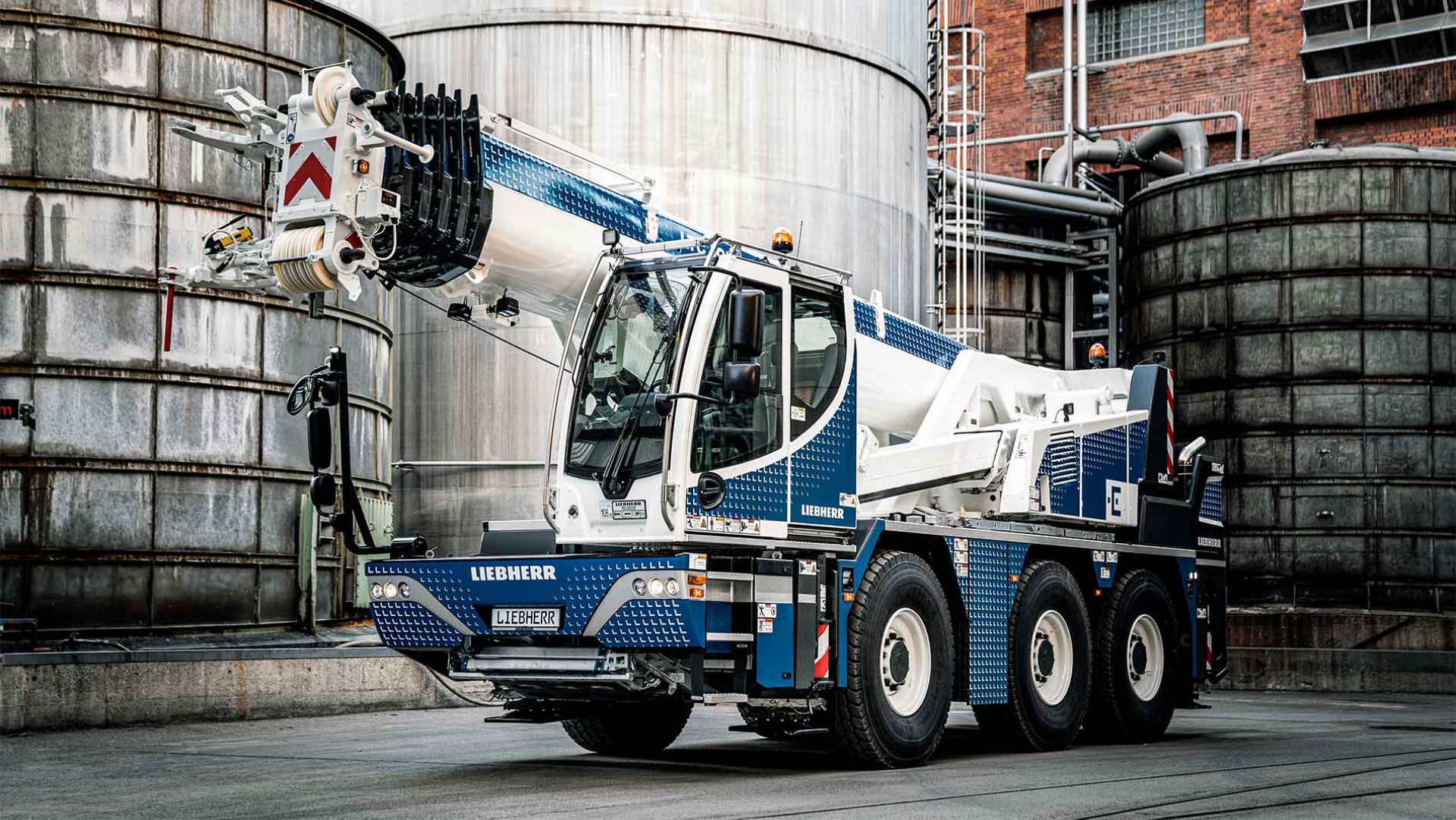
9 minutes | magazine 02/2022
Zero emission, full power
The accelerating climate revolution demands drive concepts to be used in the construction industry which reduce emissions of greenhouse gases.
LTC 1050-3.1 now also with electric drive
To meet the needs of customers and the demand for greener equipment as well as possible, Liebherr is working on alternative drive units, which are perfectly tailored to the application and location of the machine, without focusing on a single technology. Our LTC 1050-3.1 compact crane now gets an electric motor in addition to the conventional drive. This enables crane movements to be powered electrically as an option. The new version of the compact 50 tonne crane therefore helps to reduce CO2 emissions and meets the requirements for operating on “zero emission” sites.
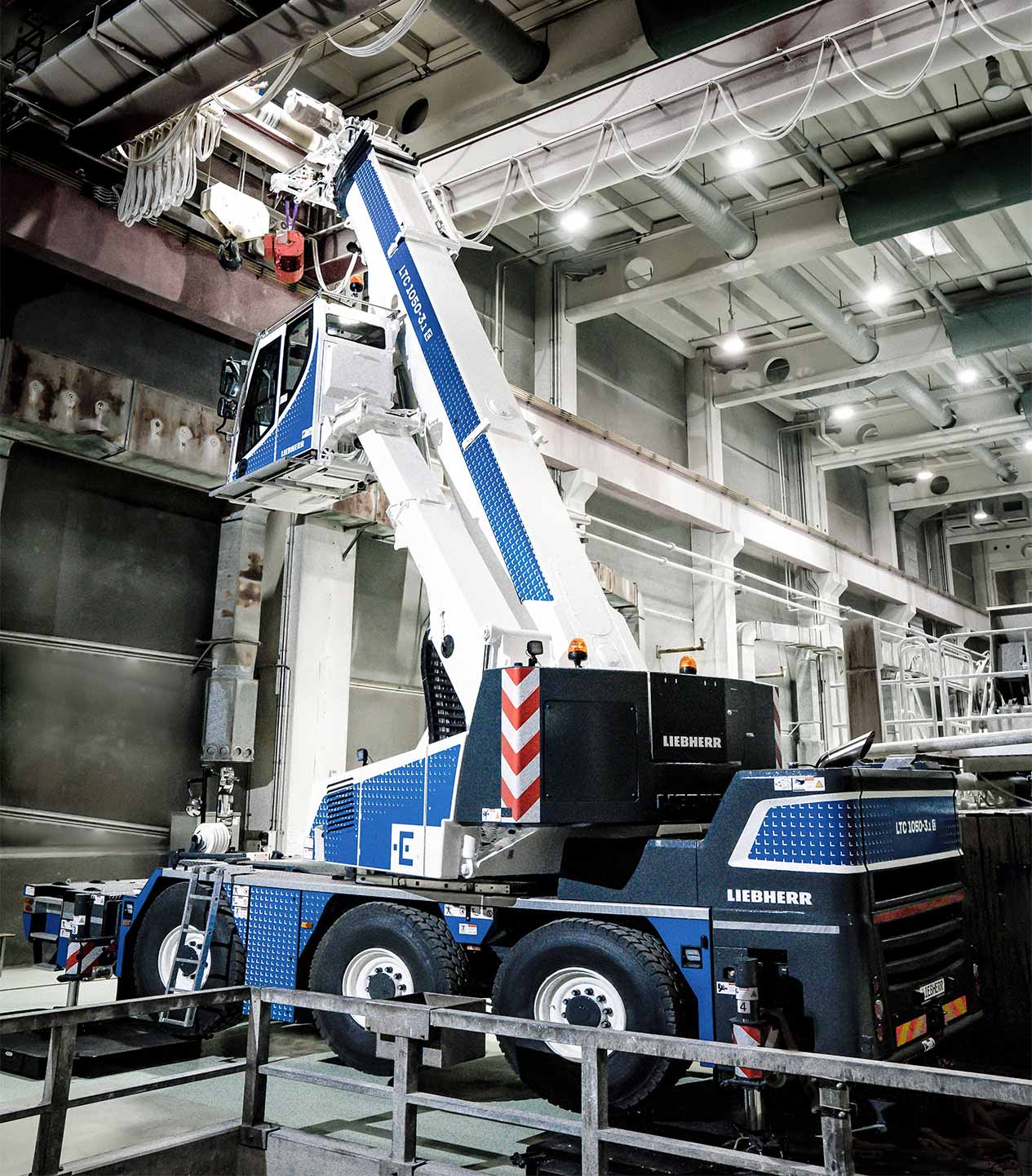
Indoor use - The LTC 1050-3.1 with electric drive and lift cabin in use in a factory workshop.
Liebherr developed the electric power unit for the LTC 1050-3.1 using the slogan “Zero emission, full power”. Dr Ulrich Hamme, Technical Director at Liebherr-Werk Ehingen GmbH, says: “We want to be able to offer our customers full crane performance even with the alternative electric power unit. The LTC 1050-3.1 still has a conventional internal combustion engine, powered by diesel or HVO, for driving on roads and for crane operations. However, as an alternative it also has an electric power unit for crane operations so that it generates “Zero emission”. That means that all the familiar usage properties of the crane will be retained, regardless of whether the crane operations are powered by its zero emission electric motor or its internal combustion engine.”
Maximum flexibility for full green credentials and customer benefits
The new alternative LTC 1050-3.1 delivers the best possible combination of green credentials, customer benefits and efficiency. On the road and off-road, it has a conventional, low emissions internal combustion engine which complies with emissions stage 5 and develops 243 kW (326 bhp). The engine can be fuelled with hydrogenated vegetable oil (HVO) with absolutely no restrictions, enabling it to reduce its CO2 emissions by up to 90 % compared to fuelling it with diesel.
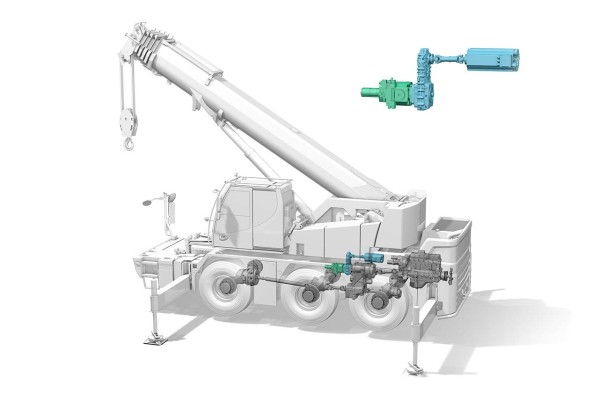
Cleverly solved - The electric motor drives the crane pump through a distributor gear.
Either the engine or the electric motor can be selected in crane mode depending on the conditions for the job. The latter reduces both air and noise emissions to a minimum. This also means that the machine is suitable for use in noise-sensitive areas and in “zero emission areas”.
Simple, clever electric motor concept – flexible electric power unit
The newly developed power unit featuring an electric motor develops 72 kW and therefore enables the crane to be operated without restriction, in other words with almost the same performance as using the 6-cylinder engine. The electric motor uses the existing hydraulic pump, which is mounted direct on the powershift transmission on the conventional LTC 1050-3.1, to transfer the power to the consumers in the crane superstructure.

Plug in and work - Full power with 125 amps, practical also with 63 amps.
Only the electric motor and a distributor gear as well as the required control equipment must be added to the conventional LTC 1050-3.1 model to transform it into an electric version. The distributer gear is located directly between the crane pump and the powershift transmission. This clever yet simple solution enables the operator to switch flexibly between diesel-hydraulic power and electro-hydraulic power. Site current at 125 A is required to achieve full performance, but the crane also operates very well with a 63 A supply. Alternatively, the crane can operate using an external conventional battery pack if the site does not have the appropriate electrical infrastructure.
Liebherr supplies the electric model of the LTC 1050-3.1 for the version with the 36 metre TELEMATIK telescopic boom. The RemoteDrive option for remote-controlled driving and height-adjustable elevating cab are also available for the new crane. The prototype with the electric power unit is currently undergoing intensive testing. We are planning the first deliveries for the first half of 2023.
3 questions for: Lars Christian Steen - Owner and CEO of Asle Skoveng Kranservice AS
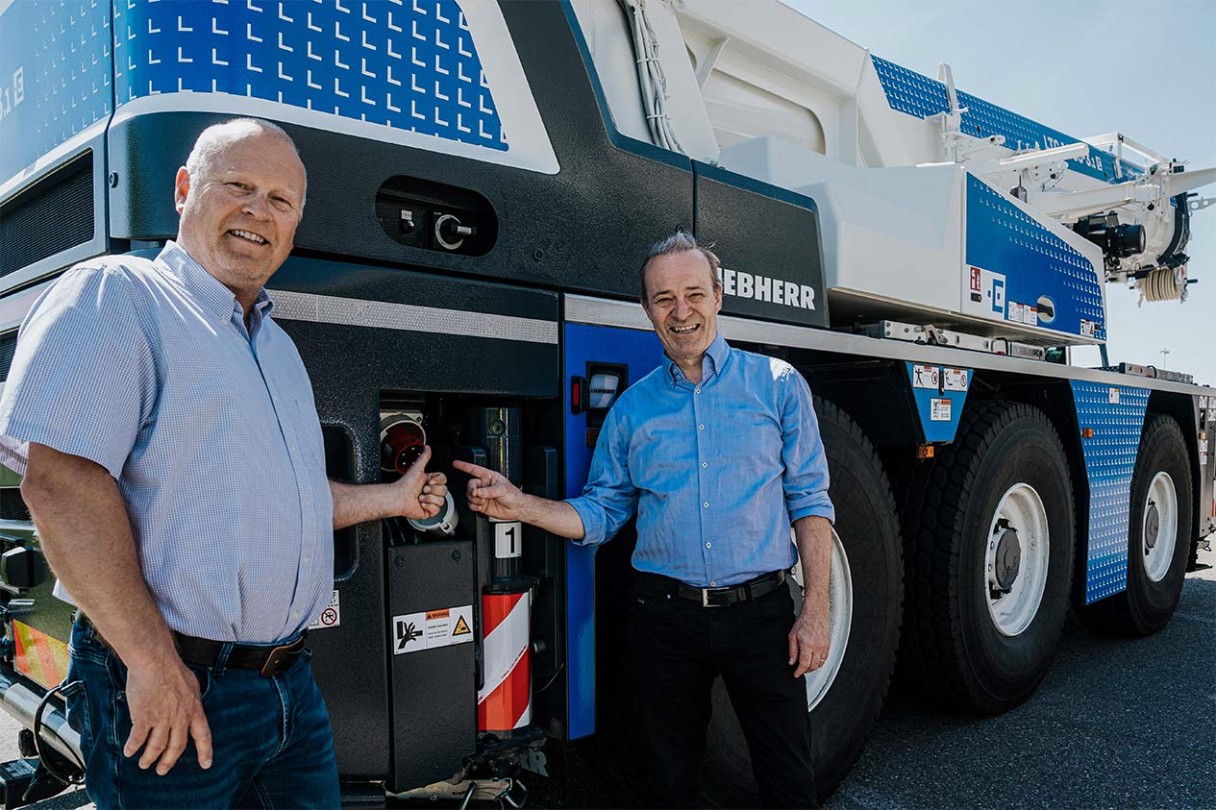
The plug makes all the difference - Lars Christian Steen (left) and co-owner Leif Petterhaagstad are convinced by the concept of the LTC 1050-3.1 with its additional superstructure electric power unit.
Asle Skoveng Kranservice AS was founded in 1976 and its head office is located in Skedsmokorset, a few kilometres north of Oslo. The crane and transport contractor has been playing a major role in the construction of the Norwegian capital for almost half a century. Sustainability, safety, efficiency and CO2 reductions are major components of Skoveng’s corporate strategy.
You were one of the first companies to order the new LTC 1050-3.1 with its electric power unit – and you did not just leave it at one but ordered five of them at once. What made you invest so heavily in cranes with electric power units?
Lars Christian Steen: Skoveng supports the Paris Climate Agreement and we are following a clear strategy – zero emissions. We are one of the leading crane contractors in the Oslo region and we have already reduced our CO2 emissions to an industryleading level using various methods including the use of hydrogenated vegetable oil HVO. But we intend to go even further. Our aim is to be a zero emissions crane contractor by 2025.
Norway is issuing ever more stringent regulations for construction sites. Seven large cities with a total of 1.4 million inhabitants, which actually accounts for 27 percent of the total population of Norway, have decided to ban fossil fuel emissions from construction sites completely from 2030. Emissions from construction sites make up around seven percent of the total emissions in the city of Oslo. Our capital is a pioneer and is pursuing some extremely ambitious targets with its climate and energy strategy. This is also preparing the way for other cities and communities. In the future, it will only be possible to use machines powered by hydrogen or electricity. Not only will this reduce CO2 emissions, of course, but also air and noise pollution.
Why did you decide to buy the new Liebherr cranes?
Lars Christian Steen: Our partnership with Liebherr is what has enabled us to deliver high quality mobile cranes to our market over the last few decades. Liebherr supplies machines which are suitable for the use of HVO. And now we have reached the time to take the next big step – “Zero emissions mobile cranes”.
We held productive dialogue with Liebherr about how we could secure our future with zero emissions mobile cranes. At the end of last year, Liebherr then unveiled its first mobile crane whose superstructure is powered by electricity, the LTC 1050-3.1. We then placed an order for five of these cranes. Our commitment to a zero emissions future using the technological innovations from Liebherr resulted in the largest ever order for mobile cranes in our corporate history.
Just like Skoveng, we believe that Liebherr has the motivation and commitment to play a leading role in the reduction of the CO2 footprint of mobile cranes. We also purchased a Liebherr MK 88 mobile construction crane which can be powered by electricity on site. And we have also had a close look at the Unplugged cranes from Liebherr Nenzing.
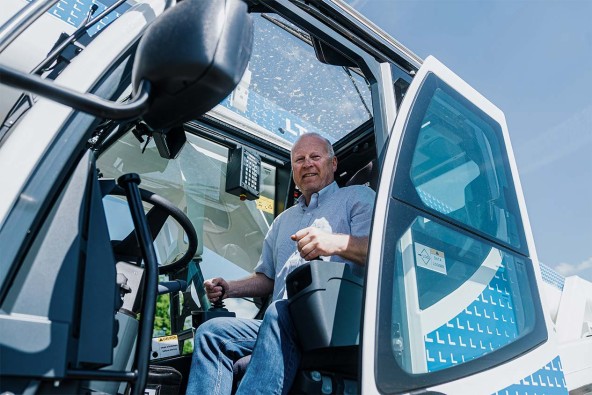
Vision - Lars Christian Steen in the crane cabin of the new LTC 1050-3.1.
How do you assess the further developments towards more environmental friendliness?
Lars Christian Steen: Even outside Norway, there are some very ambitious targets being set. In May, Finland started to support the measures put in place by its cities by signing off on the Green Deal Agreement which states that as from 2025, 20 percent of work on sites must be powered by electricity, biogas or hydrogen. As from 2030, the government wants to ensure that 50 percent of site work is carried out using these regenerative energy sources. Copenhagen, Stockholm and Amsterdam have also started to move in this direction by supporting pilot projects and adopting green criteria in their procurement strategies. Many cities and regions will follow their example over the next few years.
This article was published in the UpLoad magazine 02 | 2022.