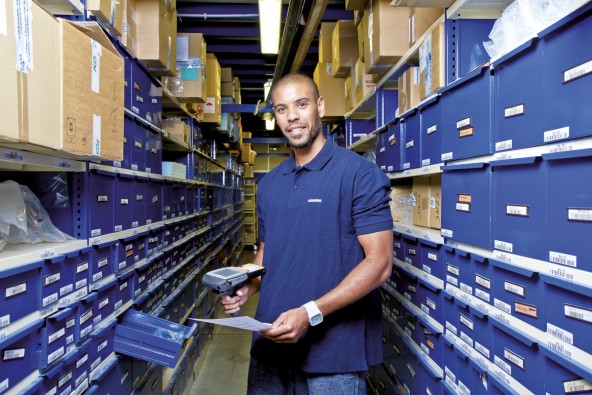
Experience lifecycle support
Liebherr offers all kinds of services in the shortest possible time in almost all places in the world. These services range from assembly works, commissioning and repairs as well as routine maintenance up to deliveries of spare parts and component upgrades. The company also provides tailored solutions to meet emerging industry standards and environmental regulations.
As a global leader in rail vehicle equipment, Liebherr specializes in HVAC and hydraulic actuation systems, backed by a worldwide service network for fast, localized support. Liebherr's diverse expertise ensures innovative, independent solutions tailored to the railway market’s evolving needs.
Design and development
Liebherr is committed to designing the next generation of services for customers and equipment alike. Drawing on system knowledge gained from millions of hours of real-life data, equipment is developed to be reliable, easy to test and maintain, and designed to exceed expectations. By pairing customer support with engineering design expertise, innovative ideas are combined with field experience to create cost-optimized systems that meet the demands of customers and today’s competitive environment.
Manufacturing
Liebherr continuously enhances manufacturing and production methods to meet future demands while preserving the tools, machinery, and expertise needed to support railway operations long after production ends. Flexibility, efficiency, quality, responsiveness, and sustainability are integral to every manufacturing process, with each site committing to ambitious environmental impact reduction targets. Close collaboration with customers ensures precise planning, anticipation of needs, and delivery of services exactly where they are required.
Entry-into-service
At Liebherr, entry-into-service is more than just the delivery of new equipment—it’s about ensuring a seamless start, whether operating a new or existing train. The company's entry-into-service package includes:
- Training sessions to prepare maintenance personnel and support the global field service network
- Distribution of technical documentation for easy reference
- Recommendations for initial provisioning to optimize system performance
- Guidance on tools and parts required for system maintenance
- Operational monitoring to assess component behavior in real-world conditions
This structured and proven framework is reinforced through regular and direct communication, ensuring that every step meets the customer's needs.
Operations
Liebherrs’ global customer service network is staffed by highly trained experts, dedicated to providing local support. Regional service stations act as focal points, offering a wide range of services tailored to customer needs, including:
- Spare parts management
- Service solutions
- Technical support
Service stations are strategically located to ensure proximity and rapid response in:
- Austria
- Canada
- China
- France
- Germany
- India
- Switzerland
- United Kingdom
- USA
Spare parts and service solutions
Spare parts management
Recognizing the unique needs of every customer, Liebherr offers customized spare parts solutions including:
- On-demand supply
- Managed fixed-price spare parts lists
- Strategic stocking at customer sites
- Short- and long-term availability
- Fixed annual cost packages
These flexible options can be mixed and matched to suit specific applications, ensuring optimal product support and peak performance at the lowest cost.
Service solutions
From design to retirement, Liebherr’s cradle-to-grave approach guarantees top system performance throughout deployment in passenger service. Services are shaped to meet customer needs through close collaboration with suppliers, customers, and operators. Options include:
- Field technician service on demand
- Fixed-rate agreements
- Route-to-market arrangements
- Guaranteed response times
- On-car/off-car support
- Full-service packages at a fixed annual cost
These solutions are designed to ensure reliability, efficiency, and customer satisfaction.
Enhancements
Liebherr’s in-service engineers focus on developing innovative repair solutions and product enhancements to reduce maintenance costs, meet evolving requirements, and exceed customer expectations. Experienced teams provide dedicated support to implement enhancements seamlessly, offering planning tools and services designed to minimize operational impact.
Energy efficiency
Liebherr supplies CO₂ sensors to ensure a sustainable reduction of energy consumption
The sensors measure the CO₂ content of the air in the car interior. Based on this signal, the respective occupancy level of the passenger area can be reliably determined and the fresh air supply can be regulated as required, increasing passenger comfort. The energy consumption is reduced and the operator saves operating costs. The occupation-dependent fresh air control system from Liebherr therefore contributes significantly to the improvement of the economic performance on board a train.
Downloads
A global network
We are always close to where your needs are
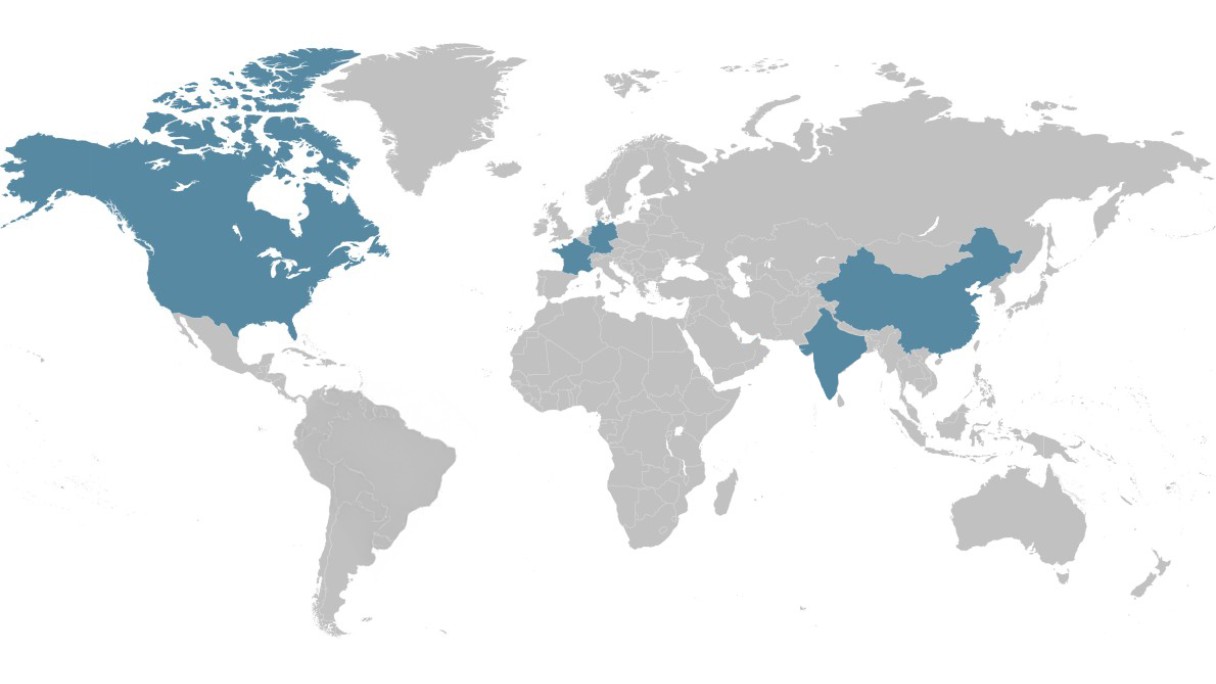
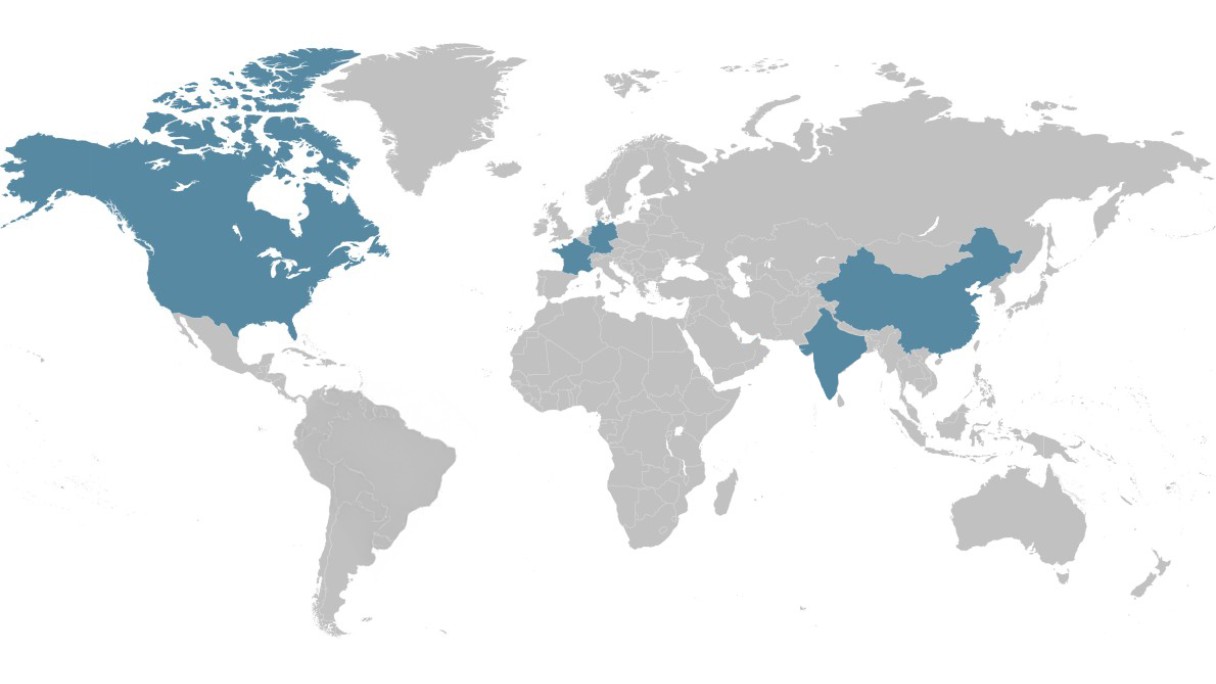
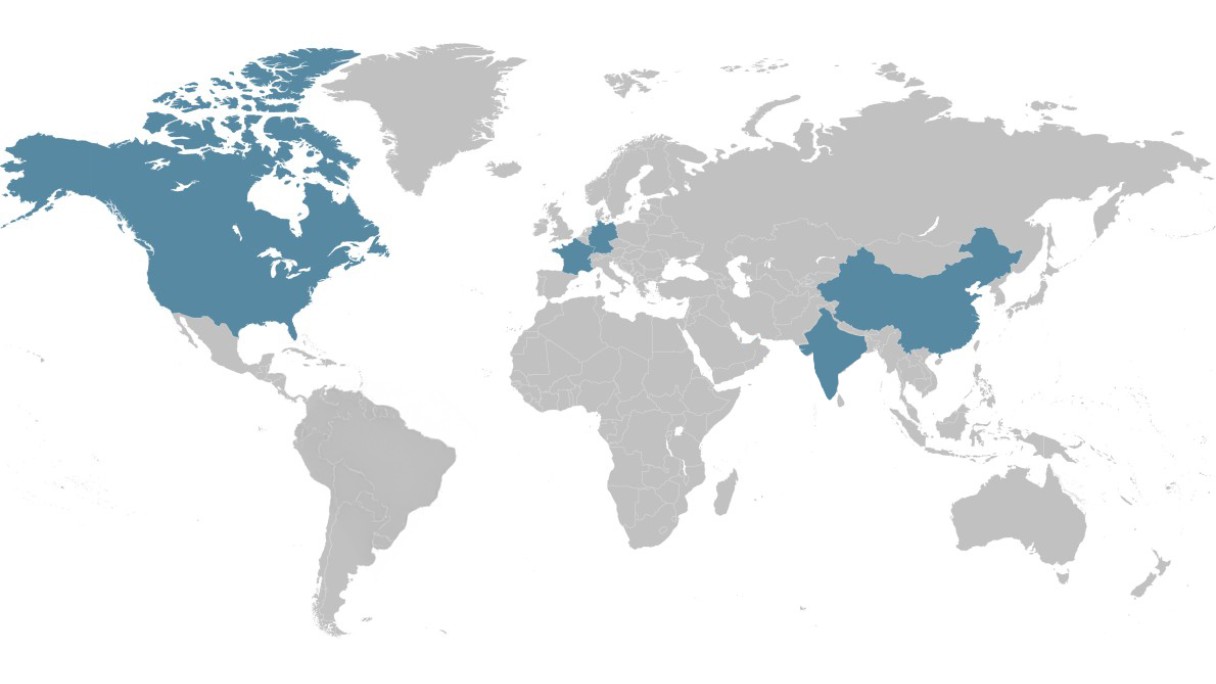
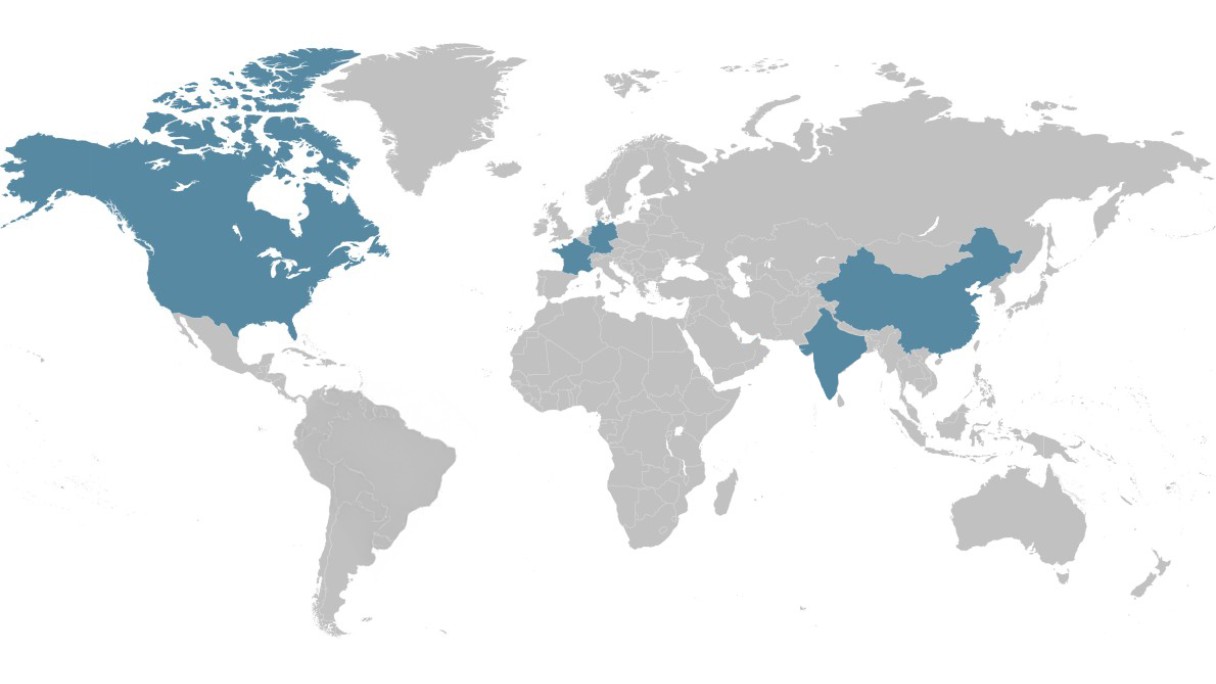
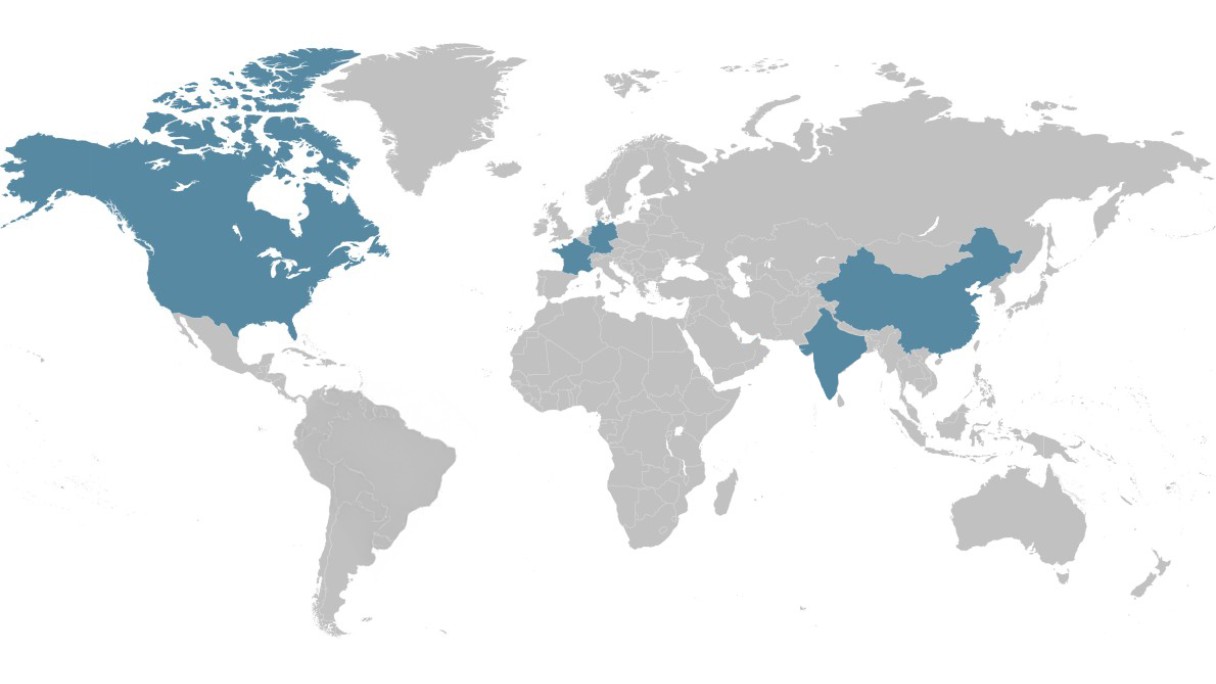
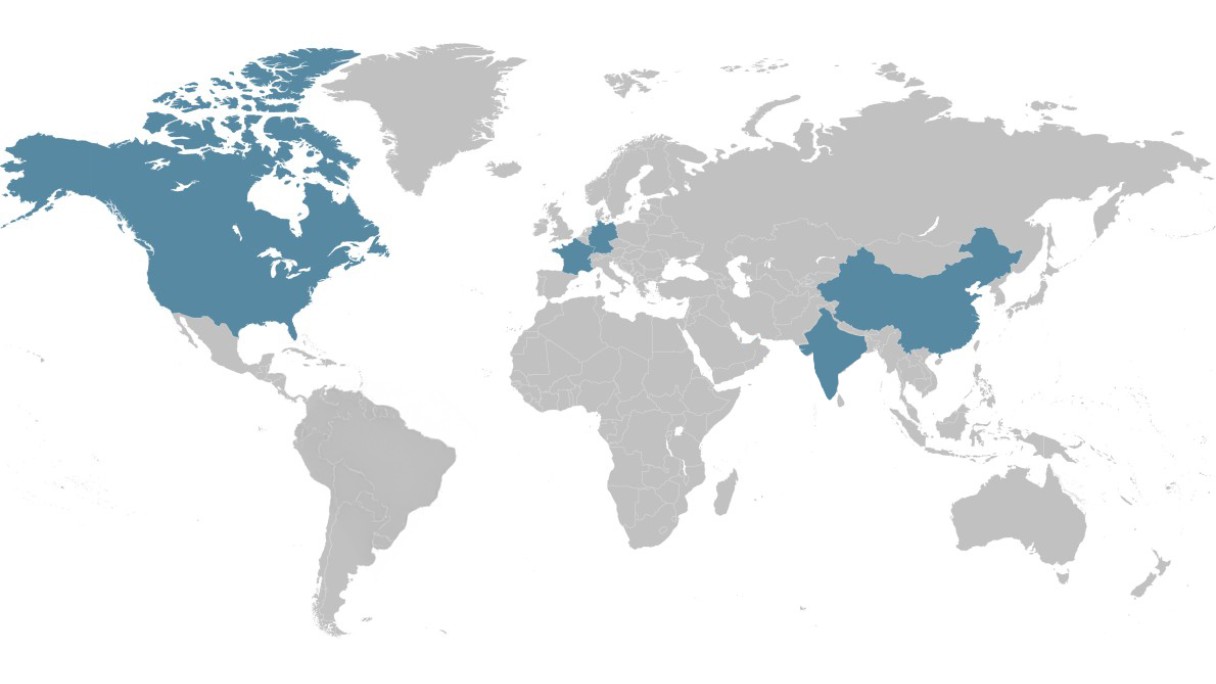
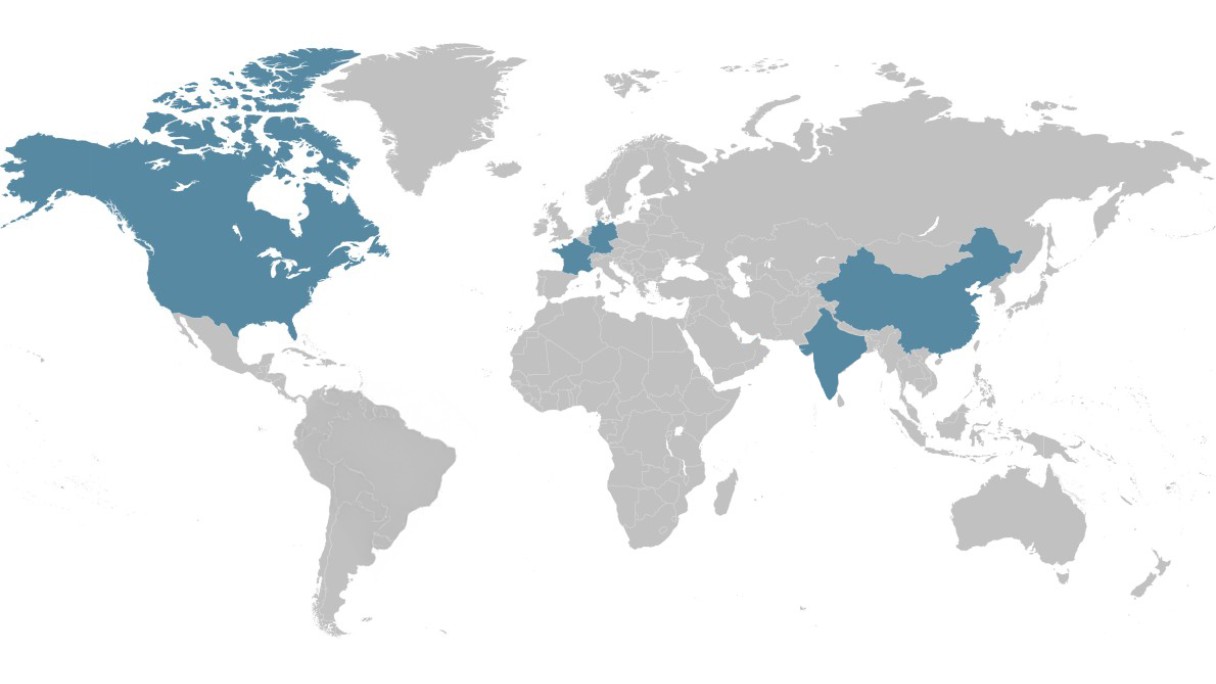
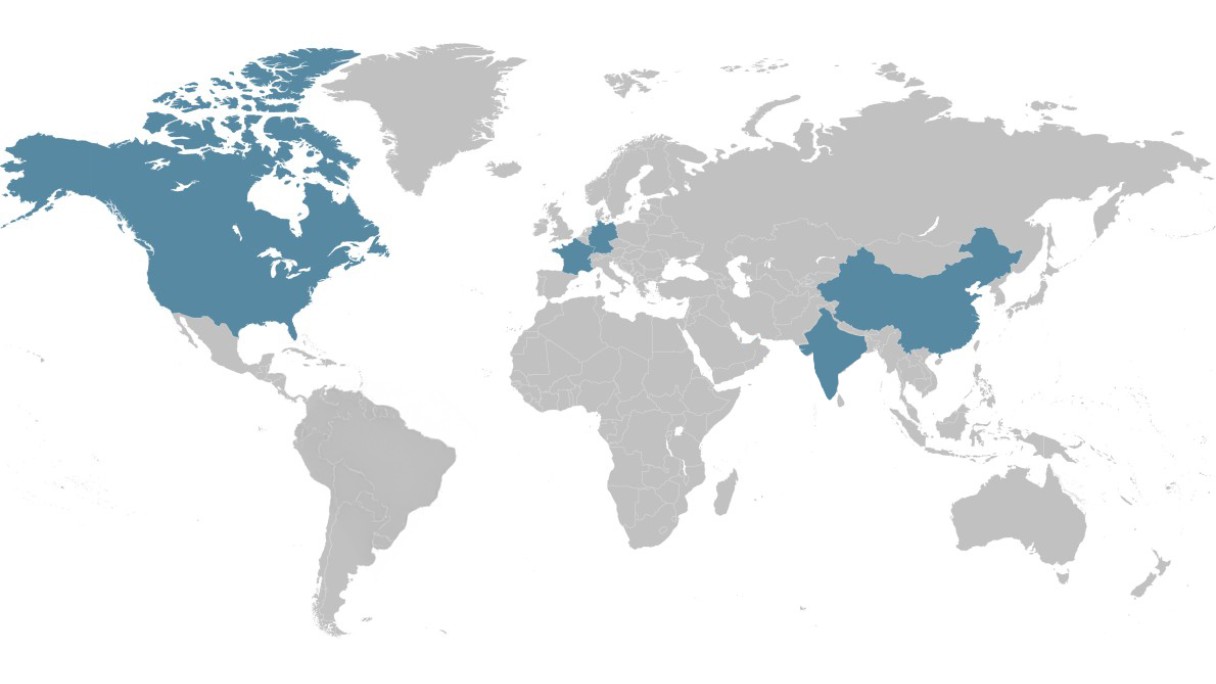
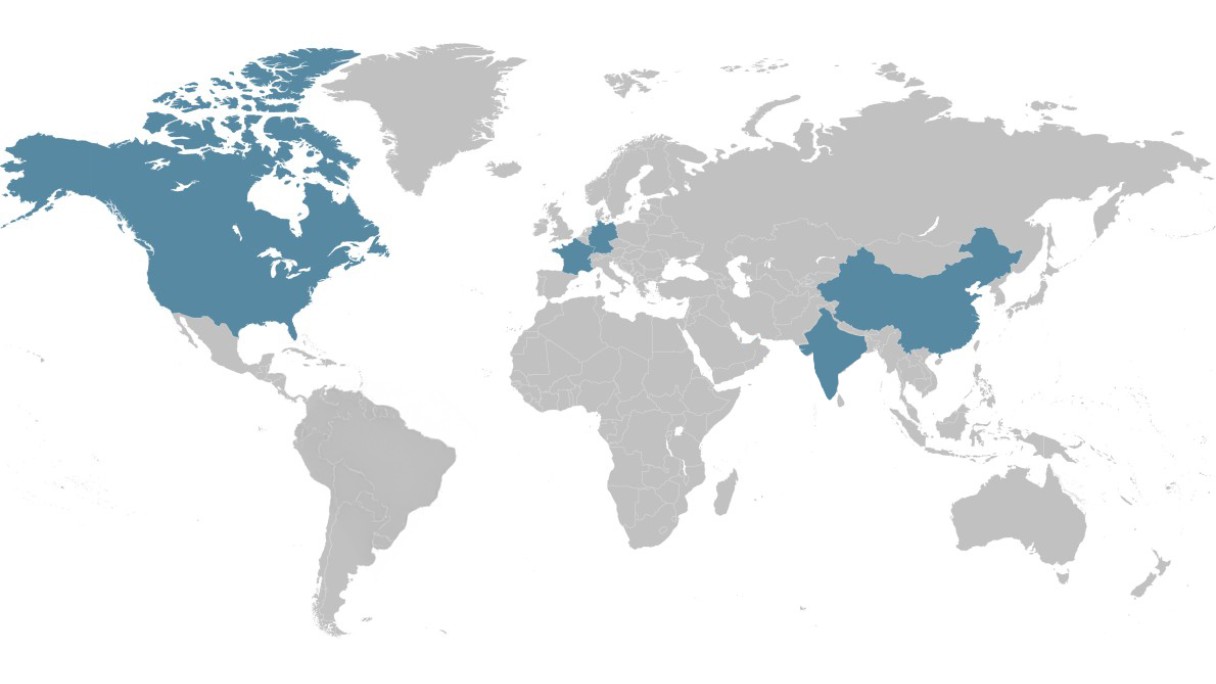
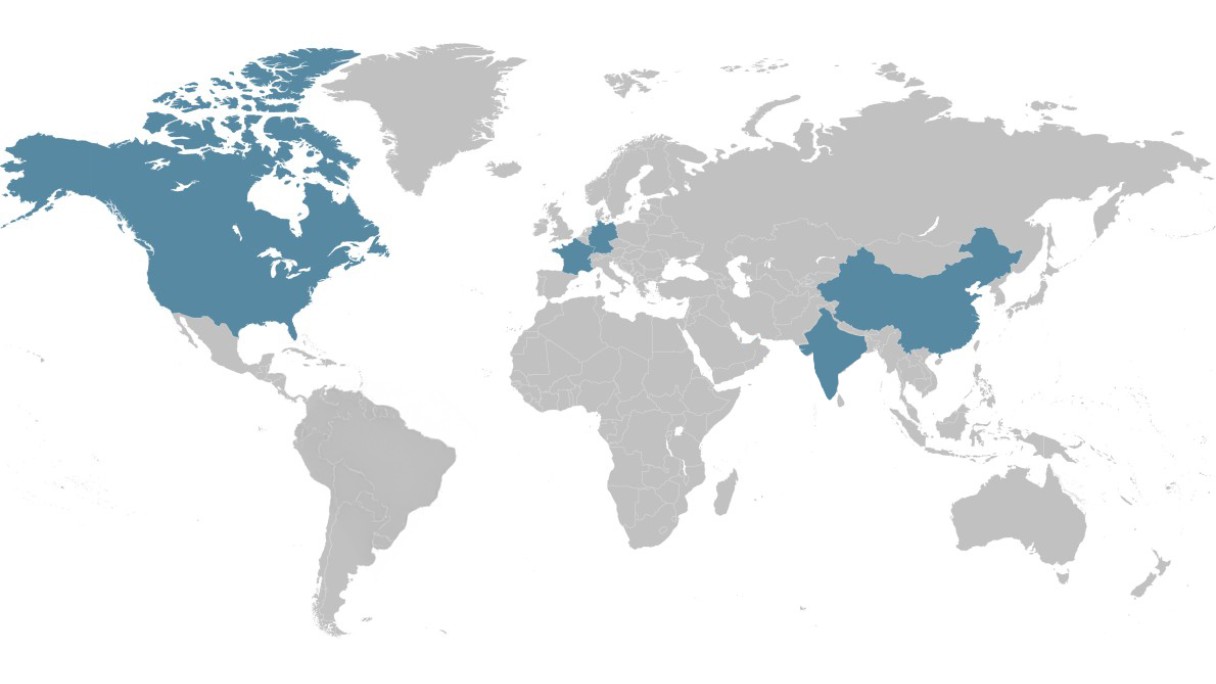
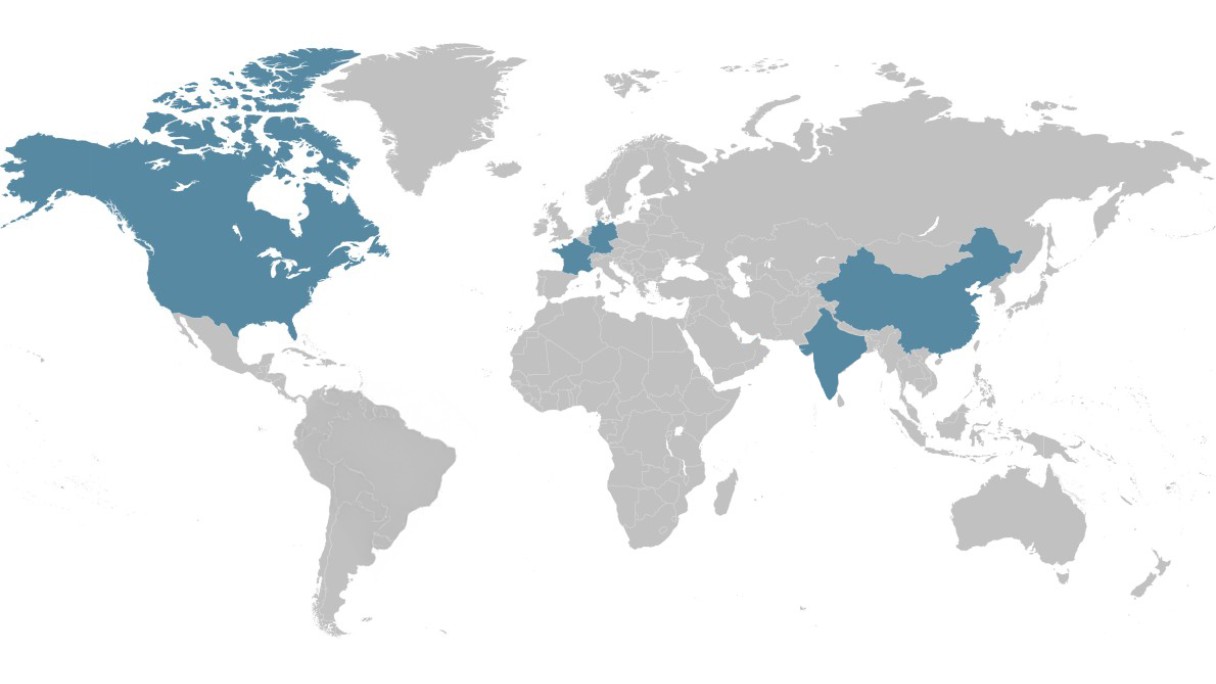
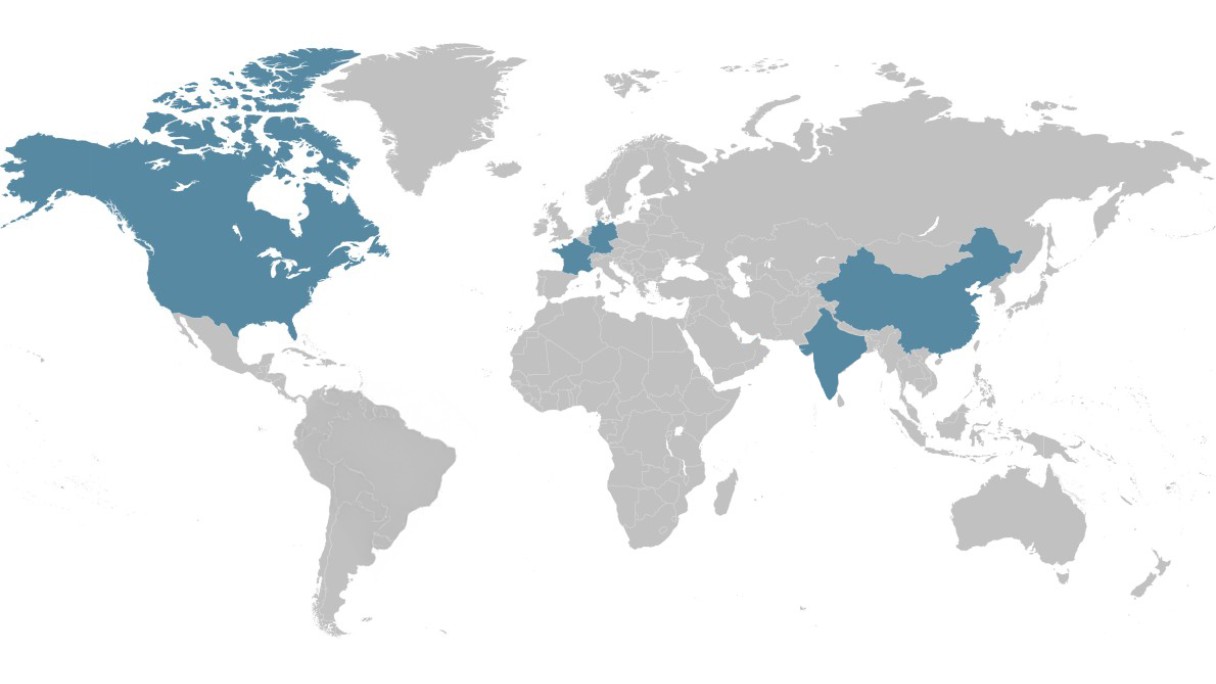
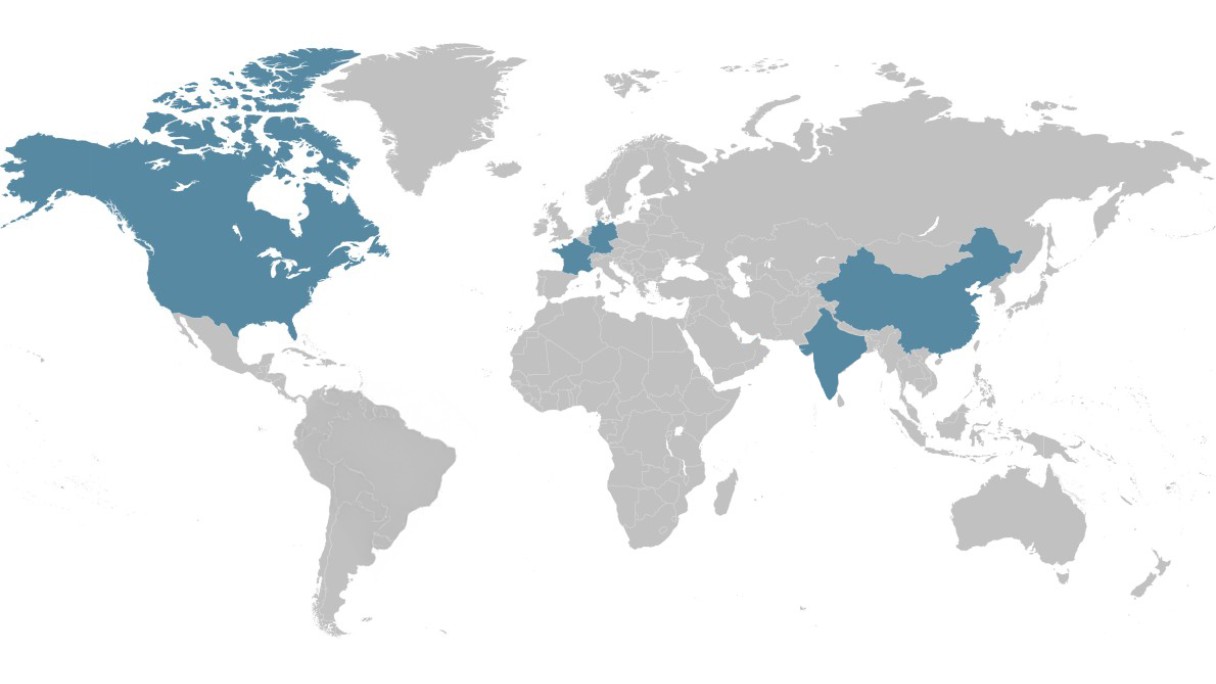
Europe
Germany
Find out more
France
Find out more
Austria
Find out more
Switzerland
Find out more
United Kingdom
Find out more
Asia
China
Find out more
India
Find out more
Americas
USA
Find out more
Canada
Find out more