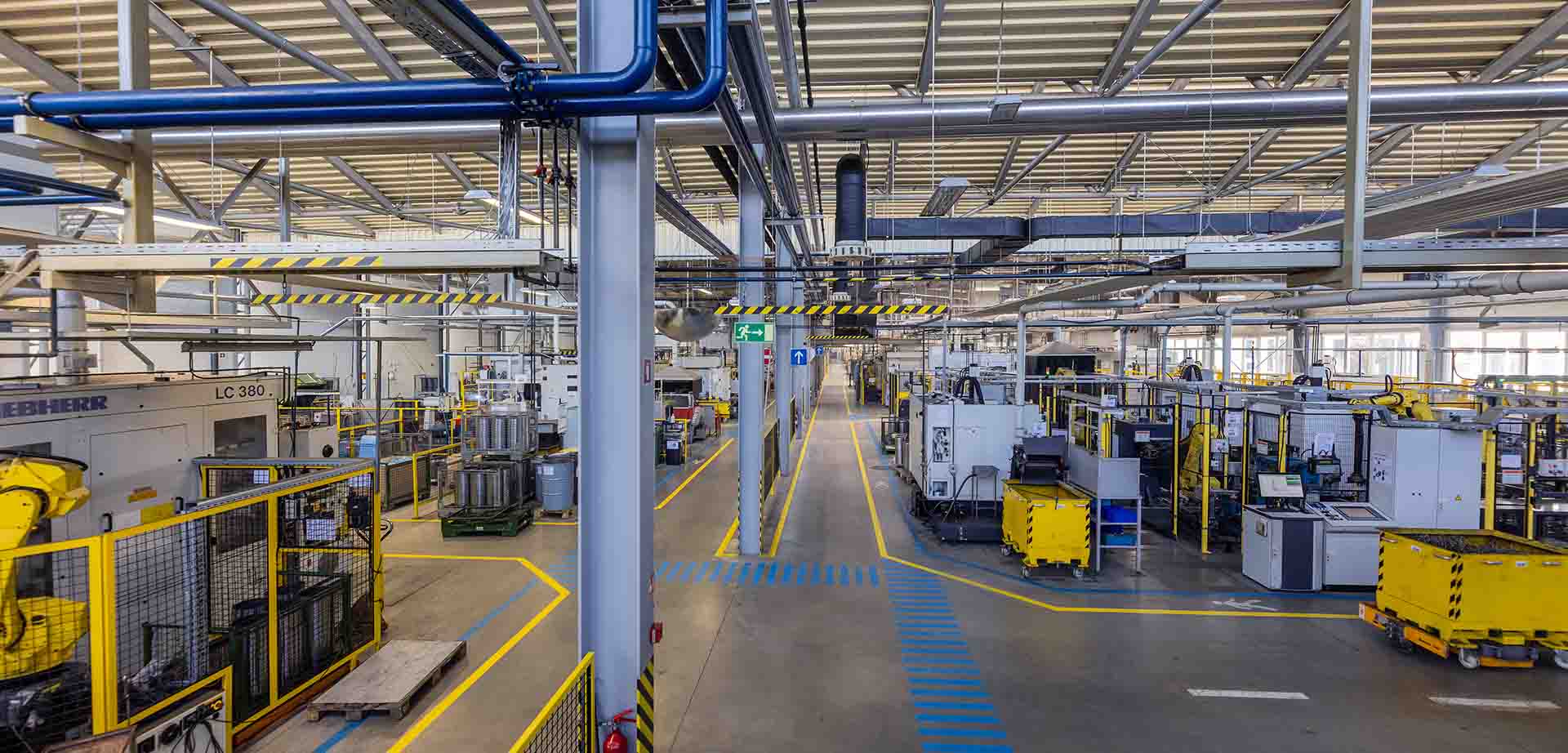
Helping out the Slovenian automotive supplier KLS after the flood disaster
26 severely damaged machines restored to operation
Following the flood disaster in Slovenia in August 2023, Liebherr-Verzahntechnik GmbH provided active assistance for the automotive supplier KLS d.o.o. With commitment, expertise and minimal bureaucracy, the team of engineers performed what seemed an impossible task in just 1,200 work-hours: all of the Slovenian company‘s gear cutting machines – initially thought to be damaged beyond repair – were back up and running before Christmas.