Landing gear systems
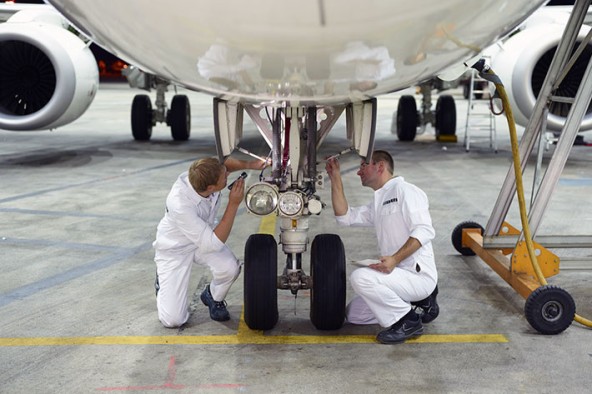
The landing gear is an essential system that allows the aircraft to start from the gate, taxi to the runway, to take off and to land safely. Liebherr-Aerospace has the capabilities and the experience to design, manufacture and service landing gear systems. This includes the landing gear structure, the extension/ retraction and steering actuation, the position and warning system, the integration of wheels and brakes and the associated sensors and controls, including cockpit controls.
Landing gear systems by Liebherr are integrated into all kinds of platforms like commercial aircraft, regional aircraft, business jets, helicopters, transport aircraft and fighters.
Landing gear structural parts
Liebherr has in-house capabilities for the design and manufacture of all structural, parts of landing gears. This comprises the main fitting, sliding tube, side stays and locking stays, wheel axle and drag braces.
Latest generation machining and surface treatment
The engineering capabilities comprise layout, design, performance-, stress- and fatigue calculation as well as full safety and reliability analyses. The in-house manufacturing competencies include latest generation machining and surface treatment.
In addition to that, Liebherr offers further integration services such as complete dressings.
By clicking on “ACCEPT”, you consent to the data transmission to Google for this video pursuant to Art. 6 para. 1 point a GDPR. If you do not want to consent to each YouTube video individually in the future and want to be able to load them without this blocker, you can also select “Always accept YouTube videos” and thus also consent to the respectively associated data transmissions to Google for all other YouTube videos that you will access on our website in the future.
You can withdraw given consents at any time with effect for the future and thus prevent the further transmission of your data by deselecting the respective service under “Miscellaneous services (optional)” in the settings (later also accessible via the “Data protection settings” in the footer of our website).
For further information, please refer to our Data Protection Declaration and the Google Privacy Policy.*Google Ireland Limited, Gordon House, Barrow Street, Dublin 4, Ireland; parent company: Google LLC, 1600 Amphitheatre Parkway, Mountain View, CA 94043, USA** Note: The data transfer to the USA associated with the data transmission to Google takes place on the basis of the European Commission’s adequacy decision of 10 July 2023 (EU-U.S. Data Privacy Framework).Video: Liebherr-Aerospace – Your Partner for Landing Gear Systems
Contacts
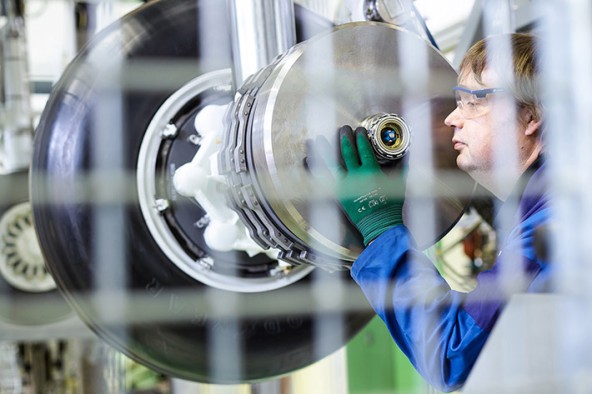
Preparation of a landing gear in its test rig
Landing gear retraction and extension sub-systems
Retraction and extension sub-systems fulfill functions such as aircraft landing gear extension and retraction or landing gear up-locking.
In-house manufacturing
Liebherr has the complete capability to design and manufacture in-house the structural, hydraulic and mechanical parts of such sub-systems (actuators, manifolds, reservoirs, valves, up-locks), and to integrate all those parts together with the electronic hardware and software controls made by Liebherr.
Contacts
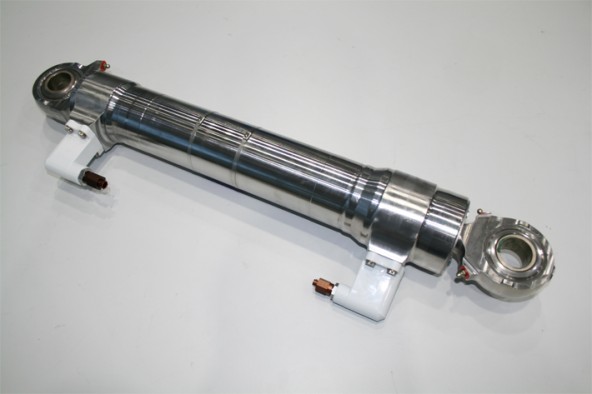
Nose landing gear retraction actuator
Landing gear supplementary sub-systems
Landing gear supplementary sub-systems fulfill functions such as nose wheel steering, aircraft braking, landing gear door actuation, position and warning.
Landing gear sub-systems
- The steering sub-system allows steering the aircraft when taxiing.
- The braking sub-system allows reducing the aircraft speed upon landing.
- The landing gear door actuation sub-system allows to close the landing gear bay doors once the aircraft is in the air and to open them when the aircraft is about to land.
- The position and warning system is used to control the sequences of the landing gears legs extension and retraction.
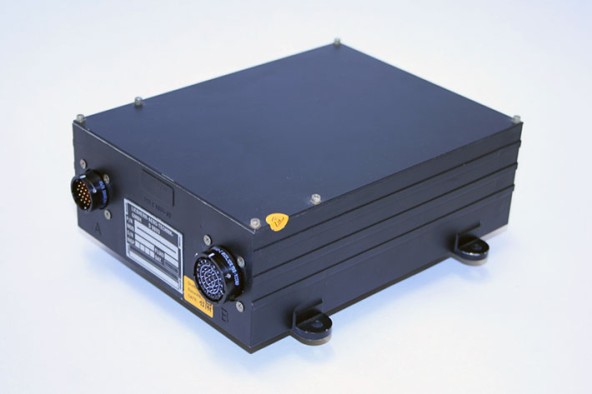
Nose wheel steering control
Landing gear in-house capabilities
Liebherr has the complete capability to design and manufacture in-house the structural, hydraulic and mechanical parts of such sub-systems (actuators, manifolds, reservoirs, valves, up-locks), to subcontract the other parts (wheels and brakes, brake control, sensors) from specialized suppliers, and to integrate all those parts together with the electronic hardware and software controls made by Liebherr.
Contacts
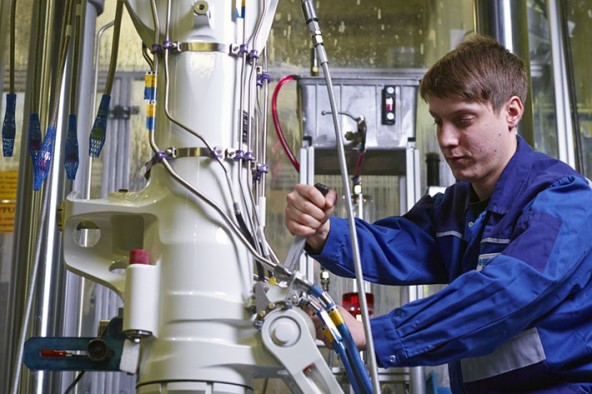
Working on a landing gear test rig
Landing gear testing capabilities
Liebherr operates modern test and support facilities for the development and integration of landing gear systems, subsystems and components.
Advanced in-house testing facilities
The test set-ups and components are designed and built in-house; they are based on the concept of modular test rigs and fixtures, including electronic control and electronic data acquisition.
They fulfill most of the testing requirements, including fatigue, endurance, static strength and environmental testing. Liebherr’s system testing capability includes the integration of subsystem tests, e. g. brake control system.
Liebherr relies on agreements with long-term partners for specific testing facilities such as drop or vibration testing.

Non-destructive testing of a landing gear housing
Non-Destructive Testing is Key
The systems and components by Liebherr-Aerospace Lindenberg GmbH, Lindenberg (Germany) are made of a variety of materials. They undergo a wide range of processes and diverse treatments to meet the high requirements for use in aircraft in terms of density, temperature and pressure. The non-destructive testing methods are certified according to Nadcap, i.e. they meet the strict uniform quality standard worldwide in the aerospace industry.
Non-destructive material testing uses different procedures for materials, geometries, manufacturing processes and requirements before, during and after the production process. Whether plastic, iron, non-ferrous metals or composite materials - the complete variety of product technology is reflected in the knowledge of the required test methods. For all materials and processes, the appropriate tests are carried out quickly, effectively and flexibly, and even the finest pores or material deviations can be detected. In doing so, Liebherr-Aerospace continuously ensures high product quality without destroying the component.
At Liebherr's facility in Lindenberg, the company uses in addition to the seven different standard NDT methods magnetic particle examination, fluorescent penetration test, natal etching process, eddy current testing, visual inspection, ultrasonic, X-ray inspection and special procedures such as the Barkhausen technology and X-ray diffractometry.
By clicking on “ACCEPT”, you consent to the data transmission to Google for this video pursuant to Art. 6 para. 1 point a GDPR. If you do not want to consent to each YouTube video individually in the future and want to be able to load them without this blocker, you can also select “Always accept YouTube videos” and thus also consent to the respectively associated data transmissions to Google for all other YouTube videos that you will access on our website in the future.
You can withdraw given consents at any time with effect for the future and thus prevent the further transmission of your data by deselecting the respective service under “Miscellaneous services (optional)” in the settings (later also accessible via the “Data protection settings” in the footer of our website).
For further information, please refer to our Data Protection Declaration and the Google Privacy Policy.*Google Ireland Limited, Gordon House, Barrow Street, Dublin 4, Ireland; parent company: Google LLC, 1600 Amphitheatre Parkway, Mountain View, CA 94043, USA** Note: The data transfer to the USA associated with the data transmission to Google takes place on the basis of the European Commission’s adequacy decision of 10 July 2023 (EU-U.S. Data Privacy Framework).