Innovative and user-friendly
The handling of deep foundation machines is particularly demanding, especially since a lot of the work is performed outwith the operator’s field of vision. The Liebherr control system has numerous useful functions and various assistance systems to simplify each piling and drilling application. They ensure quick and precise working cycles, increase safety on the jobsite and minimize wear on the machine.

Joystick control for all machine functions
All machine functions are carried out using the two joysticks. Furthermore, several movements can be made simultaneously.
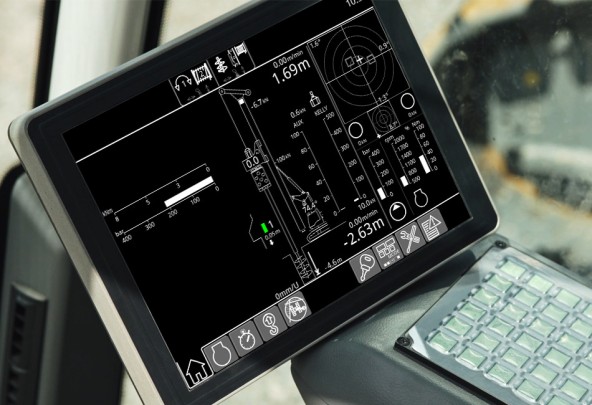
Everything at a glance
The most important machine data are displayed on the control monitor with touchscreen. These vary depending on the configuration of the machine and the operation mode.
Drilling assistance systems
Cruise Control for all main functions: depending on the mode of operation, the operator can preselect defined values for the rope crowd system, as well as the speed and torque of the rotary drive. After activation, the drilling assistant functions similarly to a cruise control in a car: the set values are held constant by the machine control system.
Single pass method
The installation of cast-in-place piles using continuous flight augers, full displacement tools or double rotary drills belong to the most efficient methods in deep foundation work. Our specially designed assistant system automates the continuous drilling and extraction of the drilling tools and ensures a high-quality result.
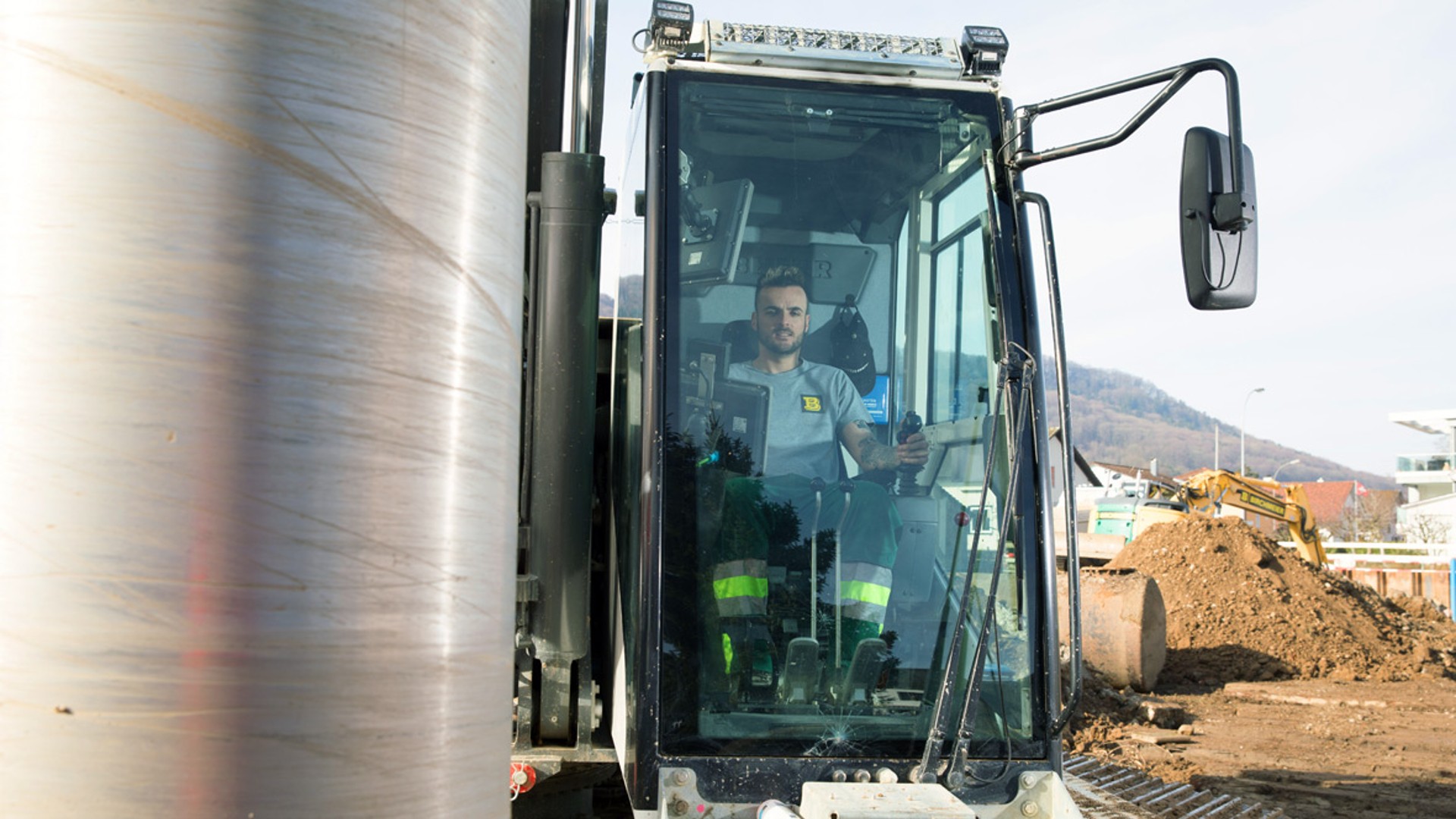
Drilling assistant for single pass method
Kelly Drilling
A range of useful operator assistance systems are also available for the most common drilling method, Kelly drilling, in order to optimize the drilling cycles.
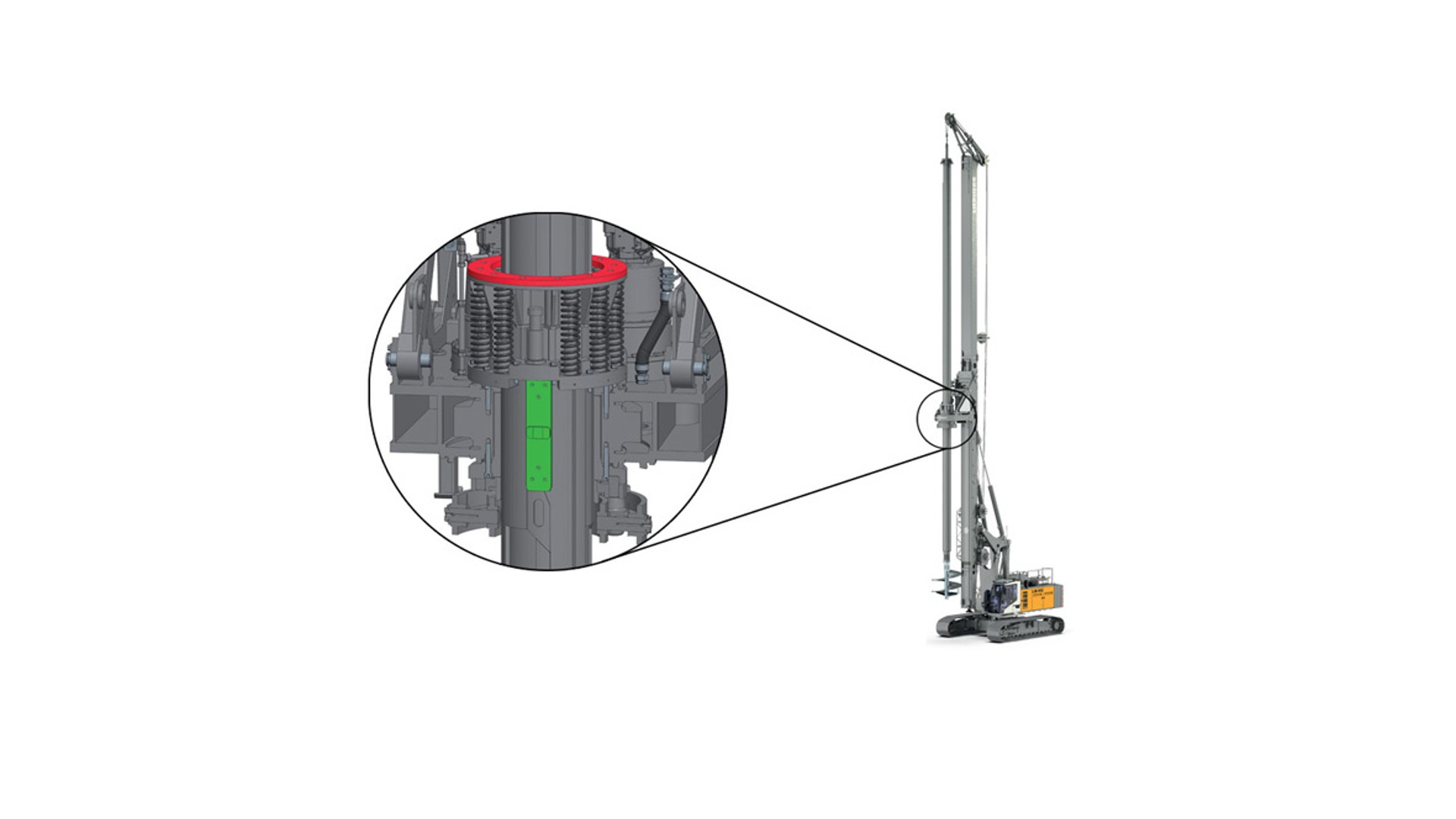
Kelly visualization
Increased pull force
Should the pull force of the crowd winch not be sufficient, the main winch can be connected.
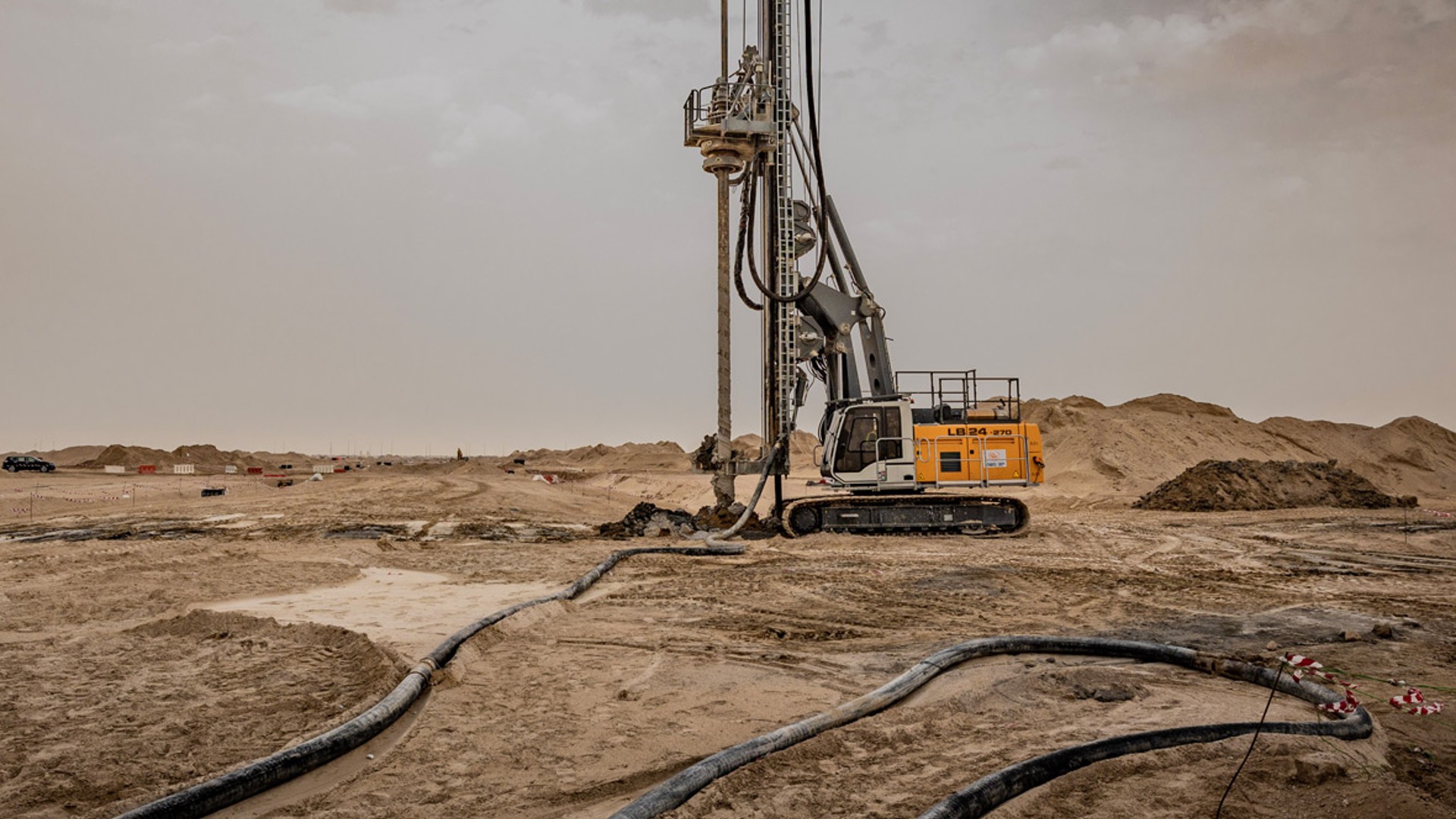
Crowd Booster
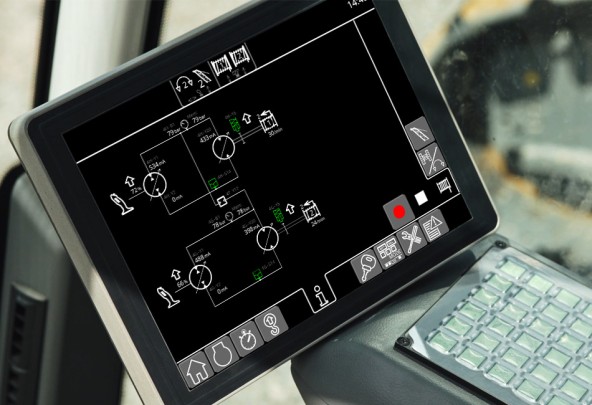
Diagnosis monitor
The diagnosis monitor observes the vital functions of your machine. Sensor signals, electrical control and the hydraulic pressure of valves and pumps of all main components are displayed on the diagnosis monitor:
- Swing gear and crawlers
- Kelly and crowd winch
- Rotary drive
This means errors can be quickly identified and so standing time kept to a minimum.