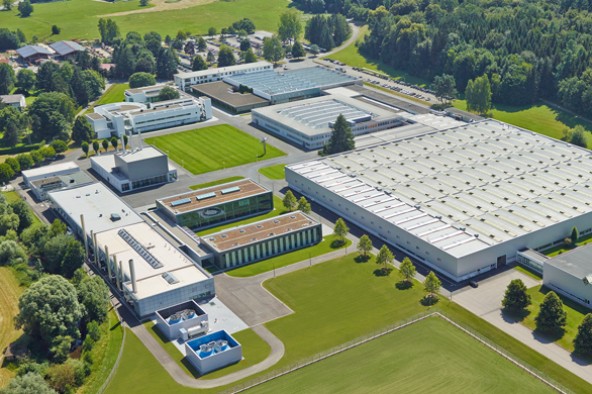
All burners are manufactured at the company’s main plant in Schwendi. This state-of-the-art production facility is a showpiece in terms of safety, precision, and cleanliness. Its design also allows operators to work efficiently during assembly of large and medium-sized burners, which are almost always custom-made. These include gas, oil and dual-fuel burners, rated up to 32 megawatts, as used in industrial processes, for example, drying plants in the vehicle manufacturing.
As part of an improvement strategy Weishaupt is reimagining its flexible manufacturing process for cubic machining. This involves the important process of machining burners and casing components. The first stage of improvements included the procurement of two new machining centres featuring a Liebherr-Verzahntechnik PHS 3500 (Pallet Handling System) integrating the manufacturing processes. This new flexible manufacturing system has been producing workpieces since spring 2016.