The Liebherr Mining Remanufacturing Program
The Liebherr Mining Remanufacturing Program enables customers to significantly reduce the total lifecycle cost of Liebherr mining equipment without compromising quality, performance and reliability. It is also an important way for Liebherr and its partners to contribute to environmental sustainability through substantial material and energy savings.
Over the course of a mining machine’s life, major components must be replaced to ensure continued safety, productivity and reliability. Liebherr Mining component exchange and repair programs offer customers an OEM alternative to purchasing brand-new replacement components, enabling customers to achieve lowest possible equipment lifecycle costs without compromising quality, performance or reliability.
The remanufacturing process
All components returned to Liebherr are quickly evaluated based on simple and clear criteria to determine the price of the replacement component. From here the remanufacturing process begins.
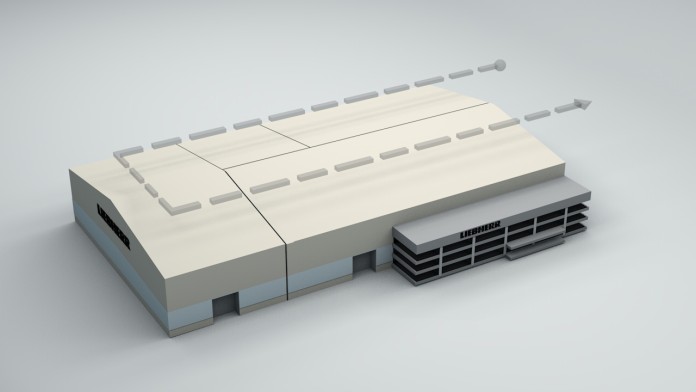
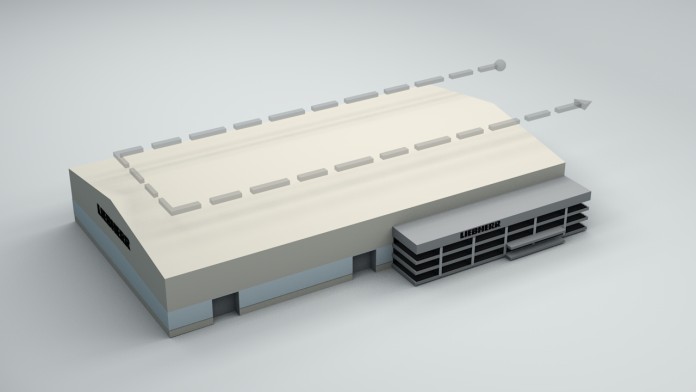
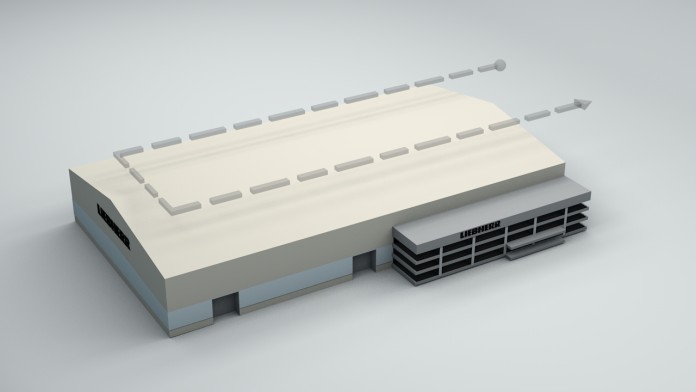
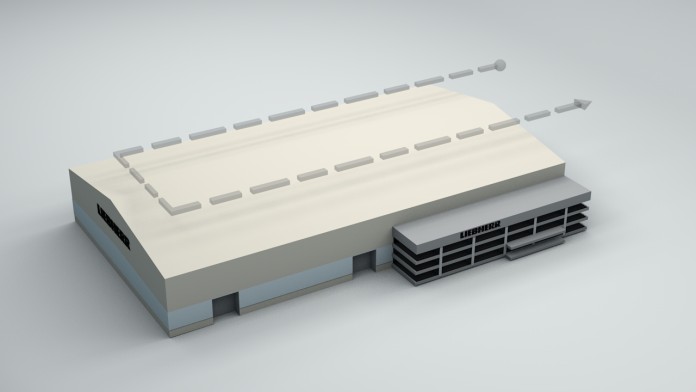
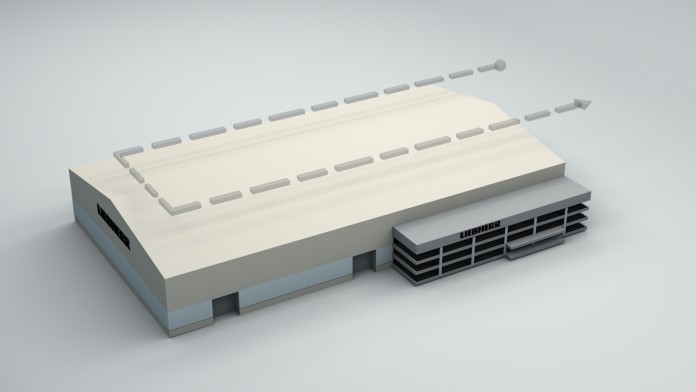
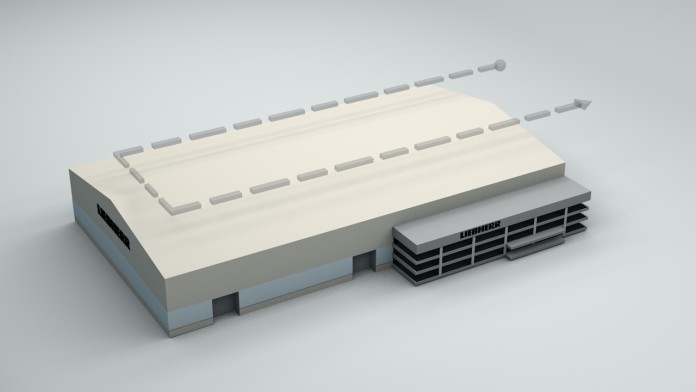
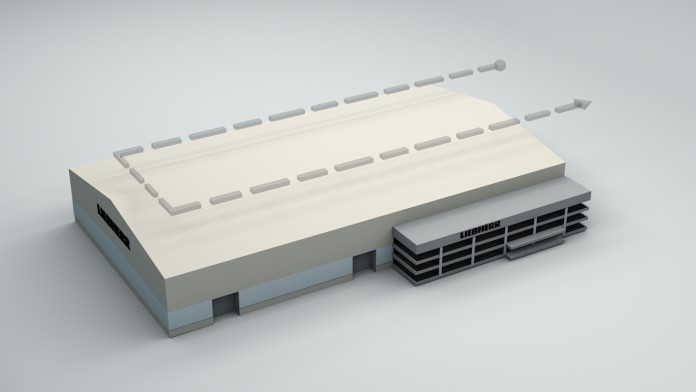
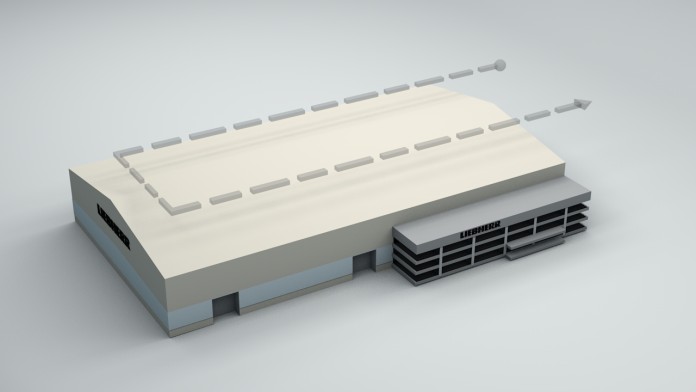
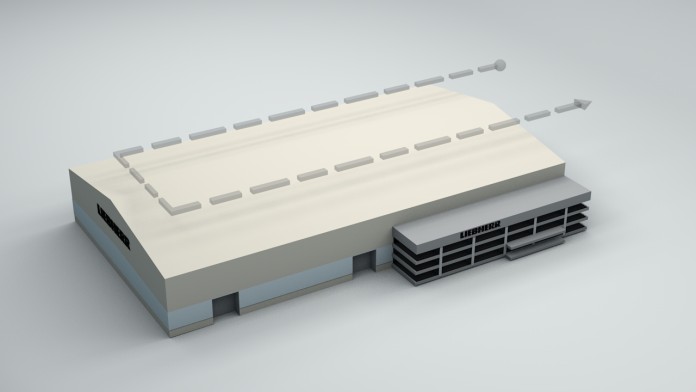
1. Disassembly
Find out more
2. Cleaning
Find out more
3. Inspection
Find out more
4. Salvage
Find out more
5. Warehouse
Find out more
6. Assembly
Find out more
7. Testing
Find out more
8. Completion
Find out more
Components
Liebherr offers a comprehensive range of remanufactured and repaired components for all types of Liebherr Mining equipment.
Mining trucks | Mining excavators | Crawler tractors |
Alternators | Travel drives | Hydraulic pumps & motors |
Wheel drives | Splitter boxes | Splitter boxes |
Electric motors and alternators | Swivelling drives | Travel drives |
Front wheel assemblies | Hydraulic cylinders | Hydraulic cylinders |
Hydraulic pumps & motors | Hydraulic pumps & motors | Diesel engines |
Suspension cylinders | Sprockets and Idlers | |
Hydraulic cylinders | Track tensioners | |
Brake calipers | Diesel engines | |
Accumulators | Radiators | |
Radiators | Rollers |
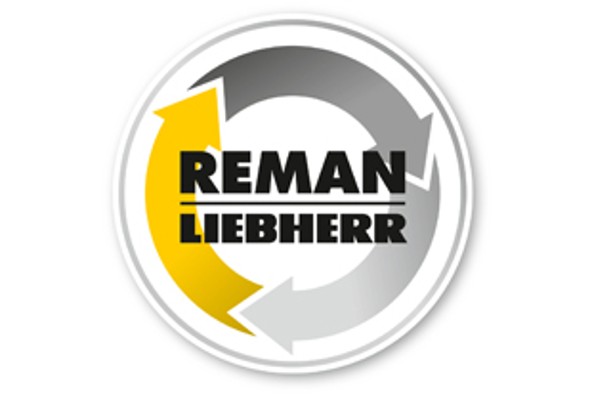
Video
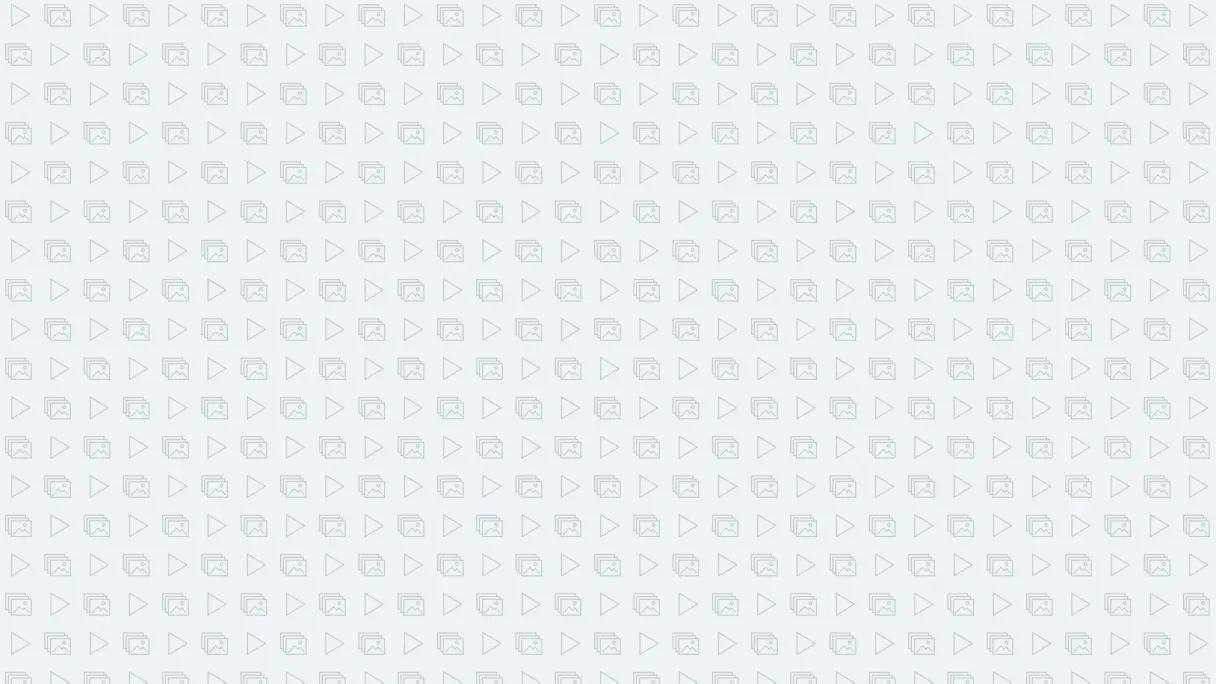
This video is provided by Google*. When you load this video, your data, including your IP address, is transmitted to Google, and may be stored and processed by Google, also for its own purposes, outside the EU or the EEA and thus in a third country, in particular in the USA**. We have no influence on further data processing by Google.
By clicking on “ACCEPT”, you consent to the data transmission to Google for this video pursuant to Art. 6 para. 1 point a GDPR. If you do not want to consent to each YouTube video individually in the future and want to be able to load them without this blocker, you can also select “Always accept YouTube videos” and thus also consent to the respectively associated data transmissions to Google for all other YouTube videos that you will access on our website in the future.
You can withdraw given consents at any time with effect for the future and thus prevent the further transmission of your data by deselecting the respective service under “Miscellaneous services (optional)” in the settings (later also accessible via the “Privacy Settings” in the footer of our website).
For further information, please refer to our Data Protection Declaration and the Google Privacy Policy.*Google Ireland Limited, Gordon House, Barrow Street, Dublin 4, Ireland; parent company: Google LLC, 1600 Amphitheatre Parkway, Mountain View, CA 94043, USA** Note: The data transfer to the USA associated with the data transmission to Google takes place on the basis of the European Commission’s adequacy decision of 10 July 2023 (EU-U.S. Data Privacy Framework).Major components account for up to 80% of customers' mining equipment maintenance costs. Liebherr offers customers a variety of component exchange and repair programs to provide maintenance budget flexibility without compromising quality, performance and reliability.
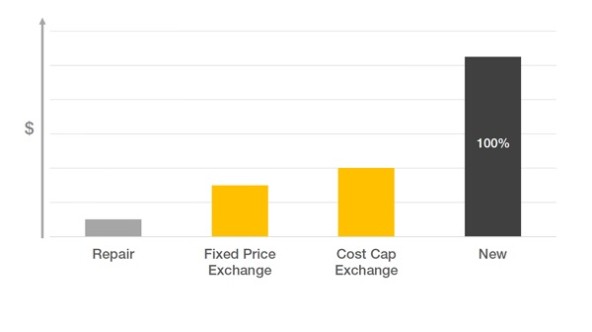
Program cost comparison
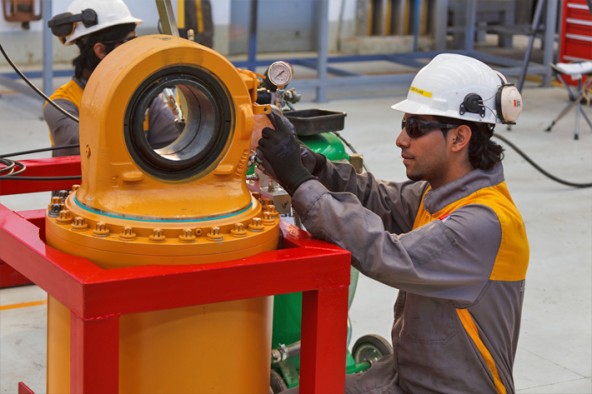
Liebherr remanufactured parts and components are prepared under Liebherr's strict standards.
The Repair program is based on a minimum standard repair scope which is expanded as per condition of the core. It provides customers transparency into the cost of repair as well as the lowest upfront repair cost on first-turn components. Customers maintain their own inventory of swing components in order to minimize machine downtime while the component is being repaired. Each “RX” component repaired under the program comes with a full new component warranty, provided the customer agrees to the Liebherr proposed repair scope. If the customer deviates from this scope, Liebherr will only warrant workmanship and parts replaced.
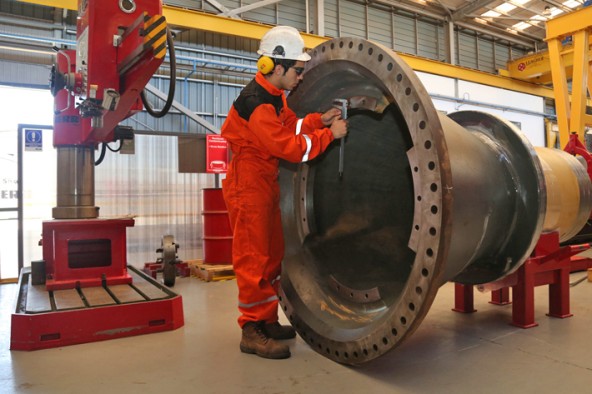
The Exchange program offers customers added-value through the delivery of an exchange component prior to the removal and return of the customers' core. This minimizes customers' downtime and eliminates the need to invest in swing component inventory. Pricing per exchange component is fixed based on simple core return criteria, allowing customers to better forecast maintenance costs regardless of the actual repair scope of each component. Even components which have failed in operation or that are beyond economical repair are eligible for a credit on the returning core. In addition to a full new component warranty, which also applies to “SX” remanufactured components, customers are also guaranteed the latest technical version to further ensure quality, performance and reliability.
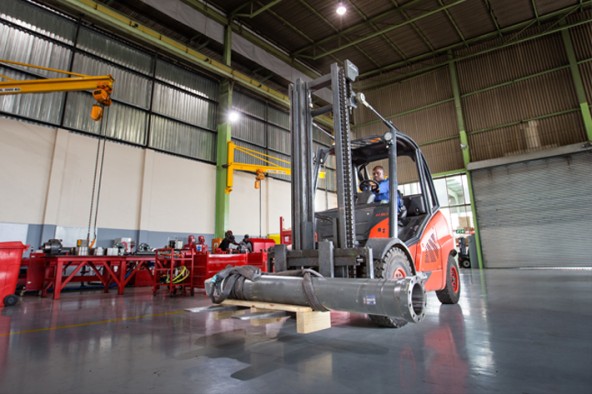
The Cost Cap Exchange program also uses new and remanufactured “SX” components and provides customers the same benefits of the Fixed Price Exchange program plus an additional extended pro-rata warranty, which guarantees, or "caps", the component cost per hour. Beyond the pro-rata warranty period, the customer has the opportunity to further reduce the cost per hour by continuing to operate the component. This program gives customers the highest degree of certainty when planning component maintenance budgets and the lowest risk for costs of early failures. The Cost Cap Exchange program is only offered to customers with best-practice and verifiable maintenance practices.
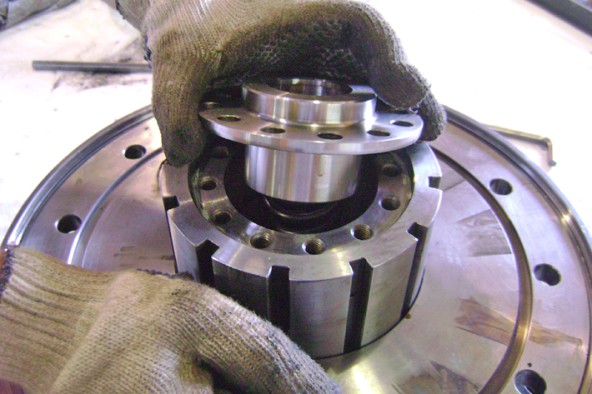
Depending on the location and size of a customer’s fleet, Liebherr can also provide a repair or exchange program tailored to customers’ specific requirements. Contact your local Liebherr Customer Service representative for more details.
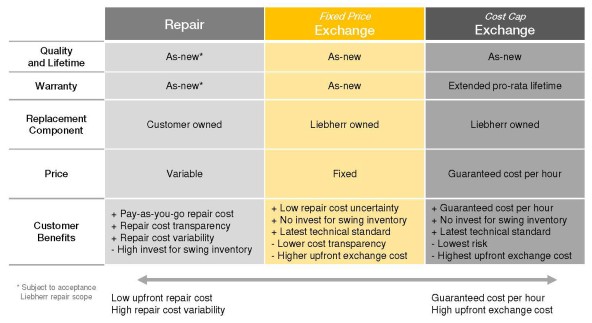
Program overview
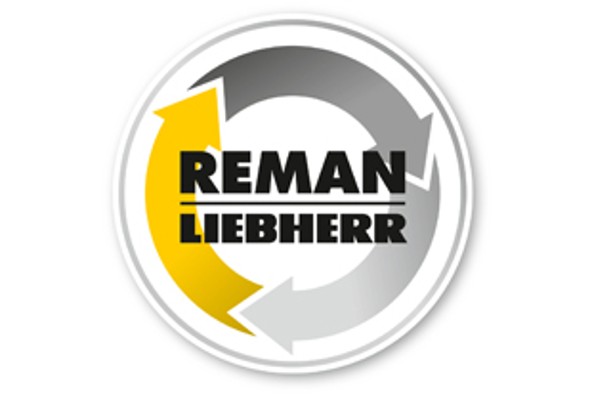
Video
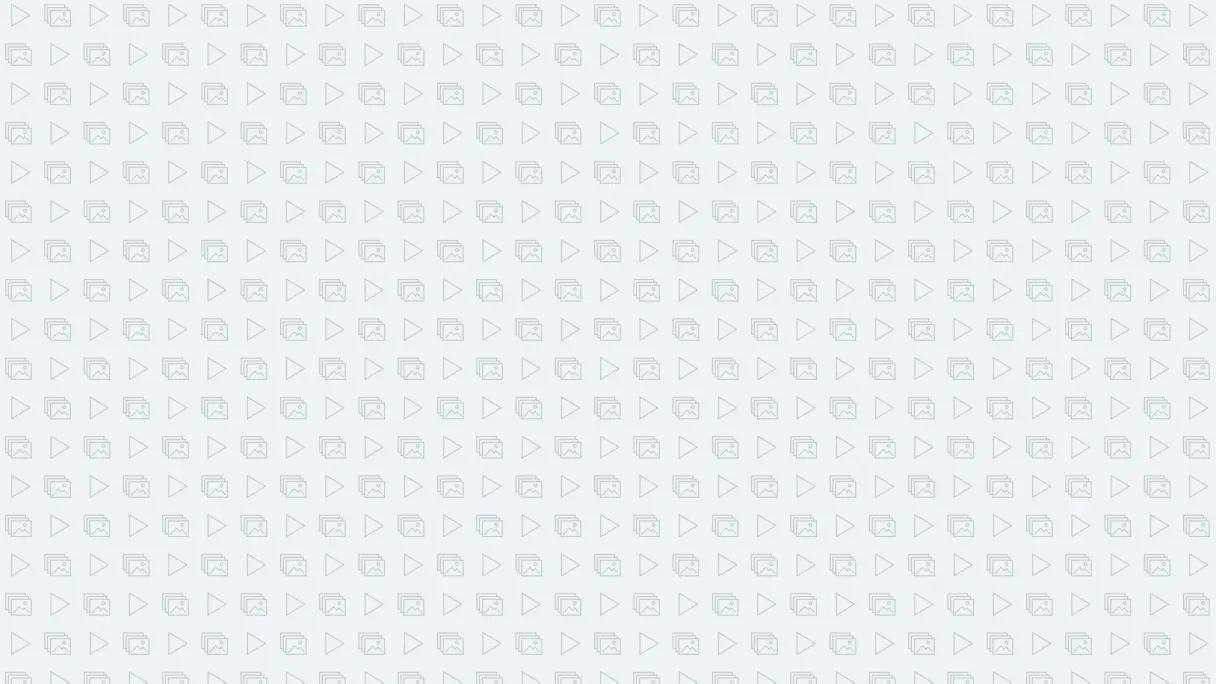
This video is provided by Google*. When you load this video, your data, including your IP address, is transmitted to Google, and may be stored and processed by Google, also for its own purposes, outside the EU or the EEA and thus in a third country, in particular in the USA**. We have no influence on further data processing by Google.
By clicking on “ACCEPT”, you consent to the data transmission to Google for this video pursuant to Art. 6 para. 1 point a GDPR. If you do not want to consent to each YouTube video individually in the future and want to be able to load them without this blocker, you can also select “Always accept YouTube videos” and thus also consent to the respectively associated data transmissions to Google for all other YouTube videos that you will access on our website in the future.
You can withdraw given consents at any time with effect for the future and thus prevent the further transmission of your data by deselecting the respective service under “Miscellaneous services (optional)” in the settings (later also accessible via the “Privacy Settings” in the footer of our website).
For further information, please refer to our Data Protection Declaration and the Google Privacy Policy.*Google Ireland Limited, Gordon House, Barrow Street, Dublin 4, Ireland; parent company: Google LLC, 1600 Amphitheatre Parkway, Mountain View, CA 94043, USA** Note: The data transfer to the USA associated with the data transmission to Google takes place on the basis of the European Commission’s adequacy decision of 10 July 2023 (EU-U.S. Data Privacy Framework).As part of its global customer service network, Liebherr has established component remanufacturing and repair facilities all-over the world to directly support its customers in the global mining industry. Liebherr understands that its ability to offer exchange components and repair services in regional proximity to customers’ operations is essential for delivering high parts availability and short repair cycle times; key success factors for equipment operating 24/7 in demanding conditions. Today, Liebherr Mining has 12 remanufacturing and repair facilities globally engaging over 250 employees.
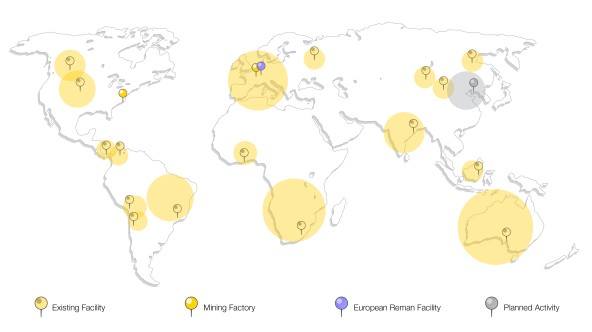
Each facility has online access to the latest remanufacturing procedures, technical specifications, standardized tooling and equipment, and the complete range of genuine Liebherr parts specific to each component. Standardized OEM component repair training further ensures that each component is refurbished efficiently, safely, and to the as-new standard. Finally, all facilities are regularly inspected and certified according to comprehensive remanufacturing guidelines and standards outlined in the Liebherr Mining Service Excellence program.
Liebherr Reman facilities
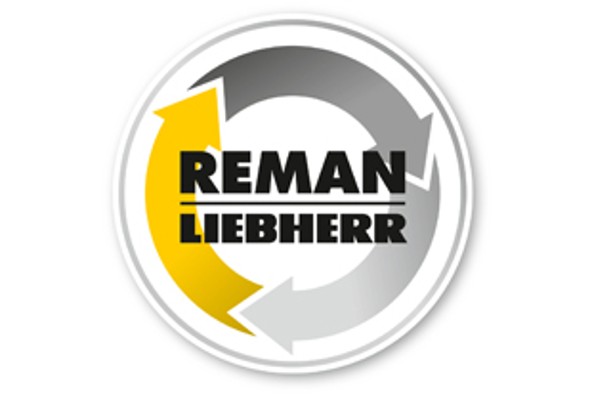
Video
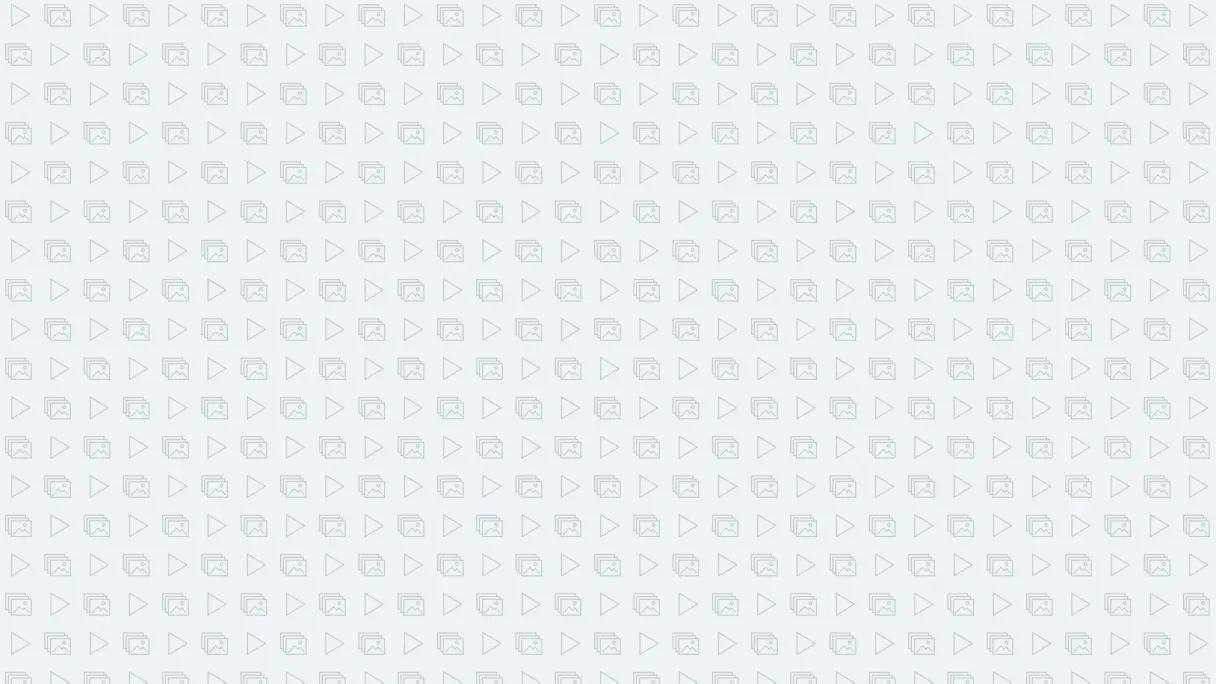
This video is provided by Google*. When you load this video, your data, including your IP address, is transmitted to Google, and may be stored and processed by Google, also for its own purposes, outside the EU or the EEA and thus in a third country, in particular in the USA**. We have no influence on further data processing by Google.
By clicking on “ACCEPT”, you consent to the data transmission to Google for this video pursuant to Art. 6 para. 1 point a GDPR. If you do not want to consent to each YouTube video individually in the future and want to be able to load them without this blocker, you can also select “Always accept YouTube videos” and thus also consent to the respectively associated data transmissions to Google for all other YouTube videos that you will access on our website in the future.
You can withdraw given consents at any time with effect for the future and thus prevent the further transmission of your data by deselecting the respective service under “Miscellaneous services (optional)” in the settings (later also accessible via the “Privacy Settings” in the footer of our website).
For further information, please refer to our Data Protection Declaration and the Google Privacy Policy.*Google Ireland Limited, Gordon House, Barrow Street, Dublin 4, Ireland; parent company: Google LLC, 1600 Amphitheatre Parkway, Mountain View, CA 94043, USA** Note: The data transfer to the USA associated with the data transmission to Google takes place on the basis of the European Commission’s adequacy decision of 10 July 2023 (EU-U.S. Data Privacy Framework).Customer benefits
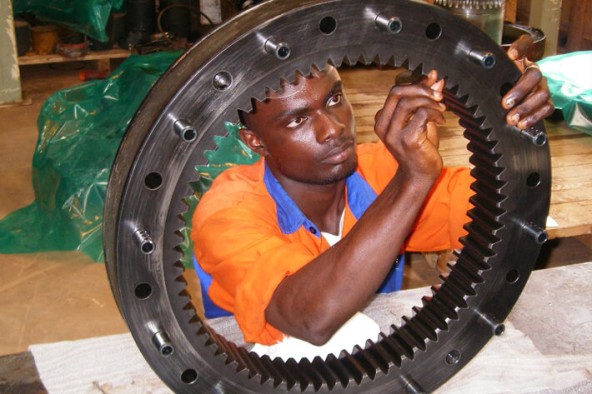
Each component is inspected, repaired and tested by qualified Liebherr trained technicians using comprehensive OEM guidelines and specialized tooling in Liebherr certified facilities to ensure that each remanufactured component performs as-new. Guaranteed.
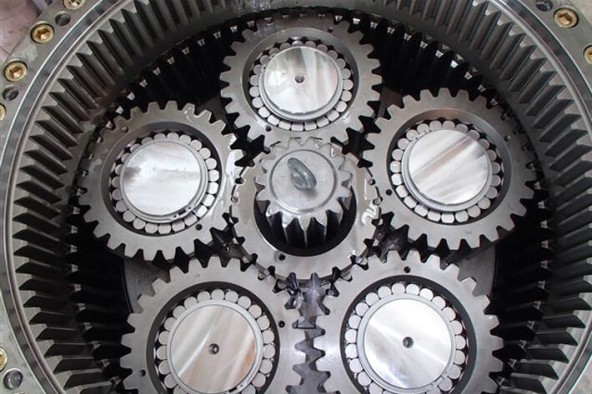
Liebherr carries the complete range of genuine parts used for repairing and remanufacturing components. This ensures that customers can benefit from the fastest turn-around times for repaired components, and the highest availability of remanufactured exchange components.
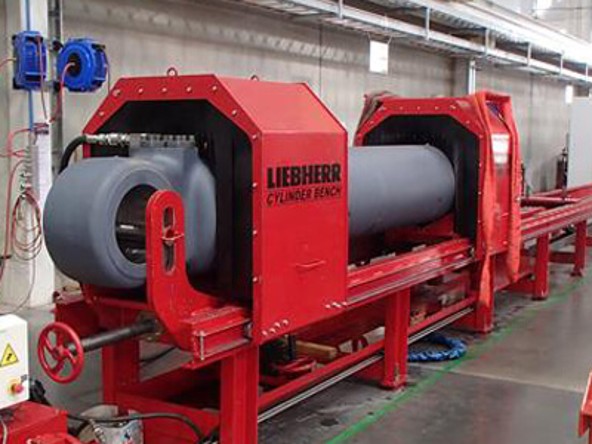
Customers benefit from a variety of comprehensive repair and exchange programs to ensure flexibility in equipment maintenance budgets without compromising quality, performance and reliability.
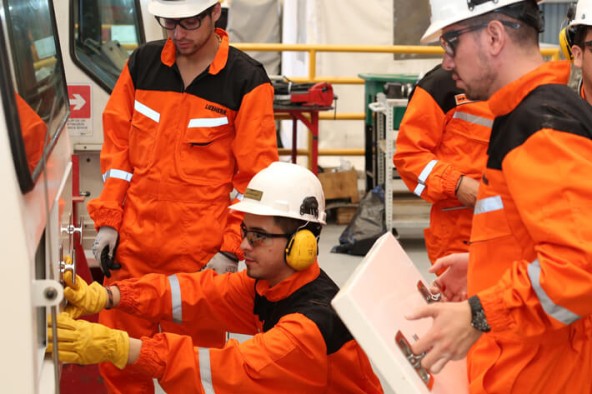
Not only do customers benefit from detailed component analysis reports on each component returned for repair or remanufacturing, but Liebherr engineers also systematically analyse and evaluate this information to continually improve component design.
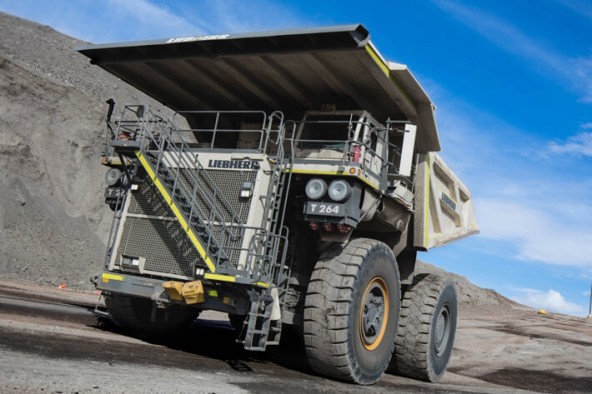
Implementing the latest technical improvements is a key part of the component remanufacturing process at Liebherr. This ensures that customers can continuously benefit from improved performance, reliability and safety each time a component is exchanged.
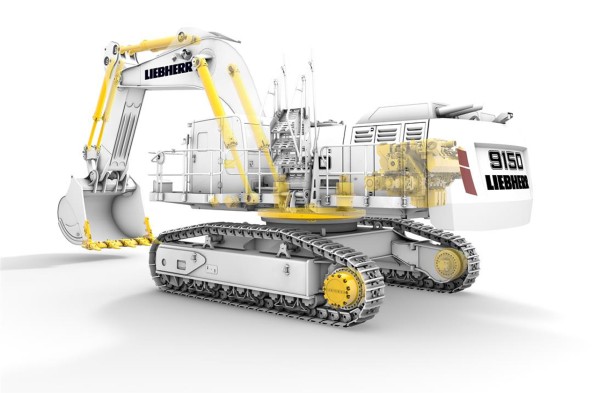
Liebherr designs and manufactures all major mining components in-house which puts it in a unique position to manage all stages of the component lifecycle; from development and manufacturing through to product support and remanufacturing. This in-depth product knowledge is essential for developing component specific tooling, defining optimal reusability criteria, and testing remanufactured components to the as-new specification.
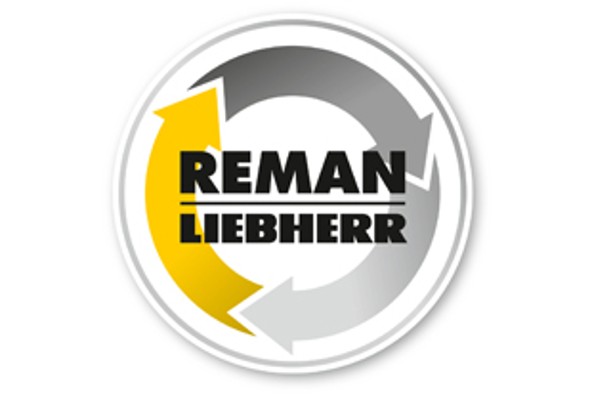
Video
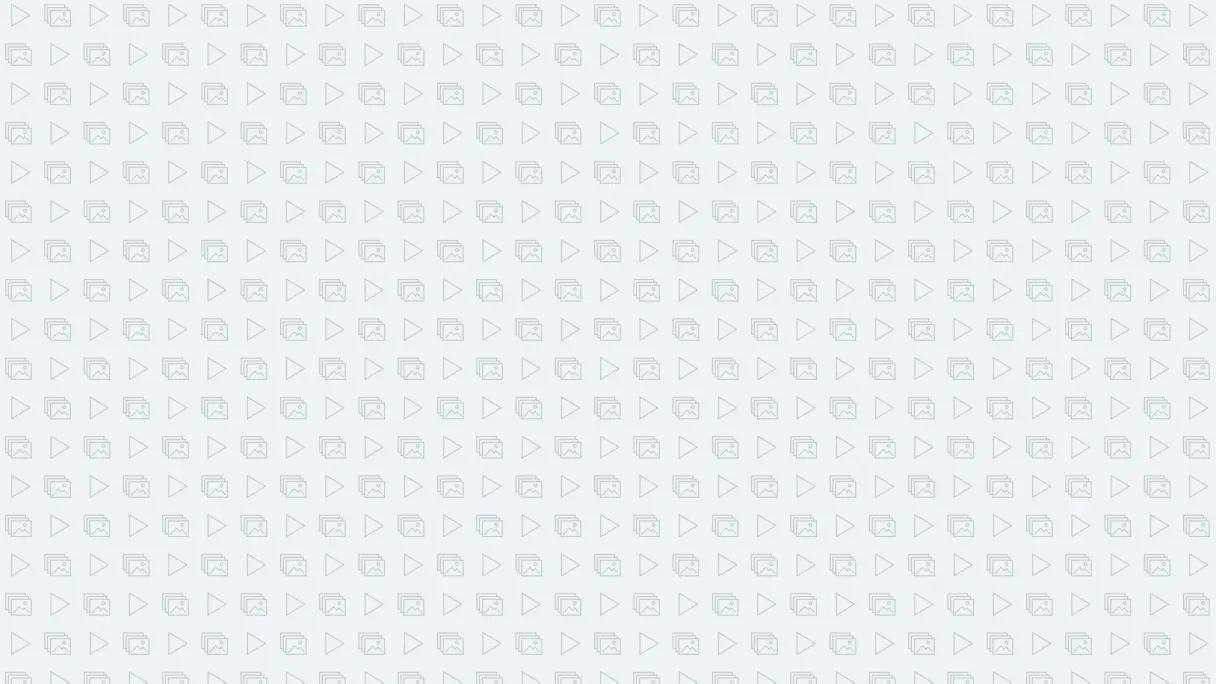
This video is provided by Google*. When you load this video, your data, including your IP address, is transmitted to Google, and may be stored and processed by Google, also for its own purposes, outside the EU or the EEA and thus in a third country, in particular in the USA**. We have no influence on further data processing by Google.
By clicking on “ACCEPT”, you consent to the data transmission to Google for this video pursuant to Art. 6 para. 1 point a GDPR. If you do not want to consent to each YouTube video individually in the future and want to be able to load them without this blocker, you can also select “Always accept YouTube videos” and thus also consent to the respectively associated data transmissions to Google for all other YouTube videos that you will access on our website in the future.
You can withdraw given consents at any time with effect for the future and thus prevent the further transmission of your data by deselecting the respective service under “Miscellaneous services (optional)” in the settings (later also accessible via the “Privacy Settings” in the footer of our website).
For further information, please refer to our Data Protection Declaration and the Google Privacy Policy.*Google Ireland Limited, Gordon House, Barrow Street, Dublin 4, Ireland; parent company: Google LLC, 1600 Amphitheatre Parkway, Mountain View, CA 94043, USA** Note: The data transfer to the USA associated with the data transmission to Google takes place on the basis of the European Commission’s adequacy decision of 10 July 2023 (EU-U.S. Data Privacy Framework).