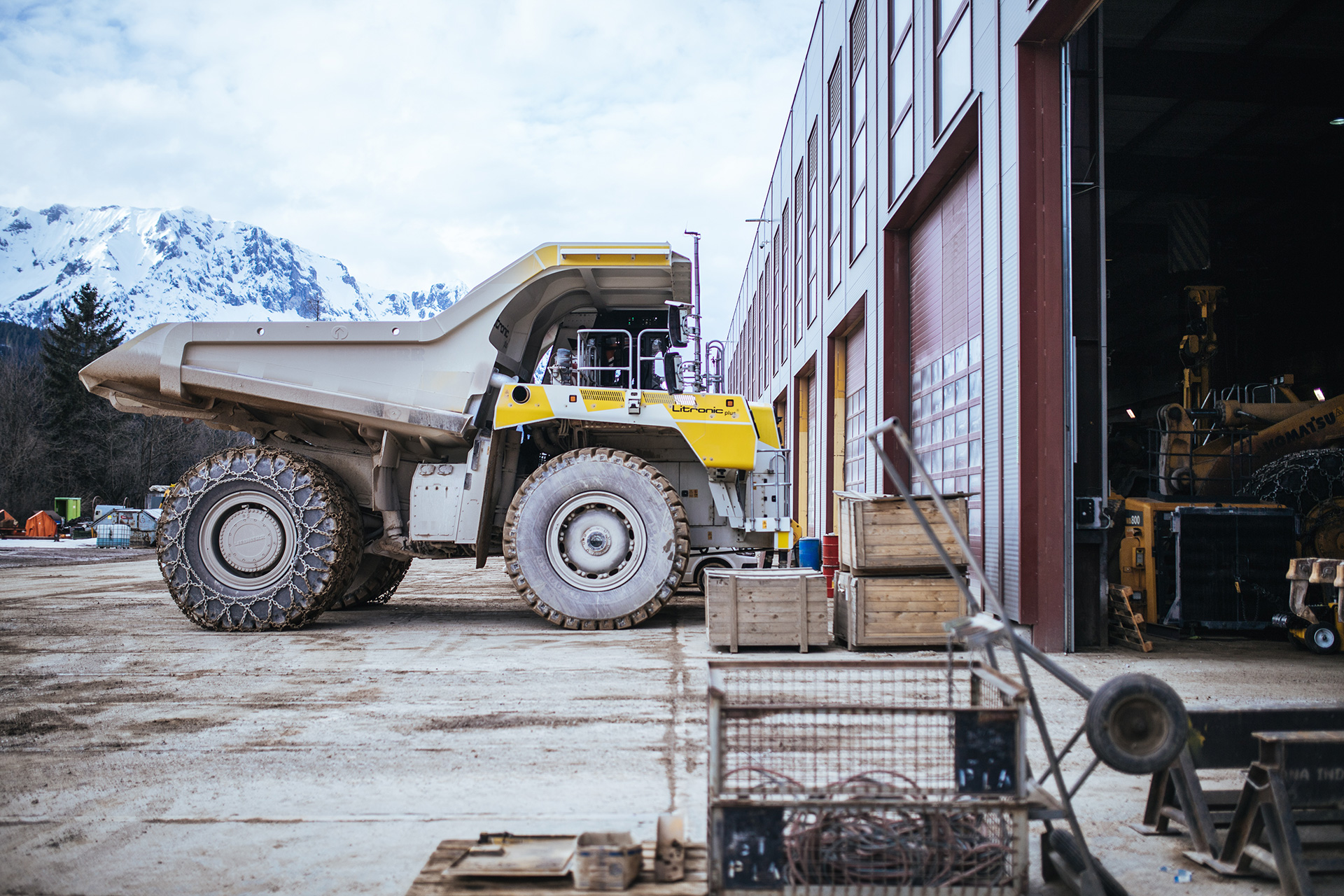
Click RELEASE VIDEO and follow the data protection notices.
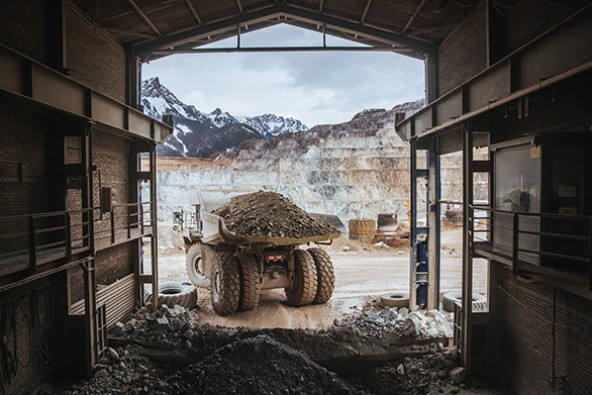
With a blast into the future
No sooner has “3-2-1: brenna tuat’s!” crackled from the walkie-talkie than the mountain begins to tremble. Around 80,000 tons of rock thunder down the slopes in a cloud of dust. We are at the Erzberg in Styria, the largest ore deposit in the Alps. Here, in the biggest and most modern open-cast mine in Central Europe, iron ore has been extracted for more than 1,300 years.
Rock is blasted twice a day so that 12 million tons of the iron-rich siderite ore can be turned into three million tons of fine ore every year. For 230 mineworkers at VA Erzberg GmbH this means they have their hands full. They work in four shifts, around the clock, the whole year. Three wheel loaders and nine heavy-duty trucks see to transportation of the material. A very special truck was added to the fleet in August last year: the T 236 from Liebherr, a 180-ton powerhouse with 1,200 HP (895 kW) designed for a load of up to 100 tons.
I was very curious about the diesel-electric drive and was immediately bowled over completely by the torque. The power is there instantaneously. A great feeling.
On-the-job around the clock – the whole year long
Sitting at the wheel is Gerhard Bayer. Having spent the last 27 years driving up, down and around the Erzberg in a variety of heavy trucks, the driver and driving instructor knows the terrain and its demands on vehicles like the back of his hand. With his experience and his ability not only to understand the vehicle, but also to convey anomalies in operation in plain language, he is well-nigh the ideal test driver and congenial partner for Laurent Fricker. The service engineer from Liebherr accompanies him constantly with his laptop, connecting to the complex vehicle electronics to measure and document all machine and driving data. Of which there is plenty.
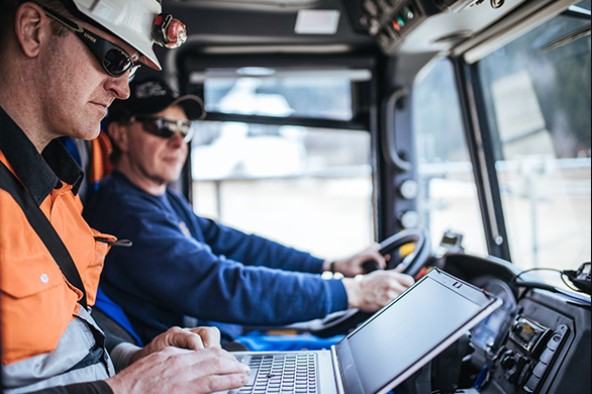
Mine as test lab
“The T 236 is a world first. Never before has a truck in this vehicle class been powered by a diesel-electric drive,” says Fricker. The rear axle of the 100-ton mining truck is driven by an electric motor, whose generator draws its energy from a diesel engine. “Now the concept must prove its worth in everyday mining operations under extreme climatic conditions,” says Fricker. Every day of driving experience makes the innovative technology a bit better. So at the end of the shift, Fricker cannot yet call it a day. He analyzes the day’s vehicle data on his laptop and then sends it to France per data line where the Development Department of Liebherr-Mining Equipment Colmar SAS is eagerly awaiting its arrival.
By clicking on “ACCEPT”, you consent to the data transmission to Google for this video pursuant to Art. 6 para. 1 point a GDPR. If you do not want to consent to each YouTube video individually in the future and want to be able to load them without this blocker, you can also select “Always accept YouTube videos” and thus also consent to the respectively associated data transmissions to Google for all other YouTube videos that you will access on our website in the future.
You can withdraw given consents at any time with effect for the future and thus prevent the further transmission of your data by deselecting the respective service under “Miscellaneous services (optional)” in the settings (later also accessible via the “Data protection settings” in the footer of our website).
For further information, please refer to our Data Protection Declaration and the Google Privacy Policy.*Google Ireland Limited, Gordon House, Barrow Street, Dublin 4, Ireland; parent company: Google LLC, 1600 Amphitheatre Parkway, Mountain View, CA 94043, USA** Note: The data transfer to the USA associated with the data transmission to Google takes place on the basis of the European Commission’s adequacy decision of 10 July 2023 (EU-U.S. Data Privacy Framework).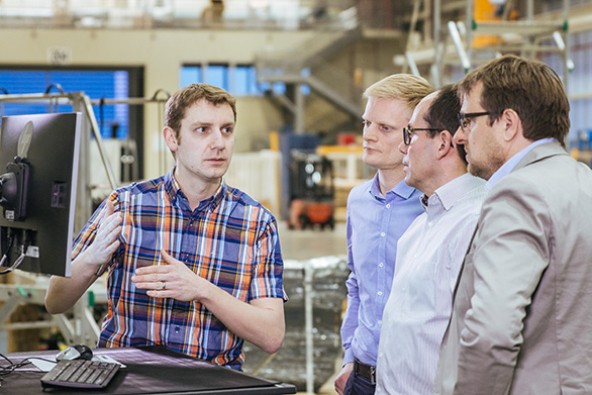
The 100-ton startup
“We want to build a truck. That was the clear message at the end of 2013,” Dr. Burkhard Richthammer recalls. The Managing Director Design & Engineering at Liebherr-Mining Equipment Colmar was tasked with developing a completely new vehicle in the middle category of heavy-duty vehicles. The machine most used in mines and large quarries had until then been missing in Liebherr’s mining range, and the new vehicle was to round off the portfolio of successful mining excavators and crawler tractors for this market.
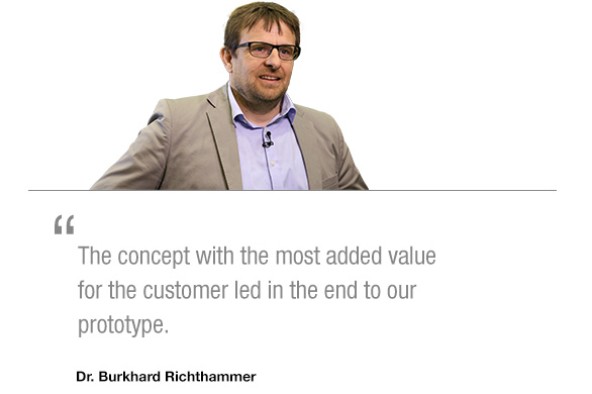
First of all, off to the customer
“At the beginning I was alone with a blank sheet of paper, a laptop and a phone. I was a one-man startup,” reports Dr. Richthammer. The first thing the mining engineer, who is at home in the sale and product management of large excavators, did was to visit customers to ask them what they really could use.
At the same time Dr. Richthammer formed a small, but fine team of engineers, service experts and salespeople, who worked hand-in-hand with experienced mining colleagues from Liebherr from the USA, South Africa and Australia. “Experienced practitioners were therefore involved in the design and load management of the new truck right from the start. Our goal: to develop a vehicle meeting the needs of customers as far as possible,” says Dr. Richthammer.
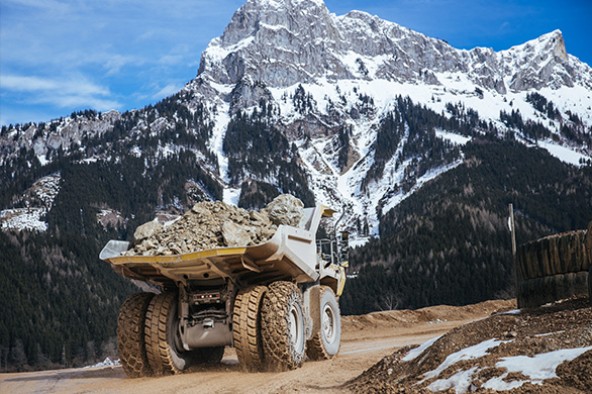
Free thinkers
For Kai Kugelstadt, the head of engineering in the Liebherr team, the special challenge, but also big appeal of the project lay in the startup character of the T 236 development. “We had nothing when we started development of this special type of mining truck – no benchmark, no predecessor model, no production experience – we were able to think freely, question everything and develop a new, own concept for this class of tonnage. And, above all, we were able to fall back on Liebherr’s complete portfolio of products and services – particularly on more than 10 years of experience in vertically integrated electric drive technologies”, Kugelstadt explains.
The advantages of the new diesel-electric drive built should sound good to the ears of the users in particular. Constant power transmission to the rear axle – and that in all driving conditions, less wear and tear, longer lifetime, longer maintenance intervals and thus cheaper maintenance costs, and better total cost of ownership (TCO).
By clicking on “ACCEPT”, you consent to the data transmission to Google for this video pursuant to Art. 6 para. 1 point a GDPR. If you do not want to consent to each YouTube video individually in the future and want to be able to load them without this blocker, you can also select “Always accept YouTube videos” and thus also consent to the respectively associated data transmissions to Google for all other YouTube videos that you will access on our website in the future.
You can withdraw given consents at any time with effect for the future and thus prevent the further transmission of your data by deselecting the respective service under “Miscellaneous services (optional)” in the settings (later also accessible via the “Data protection settings” in the footer of our website).
For further information, please refer to our Data Protection Declaration and the Google Privacy Policy.*Google Ireland Limited, Gordon House, Barrow Street, Dublin 4, Ireland; parent company: Google LLC, 1600 Amphitheatre Parkway, Mountain View, CA 94043, USA** Note: The data transfer to the USA associated with the data transmission to Google takes place on the basis of the European Commission’s adequacy decision of 10 July 2023 (EU-U.S. Data Privacy Framework).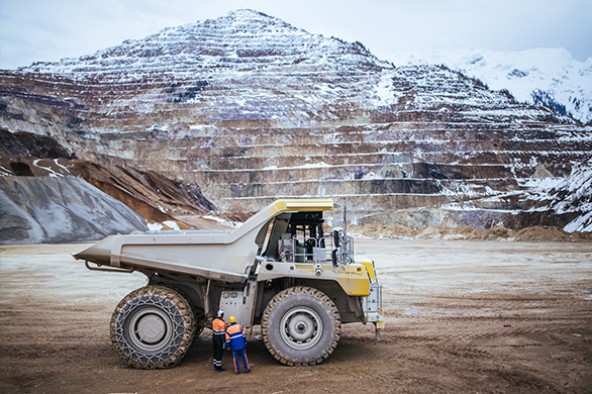
Under the toughest conditions
“The T 236 is designed for maximum performance under the toughest conditions,” Dr. Burkhard Richthammer emphasizes. The purpose of the year-long test in practical service on the Erzberg is now final fine tuning of the vehicle before it goes into series production in 2019. “That is best live engineering in cooperation with our customers. This always results in further new perspectives.”
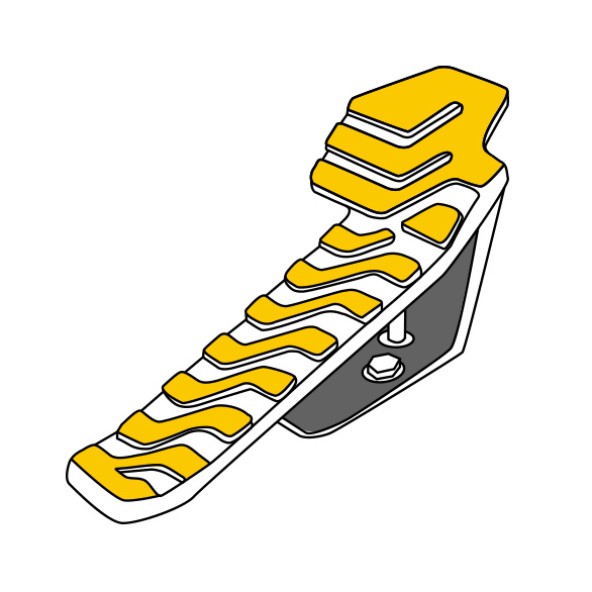
Engineering know-how: diesel-electric drive
When gradients change while climbing uphill, mechanically driven heavy-duty vehicles need to switch gear. High forces act on the drive wheels during this load change. On gravel roads this often results in juddery irregularities, which additionally hamper a smooth ascent and push up fuel consumption.
Based on the Litronic Plus Generation 2 developed by Liebherr, the diesel-electric drive of the T 236 performs its job without gear changes and pulls its load upwards at a constant speed.
The driving concept in detail
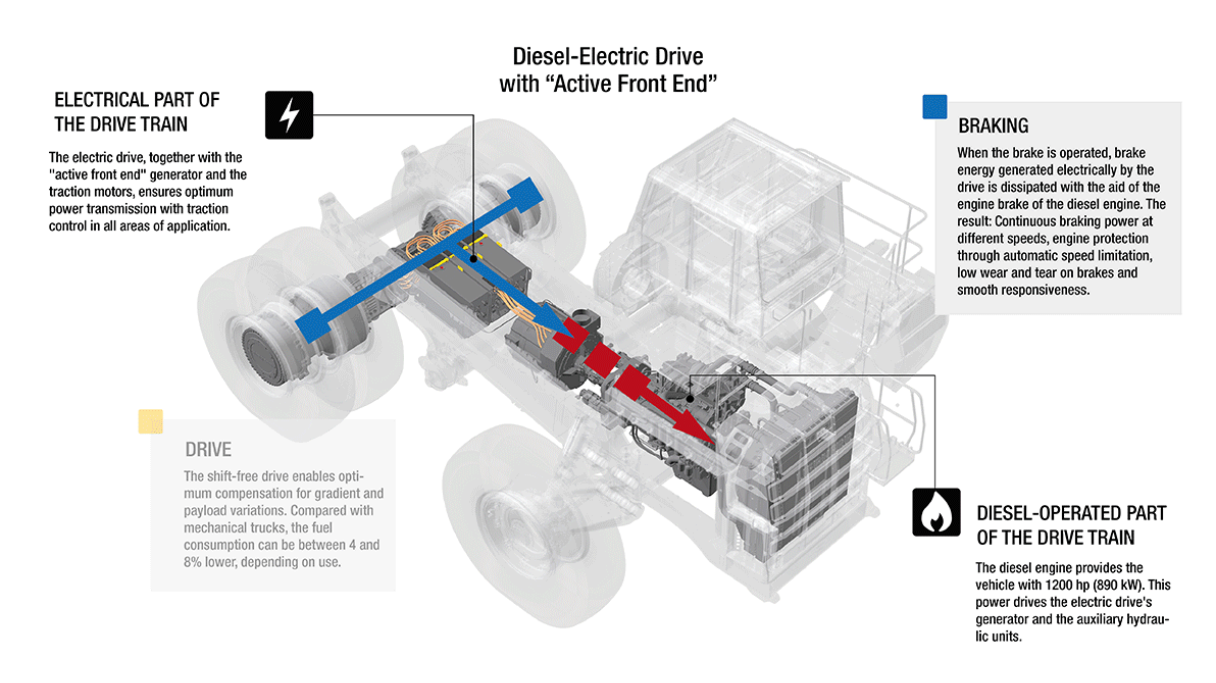
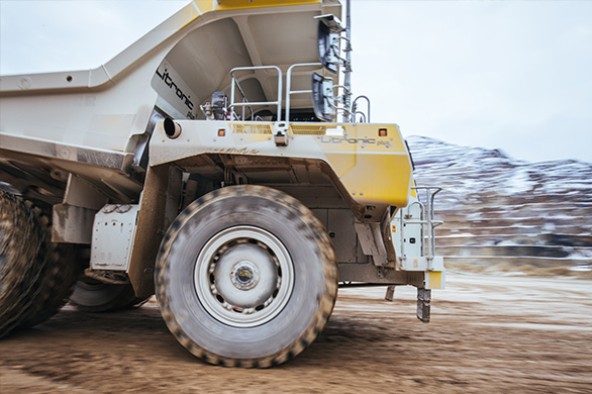
High starting torque
In the field operation trials at the Erzberg mine the T 236 impressed the test drivers with its high starting torque and good continuous power transmission. The truck has thus shown itself to be impervious to driving speed in varying gradients and payloads.
When braking, the truck “draws” on the electric motor. The generator is used in the Active-Front technology in deceleration mode as motor to power the combustion engine. The drive system then works with a controlled engine speed virtually without consuming fuel and can never over-rev. In addition to this, oil-cooled multiple disc brakes allow simultaneous, especially reliable and continuous braking with the front and rear axles.
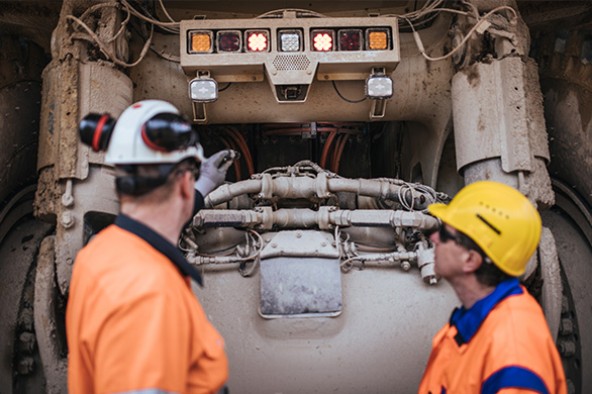
Maintenance-friendly concept
The diesel-electric drive works with a low voltage of 690 VAC and 900 VDC. This makes it possible for normal technicians without special heavy current qualifications to carry out maintenance work on the system on site. This increases safety at the workplace and saves maintenance costs.
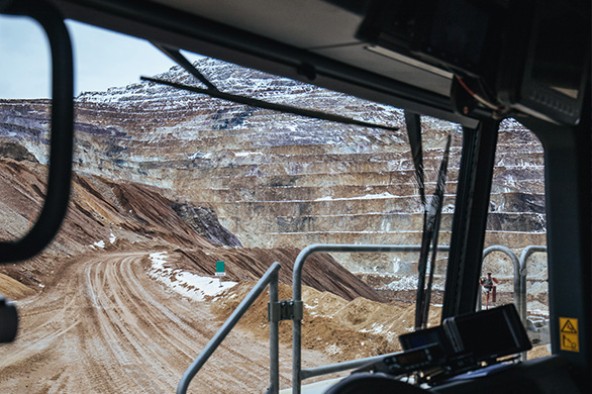
Full speed in the perfect range
Six kilometers steep uphill. The trip on the ramp up to the “Sturz”, where the debris is dumped demands everything the fully laden trucks have to offer. For Gerhard Bayer and his co-pilot Laurent Fricker this means 10 to 12 minutes at full throttle. All systems turned to max. Where conventional diesel-mechanical trucks need to change gear time and again and engine speed rises and falls, the T 236 pulls smoothly. “I can drive the complete section at an ideal rpm of around 1,800 revs. No jerking or jolting, no revving of the engine, just a very comfortable drive,” says Gerhard Bayer happily.
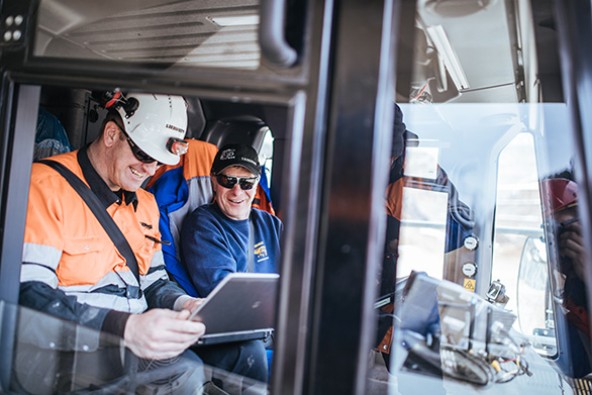
Scrutinizing the lot
Gerhard Bayer enjoys taking over all transport work in routine life at the mine with the new machine. But he enjoys his role as test driver just as much. “With Laurent I scrutinize everything: not just the drive system, but also the cab and its equipment and the suspension concept. Together we work with the developers in Colmar on making the T 236 a little bit better step by step.” Whenever Laurent Fricker installs new software from Colmar, the handling changes. “That is always very exciting,” says Bayer.
Josef Pappenreiter also monitors the progress in the development of the mining truck very closely. The technical director of VA Erzberg GmbH has great expectations of the diesel-electric drive regarding the performance, efficiency and economy of such mining vehicle concepts. “Good performance and trouble-free availability of the transport vehicles are a significant factor for success in the competitive world of mining. We therefore want to stay at the forefront technologically at all times,” says Pappenreiter.
By clicking on “ACCEPT”, you consent to the data transmission to Google for this video pursuant to Art. 6 para. 1 point a GDPR. If you do not want to consent to each YouTube video individually in the future and want to be able to load them without this blocker, you can also select “Always accept YouTube videos” and thus also consent to the respectively associated data transmissions to Google for all other YouTube videos that you will access on our website in the future.
You can withdraw given consents at any time with effect for the future and thus prevent the further transmission of your data by deselecting the respective service under “Miscellaneous services (optional)” in the settings (later also accessible via the “Data protection settings” in the footer of our website).
For further information, please refer to our Data Protection Declaration and the Google Privacy Policy.*Google Ireland Limited, Gordon House, Barrow Street, Dublin 4, Ireland; parent company: Google LLC, 1600 Amphitheatre Parkway, Mountain View, CA 94043, USA** Note: The data transfer to the USA associated with the data transmission to Google takes place on the basis of the European Commission’s adequacy decision of 10 July 2023 (EU-U.S. Data Privacy Framework).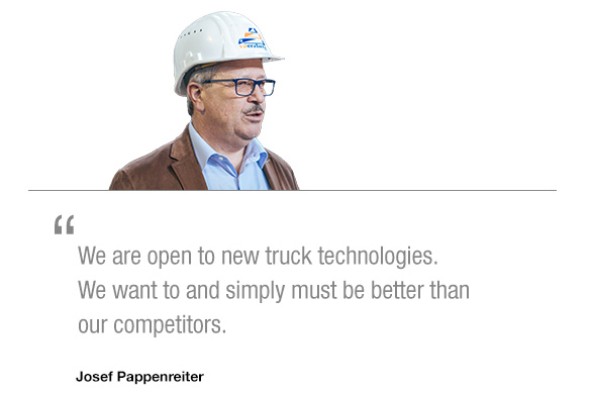
Continuous research
The mine operator therefore gladly broke new technological ground together with Liebherr with the diesel-electric drives in the 100-ton class. But for VA Erzberg GmbH, the journey does not stop there. “We are already thinking with Liebherr about how we can develop electrification of the drives further,” says Pappenreiter. “It is already clear now: the effort is worth its while. The performance of the vehicles increases, the energy and maintenance costs drop, and the environment is protected. That's what I call win-win in the best sense.”