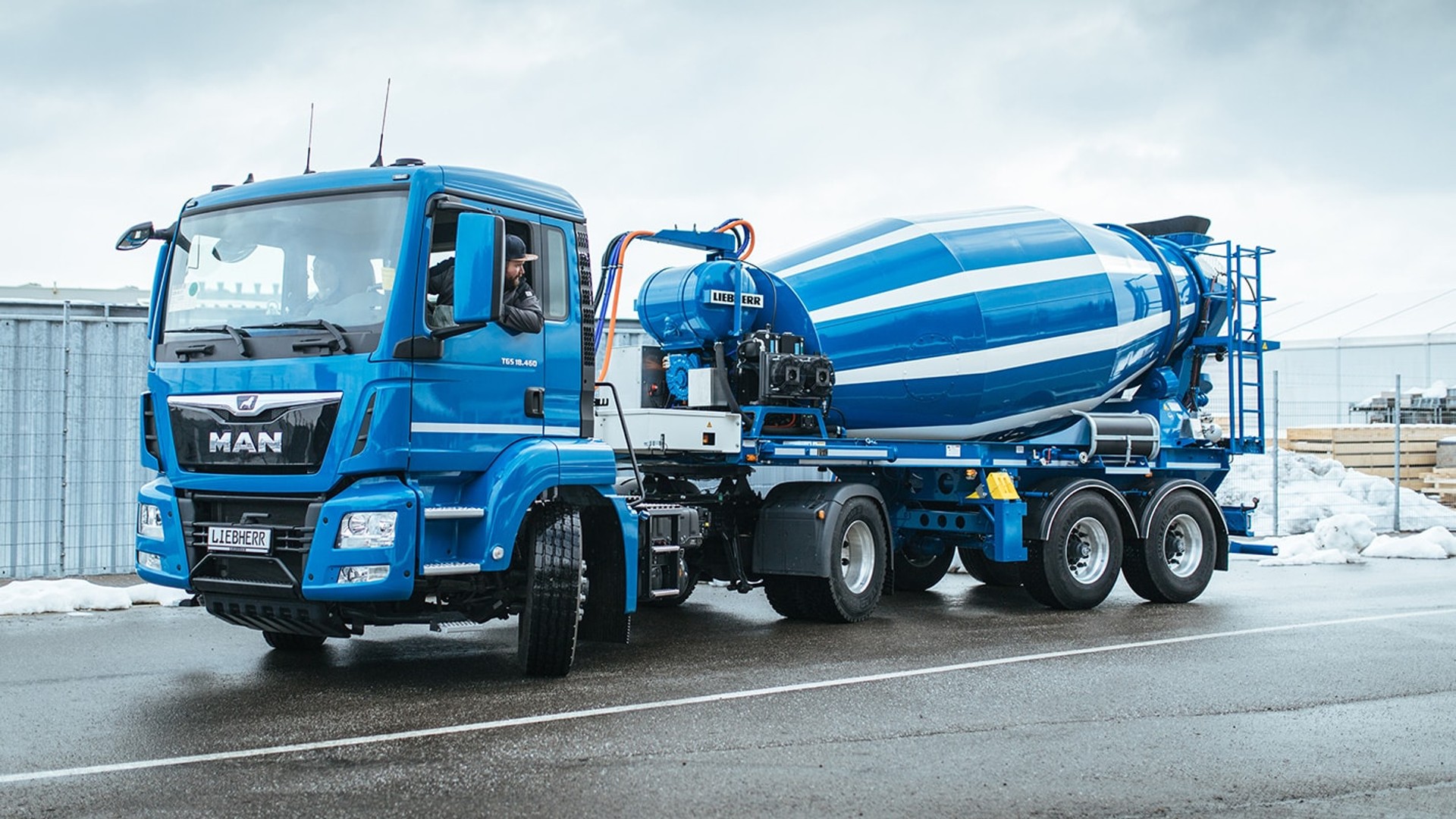
6 minutes reading time
‘E’ Makes all the Difference
For two years, the engineers and developers at Liebherr-Mischtechnik GmbH have been tinkering around to help create the emission-free construction site of the future. At Bauma, they not only showcased the first electrically-powered truck mixer that is comparable in performance to a diesel one, but also presented solutions that had previously been regarded as impossible.
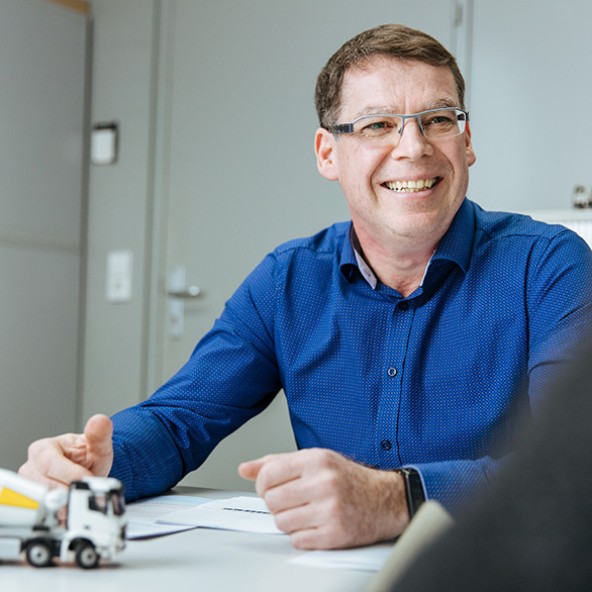
E-pioneers all charged up
The central console in the driver’s cabin is in a jumble. There are cables all over the place, tiny lights flashing and jacks waiting to be connected to laptops and other mobile computing devices. The whole thing is more reminiscent of a server room than the workspace in a truck mixer.
At the Liebherr-Mischtechnik GmbH test hall in Bad Schussenried, there is a high demand for complex electronic measurement technology – all the more so when it comes to designing innovative construction machinery for use in high-emission city centres and giving it emission-free status.
For more than two years, a team of developers lead by Gerhard Zenne, the Head of Engineering and Development at Liebherr-Mischtechnik GmbH, has been refining the new ETM production series. ‘It certainly wasn’t easy’, recalls Gerhard Zenne. ‘Unlike the car industry, applying electronic technology in construction site vehicles is completely uncharted waters – our work really is pioneering.’
At this point, it’s worth thinking back to how we got here.
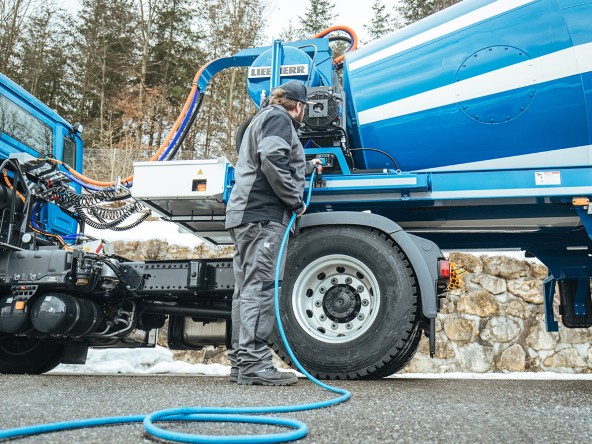
Gerhard Zenne’s team was given the task of combining the advantages of two driving technologies – and to work out how to fit them into the same amount of space, with the same axle load distribution. ‘These types of products aren’t already out there, waiting to be used’, says Alexander Pifko, the e-mobility project leader in Gerhard Zenne’s team. ‘And what’s more, many devices that function in an indoor industrial setting cannot cope with tough outdoor working conditions, where the power electronics are constantly exposed to adverse temperatures and weather.’ Given the challenging outdoor requirements, some e-pioneers were hesitant when it came to collaborating on a project like this.
Eventually, the engine technology and chassis construction experts from ZF Friedrichshafen came on board for this demanding project, despite all its unknowns. ‘It was actually a stroke of luck for both parties’, says Gerhard Zenne. Their joint objective was to build a plug-in hybrid with an electric drum motor, generator and battery – with the right power conversion technology and hot and cold temperature management for the battery. Furthermore, it was only possible to add approximately 750 kilograms of extra weight, so that the whole vehicle including its lightweight drum would have a total weight of 4.1 tonnes.
‘During the development process we learned a lot from each other in a relatively short amount of time, both individually and as a team. And as a result we were able to present our ETM as a product ready for series production at Bauma’, says Gerhard Zenne, proudly. One particular challenge was to make the battery the right size. ‘We needed special temperature management. To deliver power immediately, at any time, for example in the depths of winter, the battery has to be at its operating temperature, which can only be done if it is kept at a constant temperature. We even found a solution for that’, explains Andreas Scherzinger, a mobile electronics developer at Liebherr.
By clicking on “ACCEPT”, you consent to the data transmission to Google for this video pursuant to Art. 6 para. 1 point a GDPR. If you do not want to consent to each YouTube video individually in the future and want to be able to load them without this blocker, you can also select “Always accept YouTube videos” and thus also consent to the respectively associated data transmissions to Google for all other YouTube videos that you will access on our website in the future.
You can withdraw given consents at any time with effect for the future and thus prevent the further transmission of your data by deselecting the respective service under “Miscellaneous services (optional)” in the settings (later also accessible via the “Data protection settings” in the footer of our website).
For further information, please refer to our Data Protection Declaration and the Google Privacy Policy.*Google Ireland Limited, Gordon House, Barrow Street, Dublin 4, Ireland; parent company: Google LLC, 1600 Amphitheatre Parkway, Mountain View, CA 94043, USA** Note: The data transfer to the USA associated with the data transmission to Google takes place on the basis of the European Commission’s adequacy decision of 10 July 2023 (EU-U.S. Data Privacy Framework).Noise pollution and harmful emissions are significantly reduced. And unlike hydraulic systems, an electric motor can achieve a minimal rate of rotations which reduces wear on the components.
To keep the truck mixer agile and manoeuvrable on the roads with suitably short wheelbases, the constructors managed to integrate the battery behind the rear drum support unit. This also provided the 32-tonne vehicle with an optimal axle load.
There are lots of benefits to having an electric motor when using the truck mixer. ‘Noise pollution and harmful emissions are significantly reduced. And unlike hydraulic systems, an electric motor can achieve a minimal rate of rotations which reduces wear on the components.’ Apparently, it can even transport and mix stiff category F1 and F2 concretes without any trouble.
As a plug-in hybrid, the battery can be charged either by the diesel-powered generator or by plugging it in to an electrical outlet. ‘During a typical 30-minute drive to a construction site, the diesel-powered generator charges the battery. When the drum is being filled at the concrete factory, power is supplied by plugging it into an electrical outlet, either at 22 kW or a supercharged 50 kW’, explains the project leader Alexander Pifko. Thus, with an average of six journeys from the mixing factory to the construction site and back, there are a total of 12 charging cycles. ‘That’s an optimal charging system, which supplies permanent power’. And since Liebherr has already agreed a system voltage of 650V/DC with the vehicle manufacturers, it is already future-proof.
For fleet managers, operating costs are just as important a consideration. ‘Despite a slight increase in diesel consumption by the generator, the e-truck mixer boasts overall fuel savings of about 30%’, calculates Gerhard Zenne. After all, there is no longer a need for a diesel motor to rotate the mixing drum at the mixing unit or the construction site, as the energy is supplied entirely by the battery. ‘It’s a fantastic base to build on for the future.’