02
Wind power is learning to swim
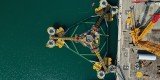
The Liebherr Group
For 75 years, Liebherr has stood for a large, continually developing range of sophisticated products and services. Exceptionally practical, seasoned and proven engineering as well as a consistent high quality level ensure customer benefit in all product areas.
Highlights from the Liebherr world
Other topics
- Merchandising shop
- Sales and service
- Used Equipment Marketplace