A conversation with Stefan Jehle, Sales Director Automation Systems: The fascination with e-mobility
Stefan Jehle has been part of Liebherr-Verzahntechnik GmbH for over 30 years. He has a wealth of experience in engineering and planning for automation systems and manufacturing plants. After working for many years as an area sales manager, he took over as head of sales for automation systems in 2013. Today, in the context of the mobility revolution, he is taking on a new challenge: e-mobility.
In this interview, we find out what he particularly enjoys about this task, why Liebherr has specialized in the assembly of battery packs, and what the future holds.
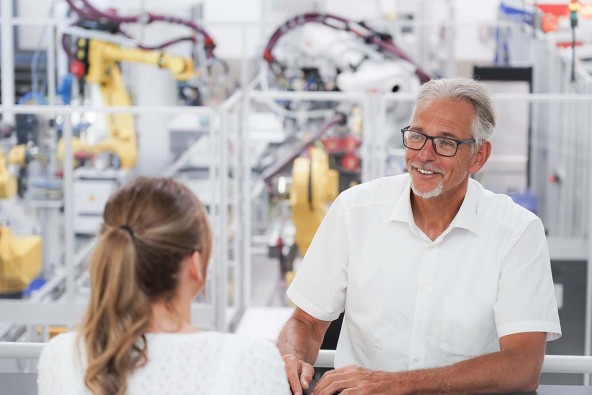
Mr. Jehle, you have dedicated many years to automating the manufacture of the combustion engine. Now the shift to e-mobility is bringing many changes. How are you dealing with this?
For me, it's quite simple: you can spin it any way you want, but e-mobility is a sure thing. Its not just on the cards. It doesn't matter what people's personal opinions are on the subject, or what alternative drive systems may come along in the future. The course has been set politically and economically, and you have to get involved with the technology. Otherwise, you'll miss out on great opportunities in a market worth billions.
So what were Liebherr's first steps into the world of electric motors? To what extent can you draw on your experience in the mass production of combustion engines when producing electric drives, and which challenges are entirely new?
We have of course been keeping an eye on the topic for a long time now. About five years ago, we started a development project with scientific support and the help of consulting companies. We looked at all areas of e-mobility and compared them with our experience, our existing products, and our possibilities. We came to the conclusion that we could see the greatest parallels in battery pack assembly. One of these packs can weigh up to 1000kg. We already had some experience here thanks to our familiarity with transporting heavy parts, for example from the assembly of engine blocks for trucks. We were able to apply everything relating to transport and storage from the existing portfolio: transport systems, conveyor systems, gantry loaders, and pallet handling systems.
What was still missing were the assembly technologies: bolting, gluing, joining, and electrical measurements. For this, our Tech Center provided the perfect space for our development department to get to grips with the new areas of activity. Our customers can also view our systems for themselves on site at our test and trial facility.
Automated plugging of module connectors
Until now, plug connections for the electrical contacting of the modules in the battery pack could only be assembled manually. Together with KOSTAL Kontakt Systeme GmbH, Liebherr is the first manufacturer to develop a plug that can be plugged in automatically. You can find more information in thisarticle.
What would an assembly line for battery packs look like?
The battery consists of a cell, which is assembled into a module. One module is about the size of a car battery. The modules then have to be assembled into a pack. Between 10 and 40 modules can be mounted in a battery tray. Once the modules have been delivered, several steps then follow in our line:
- Applying the heat-conducting paste for cooling the battery
- Installing the module (gripping and screwing it into the tray)
- Electrical contacting of the modules
- Screwing and gluing the cover
- Leak tests / end-of-line check (EoL)
- Further transport to assembly stations or shipment
There is also a special process instead of module to pack, there is also cell-to-pack. Here, the cell is installed directly into the pack. The intermediate step of the module is therefore saved. We have brought a partner on board to connect the cells: Jonas & Redmann focuses on special-purpose machinery and is a specialist in the field of cell and pack. With the combined expertise of both companies, we are a reliable partner for customers in the cell-to-pack sector.
What are the challenges you face when discussing battery pack assembly with your customers and how do you deal with them?
First, of course, there are technical issues that we have to clarify with each customer. What should be done manually? Where does automation make sense? This has to be considered for each process. There are several issues that our customers have to face. We always have to be well prepared for all assembly line technologies in order to be able to provide the customer with first-class technical advice.
Another topic, and major challenge, is how we break into the relatively new field. In the case of the internal combustion engine, we can draw on a long list of projects that we have already implemented. However with assembly lines for battery packs, it's a little more difficult. This is where our Tech Center plays an important role. When our customers visit us on site, we can present our technology in person and assure them that we know what we are talking about. Due to the size of our company, we obviously also have the manpower needed to implement large assembly lines.
What has been your personal highlight in your work in e-mobility so far?
As an engineer, I'm particularly excited by the new technical challenges. Every battery looks different. There is no magic formula for how to assemble a battery. In each project you have to examine the process technologically and select the right assembly step in each case. Of course, we try to use standardized assemblies from which we then tailor specific applications for our customers. But every project is different and we learn something new with each one.
How do you like working on this technological change at Liebherr?
Our company structure means we have short decision-making paths. That's especially important when you enter into a new field. If it took a long time for decisions to be made here, the product would never get off the ground. Thanks to the size of our Group, we have the opportunity and the space to tackle projects of these dimensions. In other circumstances, we would certainly have less leeway in this respect.
For me personally, it's great: I was involved with the combustion engine for 30 years and have now been given another opportunity to tackle a new topic and challenge.
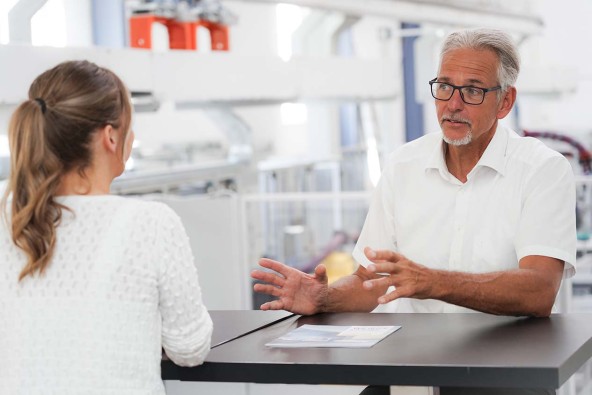
Can you give us a brief glimpse into the future of mobility?
As I mentioned before, the topic of e-mobility is here to stay. However, I think the world will be a lot more diverse in the future. It will not consist of just one combustion engine, as it does now. We will see a variety of drives: electric with a battery, fuel cells, hydrogen.
We are also already thinking beyond the production of the battery. For example, as part of a research project, we are currently also looking at recycling, in collaboration with institutes. We are investigating how best to recycle the battery so that we can recover the maximum amount possible of the raw materials used. This is also an exciting topic for the future in the field of automation.