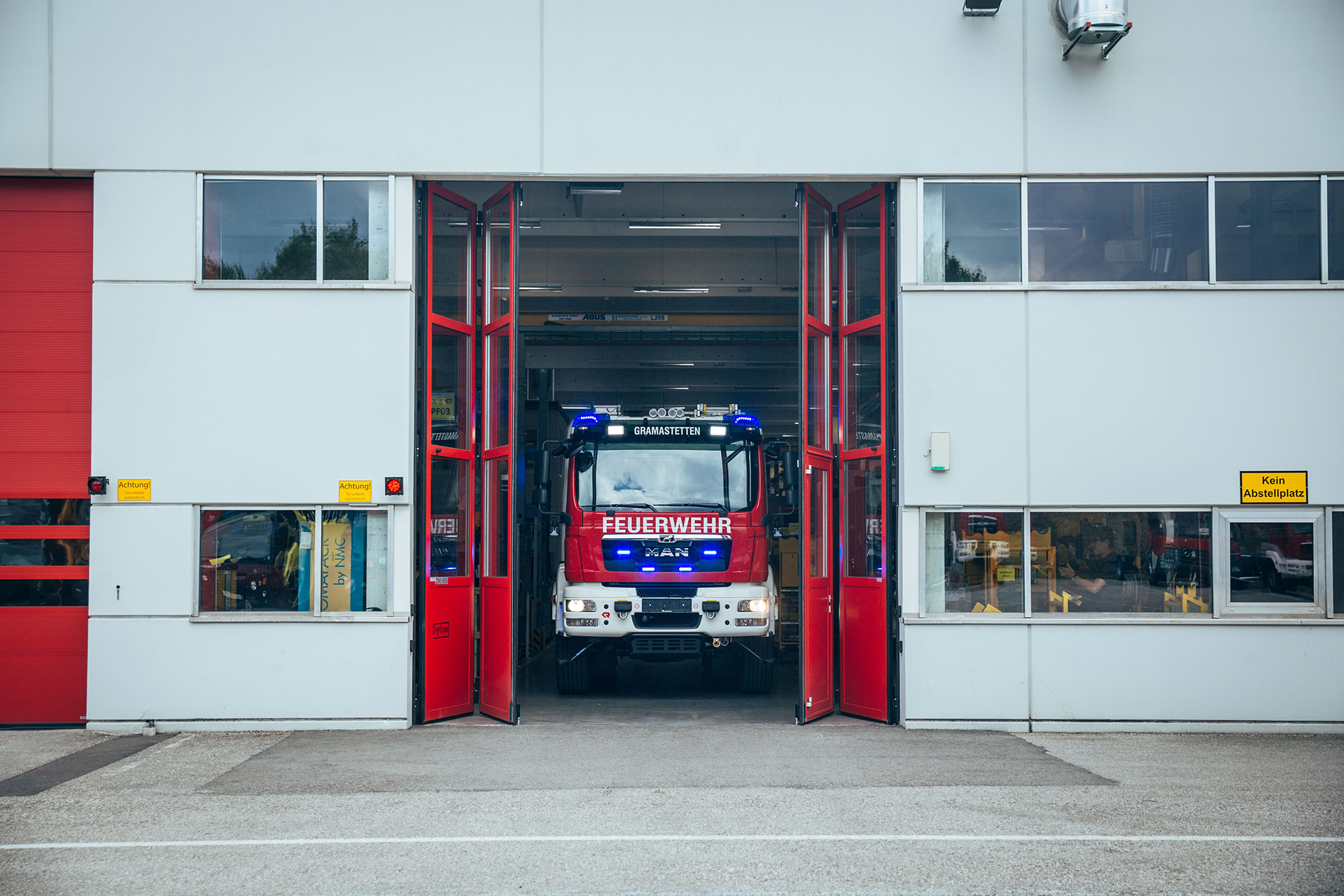
Click RELEASE VIDEO and follow the data protection notices.
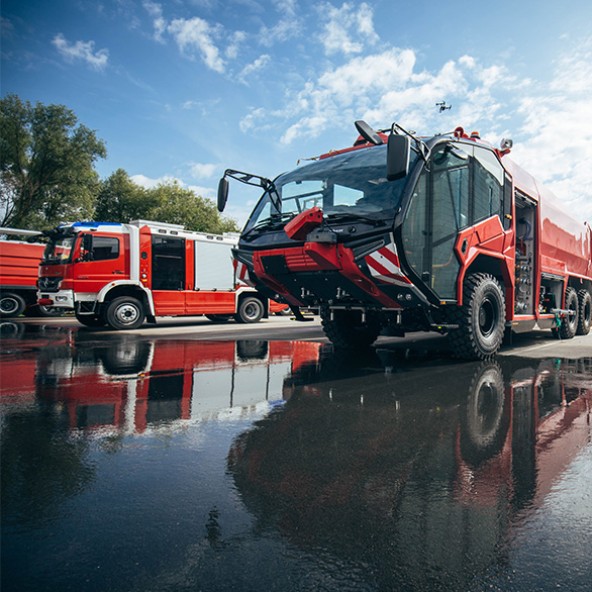
The pump is the heart
The ultimate vehicle: 4,500 litres of fire-extinguishing water, 400 litres of foam, nine crew members on board, plus all the tools and hydraulic rescue equipment necessary to provide help as quickly as possible in the event of an accident on the motorway. Wilfried Thelen, head of the volunteer fire service in Aldenhoven near Aachen, and the members of his unit have high expectations of a fire-fighting vehicle. "Putting out fires, rescuing accident victims and clearing the road for traffic again: we have to do all that under intense stress while maintaining the utmost concentration," says Thelen.
"For that we need a real all-rounder that will operate fully automatic extinguishing and pump systems, transport as much extinguishing agent (water, foam) and as many crew members as possible and, at the same time, still have enough space for technical equipment. Rosenbauer offers us exactly the all-round performer we need." The AT (AT stands for "Aluminium Technology") is a "classic" among municipal emergency vehicles. "It is our first fire-fighting vehicle from this manufacturer," says Thelen. And it was a good investment. "Whereas previously we had to take two vehicles out, now one is enough."
The firefighters from Aldenhoven are particularly impressed by the fully automatic extinguishing and pump technology. "When I clap my hands, it has to work," says Thelen, summing up with a grin the demands on the technology. Even though it is not quite as simple as that, despite being so high-tech, it is important to keep the set-up and operating times as short as possible when deploying the fire-fighting equipment at the site of a fire or accident. "At the push of a button, the pump goes into automatic mode and no longer has to be monitored by our people during operation," says Thelen. "Anything that runs automatically is a help to our emergency service personnel. It means that we can concentrate all our efforts on firefighting and rescue."
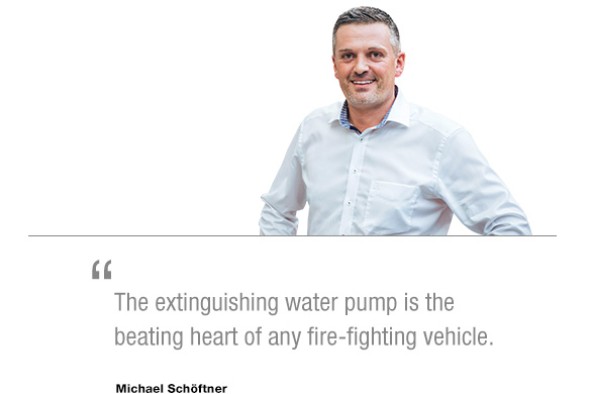
High tech for the heart
Retracing the Aldenhoven fire service's search for this solution leads us to Leonding near Linz, in Upper Austria, where Rosenbauer, one of the world's leading manufacturers of fire-fighting equipment, has its production facility. "The extinguishing water pump is the beating heart of any fire-fighting vehicle," says Michael Schöftner, head of mechanical production of fire-extinguishing systems at Rosenbauer, as we make our way to the "pump line" in Plant I. Michael Wizany is at the set-up station there, in the process of aligning a cast aluminium part for a pump distributor for further processing in the milling machine. It is no conventional computer-controlled CNC milling machine that the 28-year-old is operating. His workstation is conspicuously different and is recognisable from some distance away. It is a four-metre-tall, light-grey round tower, with Liebherr RLS 800 written on it in large letters. "The rotary loading system is located upstream of our milling and drill-machining centre," says Schöftner. Small windows in the tower afford a clear view of 21 pallet spaces in which Michael Wizany can place up to 63 different water pump components ready for fully automatic precision machining. "In this way, we can very precisely fit the order-specific production of pump elements into the cutting, turning and milling process," explains Wizany.
By clicking on “ACCEPT”, you consent to the data transmission to Google for this video pursuant to Art. 6 para. 1 point a GDPR. If you do not want to consent to each YouTube video individually in the future and want to be able to load them without this blocker, you can also select “Always accept YouTube videos” and thus also consent to the respectively associated data transmissions to Google for all other YouTube videos that you will access on our website in the future.
You can withdraw given consents at any time with effect for the future and thus prevent the further transmission of your data by deselecting the respective service under “Miscellaneous services (optional)” in the settings (later also accessible via the “Data protection settings” in the footer of our website).
For further information, please refer to our Data Protection Declaration and the Google Privacy Policy.*Google Ireland Limited, Gordon House, Barrow Street, Dublin 4, Ireland; parent company: Google LLC, 1600 Amphitheatre Parkway, Mountain View, CA 94043, USA** Note: The data transfer to the USA associated with the data transmission to Google takes place on the basis of the European Commission’s adequacy decision of 10 July 2023 (EU-U.S. Data Privacy Framework).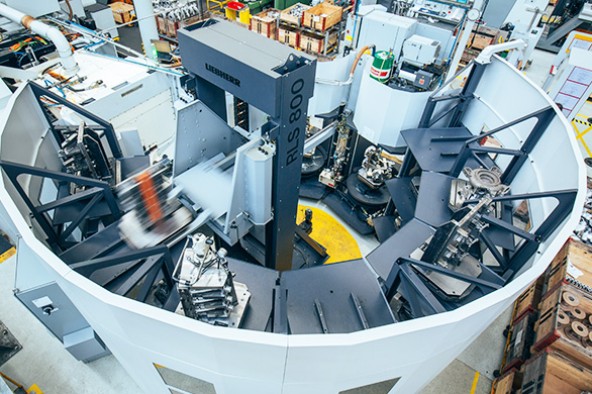
The Liebherr RLS 800 rotary loading system
The rotary loading system from Liebherr is an automation solution which is connected upstream of the machining of parts as an intelligent transport and storage system. The aim: to lower production costs and enable rapid and flexible responses to demand changes in the market, while simultaneously providing maximum user-friendliness, quality and reliability. The machine can independently process 21 pallets containing up to 63 components with up to four hours follow-on production time. During this time, there doesn't have to be an operator standing at the machine.
The RLS 800 is the most productive machine we have. The time saving in production alone is in the order of 30 to 50 per cent.
More productive than ever
"Automation with the aid of the rotary loading system is another milestone for us, enabling us to further customise the manufacture of our pumps and to be very flexible, producing exactly to customer requirements," says Michael Schöftner. "This allows us to work with smaller batch sizes and even, if required, to run a just-in-time production system." The entire system also takes individual delivery dates into account and can be adjusted dynamically according to what the priorities are. And this can be achieved with consistently high efficiency. "Here, we produce an average of 2,000 to 2,500 parts a month, at peak times even 4,000, and this with an error rate of no more than 0.4 per cent," says Michael Wizany. "The RLS 800 is the most productive machine we have," adds Schöftner, the head of production. The time saving in production alone is in the order of 30 to 50 per cent.
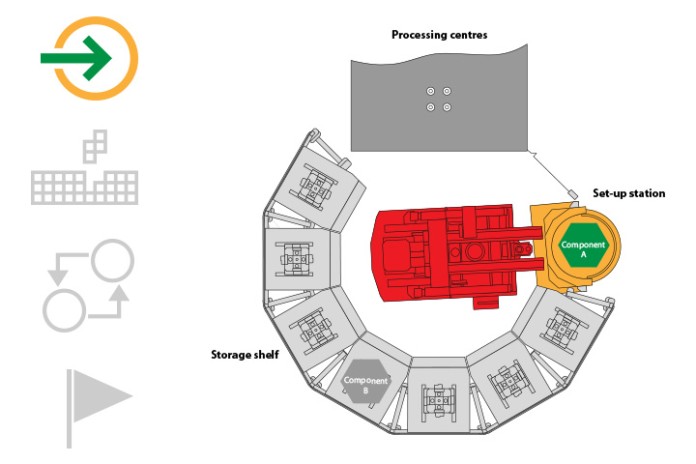
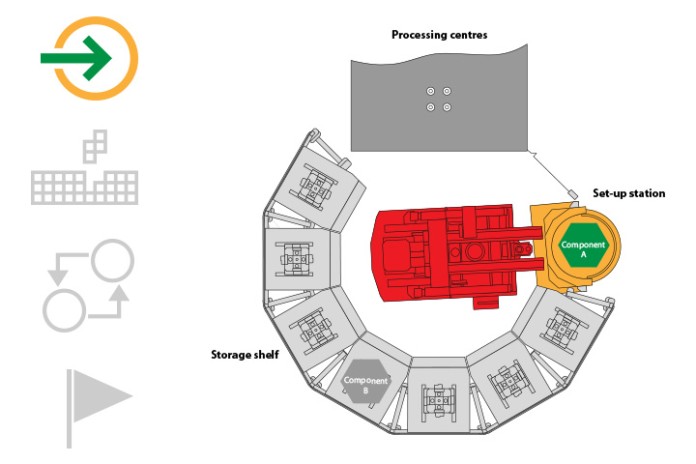
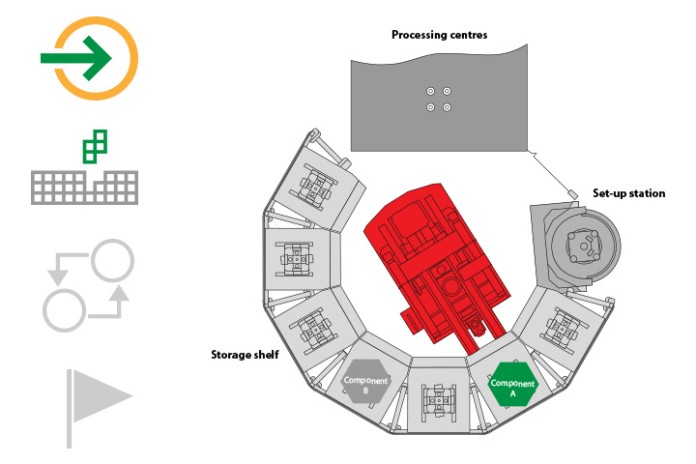
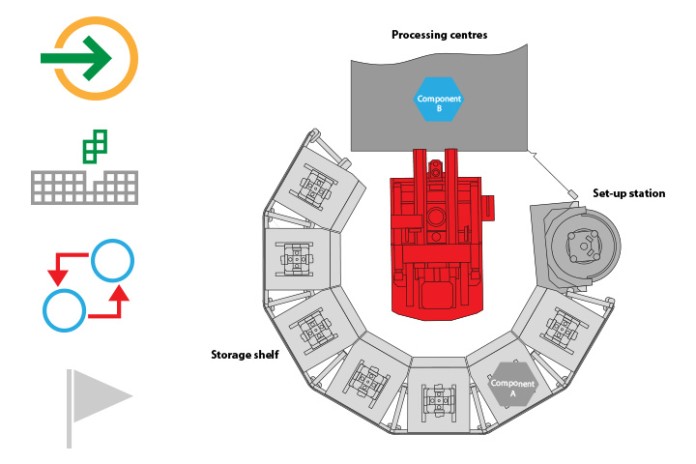
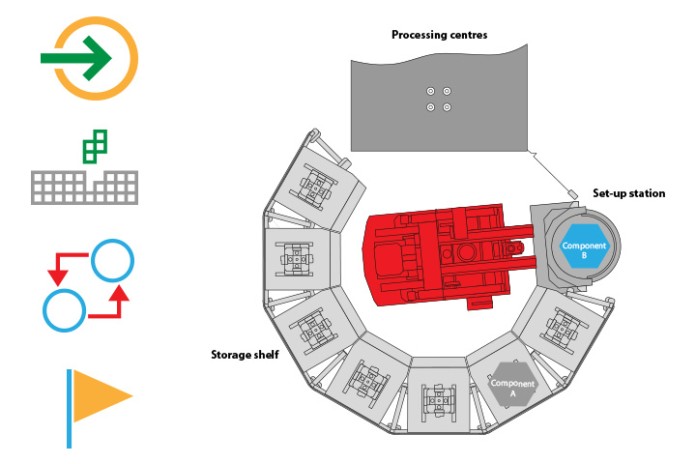
Set-up station
Find out more
Storage shelf
Find out more
Machine load
Find out more
Output
Find out more
Automation will not make people superfluous. On the contrary, the expertise of operators is indispensable in production and will remain so.
Automation: there is still a need for professionals
"We work a two-shift cycle on the Liebherr machine, but thanks to automation, we can continue production for up to four hours after the end of the shift. The next morning, the employee coming on shift simply takes off the parts that have been machined overnight and can set up new workpieces," explains production manager Michael Schöftner. There is no reason to fear that people will become superfluous. "Trained operators will always be needed. Their expertise in materials science and in assessing the status of the machine, the loading system and the components is essential." Michael Wizany, who has two-and-a-half years' experience in this field, realised a long time ago that "Automated systems will always need professionals to operate them. You always have to be on the ball. For me, that is what makes working with the latest technology so exciting."
RLS 800: Next level efficiency
By clicking on “ACCEPT”, you consent to the data transmission to Google for this video pursuant to Art. 6 para. 1 point a GDPR. If you do not want to consent to each YouTube video individually in the future and want to be able to load them without this blocker, you can also select “Always accept YouTube videos” and thus also consent to the respectively associated data transmissions to Google for all other YouTube videos that you will access on our website in the future.
You can withdraw given consents at any time with effect for the future and thus prevent the further transmission of your data by deselecting the respective service under “Miscellaneous services (optional)” in the settings (later also accessible via the “Data protection settings” in the footer of our website).
For further information, please refer to our Data Protection Declaration and the Google Privacy Policy.*Google Ireland Limited, Gordon House, Barrow Street, Dublin 4, Ireland; parent company: Google LLC, 1600 Amphitheatre Parkway, Mountain View, CA 94043, USA** Note: The data transfer to the USA associated with the data transmission to Google takes place on the basis of the European Commission’s adequacy decision of 10 July 2023 (EU-U.S. Data Privacy Framework).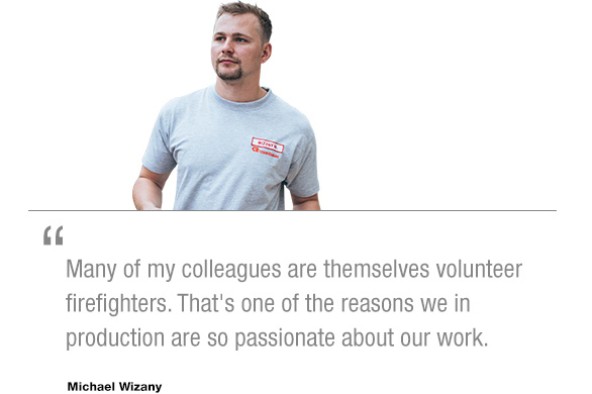
Fired up about rescue work
Michael Wizany's fascination with technology is fuelled by his fascination with the fire service. "Many of my colleagues are themselves volunteer firefighters. They are really passionate about it." This means that when it comes to innovations in designing and equipping the vehicles, there is always plenty of practical experience to draw on. Right at the top of Rosenbauer's agenda is the need to reduce the weight of vehicles and to ensure that operating them is as easy and intuitive as possible. "Nowadays, because there are more and more women and older firefighters on active service, it is important for people with less physical strength to be able to do the work," says Michael Schöftner. "That's why our technology is aimed at making it possible for on-duty firefighters to work more efficiently, safely, ergonomically and in a more environmentally friendly way."
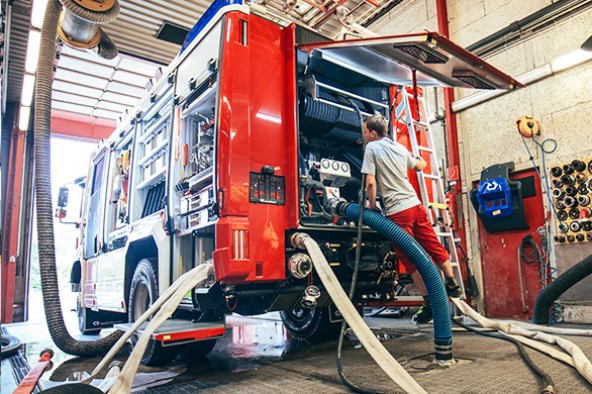
Fire engines for the whole world
Rosenbauer obviously has its finger firmly on the pulse of the industry here. Rosenbauer produces approximately 2,500 vehicles worldwide, which are deployed around the globe - in Europe and the USA, in Asia, in the Arab states and in South America. This means constantly having to meet different sets of requirements and standards. They manufacture around 2,000 versions of the pump alone – without automation, this wouldn't really be economically viable nowadays. Fitted with the appropriately configured peripherals and equipped with suction device, venting device, pump pressure regulator, foam premixing system, pipework and controls, the pump is then installed in the vehicle as a ready-to-install component.
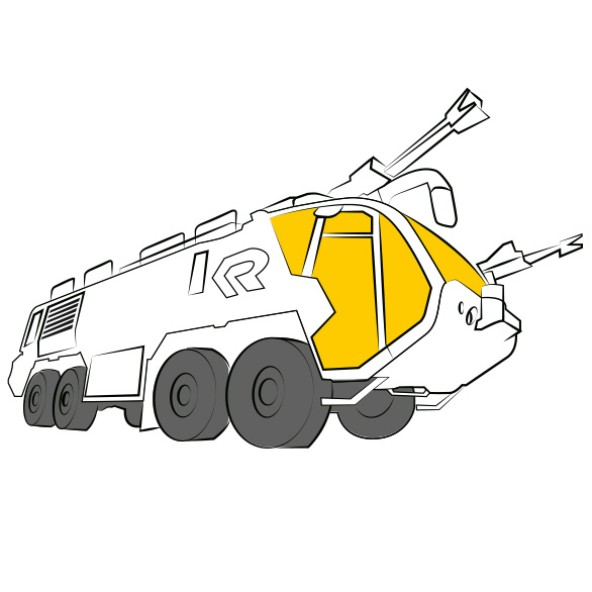
Maximum power for the airport:
The Panther is one of Rosenbauer's flagship products. It is a firefighting colossus that was specially designed for use at airports and can transport up to 19,000 litres of water in its tank. The technology, the chassis and the customised design are all produced by Rosenbauer. Depending on the engine type, the Panther can accelerate from 0 to 80 kilometres per hour in 25 seconds or less. With the Panther, the hoses can be charged even at full speed. The roof and bumper turrets are designed for an output of 10,000 litres per minute and a throw range of up to 90 metres.
The Panther
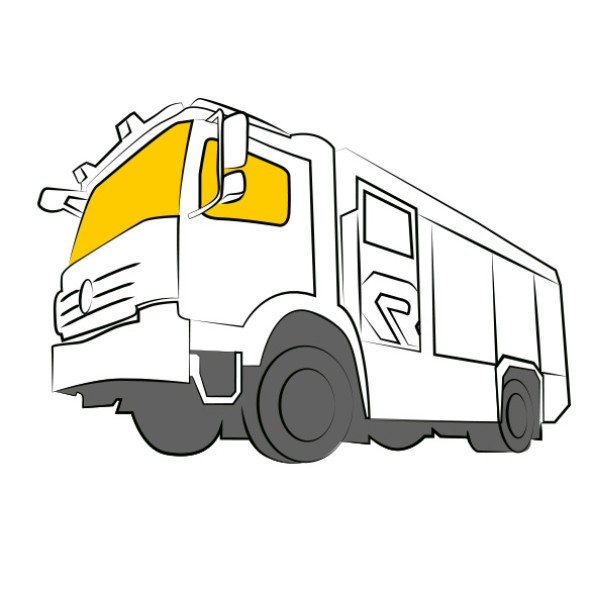
For town and country:
Municipal vehicles, such as those in the AT range, account for more than half of Rosenbauer's annual production. AT stands for “Aluminium Technology”, since the frame (also developed by Rosenbauer), which is later wedded to the chassis, is made of aluminium. The water tanks for these vehicles hold up to 4,500 litres of extinguishing water. They are used as fire-fighting and rescue vehicles by countless fire services.
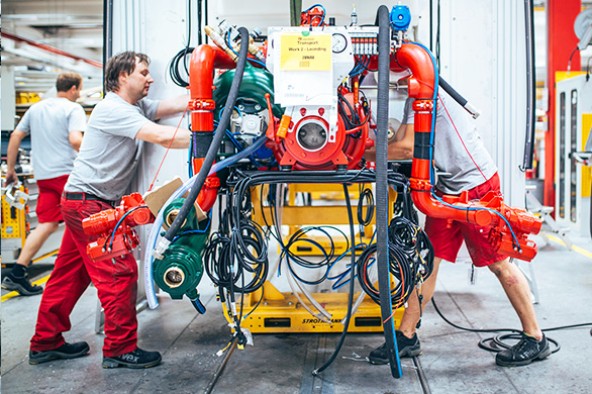
Extinguishing fires with a lantern
For installation in municipal or airport fire engines, the pump will have been shuttled to the nearby Factory II. Prior to this, it will have undergone various machining, finishing and inspection stages. The main focus here is on the pump drive. The so-called "lantern" will later establish the connection with the engine and is often supplemented with a gearbox for optimal synchronisation of the pump speed and the engine speed. During discussions about the design of their new vehicle, the Aldenhoven firefighters were particularly keen for it to have simple, fully automatic and safe user guidance and control technology.
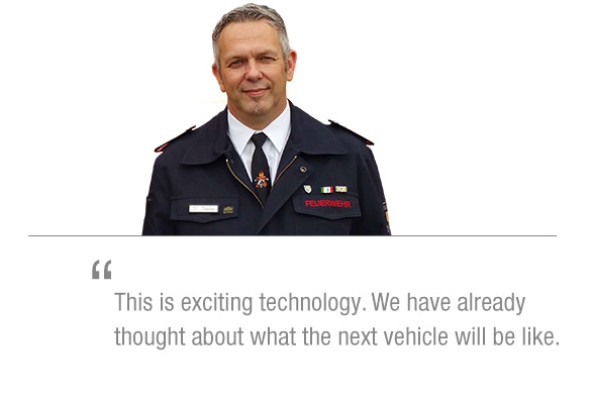
A fire engine as a composition
The firefighters had already discussed beforehand all the details and special requirements in terms of vehicle and extinguishing technology with the experts at Rosenbauer. On the AT assembly line, everything they discussed goes straight into the "composition" of the Aldenhoven fire engine. At the various stations, 14 in all, the vehicle "grows" step by step. This process means that not all but very many vehicles are as unique as their customers.
By clicking on “ACCEPT”, you consent to the data transmission to Google for this video pursuant to Art. 6 para. 1 point a GDPR. If you do not want to consent to each YouTube video individually in the future and want to be able to load them without this blocker, you can also select “Always accept YouTube videos” and thus also consent to the respectively associated data transmissions to Google for all other YouTube videos that you will access on our website in the future.
You can withdraw given consents at any time with effect for the future and thus prevent the further transmission of your data by deselecting the respective service under “Miscellaneous services (optional)” in the settings (later also accessible via the “Data protection settings” in the footer of our website).
For further information, please refer to our Data Protection Declaration and the Google Privacy Policy.*Google Ireland Limited, Gordon House, Barrow Street, Dublin 4, Ireland; parent company: Google LLC, 1600 Amphitheatre Parkway, Mountain View, CA 94043, USA** Note: The data transfer to the USA associated with the data transmission to Google takes place on the basis of the European Commission’s adequacy decision of 10 July 2023 (EU-U.S. Data Privacy Framework).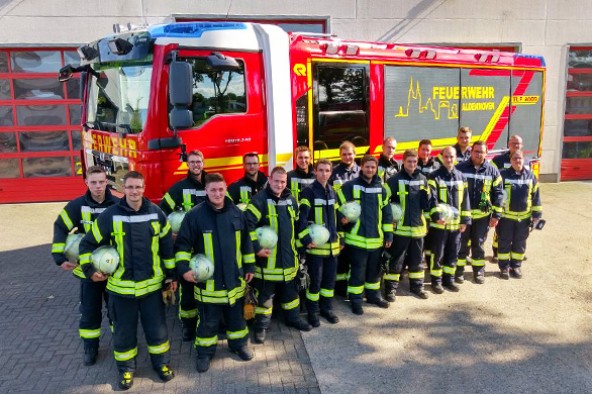
Made to match
Prior to the fitting-out of the vehicle, the Aldenhoven firefighters had discussed their operational needs right down to the last detail. One month sooner than expected, six men from the Aldenhoven volunteer fire service were finally able to turn out and collect their new vehicle from Rosenbauer's German branch plant in Luckenwalde. "Right from the beginning, our new, custom-built vehicle has been a perfect match for us," says Thelen happily. "It was clear from the very first callouts: This is exciting technology. We have already thought about what the next vehicle will be like."