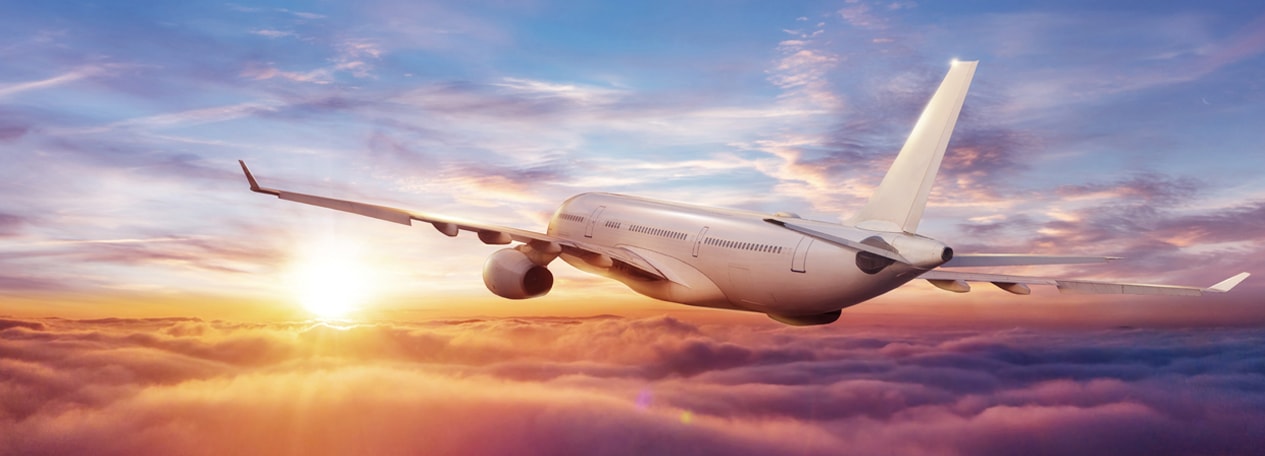
Auxiliary spindle for challenging grinding
The machining of gears with interfering contours for the aerospace industry places the highest demands on the grinding tool and often cannot be carried out with standard grinding heads due to the small tool diameters. Liebherr has developed an auxiliary spindle for these applications which can be retrofitted. This enables the production of challenging aerospace components on existing LGG gear grinding machines.
The greatest possible flexibility, even for special applications, by means of simple conversion or retrofitting of the necessary tools: Liebherr has been successfully pursuing this approach for several years with its adaptable internal grinding arms. With the existing range of internal grinding arms, a machine can be converted from external grinding to profile grinding of internal gears in a very short time. Why shouldn’t this proven concept also work for the external grinding of special aerospace components? Following this thought, Liebherr developed an auxiliary spindle as an optional accessory that can be offered for LGG gear and profile grinding machines and can be retrofitted to existing machines.
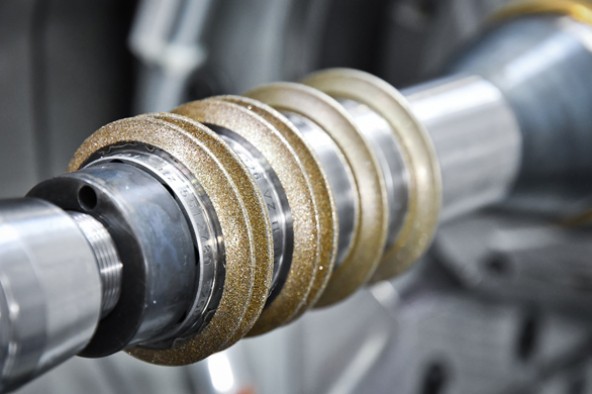
A further option for special applications
The newly developed auxiliary spindle is part of a machine purchase and will be handed over to production at the sister company, Liebherr-Aerospace Lindenberg GmbH, at the end of 2020. This sophisticated new development is designed in close cooperation with the user so that the practical needs of machine operators can be incorporated into the design at an early stage. This applies to setup procedures and service tasks, in particular. A typical aerospace application is profile grinding of what is known as a 3-stage planetary gear, which is required for the wing flap adjustment. Due to the weight-optimized, compact component geometry, only small CBN grinding wheels are technically possible for final hard gear finishing.
With the auxiliary spindle, the user can use the LGG gear grinding machine to produce aerospace components with interference contours, along with their special technical challenges, in small batch sizes without having to invest in an expensive, possibly underutilized, special machine. The geometrically demanding components can thus be manufactured with high gear quality and surface quality. This expands the range of LGG grinding applications to include an additional option for critical, very small and high-quality components.
The auxiliary spindle – just like the internal grinding arm – can be mounted on all new Liebherr grinding heads with counter bearings via a changeover interface, which ensures short setup times. The additional functions of the grinding heads, such as an inductive meshing sensor, a movable cooling lubricant nozzle and a swiveling measuring probe, can also be used in combination with the auxiliary spindle.
We view our standard products as the basis for flexible solutions that are always geared to our customers and their require-ments.
Spindle and matching CBN grinding wheels from Liebherr
Machining parts with very small grinding discs requires high spindle speeds to ensure the required cutting speeds of at least 30 meters per second. At speeds of up to 30,000 revolutions per minute, the auxiliary spindle must meet the highest requirements in terms of vibration behavior and temperature resistance. A bearing on both sides ensures high rigidity, a stable concentricity and additionally allows the use of a longer grinding arbor, which is the technical prerequisite for the safe mounting of several grinding discs. This enables up to two duo roughing discs and two finishing discs with increased feed rates to be used, significantly reducing machining times.
Liebherr now has over 30 years of CBN expertise for its globally successful gear grinding machines. For this reason, a sophisticated development project was started for the extremely small CBN profile grinding discs, in order to galvanize the extremely fine CBN grains (grain size ~ 25 to 35 micrometers) onto the high-precision main bodies, so that the narrow gear tolerances and high surface qualities can be ensured with the finest CBN coatings.
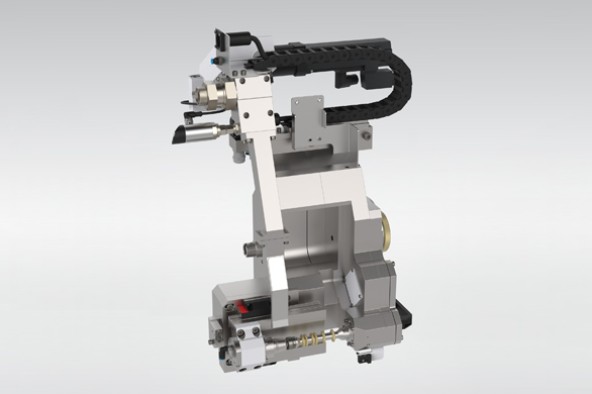
Core competence: grinding process
Liebherr aims to be able to supply all the key components from a single source in order to offer customers the best possible solution:
- Gear grinding machines with accessories
- Technological expertise
- Tool design and production
“We view our standard products as the basis for flexible solutions that are always geared to our customers and their requirements,” says Thomas Breith, Head of Product Management Gear Cutting Machines at Liebherr, summarizing the philosophy.