"Compact, flexible, expandable and with strict pursuit of a modular concept." This is how Thomas Mattern, Head of Automation Systems Development, describes the new compact class in the Liebherr world of automation. The PHS Allround fills the gap between the Liebherr RLS rotary loading system as a circular storage system for one or two machines and the PHS PRO linear pallet handling system for maximum flexibility with any number of machines. It is an expandable entry-level solution similar to a Lego building set. The pre-made modules can be assembled together in different layout variants.
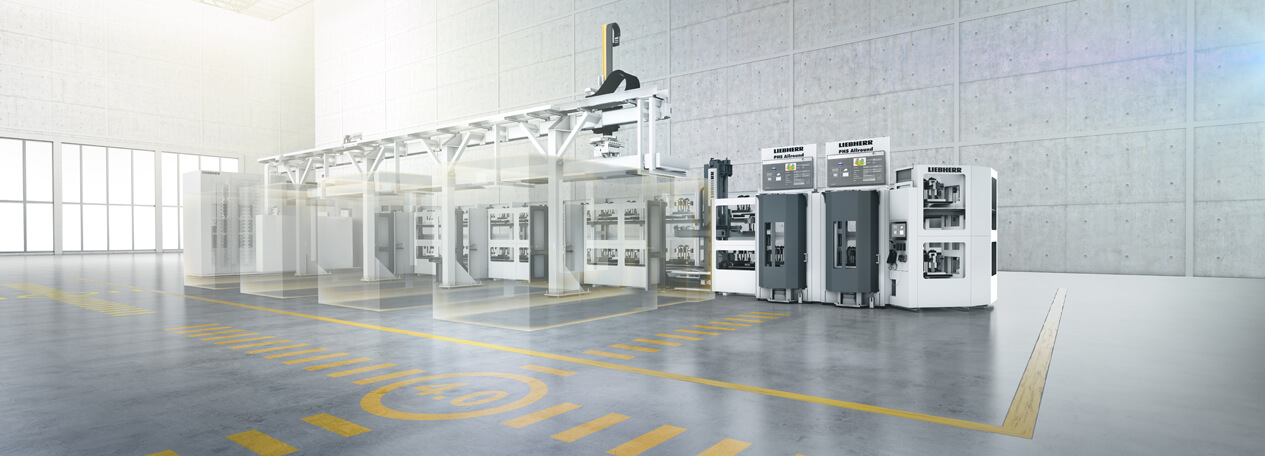
Universally usable
Liebherr has met the needs of automation customers with the PHS Allround: The compact class for universal users has been in great demand since its introduction in 2017. Alongside the current PHS 1500 Allround version, Liebherr has announced two more sizes—the 800 and 3000.
The system that grows along with you
"Our rail system is configurable and expandable meter by meter. Most customers begin with two machines but immediately start planning for expansion in the near future. This makes the PHS Allround, with its modular design and flexibility, the ideal solution," states Mattern. Additional storage locations, machines and loading stations can easily be added.
The ability to place machines, loading stations, inspection machines and shelf space or even peripherals for additional tasks on the front side enhances the flexibility in the system design. This enables the realization of high storage density while providing versatile design options at the same time. The rotating tower storage, a well-known feature of the rotary loading system, provides additional storage. You can significantly increase the number of storage locations in the smallest space.
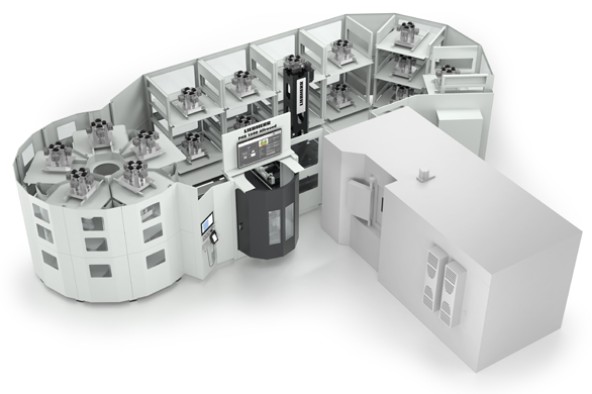
Technical refinements
The optional double loader, available starting in 2019, reduces the pallet changing time on the machine tool, enabling lower system cycle times. Significant advantages emerge for machines without pallet changers.
In one pass, the part to be machined can be exchanged with a new blank on the second telescopic fork. That is particularly worthwhile if a loading system serves several machines. "In the design engineering phase, our focus was on the reduction in idle time. This ensure us the lowest possible number of interruptions and high productivity and utilization of machine tools," Mattern explains.
A design principle that combines turning and telescoping makes it possible to achieve separate front access of the machine tool as needed. Maintenance, measuring tasks and direct clamping onto the machine can be carried out while the system is running. The area in front of the machine tool is separated from the rest of the system without restricting the travel of the lift modules. All other machines connected to the system can continue to be supplied with pallets in automatic mode. "That is a true Liebherr innovation no other provider has in their portfolio," emphasizes Knut Jendrok, from Sales in pallet handling systems.
Everything modular
In order to realize short delivery times, the PHS Allround adheres to a strict modular design. Nevertheless, diverse combination options enable the right solution for virtually every application.
In terms of the control systems, Liebherr uses axis control from Siemens, which has also proven it’s value in many other systems. Users can choose between Soflex and Procam for the host computer. Both systems can be configured and set up to best meet the requirements of the users. Options include features such as NC and tool data management.