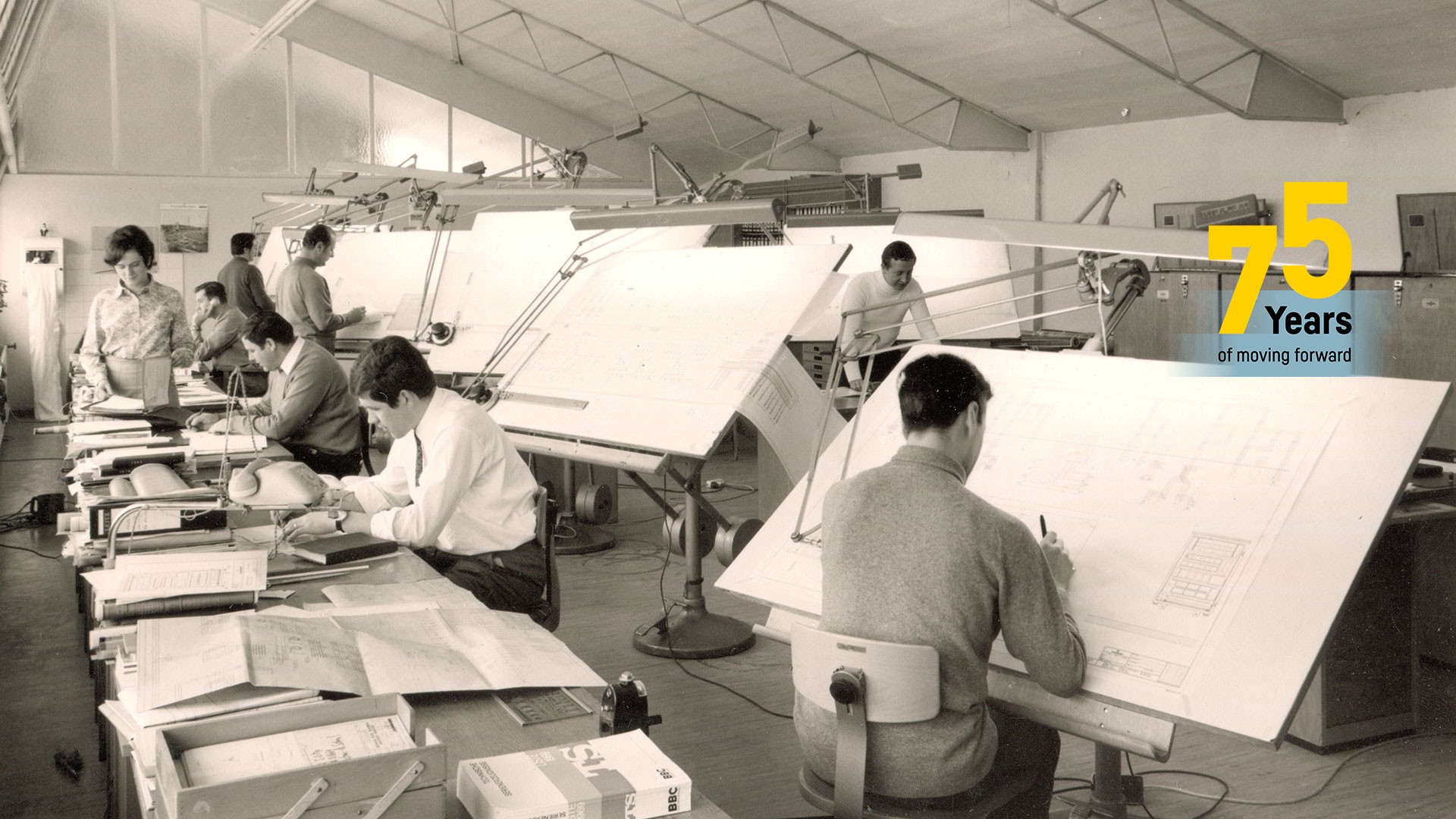
June 2024
Determined to make a difference: pioneering spirit – yesterday, today and tomorrow
When Hans Liebherr invented the mobile tower crane in 1949, he paved the way for a global enterprise and a wide spectrum of groundbreaking innovations in a range of different technological fields. His pioneering spirit has been ingrained in the very fabric of Liebherr ever since.
‘The only constant in life is change,’ even Leonardo da Vinci subscribed to this principle. The polymath ventured the unimaginable, engineering a parachute, a robotic knight and a muscle-powered helicopter. While some considered him a genius, others saw him as a sorcerer or simply denounced him as insane.
Today, we know for certain: it takes more than a momentary flash of inspiration to truly open up new horizons. As well as having the right idea at the right time in the right place, innovators must have the capacity to really get an innovation off the ground. So it was that in 1949 – faced with the enormous challenges of rebuilding towns and cities decimated by war – Hans Liebherr invented a mobile tower crane. A stroke of mechanical genius that would revolutionise work on the construction site and the way we see and achieve great objectives. ‘With dogged determination, it is also possible to achieve what appear to be almost unattainable targets. Don’t allow yourself to be disheartened by setbacks, having faith can move mountains’ – this was the mantra of the company founder.
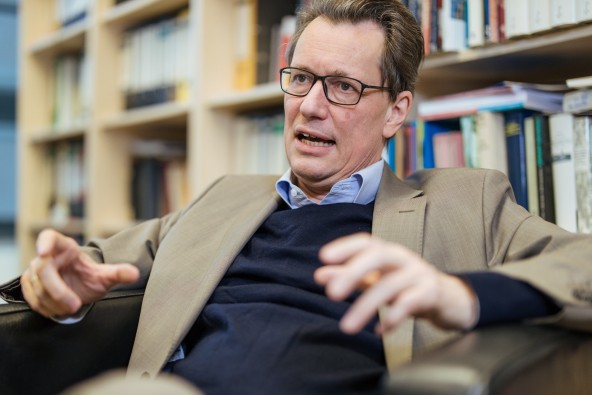
Ultra-fit for the future
According to technology historian and future researcher Professor Hans-Liudger Dienel from the Faculty for Work Sciences, Technology and Participation at the Technische Universität Berlin Institute of Technology, there is a particular strength to this kind of pioneering spirit: ‘Anyone who can fully devote themselves to something with this basic trust will find countless opportunities to venture into uncharted territory, to develop innovative, pragmatic solutions and to continuously expand the product programme.’
The following examples of developments and groundbreaking projects from the world of Liebherr offer insight into the extensive impact that more than 75 years of this special pioneering spirit have had across all product segments – yesterday, today and tomorrow. Perhaps if Leonardo da Vinci were to read these, he might be inclined to rephrase the principle he lived by: the only constant in life is change – and it gets faster and more beguiling over time. Before then flying off in his helicopter.
Digitalisation – systematic progress
Safety and efficiency on the construction site place stringent requirements on cranes and their operators. This is why Liebherr combines extensive expertise in engineering and digital fields, raising the planning and management of work operations to a whole new level. For the benefit of the people on site.
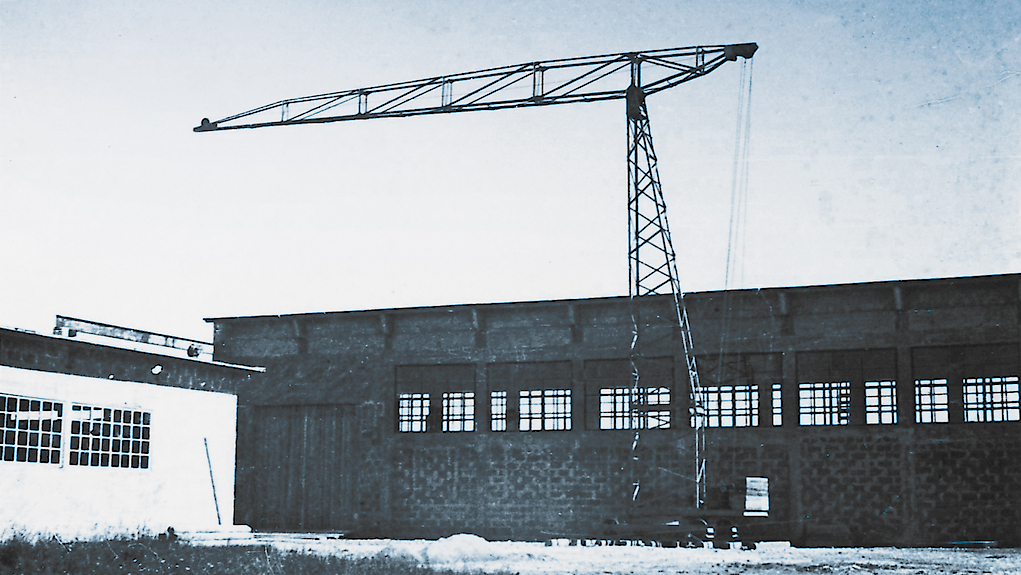
Yesterday
In the right place at the right time – with the right technology: in 1949, Hans Liebherr presents the world’s first mobile tower crane, the TK 10. A revolution on the construction site: it can be assembled easily on site for fast and low-cost setup and dismantling. A pioneering innovation that accelerates and dramatically simplifies Germany’s post-war reconstruction. This paves the way for the Group we know today and its enduring success.
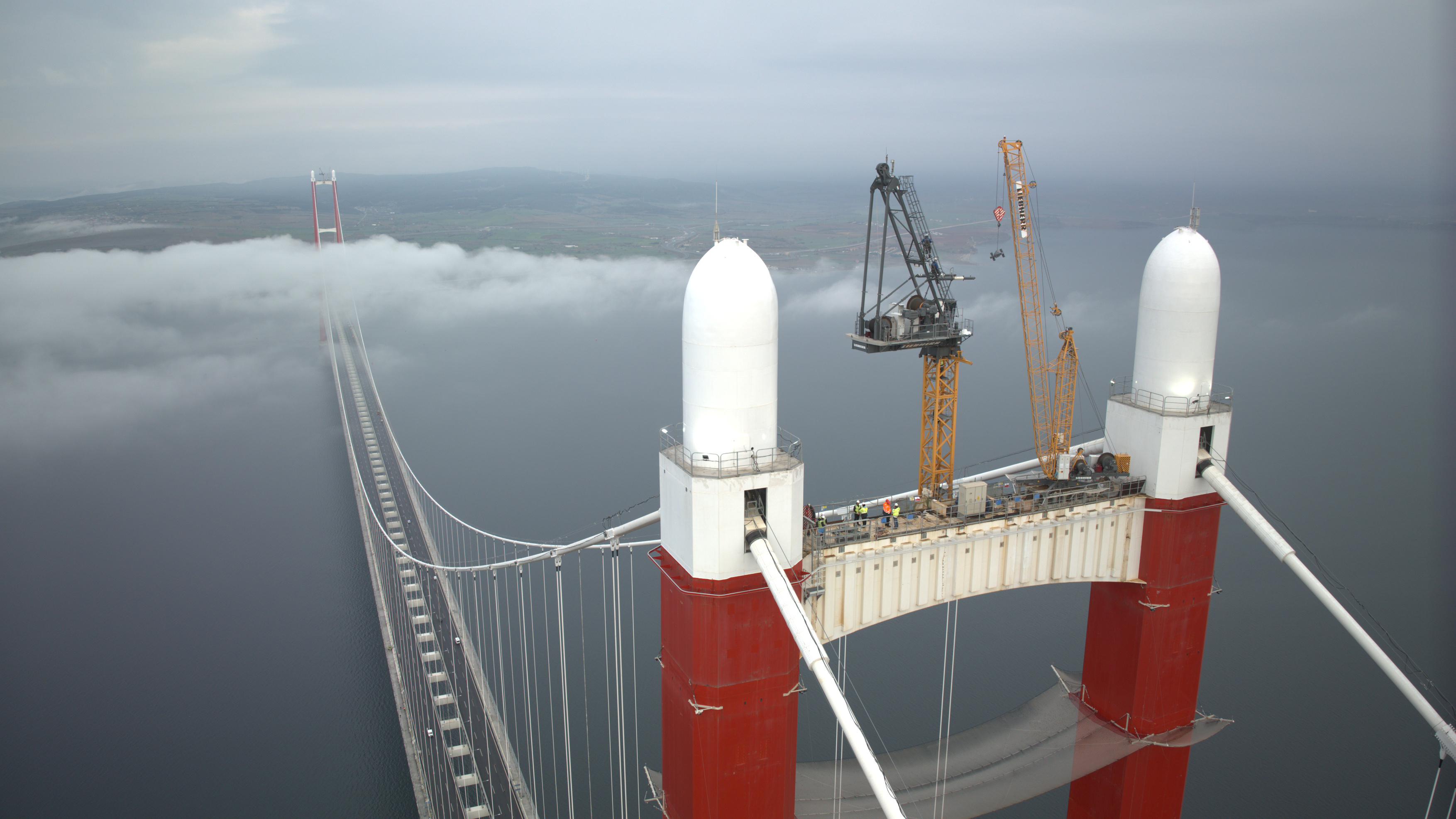
Today
Liebherr has continuously fine-tuned the idea of a flexible, quick-assembly and economical tower crane. Innovations such as the fibre rope for top-slewing cranes, mobile construction cranes with their taxi crane concept or digital solutions, such as MyLiebherr, are shaping this technological progress. In services surrounding crane operation, too, Liebherr always offers its customers holistic solutions to tackle individual challenges. This is how, for instance, the Group’s Tower Crane Solutions department has come to specialise in advising on and planning major and specialist projects as well as specialist applications for tower cranes in the fields of mines and mining, shipyards and (power) plant construction. For these projects, the team of experienced specialists uses Liebherr’s global network and coordinates the collaboration between different departments, e.g., design, structural engineering, production, sales, rental and service. Using CAD-supported digital planning of construction sites, Liebherr can provide customers with a comprehensive service for economical crane deployment in their building projects. On the construction site itself, intelligent assistance systems simplify the work of crane operators, counteract dangerous situations such as excessive swinging of the load, and contribute to significantly increased safety.
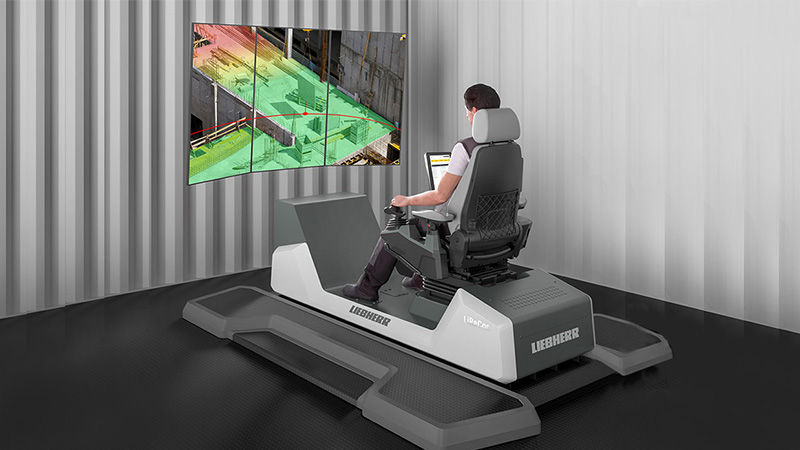
Tomorrow
Safety and efficiency on the construction site are and will always be a main focus of Liebherr’s. This is where Liebherr combines foresight with decades of practical experience and extensive knowledge of engineering and digital technologies. Liebherr’s developments unite cutting-edge technology with highly cost-effective design. In future, more assistant systems and networked systems will facilitate automated processes on the construction site, which form the basis for teleoperation. With the Liebherr Remote Control system (LiReCon) for tower cranes, machine controls for multiple cranes can in future be positioned right next to the foreperson, for instance. This allows crane operators and forepersons to interact and discuss any changes to the construction process straight away and face-to-face. This development will help to enhance safety on construction sites in the future. All segments in the Group are working towards remote operation. After all, LiReCon will make it possible to switch between different construction machines in the future.
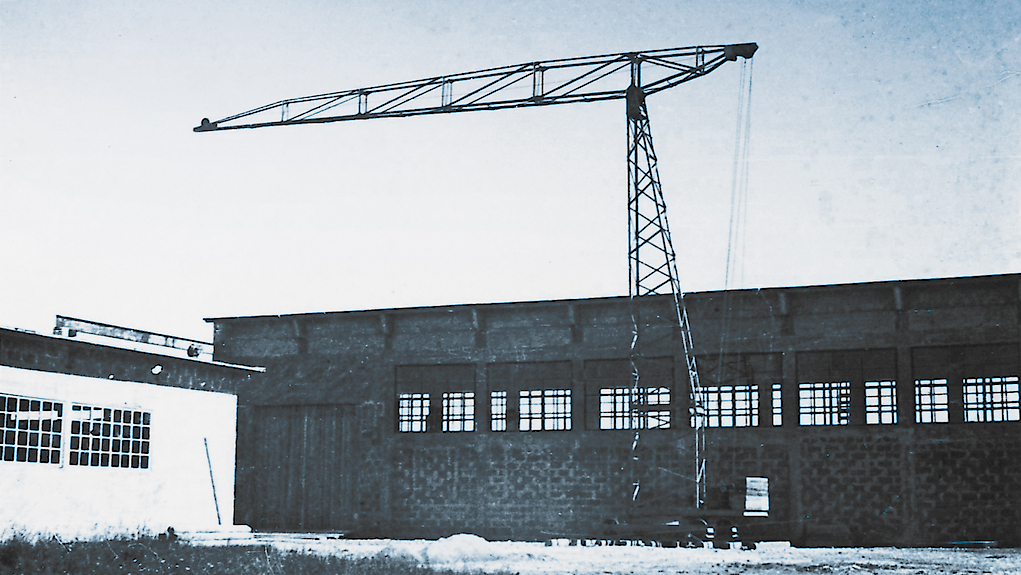
Yesterday
In the right place at the right time – with the right technology: in 1949, Hans Liebherr presents the world’s first mobile tower crane, the TK 10. A revolution on the construction site: it can be assembled easily on site for fast and low-cost setup and dismantling. A pioneering innovation that accelerates and dramatically simplifies Germany’s post-war reconstruction. This paves the way for the Group we know today and its enduring success.
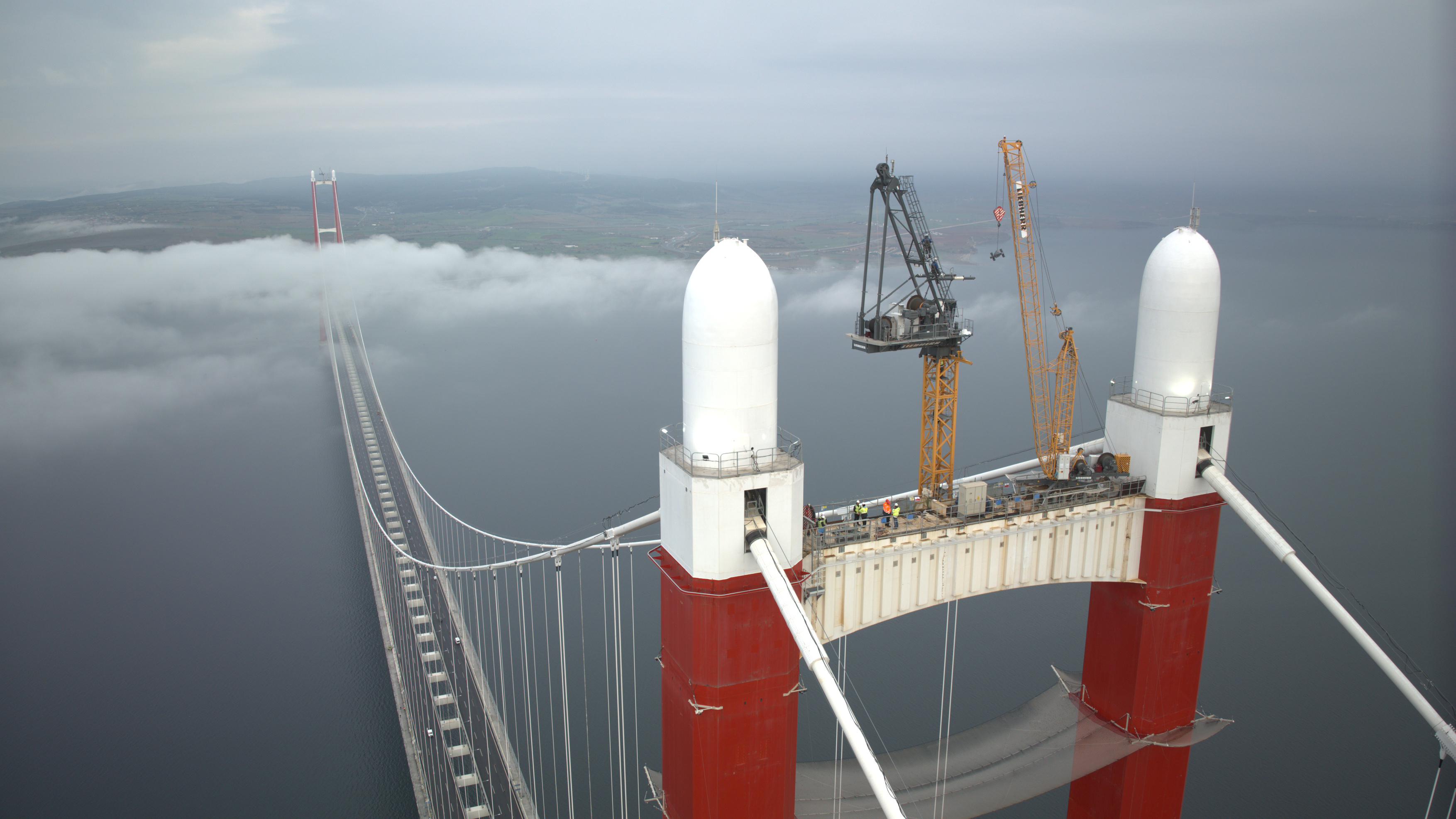
Today
Liebherr has continuously fine-tuned the idea of a flexible, quick-assembly and economical tower crane. Innovations such as the fibre rope for top-slewing cranes, mobile construction cranes with their taxi crane concept or digital solutions, such as MyLiebherr, are shaping this technological progress. In services surrounding crane operation, too, Liebherr always offers its customers holistic solutions to tackle individual challenges. This is how, for instance, the Group’s Tower Crane Solutions department has come to specialise in advising on and planning major and specialist projects as well as specialist applications for tower cranes in the fields of mines and mining, shipyards and (power) plant construction. For these projects, the team of experienced specialists uses Liebherr’s global network and coordinates the collaboration between different departments, e.g., design, structural engineering, production, sales, rental and service. Using CAD-supported digital planning of construction sites, Liebherr can provide customers with a comprehensive service for economical crane deployment in their building projects. On the construction site itself, intelligent assistance systems simplify the work of crane operators, counteract dangerous situations such as excessive swinging of the load, and contribute to significantly increased safety.
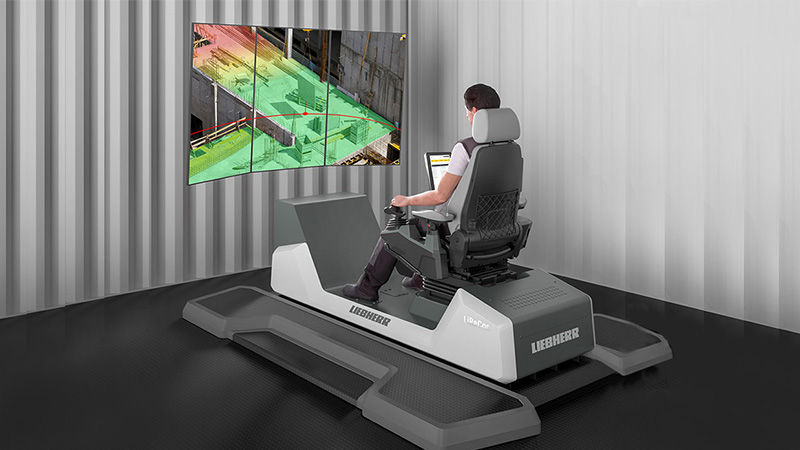
Tomorrow
Safety and efficiency on the construction site are and will always be a main focus of Liebherr’s. This is where Liebherr combines foresight with decades of practical experience and extensive knowledge of engineering and digital technologies. Liebherr’s developments unite cutting-edge technology with highly cost-effective design. In future, more assistant systems and networked systems will facilitate automated processes on the construction site, which form the basis for teleoperation. With the Liebherr Remote Control system (LiReCon) for tower cranes, machine controls for multiple cranes can in future be positioned right next to the foreperson, for instance. This allows crane operators and forepersons to interact and discuss any changes to the construction process straight away and face-to-face. This development will help to enhance safety on construction sites in the future. All segments in the Group are working towards remote operation. After all, LiReCon will make it possible to switch between different construction machines in the future.
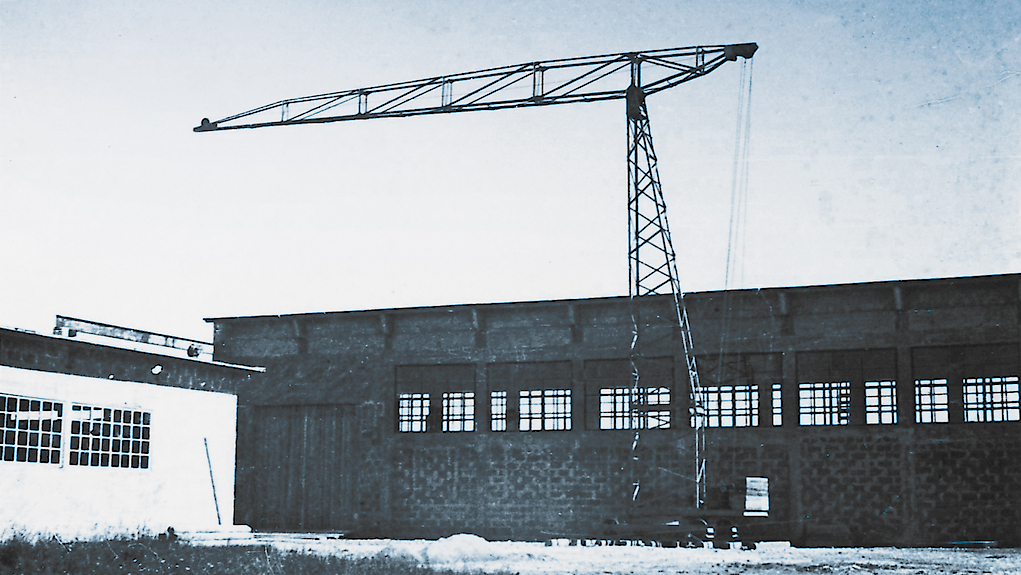
Yesterday
In the right place at the right time – with the right technology: in 1949, Hans Liebherr presents the world’s first mobile tower crane, the TK 10. A revolution on the construction site: it can be assembled easily on site for fast and low-cost setup and dismantling. A pioneering innovation that accelerates and dramatically simplifies Germany’s post-war reconstruction. This paves the way for the Group we know today and its enduring success.
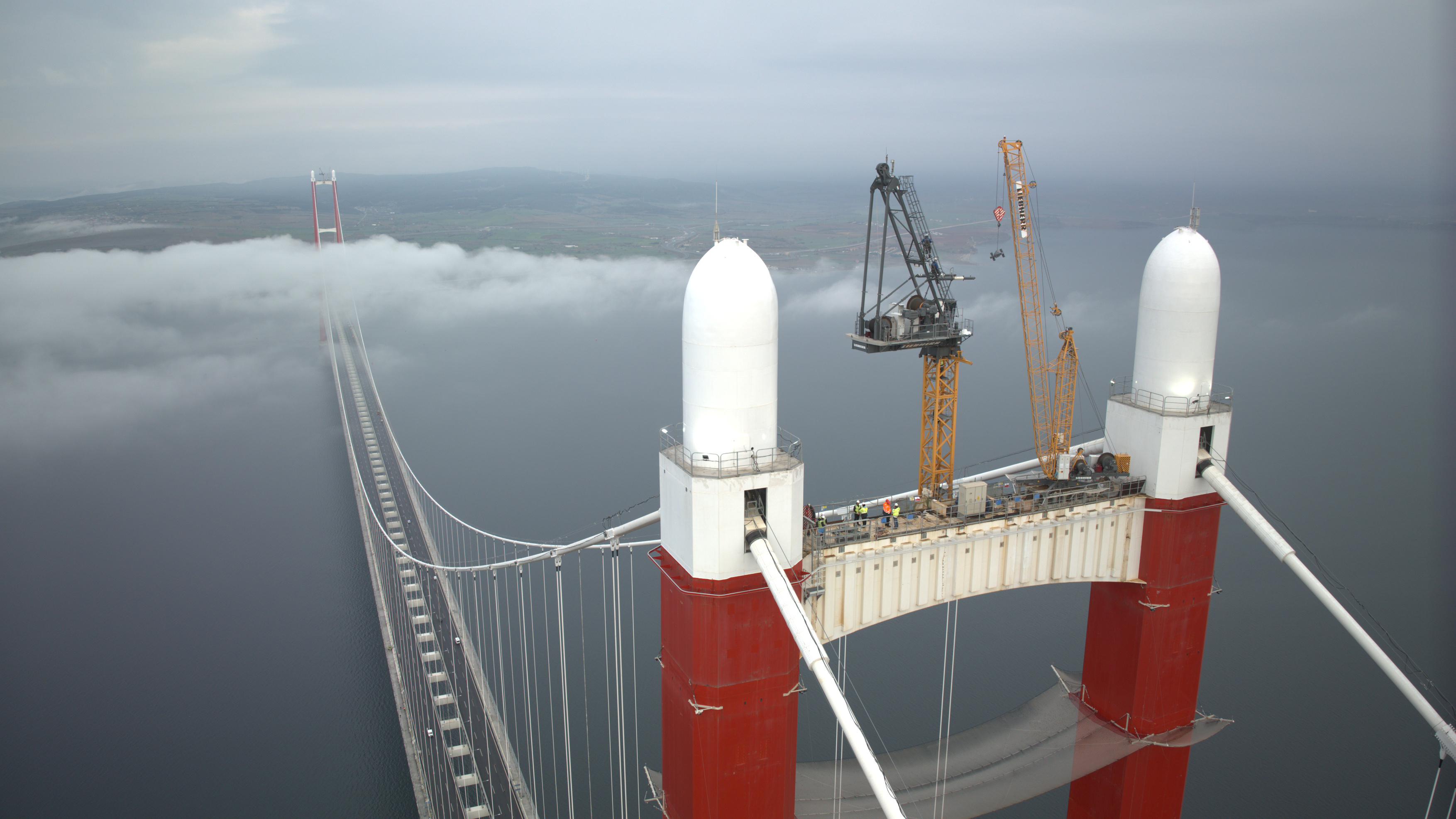
Today
Liebherr has continuously fine-tuned the idea of a flexible, quick-assembly and economical tower crane. Innovations such as the fibre rope for top-slewing cranes, mobile construction cranes with their taxi crane concept or digital solutions, such as MyLiebherr, are shaping this technological progress. In services surrounding crane operation, too, Liebherr always offers its customers holistic solutions to tackle individual challenges. This is how, for instance, the Group’s Tower Crane Solutions department has come to specialise in advising on and planning major and specialist projects as well as specialist applications for tower cranes in the fields of mines and mining, shipyards and (power) plant construction. For these projects, the team of experienced specialists uses Liebherr’s global network and coordinates the collaboration between different departments, e.g., design, structural engineering, production, sales, rental and service. Using CAD-supported digital planning of construction sites, Liebherr can provide customers with a comprehensive service for economical crane deployment in their building projects. On the construction site itself, intelligent assistance systems simplify the work of crane operators, counteract dangerous situations such as excessive swinging of the load, and contribute to significantly increased safety.
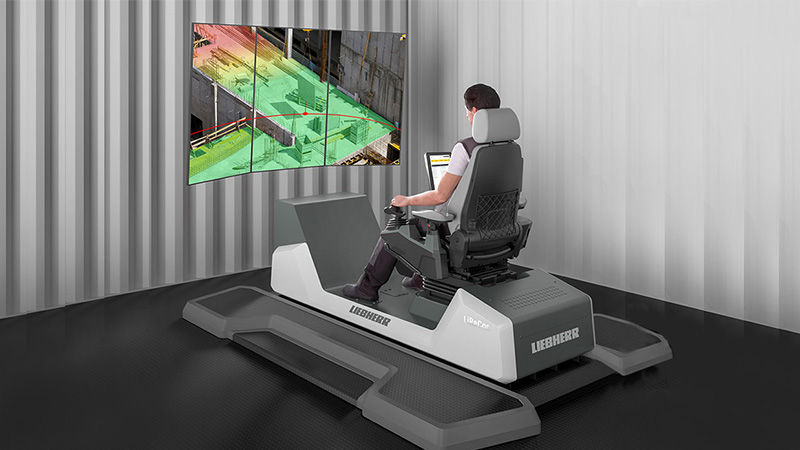
Tomorrow
Safety and efficiency on the construction site are and will always be a main focus of Liebherr’s. This is where Liebherr combines foresight with decades of practical experience and extensive knowledge of engineering and digital technologies. Liebherr’s developments unite cutting-edge technology with highly cost-effective design. In future, more assistant systems and networked systems will facilitate automated processes on the construction site, which form the basis for teleoperation. With the Liebherr Remote Control system (LiReCon) for tower cranes, machine controls for multiple cranes can in future be positioned right next to the foreperson, for instance. This allows crane operators and forepersons to interact and discuss any changes to the construction process straight away and face-to-face. This development will help to enhance safety on construction sites in the future. All segments in the Group are working towards remote operation. After all, LiReCon will make it possible to switch between different construction machines in the future.
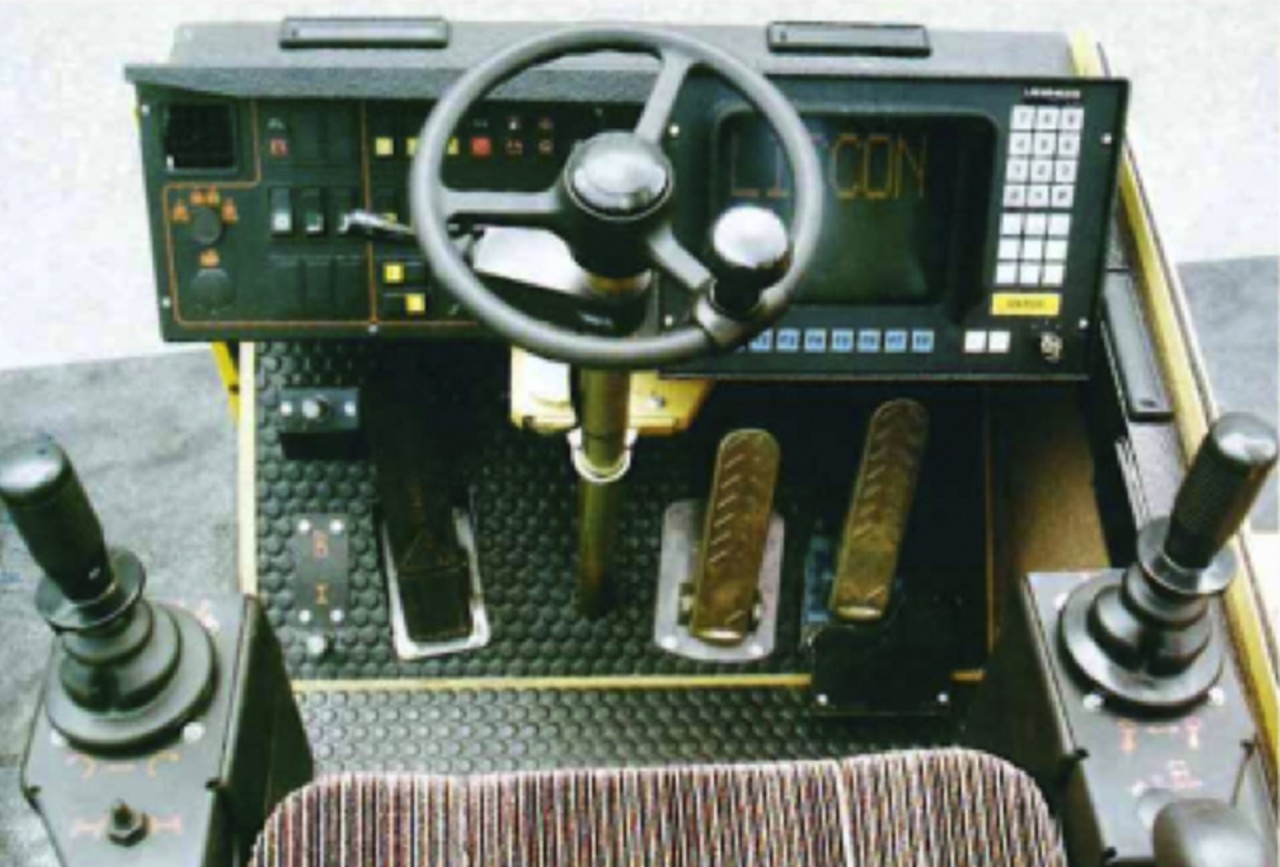
Yesterday
In 1977, Liebherr presents the LTM1025. With a telescopic boom length of 24metres and a load capacity of 25tonnes, the new mobile crane can be deployed on-road as well as off-road for never-before-seen perfection. This pioneering achievement is recognised across the industry and the term ‘all-terrain crane’ is coined. Once again, Liebherr is able to set the benchmark. In the mid-1980s, electronics are gaining more and more impact, even in crane construction, and Liebherr developers revolutionise the previously predominant plug-in card principle of crane control. The solution: ‘Liebherr Computed Control’ – LICCON for short. Central, simple and practical – that’s the guiding principle. ‘We integrated hardware components into a control system whose logic we had designed and programmed ourselves,’ explains Erwin Morath, head of the control department at the time. ‘LICCON was thus unique and could not be copied by the competition.’
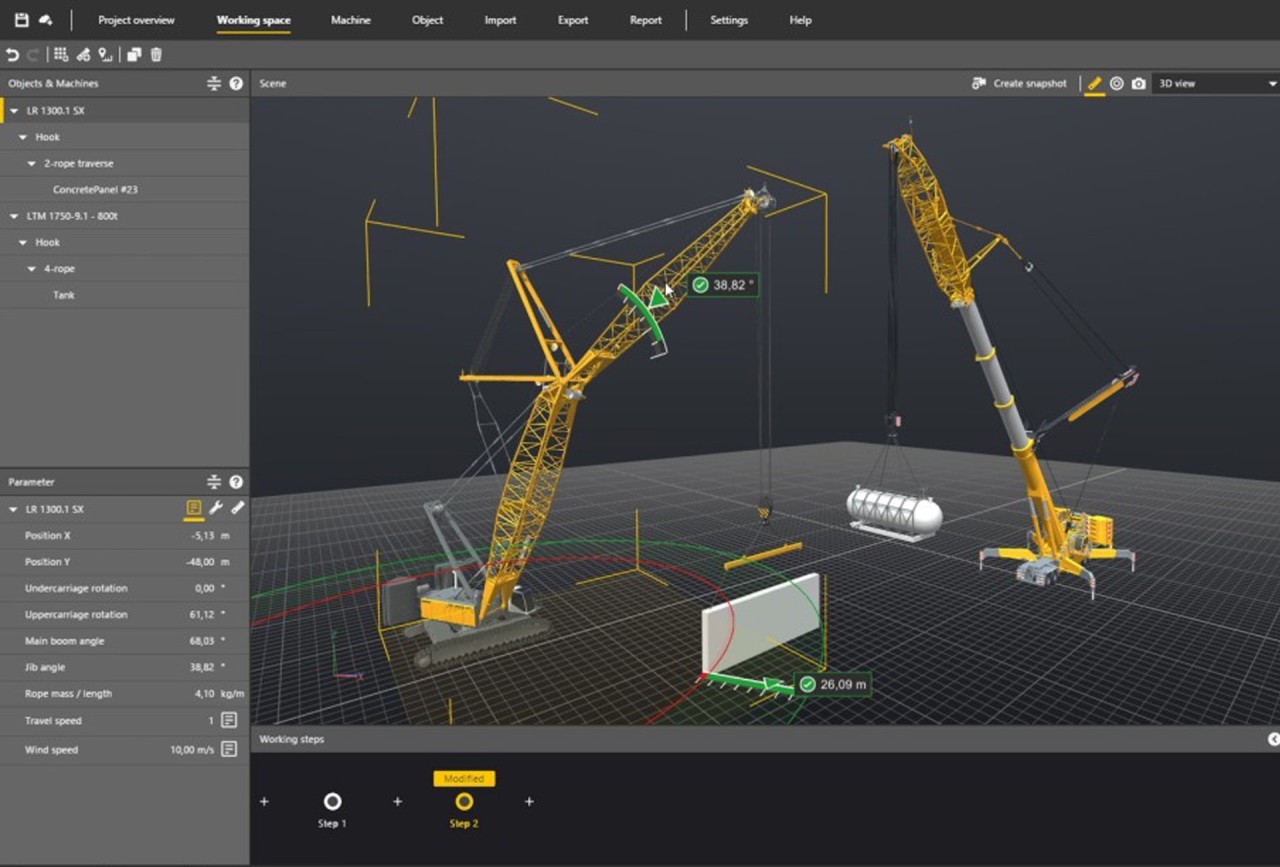
Today
Mobile and crawler cranes are becoming ever more powerful – and more sophisticated. They are also faced with increasing standards for maximum safety. To fulfil these standards, more and more safety systems are being integrated, including cameras, sensors, automated assistance systems and remote control for a better view of the load or of what’s happening around the lift during operations. The latest crane data in the work process is used in real time and visualised on the monitor in the crane cab. This also allows for more extensive and more complex data management. It is also laying the foundation for the new CranePlanner2.0. With this digital planning tool, users can adjust the crane to their exact application scenarios, test functions and clarify the necessary safety conditions. This is opening up a brand new and greatly expanded horizon for planning.
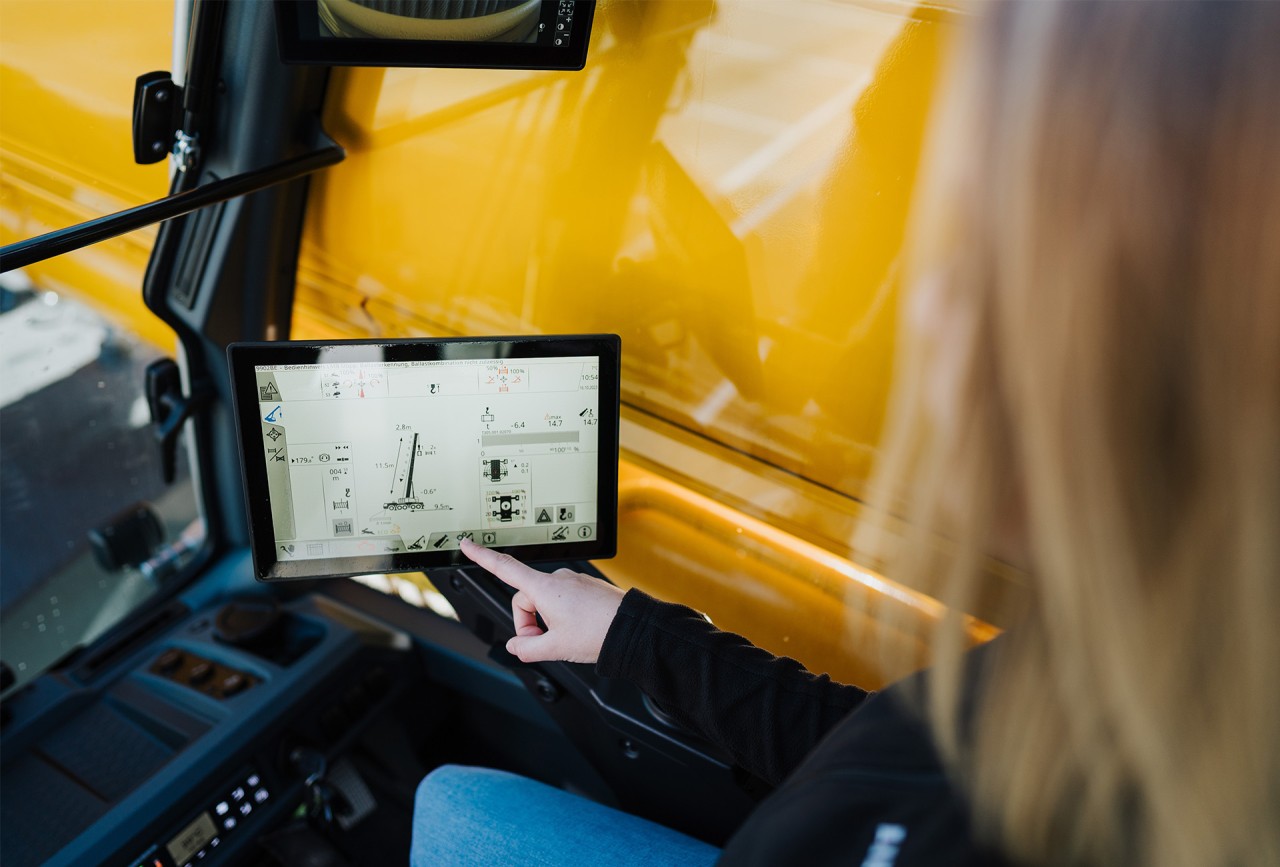
Tomorrow
Increasingly complex construction sites and more stringent requirements for mobile and crawler cranes are shifting the focus of Liebherr’s research and development onto the expansion and integration of intelligent assistance systems. One such development is LICCON3. With this latest version of crane control, Liebherr is setting yet another milestone in the industry – with fast data bus, new programming language and software, significantly more memory, higher processing power and improved safety tools. However, digitalisation is not an end in itself. As in the company’s formative days, technology continues to serve a function at Liebherr. At the centre of it all, however, are the people. To support crane operators in their increasingly challenging and high-responsibility job, Liebherr will therefore not only bring control and the latest digital tools to the design, but also prioritise ergonomic and safe working operations for crane assembly or setup tasks.
Technology-neutral approach – making the possible possible
Construction vehicles/machines and units need to meet high standards when it comes to performance, robustness, safety and reliability – often in the toughest conditions. This is why Liebherr is committed to providing the right drive solutions for every circumstance.
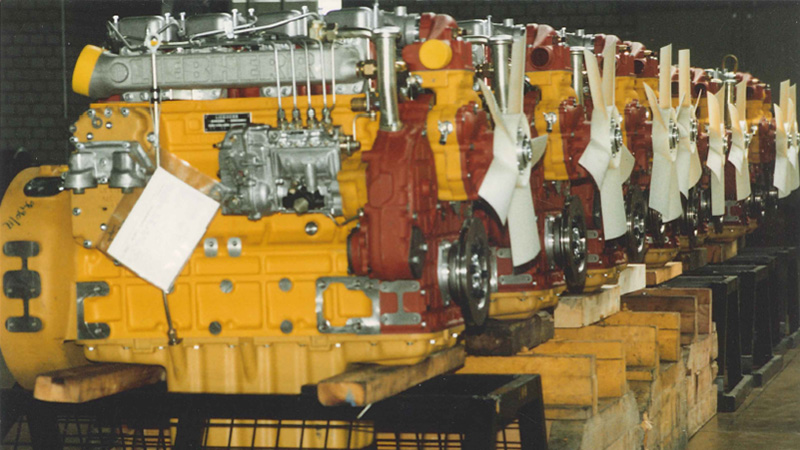
Yesterday
In the 1970s and 1980s, standard built-in engines on the market are derived from HGV drives. The drawback of this is that the often air-cooled engines prove to be neither reliable nor durable enough for use in heavy construction machines. On top of all that, they often need repairing during off-road operations. Moreover the supply of spare parts and availability of customer services are not always guaranteed worldwide. In 1981, Hans Liebherr therefore decides to develop in-house combustion engines for construction machines: robust, powerful, economical. So, in 1985, the first series-production engines, the D924 and D926, roll off the conveyor at Liebherr Machines Bulle S.A. in Switzerland. Some of these are still in production today.
Liebherr is continuously developing the engine portfolio further to reflect the ever-changing requirements of the respective industry, the legislation, the customer and environment. The standard basic engine is testament to decades of system expertise. Using the modular principle, this can be modified for compliance with the exhaust gas aftertreatment regulations of different countries and regions.
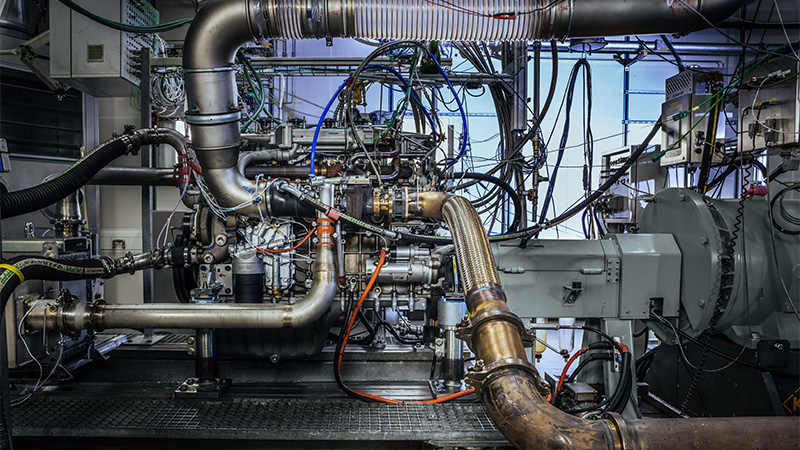
Today
The key components of a drivetrain, such as injection systems, controls, engines, gearboxes, etc., are developed and produced in-house by Liebherr. This allows the necessary flexibility to adapt to the specific requirements of individual construction machines.
The product range today spans from four-cylinder engines with 140 kW power to D98 series engines with up to 4.3MW power. A technology-neutral approach is a basic prerequisite for developing a suitable drive solution for the applications in question.
„Besides alternative fuels like HVO, Liebherr is committed to green hydrogen as a key alternative for driving down emissions. Hydrogen-combustion engines can be used anywhere, where batteries or fuel cells reach their limits. For example, this may include applications on construction sites where heavy vibrations or impurities are generated or when providing the energy needed to deliver competitive machine productivity results in excessive running costs.
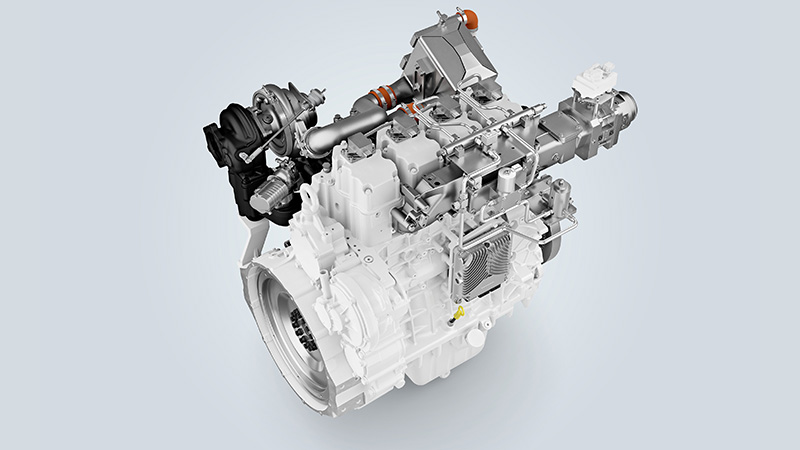
Tomorrow
A pioneering spirit is always clearly focused on the future. For instance, in light of global warming, legislators and society in general are calling for the decarbonisation of the construction and industrial sectors. Within the components product segment, Liebherr is working on alternative drive solutions, including the developing of hydrogen engines. Beyond this, the company is researching specialist injection solutions to further optimise the combustion and power density.
Liebherr is also working on a dual-fuel engine, which can be powered by hydrogen and HVO or HVO alone. Electric motors are also being further developed specifically for use in battery-powered or hybrid vehicles and machinery. The new-generation motors are more compact and require less maintenance than their predecessors.
Another pioneering innovation is the mobile energy storage system, Liduro Power Port. This flexible and highly efficient solution supplies electrical machines and machine fleets with energy on site of use, representing a major milestone on the path to zero-emissions construction sites.
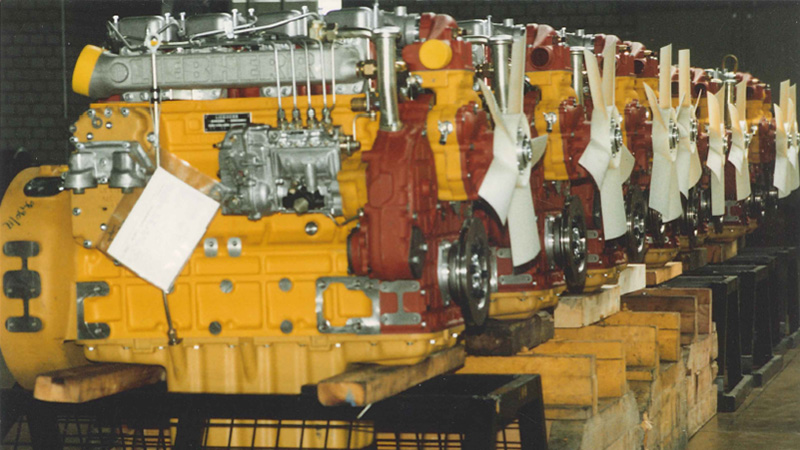
Yesterday
In the 1970s and 1980s, standard built-in engines on the market are derived from HGV drives. The drawback of this is that the often air-cooled engines prove to be neither reliable nor durable enough for use in heavy construction machines. On top of all that, they often need repairing during off-road operations. Moreover the supply of spare parts and availability of customer services are not always guaranteed worldwide. In 1981, Hans Liebherr therefore decides to develop in-house combustion engines for construction machines: robust, powerful, economical. So, in 1985, the first series-production engines, the D924 and D926, roll off the conveyor at Liebherr Machines Bulle S.A. in Switzerland. Some of these are still in production today.
Liebherr is continuously developing the engine portfolio further to reflect the ever-changing requirements of the respective industry, the legislation, the customer and environment. The standard basic engine is testament to decades of system expertise. Using the modular principle, this can be modified for compliance with the exhaust gas aftertreatment regulations of different countries and regions.
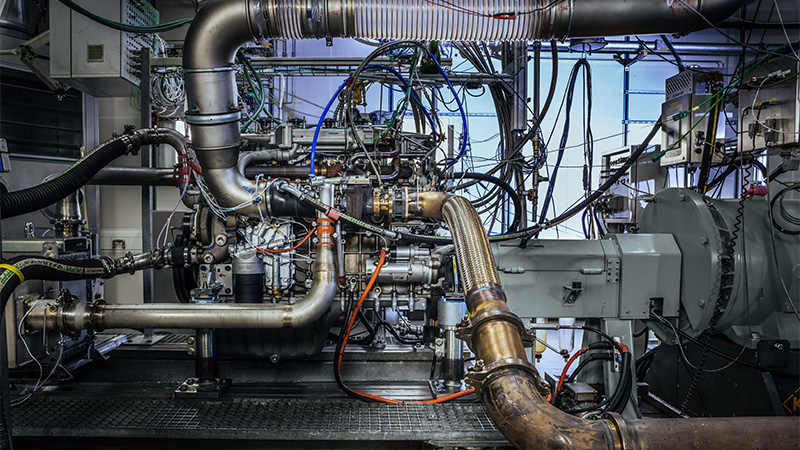
Today
The key components of a drivetrain, such as injection systems, controls, engines, gearboxes, etc., are developed and produced in-house by Liebherr. This allows the necessary flexibility to adapt to the specific requirements of individual construction machines.
The product range today spans from four-cylinder engines with 140 kW power to D98 series engines with up to 4.3MW power. A technology-neutral approach is a basic prerequisite for developing a suitable drive solution for the applications in question.
„Besides alternative fuels like HVO, Liebherr is committed to green hydrogen as a key alternative for driving down emissions. Hydrogen-combustion engines can be used anywhere, where batteries or fuel cells reach their limits. For example, this may include applications on construction sites where heavy vibrations or impurities are generated or when providing the energy needed to deliver competitive machine productivity results in excessive running costs.
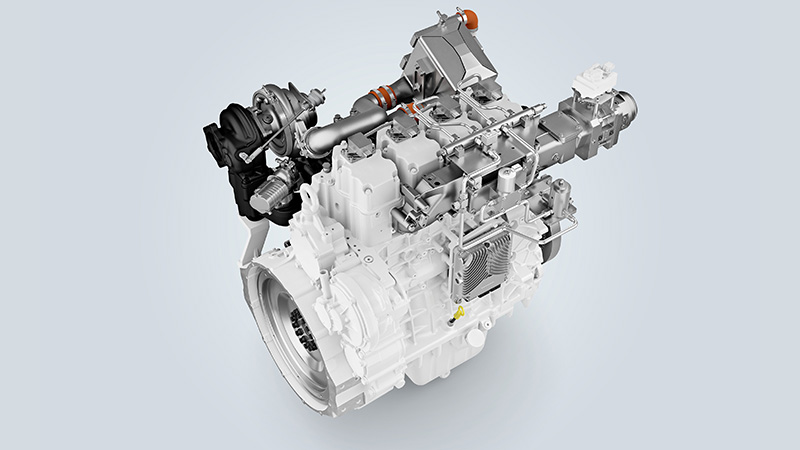
Tomorrow
A pioneering spirit is always clearly focused on the future. For instance, in light of global warming, legislators and society in general are calling for the decarbonisation of the construction and industrial sectors. Within the components product segment, Liebherr is working on alternative drive solutions, including the developing of hydrogen engines. Beyond this, the company is researching specialist injection solutions to further optimise the combustion and power density.
Liebherr is also working on a dual-fuel engine, which can be powered by hydrogen and HVO or HVO alone. Electric motors are also being further developed specifically for use in battery-powered or hybrid vehicles and machinery. The new-generation motors are more compact and require less maintenance than their predecessors.
Another pioneering innovation is the mobile energy storage system, Liduro Power Port. This flexible and highly efficient solution supplies electrical machines and machine fleets with energy on site of use, representing a major milestone on the path to zero-emissions construction sites.
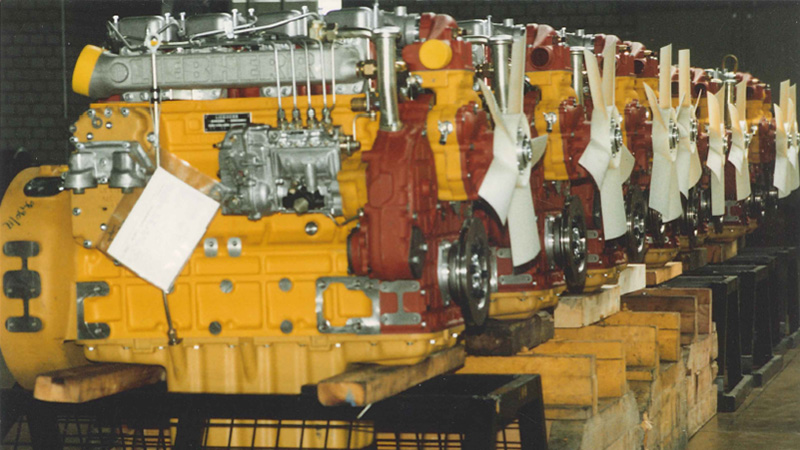
Yesterday
In the 1970s and 1980s, standard built-in engines on the market are derived from HGV drives. The drawback of this is that the often air-cooled engines prove to be neither reliable nor durable enough for use in heavy construction machines. On top of all that, they often need repairing during off-road operations. Moreover the supply of spare parts and availability of customer services are not always guaranteed worldwide. In 1981, Hans Liebherr therefore decides to develop in-house combustion engines for construction machines: robust, powerful, economical. So, in 1985, the first series-production engines, the D924 and D926, roll off the conveyor at Liebherr Machines Bulle S.A. in Switzerland. Some of these are still in production today.
Liebherr is continuously developing the engine portfolio further to reflect the ever-changing requirements of the respective industry, the legislation, the customer and environment. The standard basic engine is testament to decades of system expertise. Using the modular principle, this can be modified for compliance with the exhaust gas aftertreatment regulations of different countries and regions.
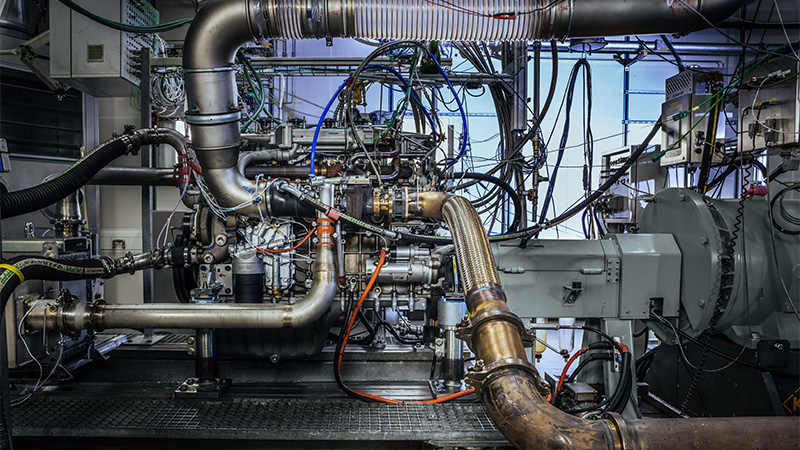
Today
The key components of a drivetrain, such as injection systems, controls, engines, gearboxes, etc., are developed and produced in-house by Liebherr. This allows the necessary flexibility to adapt to the specific requirements of individual construction machines.
The product range today spans from four-cylinder engines with 140 kW power to D98 series engines with up to 4.3MW power. A technology-neutral approach is a basic prerequisite for developing a suitable drive solution for the applications in question.
„Besides alternative fuels like HVO, Liebherr is committed to green hydrogen as a key alternative for driving down emissions. Hydrogen-combustion engines can be used anywhere, where batteries or fuel cells reach their limits. For example, this may include applications on construction sites where heavy vibrations or impurities are generated or when providing the energy needed to deliver competitive machine productivity results in excessive running costs.
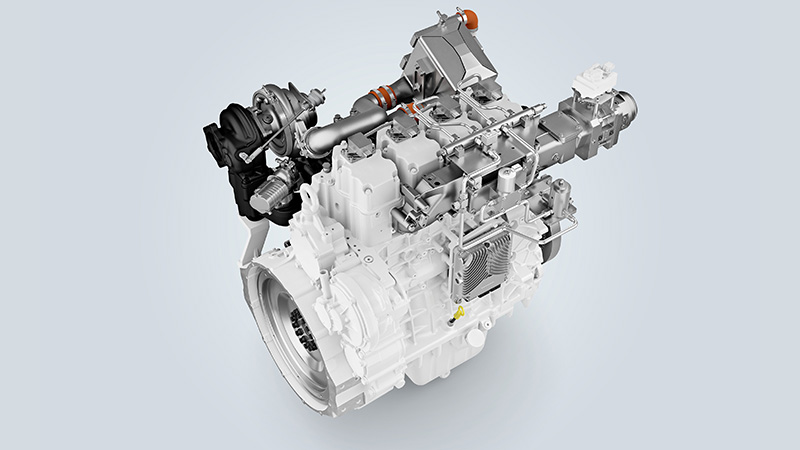
Tomorrow
A pioneering spirit is always clearly focused on the future. For instance, in light of global warming, legislators and society in general are calling for the decarbonisation of the construction and industrial sectors. Within the components product segment, Liebherr is working on alternative drive solutions, including the developing of hydrogen engines. Beyond this, the company is researching specialist injection solutions to further optimise the combustion and power density.
Liebherr is also working on a dual-fuel engine, which can be powered by hydrogen and HVO or HVO alone. Electric motors are also being further developed specifically for use in battery-powered or hybrid vehicles and machinery. The new-generation motors are more compact and require less maintenance than their predecessors.
Another pioneering innovation is the mobile energy storage system, Liduro Power Port. This flexible and highly efficient solution supplies electrical machines and machine fleets with energy on site of use, representing a major milestone on the path to zero-emissions construction sites.
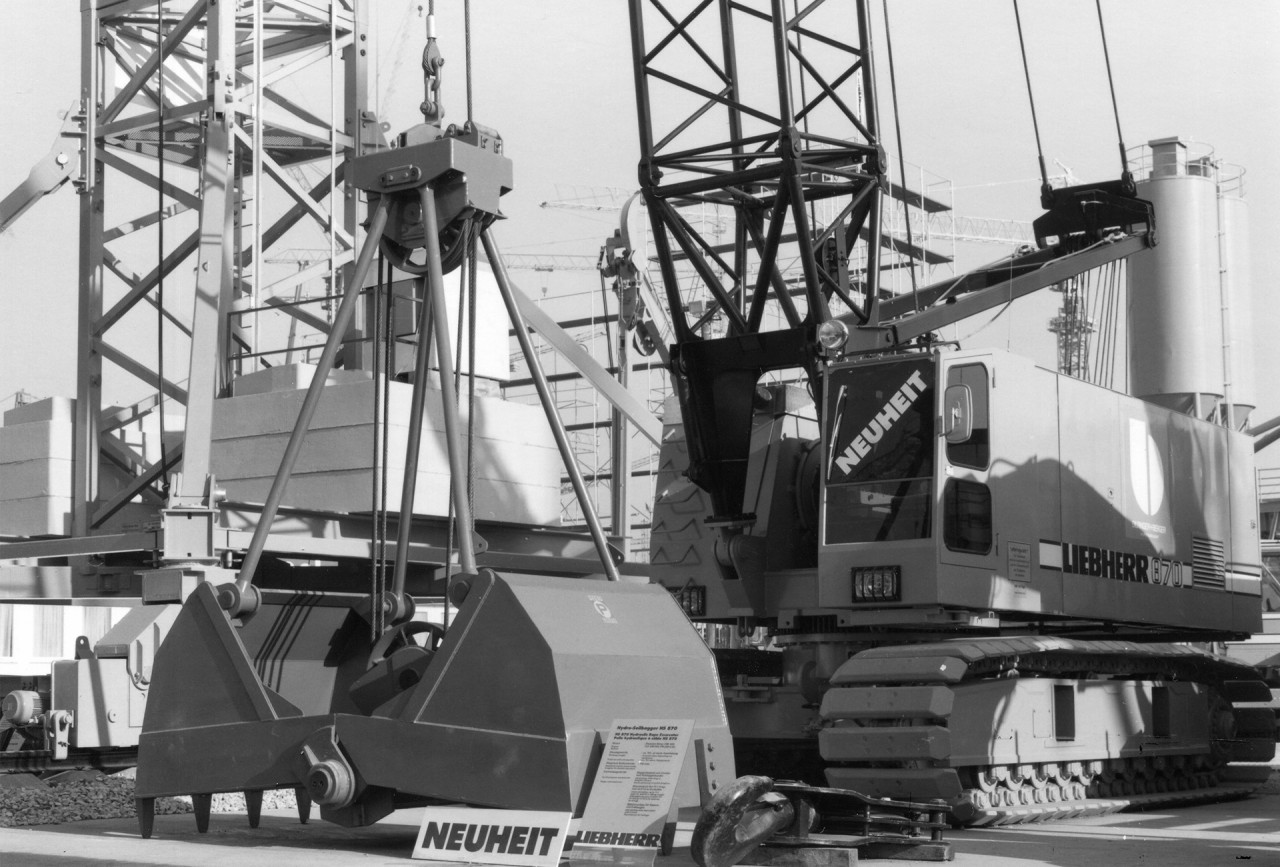
Yesterday
From the 1970s onwards, Liebherr-Werk Nenzing GmbH has been gradually expanding its offering – previously centred around ship cranes and offshore cranes – with a whole range of new products. So, by the end of the 70s, it adds the duty cycle crawler crane to its portfolio, followed in the 90s by a new kind of crawler crane and a series of combined piling and drilling rigs. This is driven by the company’s guiding principle of manufacturing its own machines for the most varied areas of deep foundation application in true Liebherr tradition – ‘all from a single source’.
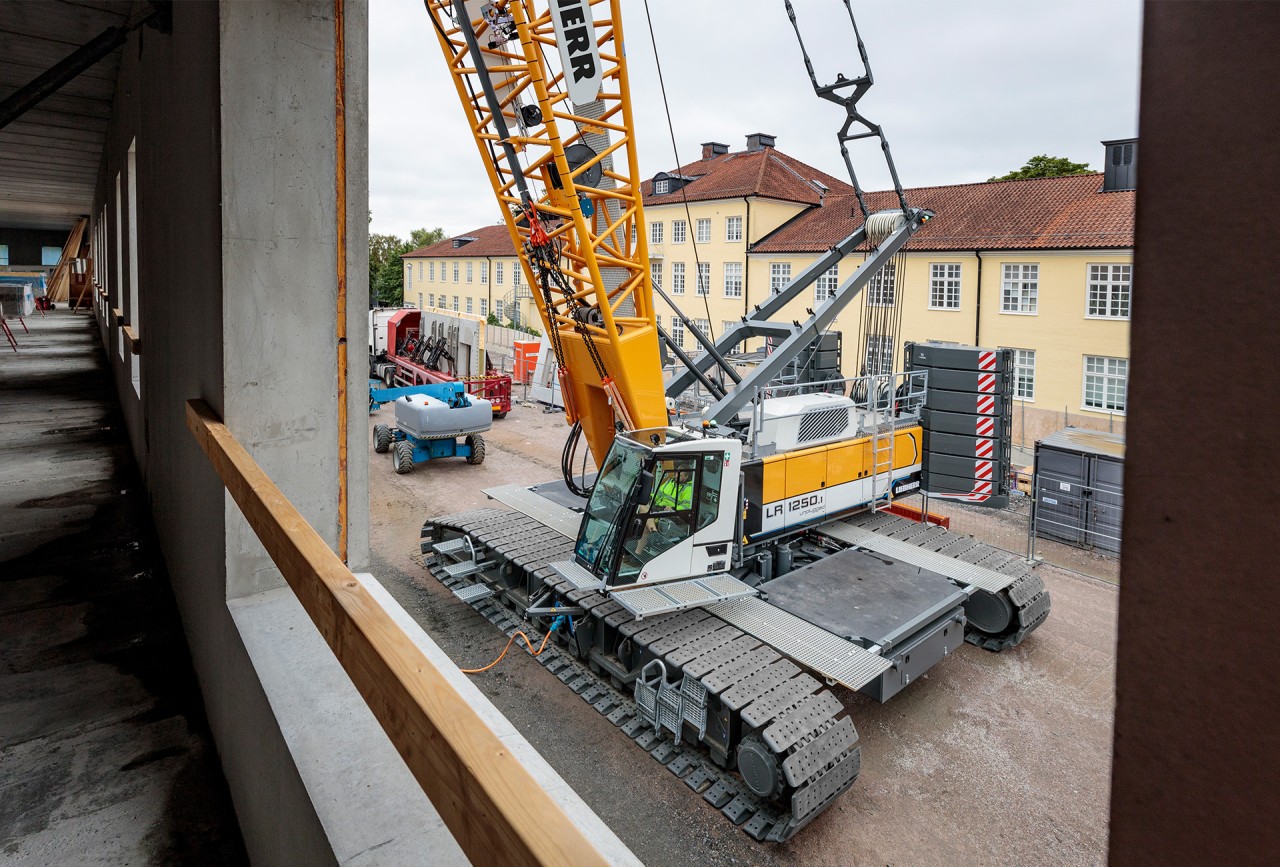
Today
As well as expanding the product families, Nenzing is also particularly focused on the electrification of its portfolio of construction machines. This allows it to meet the growing need for a significant reduction in CO2 and noise emissions. Liebherr's vision of an emission-free future for lifting operations is exemplified in the LR 1250.1 unplugged, the world’s first battery-powered crawler crane, unveiled in 2020. Barely a year later, the first LR 1160.1 unplugged is delivered. In ‘plugged-in’ mode, the crane produces the exact same output as the diesel-powered equivalent. ‘Unplugged’, the crane’s work performance is identical to when powered by the mains. The range in battery mode is currently sufficient for approx. eight hours of crane operation, which can be extended by between 20 and 60% by integrating additional batteries.
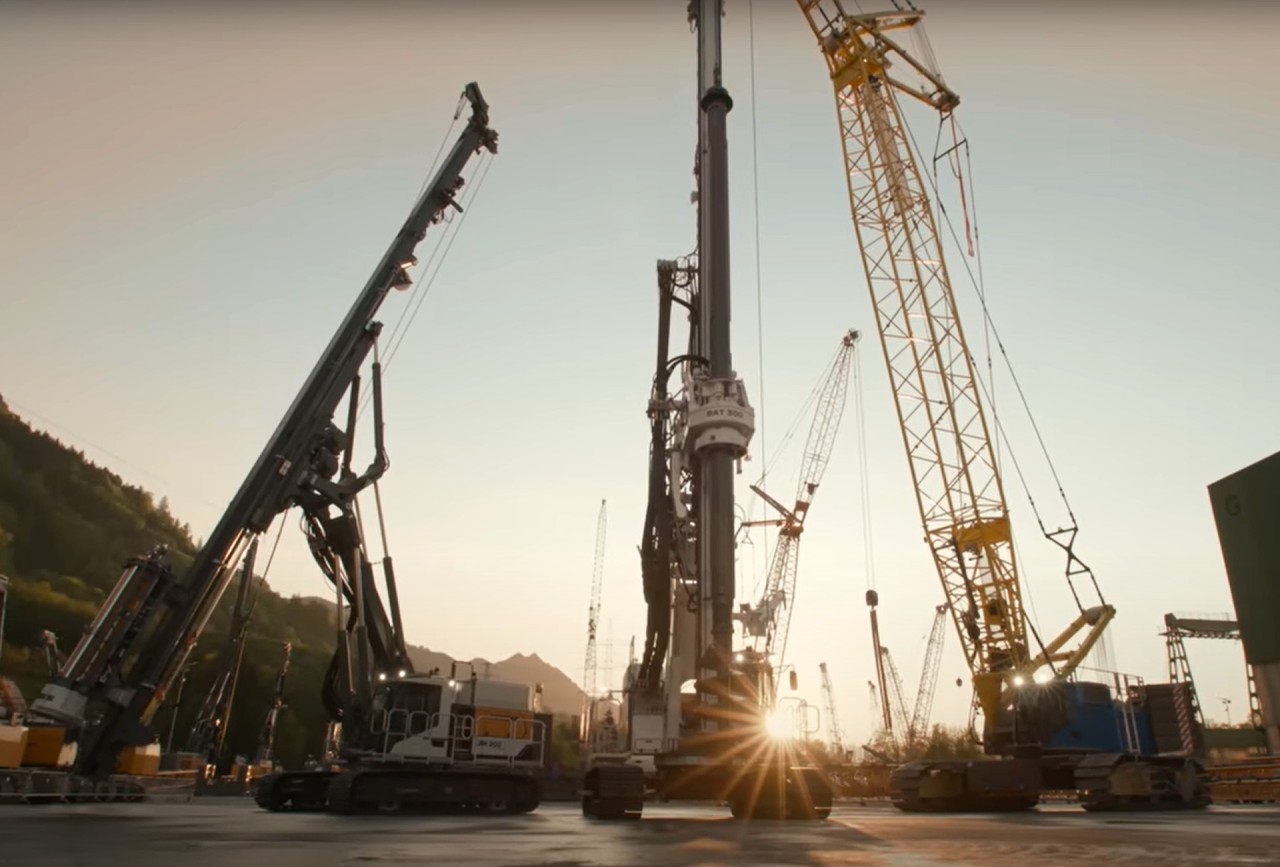
Tomorrow
Achieving zero-emissions is the greatest challenge facing the construction sites of the future. Many towns and cities are already enforcing regulations to further minimise CO2 emissions and to significantly reduce the particle load and noise pollution of construction projects, namely in areas with a high volume of people, such as amusement parks, hospitals and residential areas. ‘The city of Oslo is considered one of the world’s trailblazers for zero-emission construction sites. From 2030, all sites there should be free of emissions,’ says Dietmar Hämmerle, product manager for crawler cranes at Liebherr-Werk Nenzing. ‘We delivered the first unplugged machine to Oslo back in November 2020. With our electric LRunplugged series (LR 1130.1, LR 1160.1, LR 1200.1, LR 1250.1), we have proven that battery-driven zero-emission electric solutions are capable of daily operation without compromise.’
Take a look at the unplugged machines in action here.
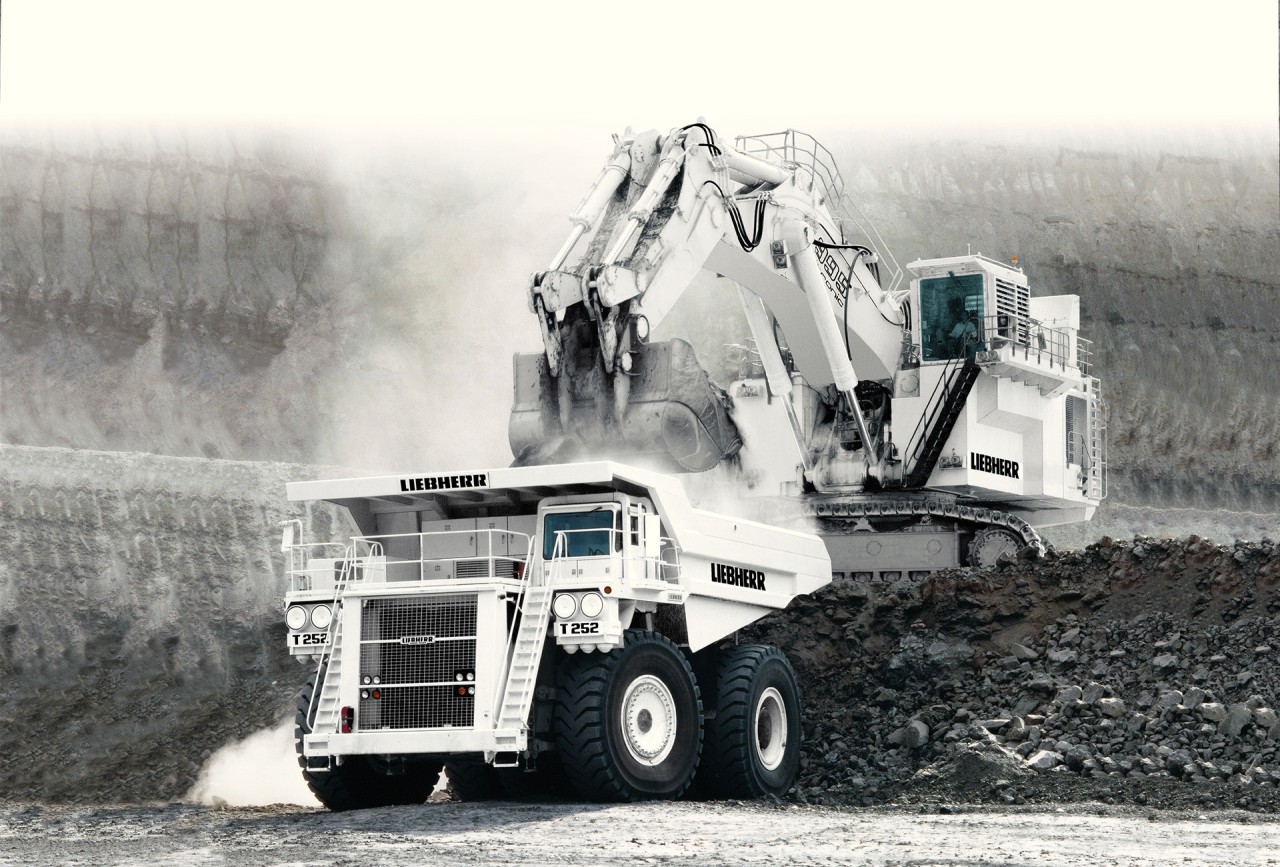
Yesterday
Liebherr’s mining product segment has its origins in the company’s Colmar site (France), which grows during the 1960s to become the leading centre of crawler excavators. The following decade, Liebherr begins producing mining excavators. To get as close as possible to global customers, Liebherr-America Inc. is established in 1970 in Newport News in the US state of Virginia. It is there that, in the 90s, Liebherr expands its business to include mining trucks, cementing the company as an important player in the mining industry. In 2011, mining becomes a dedicated product segment. At its birthplace in Colmar, a new plant is built to expand the segment further.
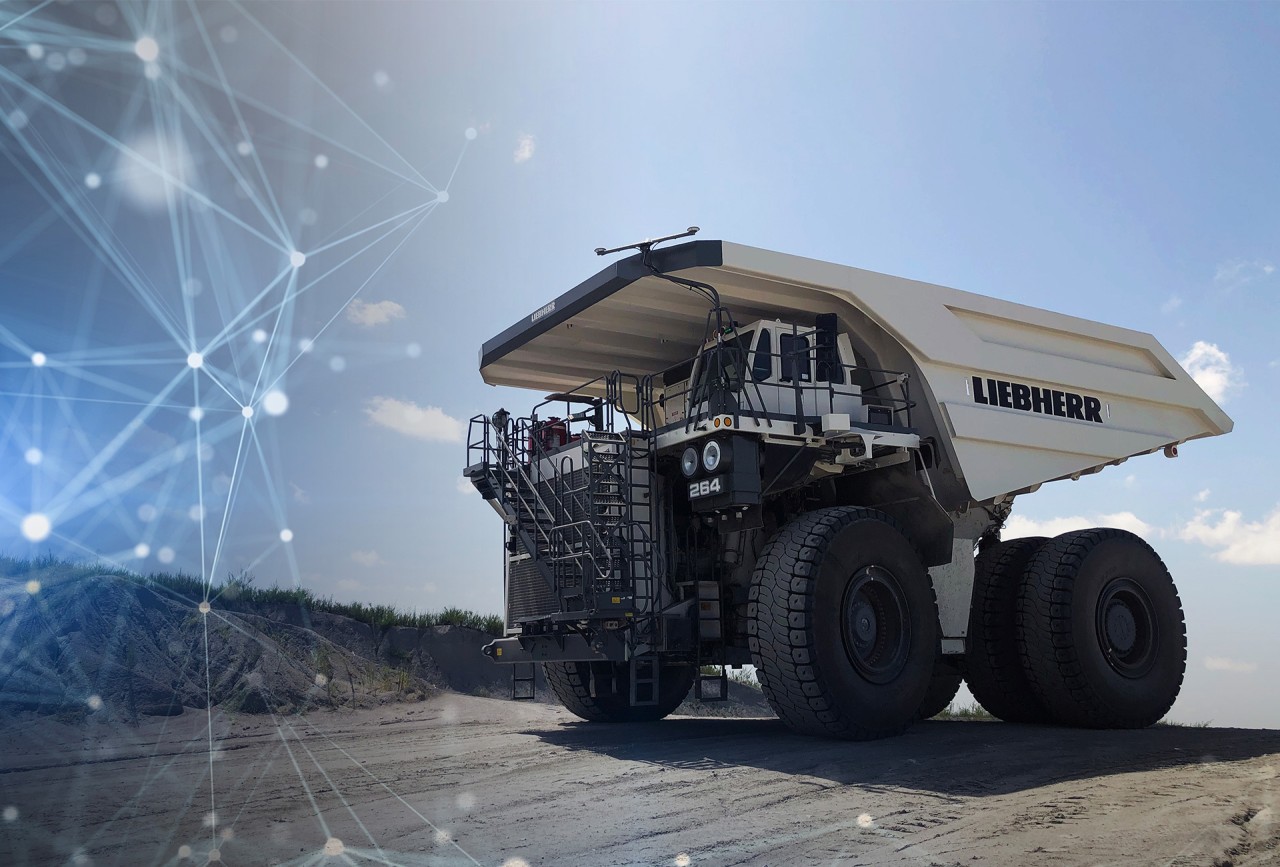
Today
The philosophy of Liebherr Mining is to offer scalable solutions, giving customers the ability to incrementally deploy tailored products and services to meet their specific needs. This approach sees Liebherr Mining expand its technology portfolio, with significant milestones recently achieved. For example, in August 2023, Liebherr announced the deployment of a fleet of four T 264 autonomous haul trucks in Western Australia for onsite validation, marking the next stage of development of a new autonomy product for the mining industry.
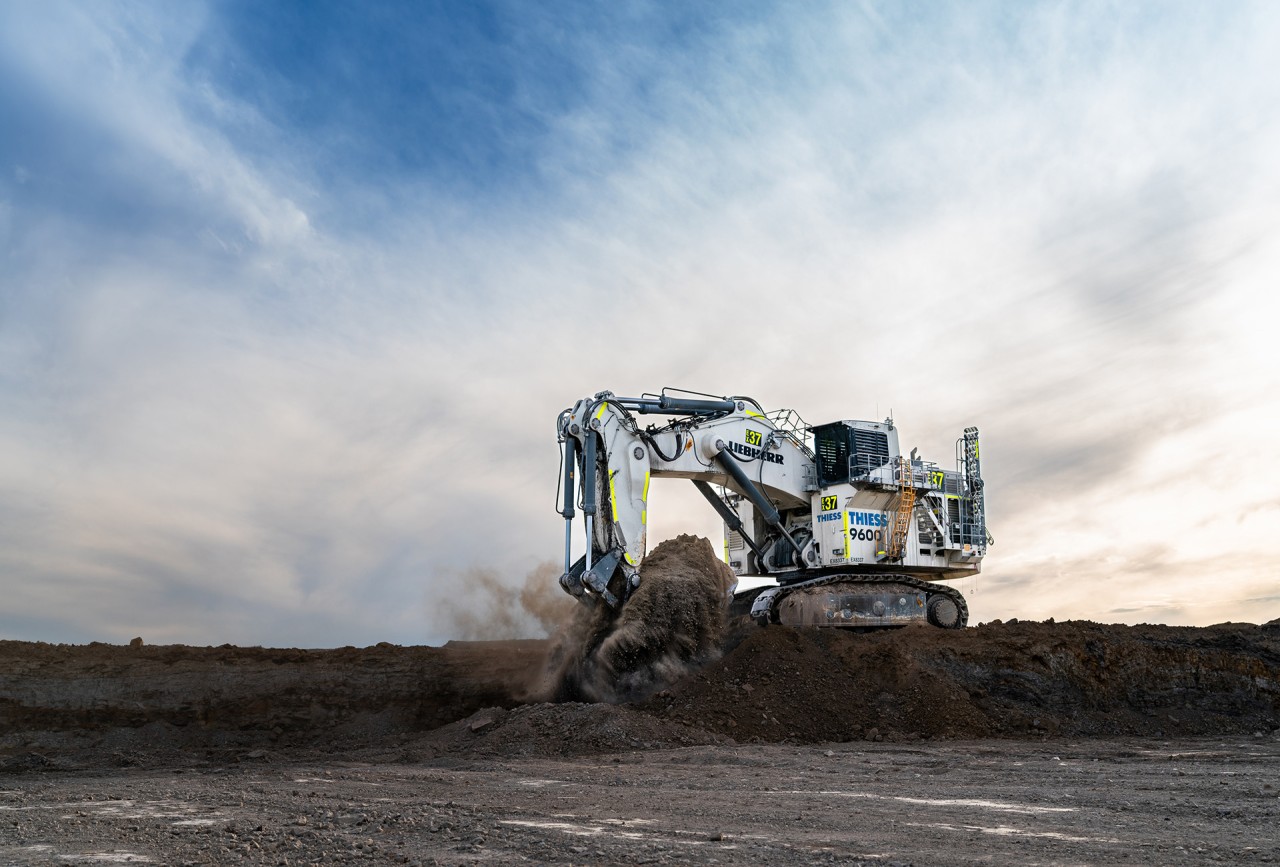
Tomorrow
‘For most applications, the nature and method of mining are changing,’ asserts Oliver Weiss, executive vice president R&D, engineering and manufacturing, Liebherr-Mining Equipment SAS. He also explains that Liebherr is closely monitoring this changing paradigm. ‘The machines running on green energy have to be used differently and the infra structure of the energy supply chain, which ends at the machine, needs to change dramatically.’ Since different types of energy are needed owing to the varying costs in different regions, Liebherr is working on variations of its equipment and more extensive adaptation of the machines. This means that drivetrains will be able to run on renewable energy from the grid, batteries, combustion engines, fuel cells and hybrids. Oliver Weiss believes a technology-neutral approach is encompassed in Liebherr Mining’s decision ‘to remain application-independent by offering a variety of solutions that can be exchanged or supplemented.’
Product development – pulling out all the stops
Liebherr’s innovations and transformations, whether big or small in scale, stem from the company’s ability to look beyond the horizon. To this end, the company always pools together wide-ranging skill sets and combines these with the practical experience of a global market leader.
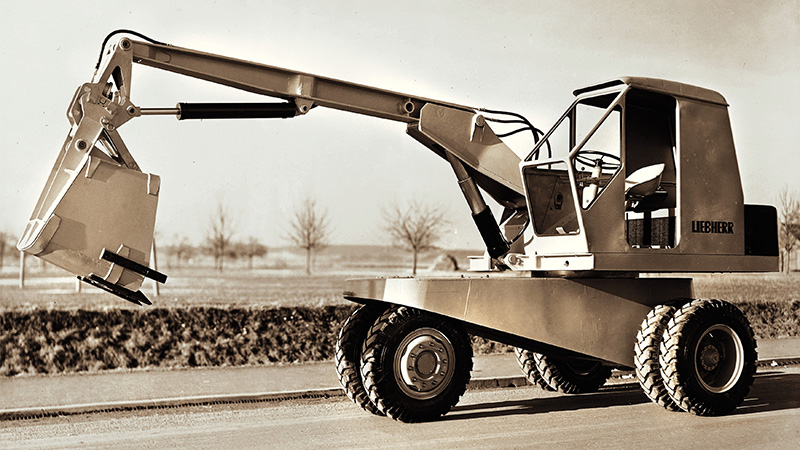
Yesterday
When Hans Liebherr hires a cable excavator in 1953, he is struck by how poor the power-to-weight ratio is. Eight months later, he presents Europe’s first hydraulic excavator – the L 300 – leaving engineers and construction companies stunned. They are impressed not only by its low weight and the transfer of existing hydraulic technology to an excavator, but also by its effective digging force. In 1954, this powerful machine goes into series production. This is followed in 1960 by another great innovation, the wheeled excavator A 650: the first fully hydraulic wheeled excavator from Liebherr combines hydraulic work equipment with a hydraulic travel drive for the first time. This united all modern technical possibilities available at the time.
From the very beginning, Hans Liebherr sees the importance of developing and producing key technologies in-house. This becomes especially apparent in 1983 with the A 912 wheeled excavator. Its diesel engine, hydraulic pump, slew drive with planetary gearbox, excavator axle and manual gearbox and transfer box in the undercarriage are all produced entirely in-house. A further innovative highlight follows in 1989 in the shape of Litronic: the entire system of intelligent electronics and functional hydraulics is designed to monitor, control, regulate and coordinate all key systems of the excavator. Having been under continuous development ever since, Litronic still optimises the efficiency of every Liebherr construction machine to this day.
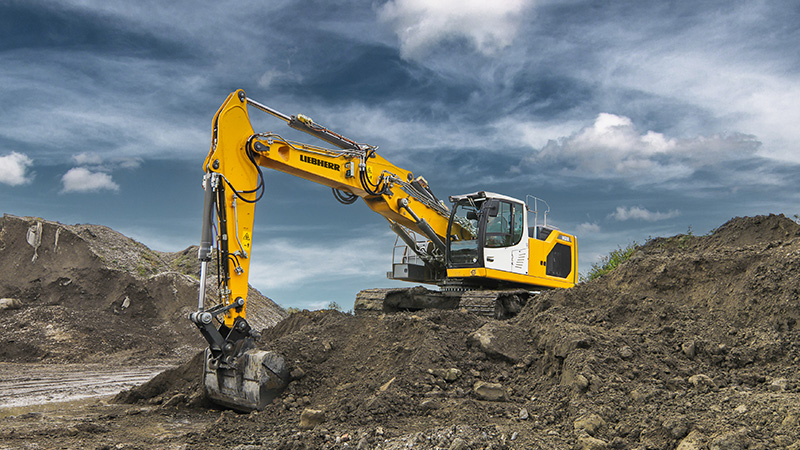
Today
More than 70 years after Liebherr’s first hydraulic excavator went into production, the newest generation sets the benchmark for wheeled and crawler excavators as well as material handling machines. Liebherr meets the often highly diverse individual customer requirements through a wide variety of equipment. In keeping with the tradition of the company founder, almost everything comes from a single source: construction or material handling machines, quick-change systems, attachment tools, special equipment as well as oils and lubricants. Between 40 and 50% of the machines are manufactured in-house. Plus, the fact that 98% of all spare parts are available 24/7 makes the Liebherr hydraulic excavators and material-handling machines robust pieces of work equipment delivering high reliability and optimum productivity. The newest generation also packs a punch in visual terms: after all, the high technical specification is not the only criterion in a customer’s purchase decision; the look of a machine is also an important consideration here.
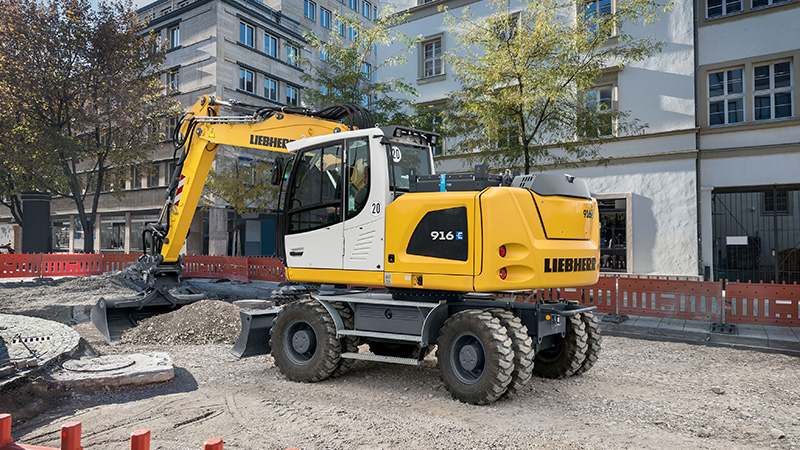
Tomorrow
In line with the Liebherr Group, the earthmoving and material handling product segments are working on a technology-neutral approach to develop a wide range of different drive technologies – with the aim of combining maximum efficiency with reduced emissions. This also incorporates in-house development and production of highly efficient engines, motors and drives. Consequently, the portfolio spans from conventional combustion engines to hydrogen combustion engines and electric motors as well as fuel cell, battery-powered and hybrid drives. In conjunction with optimally matched components, some of which are also manufactured in-house, Liebherr achieves a consistently high overall efficiency of the drivetrain. Potential sustainable energy sources include electrical energy, hydrogen, ammonia, e-fuels, methanol, hydrogenated vegetable oil (HVO), biodiesel and fossil diesel. Which drive technology can be used for an application is ultimately also influenced by the region of use and its usable infrastructure. Innovative strength is needed in all fields, as there is no one-fits-all drive technology for the heterogeneous areas of application. It is not only drives that Liebherr places importance on, but also the continuous development and improvement of new and existing assistance systems. These support the machine operators in their daily work, while also increasing safety and productivity.
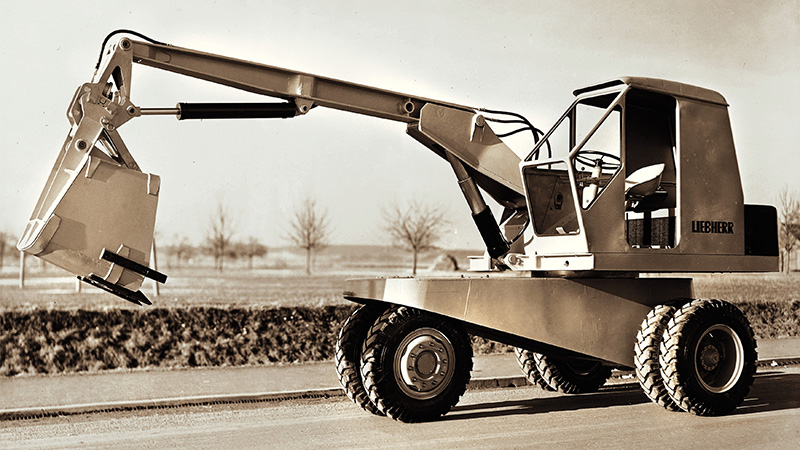
Yesterday
When Hans Liebherr hires a cable excavator in 1953, he is struck by how poor the power-to-weight ratio is. Eight months later, he presents Europe’s first hydraulic excavator – the L 300 – leaving engineers and construction companies stunned. They are impressed not only by its low weight and the transfer of existing hydraulic technology to an excavator, but also by its effective digging force. In 1954, this powerful machine goes into series production. This is followed in 1960 by another great innovation, the wheeled excavator A 650: the first fully hydraulic wheeled excavator from Liebherr combines hydraulic work equipment with a hydraulic travel drive for the first time. This united all modern technical possibilities available at the time.
From the very beginning, Hans Liebherr sees the importance of developing and producing key technologies in-house. This becomes especially apparent in 1983 with the A 912 wheeled excavator. Its diesel engine, hydraulic pump, slew drive with planetary gearbox, excavator axle and manual gearbox and transfer box in the undercarriage are all produced entirely in-house. A further innovative highlight follows in 1989 in the shape of Litronic: the entire system of intelligent electronics and functional hydraulics is designed to monitor, control, regulate and coordinate all key systems of the excavator. Having been under continuous development ever since, Litronic still optimises the efficiency of every Liebherr construction machine to this day.
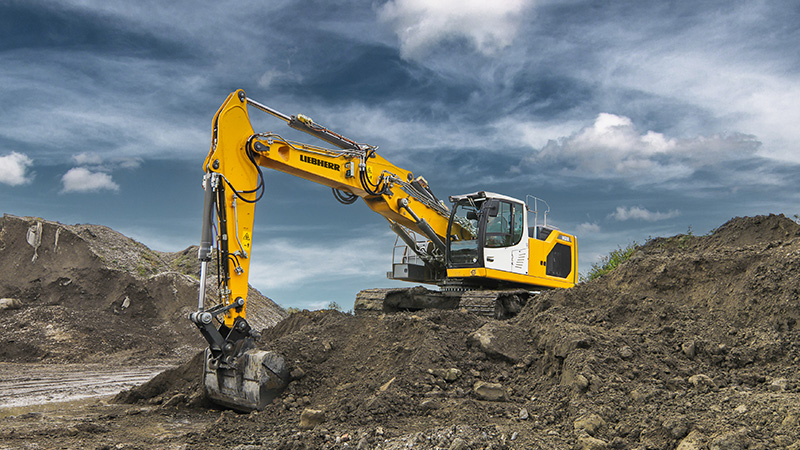
Today
More than 70 years after Liebherr’s first hydraulic excavator went into production, the newest generation sets the benchmark for wheeled and crawler excavators as well as material handling machines. Liebherr meets the often highly diverse individual customer requirements through a wide variety of equipment. In keeping with the tradition of the company founder, almost everything comes from a single source: construction or material handling machines, quick-change systems, attachment tools, special equipment as well as oils and lubricants. Between 40 and 50% of the machines are manufactured in-house. Plus, the fact that 98% of all spare parts are available 24/7 makes the Liebherr hydraulic excavators and material-handling machines robust pieces of work equipment delivering high reliability and optimum productivity. The newest generation also packs a punch in visual terms: after all, the high technical specification is not the only criterion in a customer’s purchase decision; the look of a machine is also an important consideration here.
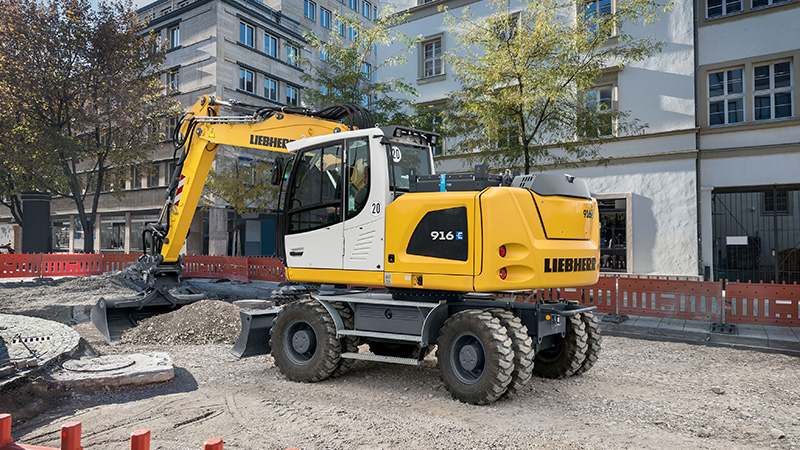
Tomorrow
In line with the Liebherr Group, the earthmoving and material handling product segments are working on a technology-neutral approach to develop a wide range of different drive technologies – with the aim of combining maximum efficiency with reduced emissions. This also incorporates in-house development and production of highly efficient engines, motors and drives. Consequently, the portfolio spans from conventional combustion engines to hydrogen combustion engines and electric motors as well as fuel cell, battery-powered and hybrid drives. In conjunction with optimally matched components, some of which are also manufactured in-house, Liebherr achieves a consistently high overall efficiency of the drivetrain. Potential sustainable energy sources include electrical energy, hydrogen, ammonia, e-fuels, methanol, hydrogenated vegetable oil (HVO), biodiesel and fossil diesel. Which drive technology can be used for an application is ultimately also influenced by the region of use and its usable infrastructure. Innovative strength is needed in all fields, as there is no one-fits-all drive technology for the heterogeneous areas of application. It is not only drives that Liebherr places importance on, but also the continuous development and improvement of new and existing assistance systems. These support the machine operators in their daily work, while also increasing safety and productivity.
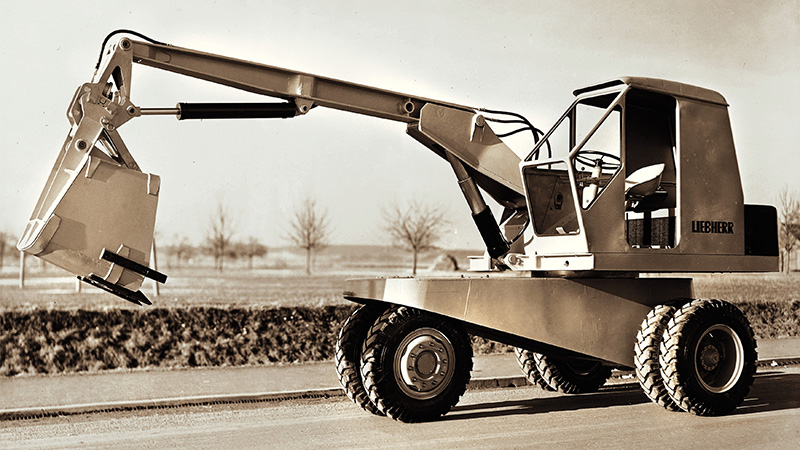
Yesterday
When Hans Liebherr hires a cable excavator in 1953, he is struck by how poor the power-to-weight ratio is. Eight months later, he presents Europe’s first hydraulic excavator – the L 300 – leaving engineers and construction companies stunned. They are impressed not only by its low weight and the transfer of existing hydraulic technology to an excavator, but also by its effective digging force. In 1954, this powerful machine goes into series production. This is followed in 1960 by another great innovation, the wheeled excavator A 650: the first fully hydraulic wheeled excavator from Liebherr combines hydraulic work equipment with a hydraulic travel drive for the first time. This united all modern technical possibilities available at the time.
From the very beginning, Hans Liebherr sees the importance of developing and producing key technologies in-house. This becomes especially apparent in 1983 with the A 912 wheeled excavator. Its diesel engine, hydraulic pump, slew drive with planetary gearbox, excavator axle and manual gearbox and transfer box in the undercarriage are all produced entirely in-house. A further innovative highlight follows in 1989 in the shape of Litronic: the entire system of intelligent electronics and functional hydraulics is designed to monitor, control, regulate and coordinate all key systems of the excavator. Having been under continuous development ever since, Litronic still optimises the efficiency of every Liebherr construction machine to this day.
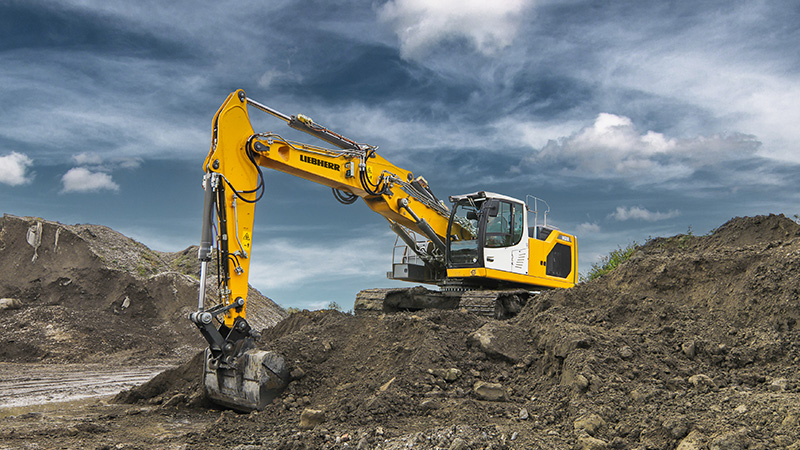
Today
More than 70 years after Liebherr’s first hydraulic excavator went into production, the newest generation sets the benchmark for wheeled and crawler excavators as well as material handling machines. Liebherr meets the often highly diverse individual customer requirements through a wide variety of equipment. In keeping with the tradition of the company founder, almost everything comes from a single source: construction or material handling machines, quick-change systems, attachment tools, special equipment as well as oils and lubricants. Between 40 and 50% of the machines are manufactured in-house. Plus, the fact that 98% of all spare parts are available 24/7 makes the Liebherr hydraulic excavators and material-handling machines robust pieces of work equipment delivering high reliability and optimum productivity. The newest generation also packs a punch in visual terms: after all, the high technical specification is not the only criterion in a customer’s purchase decision; the look of a machine is also an important consideration here.
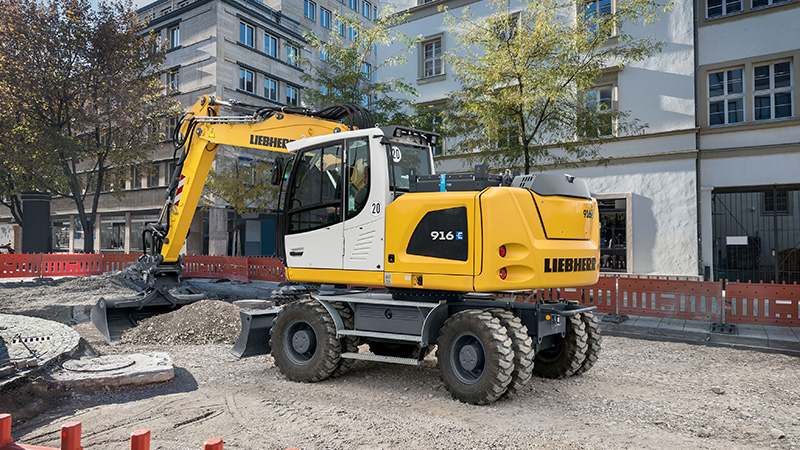
Tomorrow
In line with the Liebherr Group, the earthmoving and material handling product segments are working on a technology-neutral approach to develop a wide range of different drive technologies – with the aim of combining maximum efficiency with reduced emissions. This also incorporates in-house development and production of highly efficient engines, motors and drives. Consequently, the portfolio spans from conventional combustion engines to hydrogen combustion engines and electric motors as well as fuel cell, battery-powered and hybrid drives. In conjunction with optimally matched components, some of which are also manufactured in-house, Liebherr achieves a consistently high overall efficiency of the drivetrain. Potential sustainable energy sources include electrical energy, hydrogen, ammonia, e-fuels, methanol, hydrogenated vegetable oil (HVO), biodiesel and fossil diesel. Which drive technology can be used for an application is ultimately also influenced by the region of use and its usable infrastructure. Innovative strength is needed in all fields, as there is no one-fits-all drive technology for the heterogeneous areas of application. It is not only drives that Liebherr places importance on, but also the continuous development and improvement of new and existing assistance systems. These support the machine operators in their daily work, while also increasing safety and productivity.
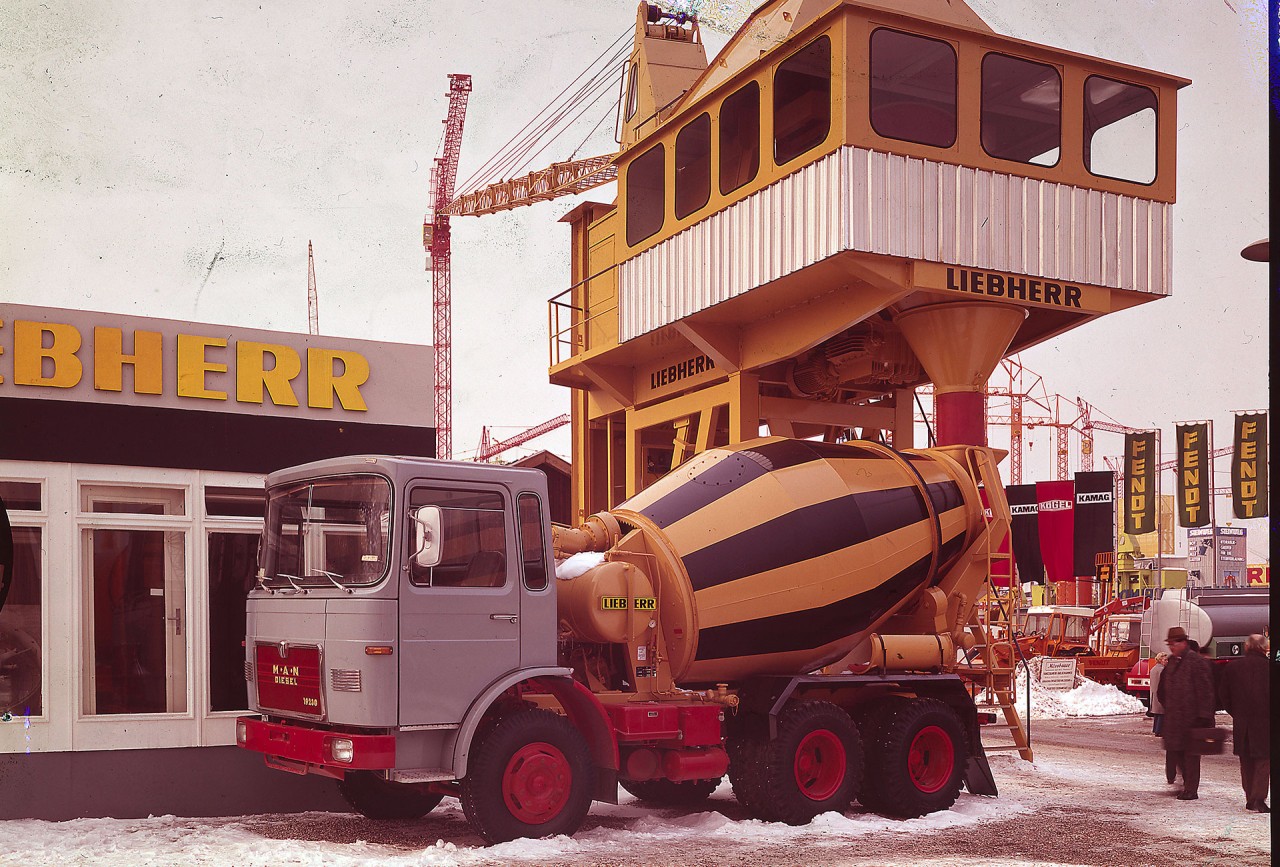
Yesterday
1 April 1954: on Hans Liebherr’s 39th birthday, the Liebherr-Werk V plant commences operations in Bad Schussenried (Germany). This paves the way for the first in-house mixing technology product: a reverse drum mixer for concrete. With on-site concrete-mixing being the norm back then, the reverse drum mixer becomes a big seller. In 1958, it is followed by the first mixing tower. This allows construction companies to produce concrete of a consistently high quality centrally and to deliver out to individual construction sites. In 1967, Liebherr builds the first truck mixers, giving operators an economical means of transporting concrete to the construction site. The advertisement at the time is (naturally!) euphoric and tells the story of its genesis: ‘Lots of concrete truck mixers are new. This one is brand new! The fully hydraulic HTM 6 concrete-transporting truck mixer from Liebherr is the result of many years of experience amassed from the production of concrete mixing systems, concrete transporters and hydraulic machinery.’
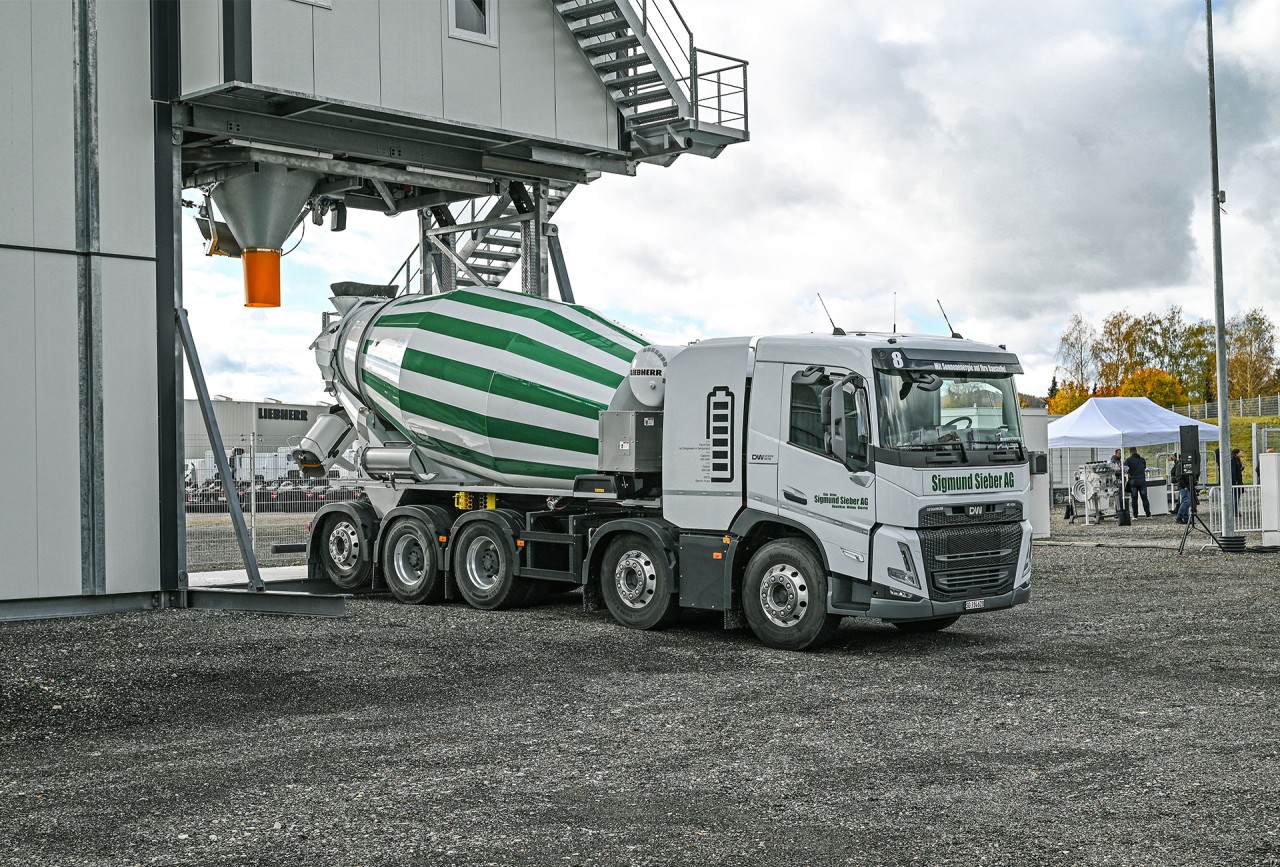
Today
The principle of mixing concrete has barely changed over the years. What has changed dramatically, however, is the expectations on product quality and availability, as well as the efficiency and sustainability of production – all of which have increased. This is why Liebherr has worked resolutely in Bad Schussenried to develop its concrete mixing plants, truck mixers and pump systems. One decisive factor in the technologies used has always been how to manufacture ever higher-quality concrete very efficiently. With concrete transportation, the development is also heading in the direction of ultra-modern fully electric ETM truck mixers. These pick up the high-quality concrete at the mixing plant and transport it to the construction site without producing any emissions. Unloading at the construction site is also clean and quiet. A single battery charge lasts the ETM truck mixer the entire day – which is ordinarily five return trips a day.
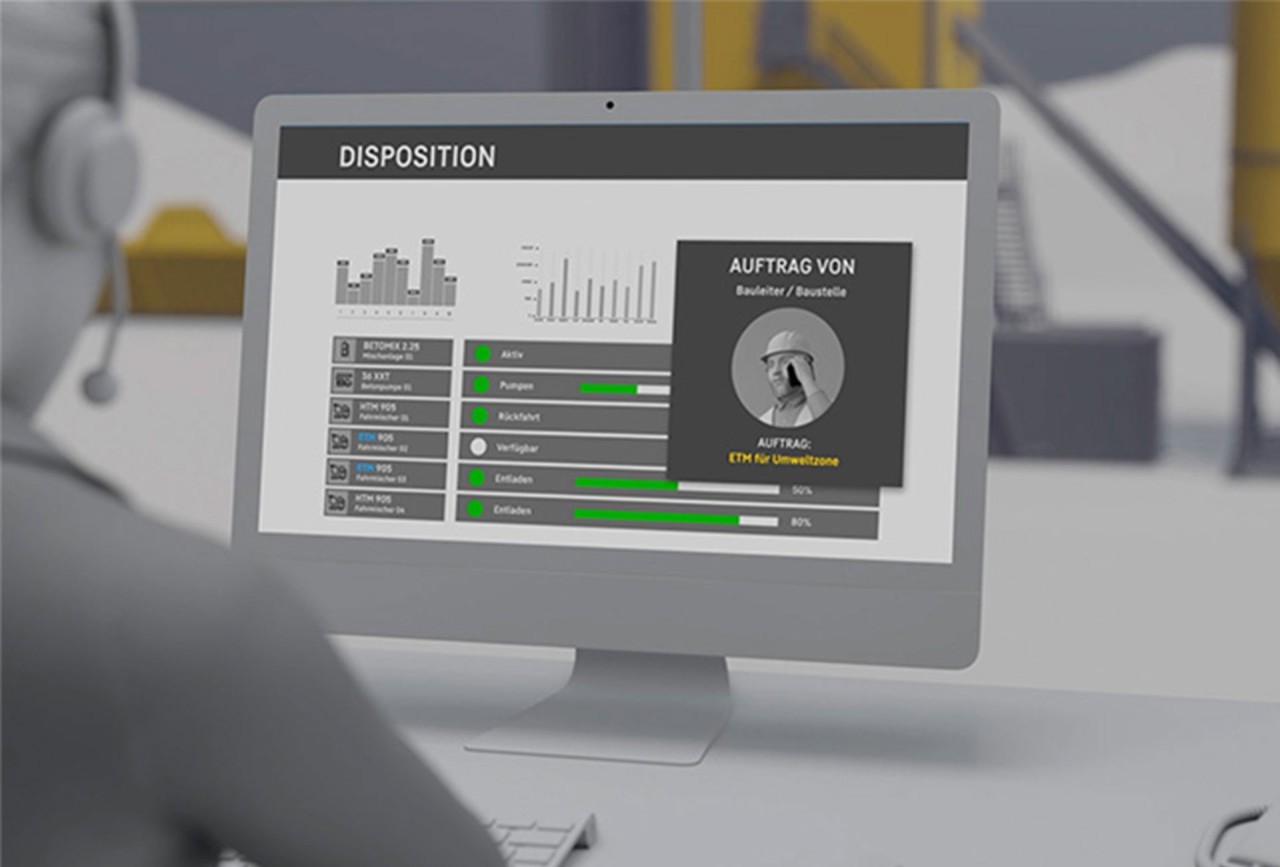
Tomorrow
The ETM series of electric truck mixers is Liebherr’s response to the growing requirements in terms of emission reductions in built-up areas. The demands of developers – and customers – are high. Even with zero-emissions operation, the central focus is still on the performance and reliability of the new generation of truck mixers. Liebherr is also keeping pace with the growing customer demand for flexibility, agility and emission reductions through its mixing plant series – for example Betomix and Mobilmix. The new plants consume up to 30% less energy than their predecessors. Plus, when the concrete is being manufactured, the recipe is far more accurate, which improves the carbon footprint. The operation of the plants and the machine fleet will in future be increasingly controlled with digital systems. This means they can be used even more efficiently and maintenance issues can be identified sooner.
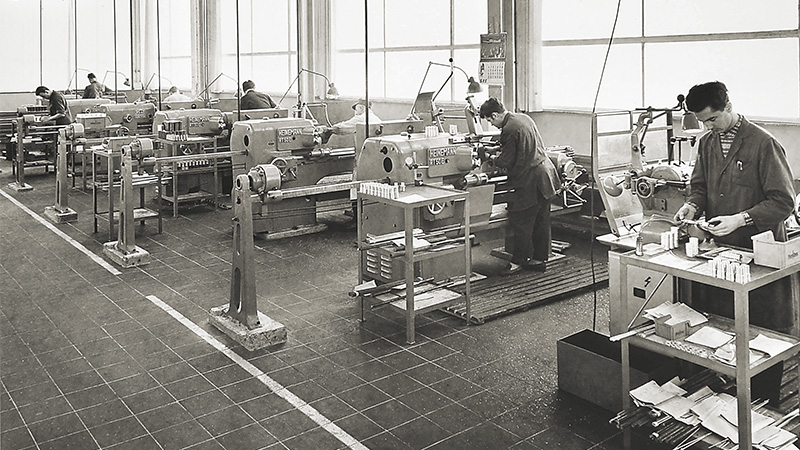
Yesterday
In March 1960, Hans Liebherr establishes Liebherr-Aero-Technik GmbH in Lindenberg in the Allgäu (Germany). One of the company’s first undertakings is to take charge of landing gear and hydraulic machines and to reproduce aeroplane spare parts under licence for certain types of aeroplane. 1963 sees the company start licensed production of machines for pressurising and air-conditioning systems. True to the pioneering spirit of Hans Liebherr, the company makes the decision to expand beyond licensed business and begins producing its own components and systems. This focus on developing its own key technologies paves the way from equipment manufacturer to systems provider. With the acquisition of Alex. Friedmann GmbH at the end of the 1990s, product development even expands into transportation systems. Here, the focus is on environmentally friendly and intelligent technologies for the railway.
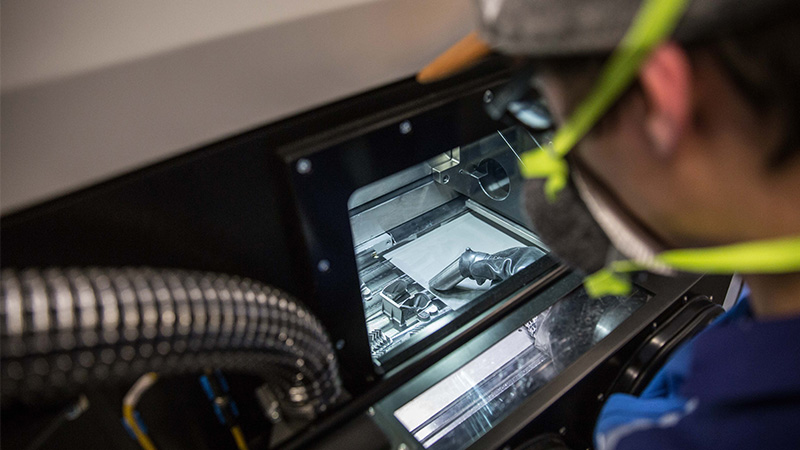
Today
The aerospace and transportation systems product segment is now a global entity and employs some 6,000 people. The actuators developed and manufactured by Liebherr are integrated into the eVTOL aircraft from Eve Air Mobility for actuation of its aileron, elevator and rudder. These actuators, developed in-house by Liebherr, feature a fully integrated control and power electronics module, making them more compact and easier to install than competitor actuators. This advantage is especially important as the installation space is getting smaller and smaller for reasons of aerodynamics. Meanwhile, the air-conditioning technology developed for aerospace comes into use on the railways: for example, the eco-friendly air cycle technology for air-conditioning in trains, which only uses ambient air for cooling, instead of conventional chemical refrigerants. Liebherr-Transportation Systems have been commissioned by SNCF from 2023 to 2030 to fit French trains in the Occitania region with the innovative air cycle air-conditioning systems.
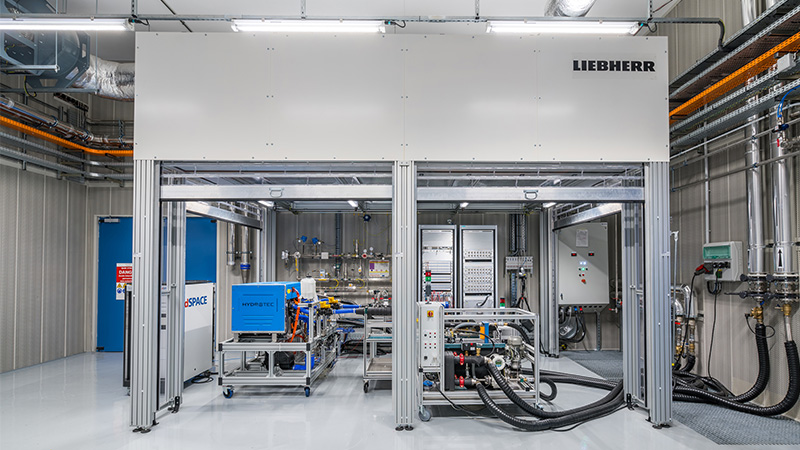
Tomorrow
‘More Electric Aircraft’ is the platform for more pioneering endeavours on the journey to aerospace of the future. Expanding the electrification of aeroplane systems, such as climate control, de-icing or the various actuators, involves combining areas of expertise within compressor technology, such as cabin air preparation, with fuel cell technology. New drive technologies such as hydrogen fuel cells are also being researched and developed in Lindenberg (Germany) and Toulouse (France). In transportation systems too, Liebherr is driving electrification forward. Together with rolling stock manufacturer Siemens Mobility, Liebherr has for the first time created an electro-hydraulic brake actuator that delivers the braking force for the braking system. This means the brake is controlled completely electronically by the new Siemens braking system, with no need for compressed air. Further testament to Liebherr’s pioneering spirit.
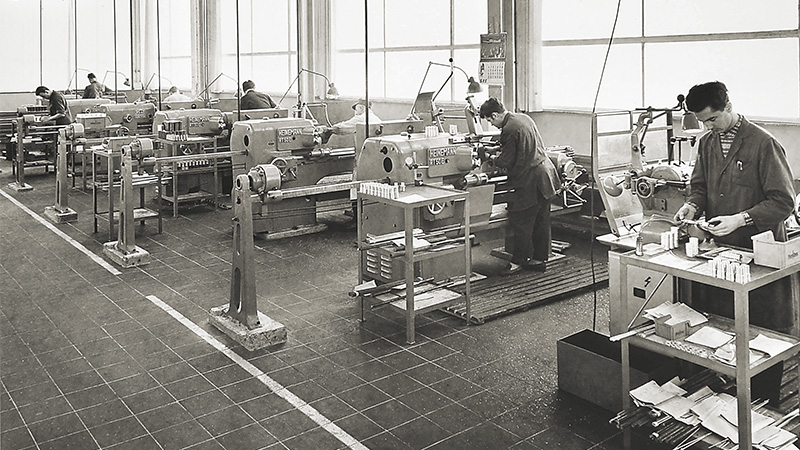
Yesterday
In March 1960, Hans Liebherr establishes Liebherr-Aero-Technik GmbH in Lindenberg in the Allgäu (Germany). One of the company’s first undertakings is to take charge of landing gear and hydraulic machines and to reproduce aeroplane spare parts under licence for certain types of aeroplane. 1963 sees the company start licensed production of machines for pressurising and air-conditioning systems. True to the pioneering spirit of Hans Liebherr, the company makes the decision to expand beyond licensed business and begins producing its own components and systems. This focus on developing its own key technologies paves the way from equipment manufacturer to systems provider. With the acquisition of Alex. Friedmann GmbH at the end of the 1990s, product development even expands into transportation systems. Here, the focus is on environmentally friendly and intelligent technologies for the railway.
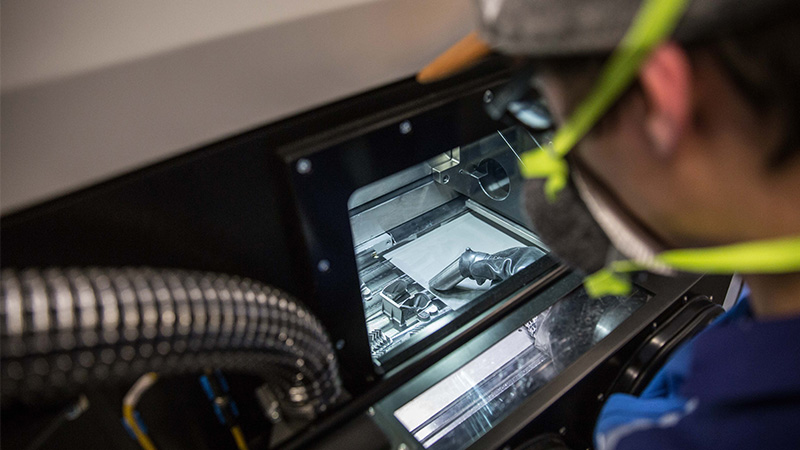
Today
The aerospace and transportation systems product segment is now a global entity and employs some 6,000 people. The actuators developed and manufactured by Liebherr are integrated into the eVTOL aircraft from Eve Air Mobility for actuation of its aileron, elevator and rudder. These actuators, developed in-house by Liebherr, feature a fully integrated control and power electronics module, making them more compact and easier to install than competitor actuators. This advantage is especially important as the installation space is getting smaller and smaller for reasons of aerodynamics. Meanwhile, the air-conditioning technology developed for aerospace comes into use on the railways: for example, the eco-friendly air cycle technology for air-conditioning in trains, which only uses ambient air for cooling, instead of conventional chemical refrigerants. Liebherr-Transportation Systems have been commissioned by SNCF from 2023 to 2030 to fit French trains in the Occitania region with the innovative air cycle air-conditioning systems.
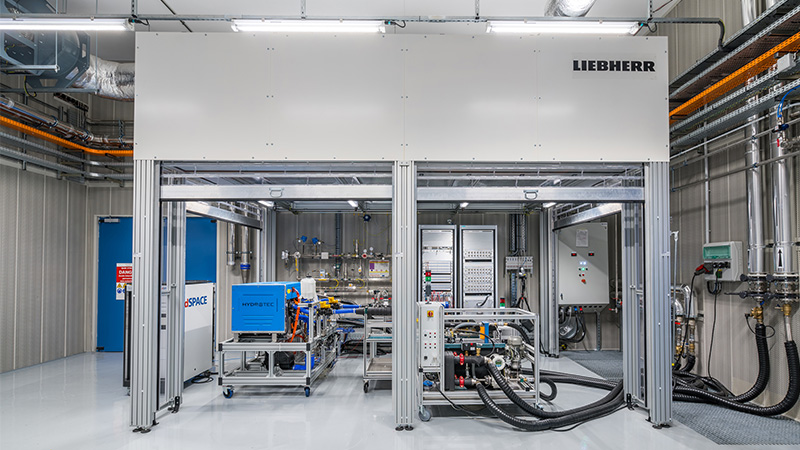
Tomorrow
‘More Electric Aircraft’ is the platform for more pioneering endeavours on the journey to aerospace of the future. Expanding the electrification of aeroplane systems, such as climate control, de-icing or the various actuators, involves combining areas of expertise within compressor technology, such as cabin air preparation, with fuel cell technology. New drive technologies such as hydrogen fuel cells are also being researched and developed in Lindenberg (Germany) and Toulouse (France). In transportation systems too, Liebherr is driving electrification forward. Together with rolling stock manufacturer Siemens Mobility, Liebherr has for the first time created an electro-hydraulic brake actuator that delivers the braking force for the braking system. This means the brake is controlled completely electronically by the new Siemens braking system, with no need for compressed air. Further testament to Liebherr’s pioneering spirit.
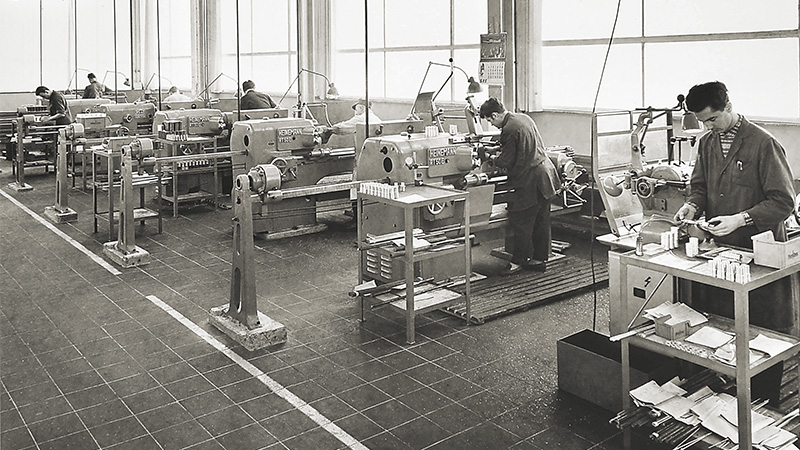
Yesterday
In March 1960, Hans Liebherr establishes Liebherr-Aero-Technik GmbH in Lindenberg in the Allgäu (Germany). One of the company’s first undertakings is to take charge of landing gear and hydraulic machines and to reproduce aeroplane spare parts under licence for certain types of aeroplane. 1963 sees the company start licensed production of machines for pressurising and air-conditioning systems. True to the pioneering spirit of Hans Liebherr, the company makes the decision to expand beyond licensed business and begins producing its own components and systems. This focus on developing its own key technologies paves the way from equipment manufacturer to systems provider. With the acquisition of Alex. Friedmann GmbH at the end of the 1990s, product development even expands into transportation systems. Here, the focus is on environmentally friendly and intelligent technologies for the railway.
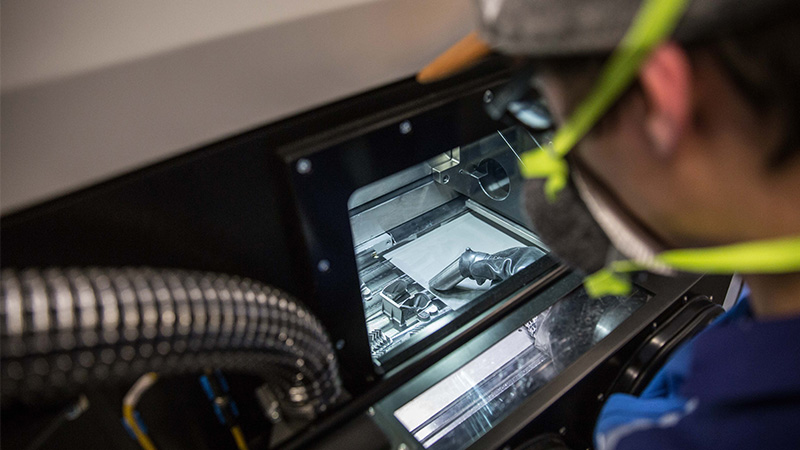
Today
The aerospace and transportation systems product segment is now a global entity and employs some 6,000 people. The actuators developed and manufactured by Liebherr are integrated into the eVTOL aircraft from Eve Air Mobility for actuation of its aileron, elevator and rudder. These actuators, developed in-house by Liebherr, feature a fully integrated control and power electronics module, making them more compact and easier to install than competitor actuators. This advantage is especially important as the installation space is getting smaller and smaller for reasons of aerodynamics. Meanwhile, the air-conditioning technology developed for aerospace comes into use on the railways: for example, the eco-friendly air cycle technology for air-conditioning in trains, which only uses ambient air for cooling, instead of conventional chemical refrigerants. Liebherr-Transportation Systems have been commissioned by SNCF from 2023 to 2030 to fit French trains in the Occitania region with the innovative air cycle air-conditioning systems.
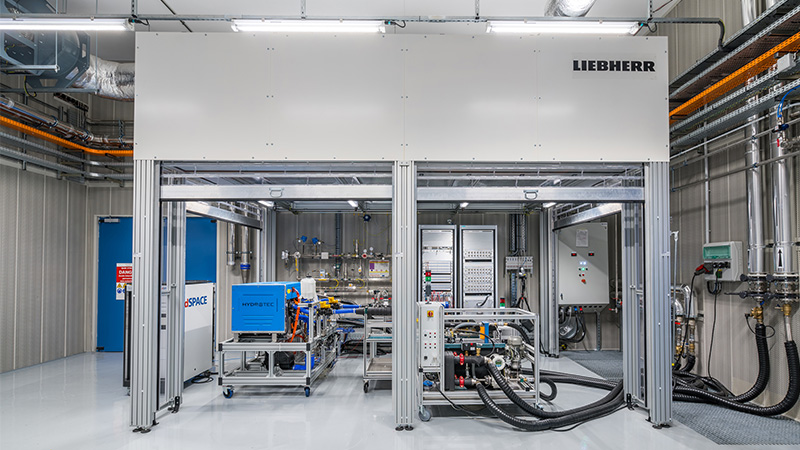
Tomorrow
‘More Electric Aircraft’ is the platform for more pioneering endeavours on the journey to aerospace of the future. Expanding the electrification of aeroplane systems, such as climate control, de-icing or the various actuators, involves combining areas of expertise within compressor technology, such as cabin air preparation, with fuel cell technology. New drive technologies such as hydrogen fuel cells are also being researched and developed in Lindenberg (Germany) and Toulouse (France). In transportation systems too, Liebherr is driving electrification forward. Together with rolling stock manufacturer Siemens Mobility, Liebherr has for the first time created an electro-hydraulic brake actuator that delivers the braking force for the braking system. This means the brake is controlled completely electronically by the new Siemens braking system, with no need for compressed air. Further testament to Liebherr’s pioneering spirit.
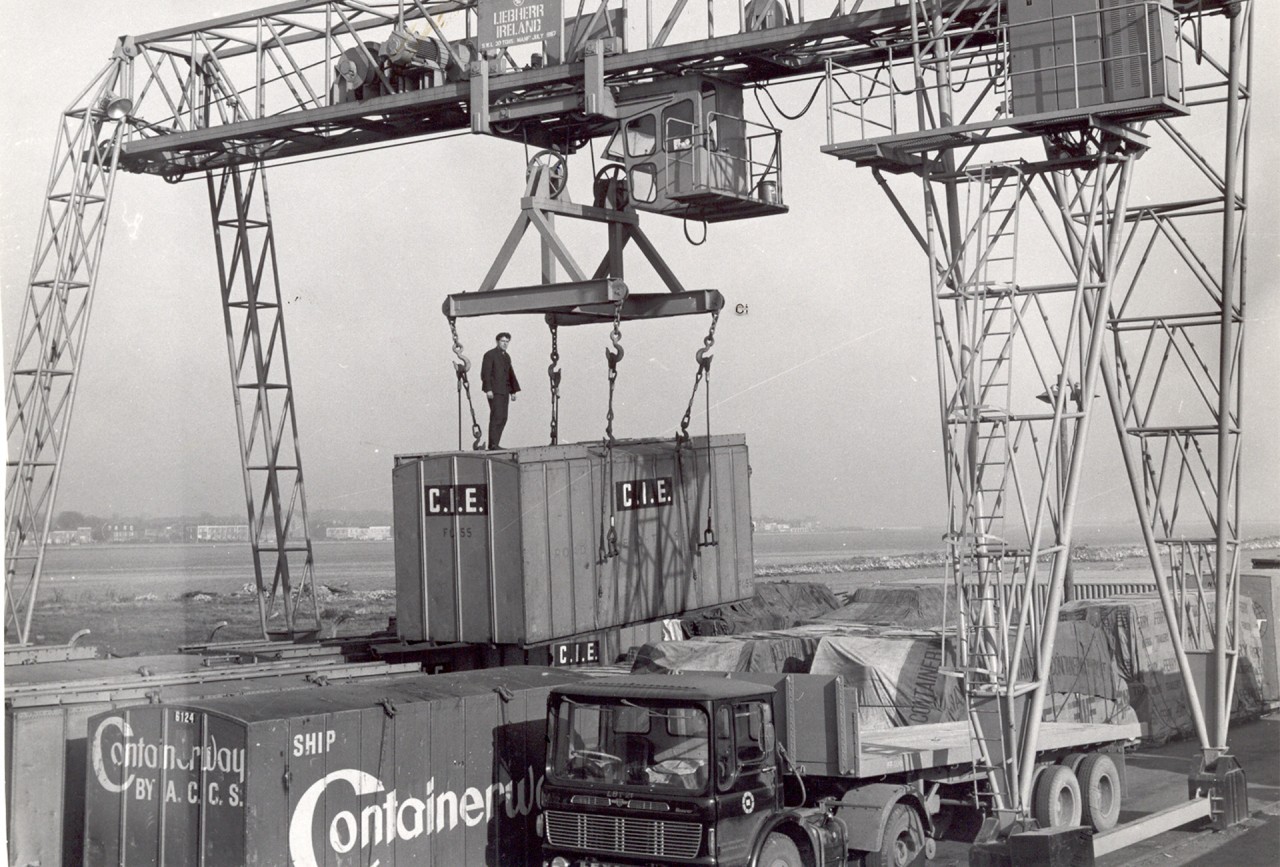
Yesterday
In the late 1950s, having made its name as a leading crane manufacturer in Germany, Liebherr commences operations at its first plant outside Germany: in the Irish town of Killarney. From here, the company aims to get a foothold in the British and North American markets with its tower cranes and subsequently its container, dockyard and specialist cranes. In 1967 in Killarney, Liebherr builds the first container crane for what is then a new industry. However, the production in the maritime crane product segment is not centred on Ireland. Parallel to this, maritime cranes are being manufactured in the Liebherr-Werk Nenzing plant in Austria. And in South Africa in the late 1950s, Hans Liebherr sets the course for the international direction of the maritime cranes and the Group as a whole by founding the Group’s first company outside Europe.
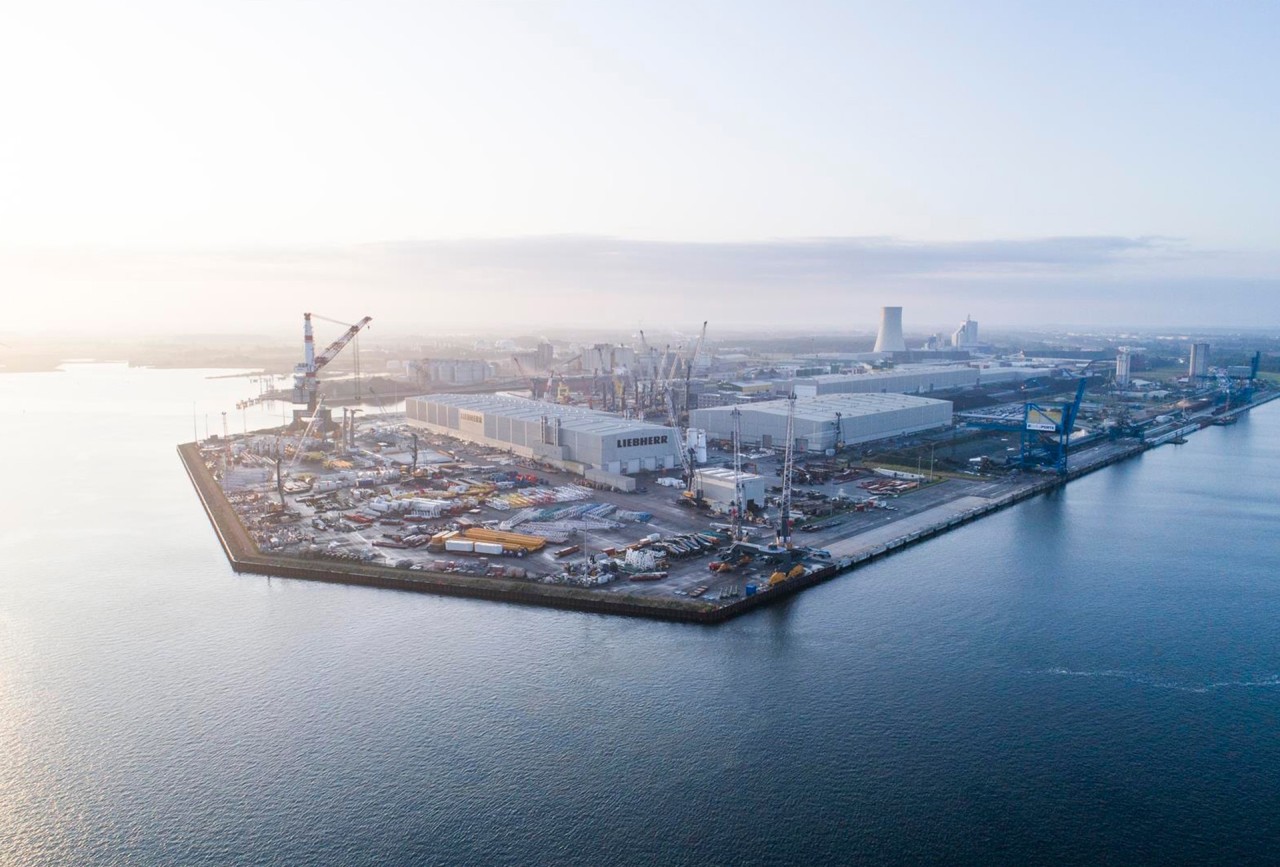
Today
In 2024, our Group comprises over 150 companies in more than 50 countries on all continents and employs more than 50,000 people around the world. Almost 4,000 of these work for the maritime cranes product segment. The products are manufactured in Killarney (Ireland), Sunderland (UK), Rostock (Germany) and Nenzing (Austria). Sales and service branches are operational on all continents. The product portfolio incorporates a versatile and well-structured product range for all types of material handling in ports and at sea. This includes ship to shore container cranes, mobile harbour cranes, offshore cranes, ship cranes, and rubber and rail mounted gantry cranes. It also incorporates a variety of digital solutions and comprehensive technical advice. Key to the success of Liebherr maritime cranes is the international collaboration within the product segment, in order to be as close as possible to the technological innovations and the customers around the world. Products that Liebherr develops in Ireland or in Rostock are largely built and tested in the same location.
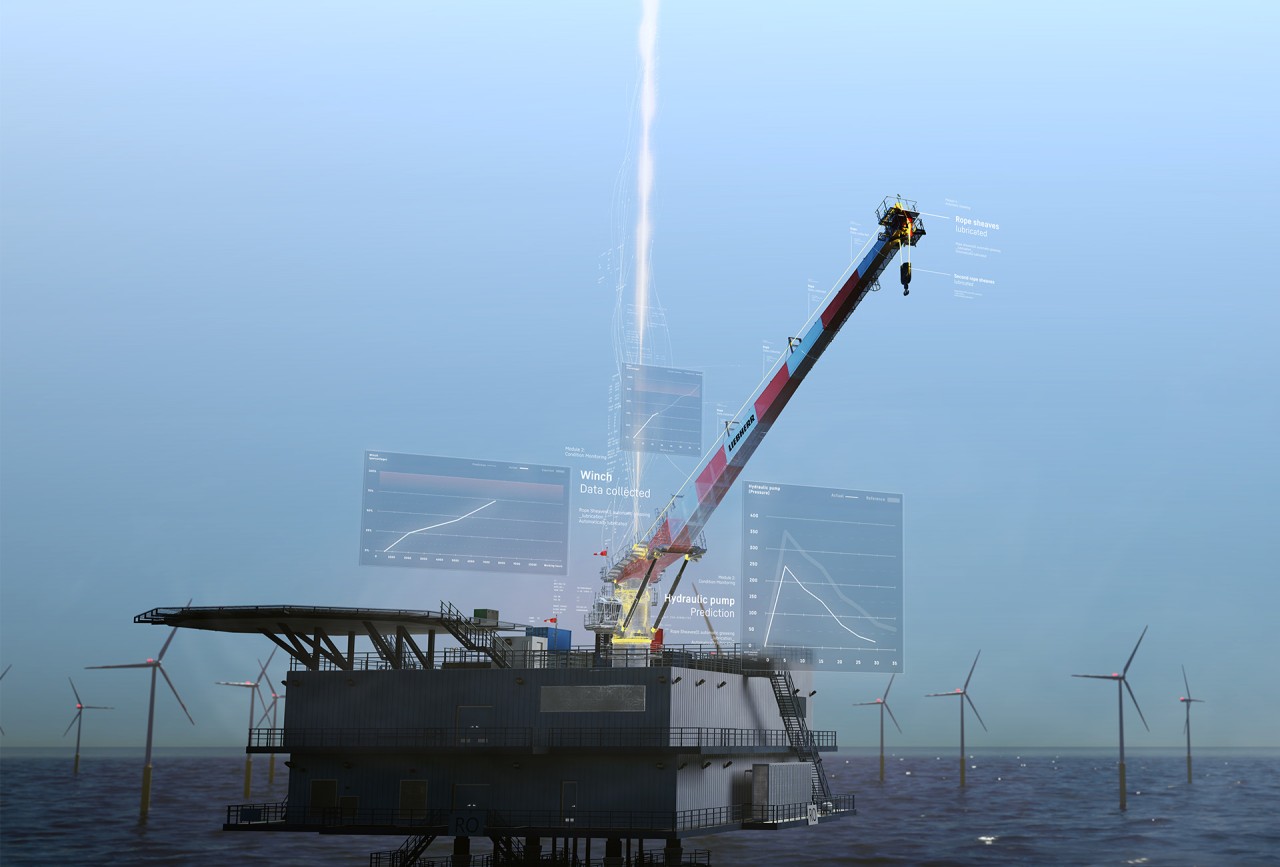
Tomorrow
Innovations in Liebherr’s maritime cranes are primarily born of intensive market monitoring and close collaboration with the customers. This involves transforming market and product requirements, which are recognised by different in-house departments, such as product management, sales and customer service, into solutions by means of a structured innovation process that incorporates other departments including engineering, production, procurement and controlling. This ensures an atmosphere of innovation and development in the plants themselves. In addition, in Nenzing, there is a specialist digital solutions and consulting department that looks at the incorporation of digital products and services along with future technologies, both within the product segment maritime cranes and across all segments. At present, development is particularly focused on innovative drive technologies, fibre rope technology, automation and assistance systems, condition monitoring and predictive maintenance.
Research and innovation – our pact with the future
From the very outset, research and innovation has always been the starting point and driver of product development at Liebherr. This calls for experience, pragmatism and boldness in equal measure to keep striking a new path, changing direction without losing sight of the ultimate goal.
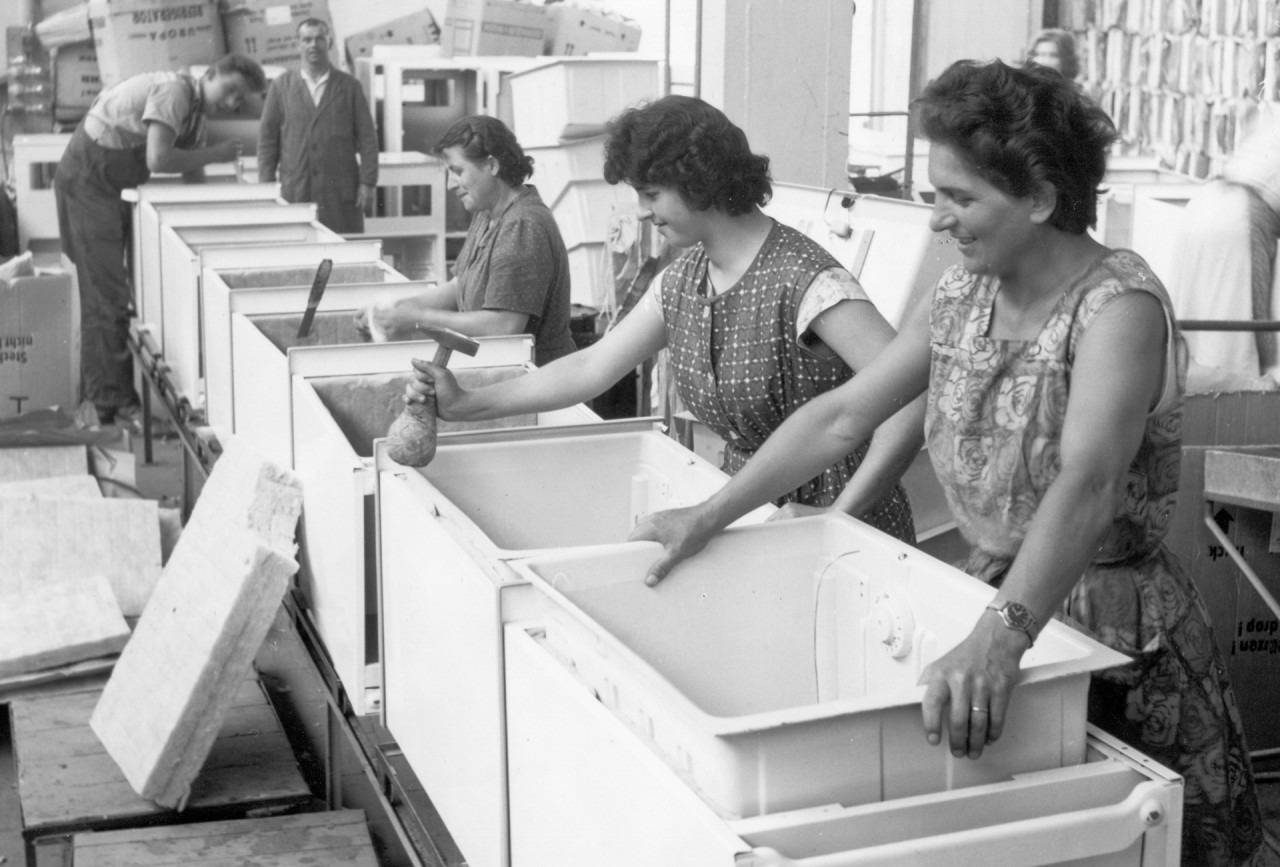
Yesterday
In the 1950s, when Hans Liebherr learns from a personal contact about a refrigerator factory that is coming up for sale, he quickly recognizes the enormous potential of the appliances and the market. Despite the fact that the technology to keep food cold at home had already been invented in Germany in the 19th century, it only really takes off in the USA to begin with. In the early 1950s, only one in ten German households owns a refrigerator but, with post-war economic growth, demand rapidly grows. Hans Liebherr decides not to buy the company but instead develops his own refrigerator with specialists in 1954. Just one year later, series production begins in Ochsenhausen in the south of Germany. From the outset, Hans Liebherr is focused on innovations and developing quality products – from the first freestanding appliances to integrated refrigerators, either as refrigerators only or fridge/freezer combinations. These are very well received on the market.
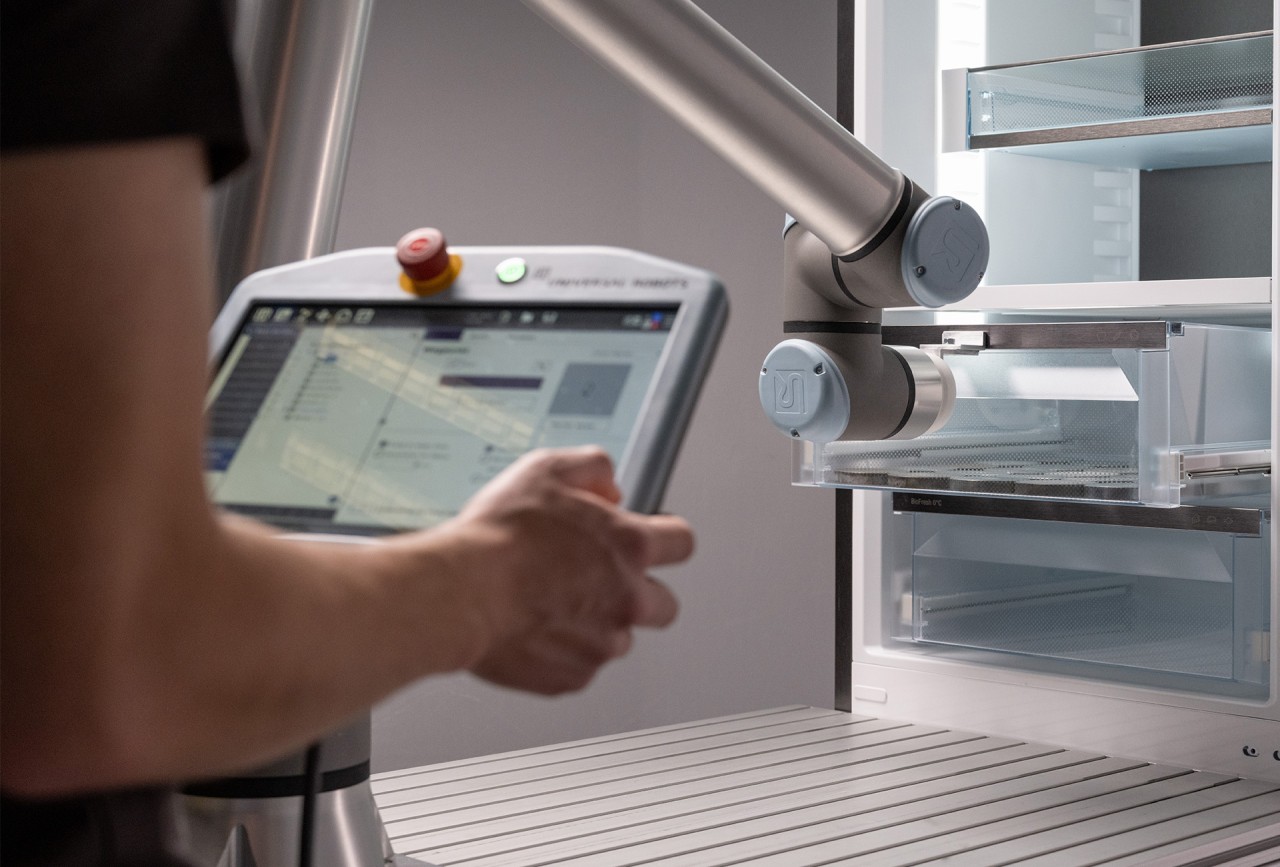
Today
For Liebherr, being close to the market means getting to know the customers’ needs and expectations of refrigerators and freezers in the home. On the path to continuous innovations, market research and customer feedback are just as important as in-depth studies and extensive physical and refrigeration testing in the ultra-modern research and development laboratories in Ochsenhausen. This is how such innovations as NoFrost, the use of natural refrigerants in combination with more efficient refrigerant circuits, and even the patented BioFresh technology came about. These innovations create the optimum storage conditions for every foodstuff, so that these can stay fresh for longer, and prevent food waste. As such, Liebherr has set and continues to set benchmarks in the field of quality refrigeration appliances in the top energy-efficiency classes.
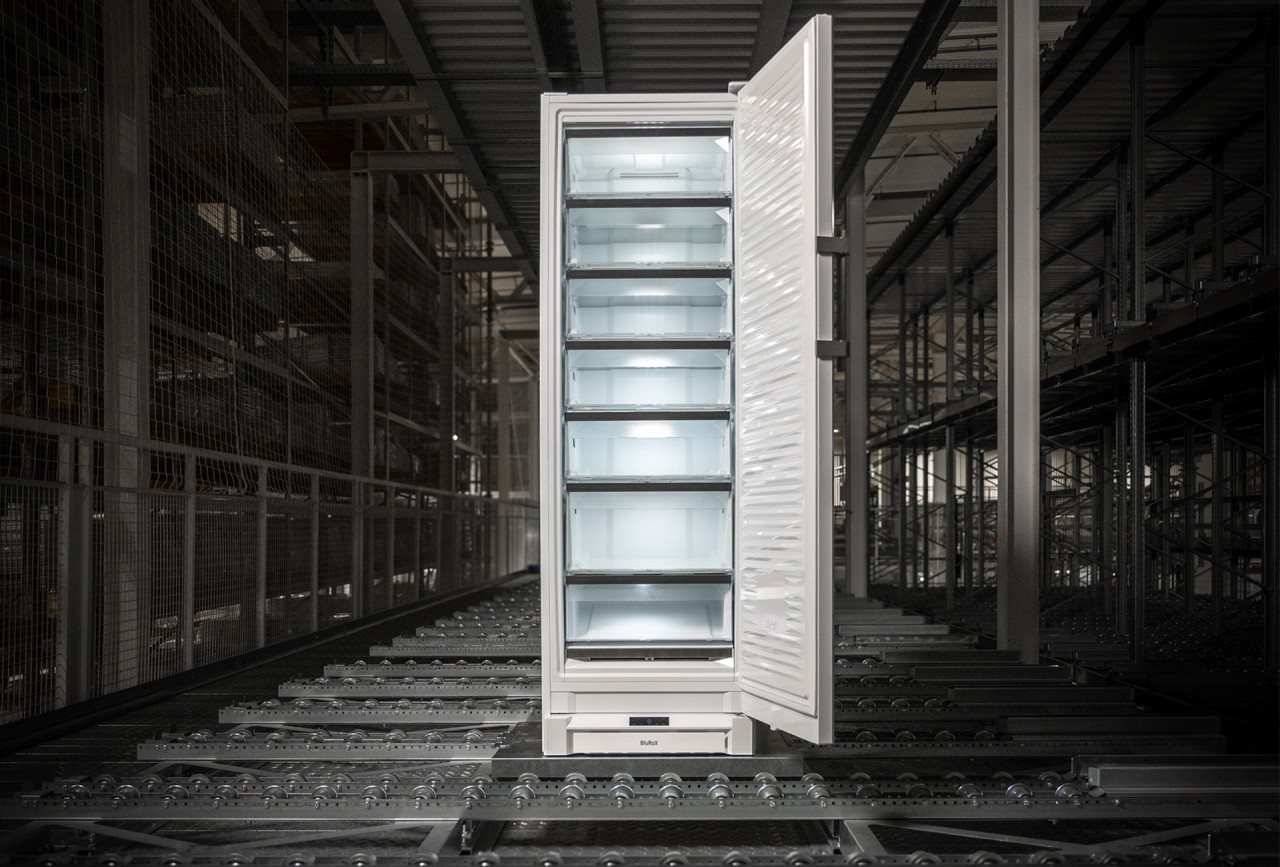
Tomorrow
Other key focuses of product development at Liebherr are sustainability and recyclability. One example of the latter is BluRoX, a new vacuum insulation technology serving as an alternative to the conventional polyurethane (PU) foam. Finely ground lava rock, or perlite as it is known, has low thermal conductivity, making it an effective form of cold insulation that also stabilises the vacuumed components. Consequently, the insulating walls of BluRoX appliances are around one third thinner than those in a conventional foam-insulated appliance. Plus, an appliance featuring exclusively vacuum-perlite insulation technology offers around 25% more capacity than a conventional unit of the same external dimensions. Another advantage: The raw material of perlite can be removed at the end of a BluRoX appliance’s useful life and be recycled without extensive processing. At present, the technology is used solely in the door insulation; in early 2026, the first fully vacuumed appliance will be available on the market.
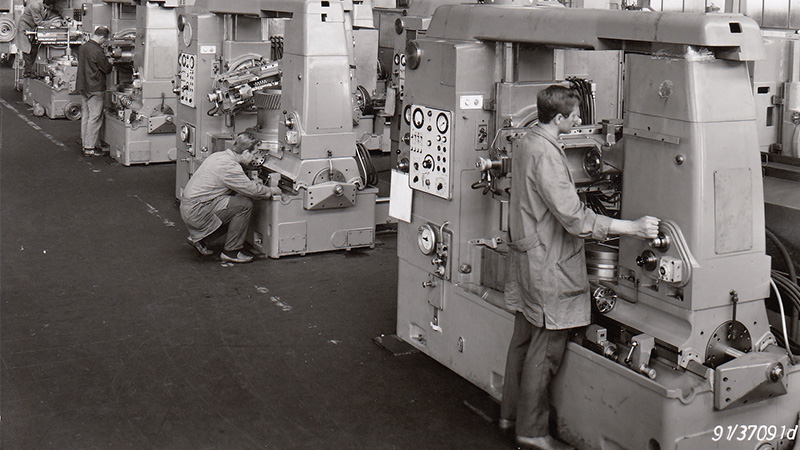
Yesterday
Gear technology has its origins in the mechanics of tower cranes. In the early 1950s, Hans Liebherr wants to buy a gear hobbing machine to manufacture gears but, when he can’t find what he is looking for, he simply builds it himself. And so the high-performance gear hobbing machine, the S 500, is born. Plus, in 1952, the gear technology segment is established in Kirchdorf. In the 1970s, the automotive industry starts to redefine material flow. The integration of robotics in production here sees the previous custom of transfer lines increasingly being replaced by agile systems. Liebherr is already on this innovative path and is quick to supply automation systems, including conveyor systems, gantry robots or pallet handling systems. Since then, automation has become an integral element of the product segment, as reflected in the name.
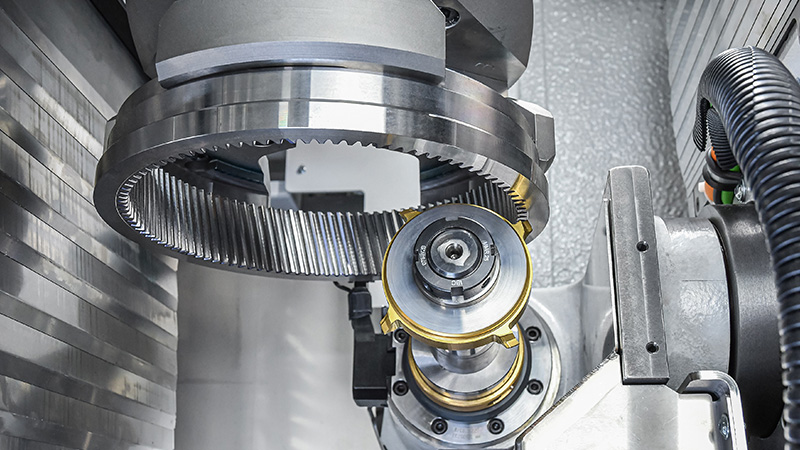
Today
Today, Liebherr brings its customers comprehensive solutions that facilitate the most varied gearings on workpieces. These include complex gear cutting machines as well as gear measuring devices and the corresponding software. Liebherr develops innovative technology solutions and provides machines, tools and processes for almost all technologies from a single source to guarantee high-quality gears. Pioneering spirit is and always will be called for at Liebherr, including in the gear technology and automation systems segment. Especially when it comes to sustainability. That’s why Liebherr-Verzahntechnik GmbH is running the research project ‘ZIRKEL’ in an interdisciplinary consortium of research and industry to investigate the entire circular economy of battery systems from the electric vehicle sector. In 2030, the batteries of an estimated four million electric vehicles could reach the end of their useful life.
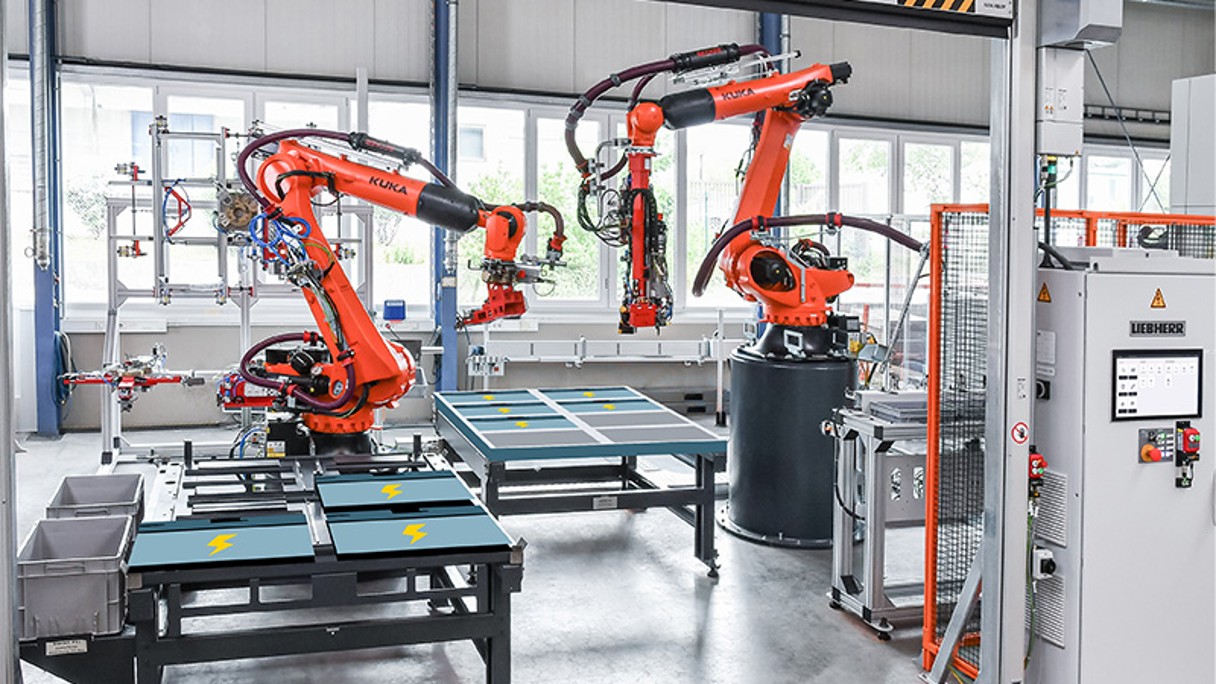
This video is provided by Google*. When you load this video, your data, including your IP address, is transmitted to Google, and may be stored and processed by Google, also for its own purposes, outside the EU or the EEA and thus in a third country, in particular in the USA**. We have no influence on further data processing by Google.
By clicking on “ACCEPT”, you consent to the data transmission to Google for this video pursuant to Art. 6 para. 1 point a GDPR. If you do not want to consent to each YouTube video individually in the future and want to be able to load them without this blocker, you can also select “Always accept YouTube videos” and thus also consent to the respectively associated data transmissions to Google for all other YouTube videos that you will access on our website in the future.
You can withdraw given consents at any time with effect for the future and thus prevent the further transmission of your data by deselecting the respective service under “Miscellaneous services (optional)” in the settings (later also accessible via the “Privacy Settings” in the footer of our website).
For further information, please refer to our Data Protection Declaration and the Google Privacy Policy.*Google Ireland Limited, Gordon House, Barrow Street, Dublin 4, Ireland; parent company: Google LLC, 1600 Amphitheatre Parkway, Mountain View, CA 94043, USA** Note: The data transfer to the USA associated with the data transmission to Google takes place on the basis of the European Commission’s adequacy decision of 10 July 2023 (EU-U.S. Data Privacy Framework).Tomorrow
A circular economy comes down to the ability to recover and recycle a high proportion of raw materials from existing products when they reach the end of their life cycle. Lithium-ion batteries contain valuable raw materials, that should be recycled for both ecological and economical reasons. And that’s what Liebherr-Verzahntechnik GmbH is setting out to do, developing all-new strategies and processes for automated dismantling of high-voltage battery systems. This is designed to recover and reuse as much of the raw materials as possible. Liebherr has made it possible to have the assembly process run in reverse, as is the case with the ZIRKEL project, through a comprehensive and innovative process design for future battery packs built for a circular economy. To this end, the battery system is measured using 2D cameras to identify the positions of the individual linking elements. ‘We have also developed a special gripper system to separate the screwed-down battery cover from the housing in order to be able to remove other components such as cables, busbars and electronics. These parts are then laid down on a table in the same order in which they were removed,’ explains Viktor Bayrhof, product manager for Automation Systems at Liebherr. ‘This guarantees the traceability of the module. A milestone for the future of battery technology,’
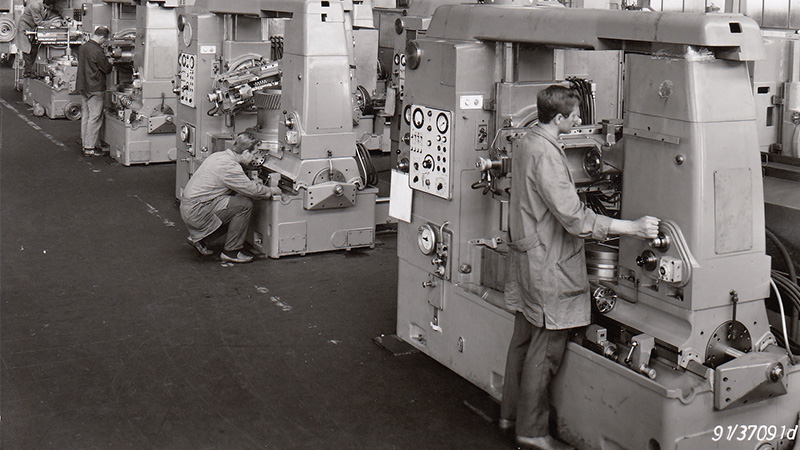
Yesterday
Gear technology has its origins in the mechanics of tower cranes. In the early 1950s, Hans Liebherr wants to buy a gear hobbing machine to manufacture gears but, when he can’t find what he is looking for, he simply builds it himself. And so the high-performance gear hobbing machine, the S 500, is born. Plus, in 1952, the gear technology segment is established in Kirchdorf. In the 1970s, the automotive industry starts to redefine material flow. The integration of robotics in production here sees the previous custom of transfer lines increasingly being replaced by agile systems. Liebherr is already on this innovative path and is quick to supply automation systems, including conveyor systems, gantry robots or pallet handling systems. Since then, automation has become an integral element of the product segment, as reflected in the name.
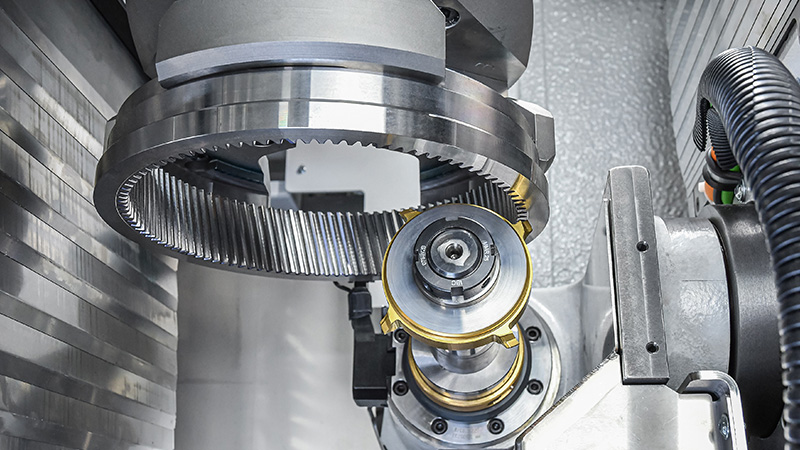
Today
Today, Liebherr brings its customers comprehensive solutions that facilitate the most varied gearings on workpieces. These include complex gear cutting machines as well as gear measuring devices and the corresponding software. Liebherr develops innovative technology solutions and provides machines, tools and processes for almost all technologies from a single source to guarantee high-quality gears. Pioneering spirit is and always will be called for at Liebherr, including in the gear technology and automation systems segment. Especially when it comes to sustainability. That’s why Liebherr-Verzahntechnik GmbH is running the research project ‘ZIRKEL’ in an interdisciplinary consortium of research and industry to investigate the entire circular economy of battery systems from the electric vehicle sector. In 2030, the batteries of an estimated four million electric vehicles could reach the end of their useful life.
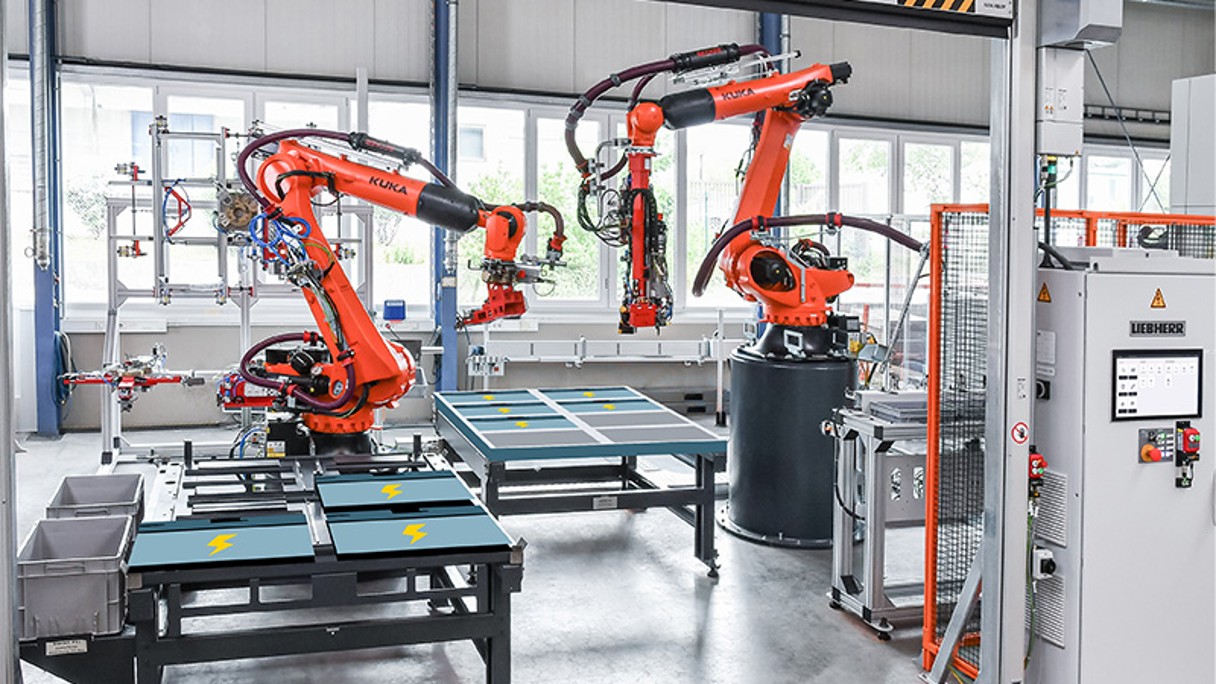
This video is provided by Google*. When you load this video, your data, including your IP address, is transmitted to Google, and may be stored and processed by Google, also for its own purposes, outside the EU or the EEA and thus in a third country, in particular in the USA**. We have no influence on further data processing by Google.
By clicking on “ACCEPT”, you consent to the data transmission to Google for this video pursuant to Art. 6 para. 1 point a GDPR. If you do not want to consent to each YouTube video individually in the future and want to be able to load them without this blocker, you can also select “Always accept YouTube videos” and thus also consent to the respectively associated data transmissions to Google for all other YouTube videos that you will access on our website in the future.
You can withdraw given consents at any time with effect for the future and thus prevent the further transmission of your data by deselecting the respective service under “Miscellaneous services (optional)” in the settings (later also accessible via the “Privacy Settings” in the footer of our website).
For further information, please refer to our Data Protection Declaration and the Google Privacy Policy.*Google Ireland Limited, Gordon House, Barrow Street, Dublin 4, Ireland; parent company: Google LLC, 1600 Amphitheatre Parkway, Mountain View, CA 94043, USA** Note: The data transfer to the USA associated with the data transmission to Google takes place on the basis of the European Commission’s adequacy decision of 10 July 2023 (EU-U.S. Data Privacy Framework).Tomorrow
A circular economy comes down to the ability to recover and recycle a high proportion of raw materials from existing products when they reach the end of their life cycle. Lithium-ion batteries contain valuable raw materials, that should be recycled for both ecological and economical reasons. And that’s what Liebherr-Verzahntechnik GmbH is setting out to do, developing all-new strategies and processes for automated dismantling of high-voltage battery systems. This is designed to recover and reuse as much of the raw materials as possible. Liebherr has made it possible to have the assembly process run in reverse, as is the case with the ZIRKEL project, through a comprehensive and innovative process design for future battery packs built for a circular economy. To this end, the battery system is measured using 2D cameras to identify the positions of the individual linking elements. ‘We have also developed a special gripper system to separate the screwed-down battery cover from the housing in order to be able to remove other components such as cables, busbars and electronics. These parts are then laid down on a table in the same order in which they were removed,’ explains Viktor Bayrhof, product manager for Automation Systems at Liebherr. ‘This guarantees the traceability of the module. A milestone for the future of battery technology,’
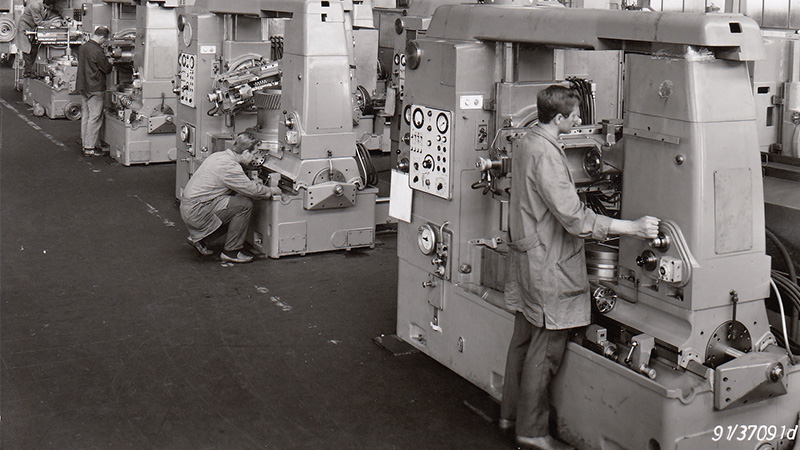
Yesterday
Gear technology has its origins in the mechanics of tower cranes. In the early 1950s, Hans Liebherr wants to buy a gear hobbing machine to manufacture gears but, when he can’t find what he is looking for, he simply builds it himself. And so the high-performance gear hobbing machine, the S 500, is born. Plus, in 1952, the gear technology segment is established in Kirchdorf. In the 1970s, the automotive industry starts to redefine material flow. The integration of robotics in production here sees the previous custom of transfer lines increasingly being replaced by agile systems. Liebherr is already on this innovative path and is quick to supply automation systems, including conveyor systems, gantry robots or pallet handling systems. Since then, automation has become an integral element of the product segment, as reflected in the name.
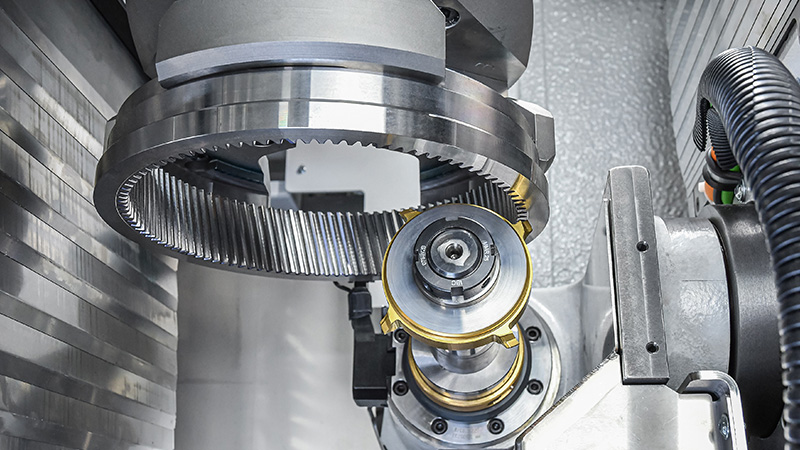
Today
Today, Liebherr brings its customers comprehensive solutions that facilitate the most varied gearings on workpieces. These include complex gear cutting machines as well as gear measuring devices and the corresponding software. Liebherr develops innovative technology solutions and provides machines, tools and processes for almost all technologies from a single source to guarantee high-quality gears. Pioneering spirit is and always will be called for at Liebherr, including in the gear technology and automation systems segment. Especially when it comes to sustainability. That’s why Liebherr-Verzahntechnik GmbH is running the research project ‘ZIRKEL’ in an interdisciplinary consortium of research and industry to investigate the entire circular economy of battery systems from the electric vehicle sector. In 2030, the batteries of an estimated four million electric vehicles could reach the end of their useful life.
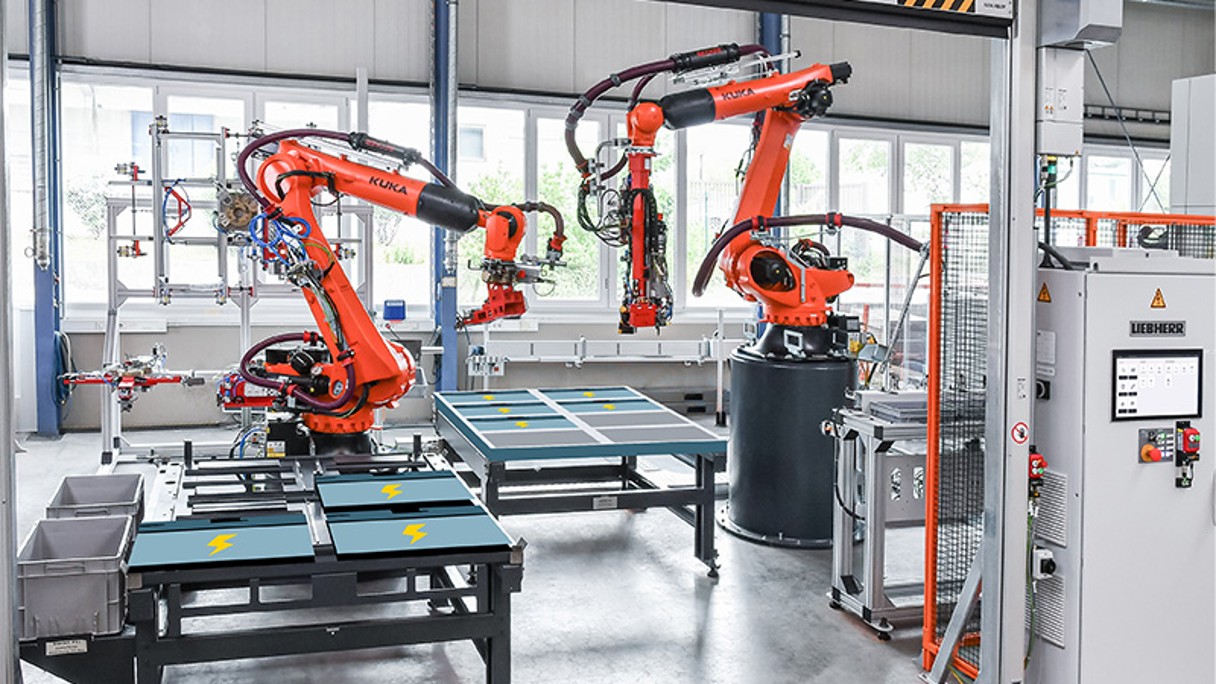
This video is provided by Google*. When you load this video, your data, including your IP address, is transmitted to Google, and may be stored and processed by Google, also for its own purposes, outside the EU or the EEA and thus in a third country, in particular in the USA**. We have no influence on further data processing by Google.
By clicking on “ACCEPT”, you consent to the data transmission to Google for this video pursuant to Art. 6 para. 1 point a GDPR. If you do not want to consent to each YouTube video individually in the future and want to be able to load them without this blocker, you can also select “Always accept YouTube videos” and thus also consent to the respectively associated data transmissions to Google for all other YouTube videos that you will access on our website in the future.
You can withdraw given consents at any time with effect for the future and thus prevent the further transmission of your data by deselecting the respective service under “Miscellaneous services (optional)” in the settings (later also accessible via the “Privacy Settings” in the footer of our website).
For further information, please refer to our Data Protection Declaration and the Google Privacy Policy.*Google Ireland Limited, Gordon House, Barrow Street, Dublin 4, Ireland; parent company: Google LLC, 1600 Amphitheatre Parkway, Mountain View, CA 94043, USA** Note: The data transfer to the USA associated with the data transmission to Google takes place on the basis of the European Commission’s adequacy decision of 10 July 2023 (EU-U.S. Data Privacy Framework).Tomorrow
A circular economy comes down to the ability to recover and recycle a high proportion of raw materials from existing products when they reach the end of their life cycle. Lithium-ion batteries contain valuable raw materials, that should be recycled for both ecological and economical reasons. And that’s what Liebherr-Verzahntechnik GmbH is setting out to do, developing all-new strategies and processes for automated dismantling of high-voltage battery systems. This is designed to recover and reuse as much of the raw materials as possible. Liebherr has made it possible to have the assembly process run in reverse, as is the case with the ZIRKEL project, through a comprehensive and innovative process design for future battery packs built for a circular economy. To this end, the battery system is measured using 2D cameras to identify the positions of the individual linking elements. ‘We have also developed a special gripper system to separate the screwed-down battery cover from the housing in order to be able to remove other components such as cables, busbars and electronics. These parts are then laid down on a table in the same order in which they were removed,’ explains Viktor Bayrhof, product manager for Automation Systems at Liebherr. ‘This guarantees the traceability of the module. A milestone for the future of battery technology,’
This may be of interest to you
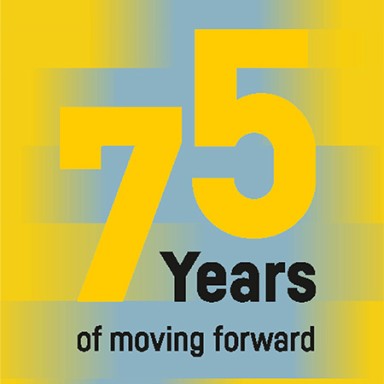
75 years of moving forward
The Liebherr Group is celebrating its 75th anniversary in 2024. To mark the occasion, we are celebrating ‘75 years of moving forward’. Learn more about the anniversary.
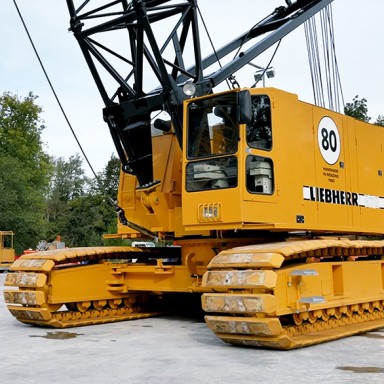
The duty cycle crawler crane that changed Liebherr
In 1979, it was a controversial topic at the ship crane manufacturer Liebherr in Nenzing – the first Liebherr duty cycle crawler crane. Yet it was to lay the foundation for the production of construction machinery at the site.
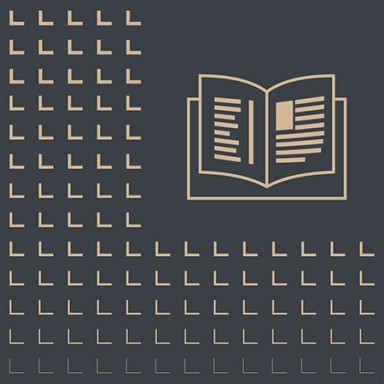
The Group magazine
In the Magazine, you can find a look behind the scenes at Liebherr. Everyday heroes are introduced and solutions for tomorrow's problems are presented. Expect exciting stories about people who achieve great things together with Liebherr.