Flexible automation solutions for the automotive and recycling industries
Non-destructive disassembly of battery packs
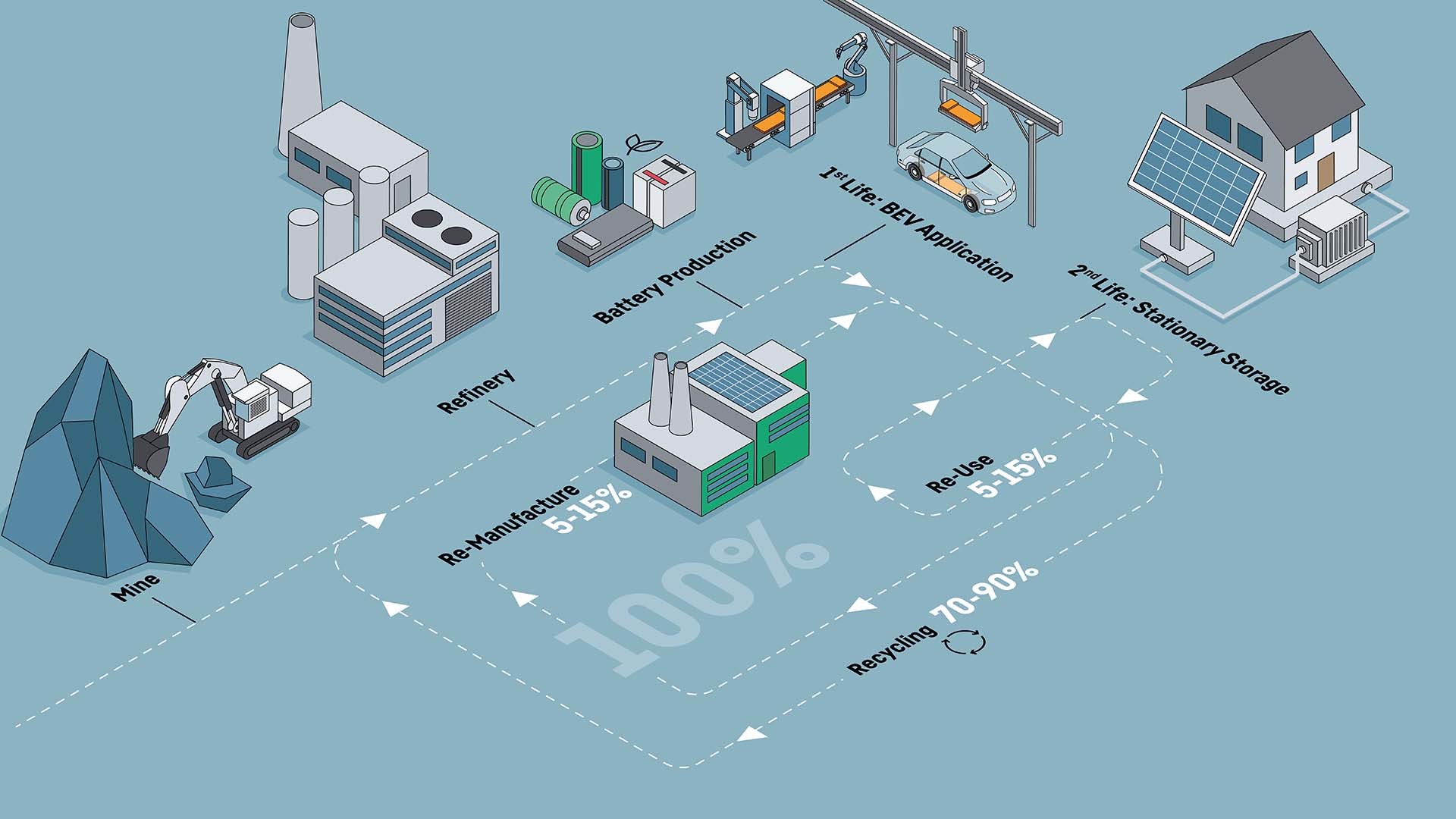
Flexible automation solutions for the automotive and recycling industries
Non-destructive disassembly of battery packs
Flexible automation solutions for the automotive and recycling industries
Non-destructive disassembly of battery packs
Flexible automation solutions for the automotive and recycling industries
Non-destructive disassembly of battery packs
Sustainability goals and increasing raw material prices are making the recycling of batteries from electric vehicles an increasingly pressing issue for the automotive industry. To recover the valuable raw materials and components from the battery packs, they must be disassembled and sorted at the end of their service life. Automated processes provide a basis for economic dismantling while minimizing the hazards to employees from high-voltage equipment. Liebherr-Verzahntechnik GmbH uses its tried and tested automation technology for this and is working with research and industry to develop scalable, flexible solutions for the automotive and recycling sectors.
The increasing number of battery-electric vehicles raises questions about their sustainability and the availability of raw materials. For economic and strategic reasons alone, securing raw materials is becoming increasingly important, and the po-litical goals are also clear, with the EU having specified higher recycling rates in the coming years for the materials used in batteries. Recycling batteries and returning raw materials to the economy thus makes an important contribution to the sus-tainability and competitiveness of German and European indus-try. The increasing number of electric vehicles and the corres-ponding political objectives mean that the recycling market will grow – and so will the demand for automation solutions.
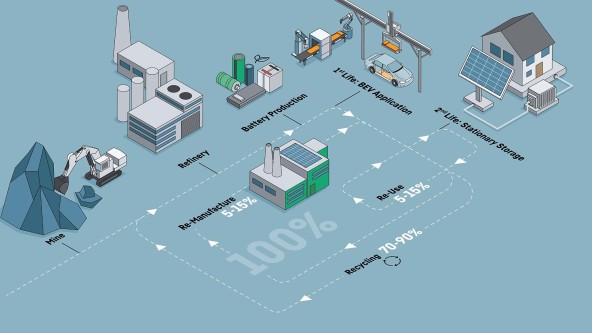
Recovering valuable raw materials
What makes the recycling of battery modules most interesting from an economical point of view is that they contain large quantities of valuable metals such as lithium, nickel, manga-nese, cobalt and copper. These metals are extracted in energy-intensive pyrometallurgical and hydrometallurgical processes from what is known as black mass, the material left over after mechanical processing of the batteries. The components of the battery pack, such as the tray, lid and cables, are dismantled and sorted – even now, usually by hand – as they also contain recyclable materials. In order to recycle batteries in large quan-tities, these processes must be automated. This means the to-pic of automated dismantling of battery systems is high on the European automotive industry‘s list of priorities. The industry is working on new products that are designed to allow automatic dismantling at the end of their life cycle.
Pilot plant for dismantling processes
As part of the ZIRKEL joint project (see box below), Liebherr-Verzahntechnik GmbH has developed a pilot plant for non-destructive battery pack disassembly, which has been operating at the research campus of Open Hybrid Lab Factory e.V. (OHLF) in Wolfsburg since November 2023. “This system is a building block in the circular economy, which will enable us to automatically dismantle battery systems in large quantities,” explains Viktor Bayrhof, Product Manager for Automation Systems. Liebherr has been a member of OHLF, which analyses the entire value chain in the circular economy, since April 2024. A subsequent project for dismantling cell-to-pack systems is also already in the works. As a public-private partnership, OHLF offers an ideal platform for developing progressive solutions for the automotive circular economy. “By jointly promoting forward-looking projects, we will develop innovative solutions for industry,” explains Techni-cal Sales Engineer Daniel Reischmann.
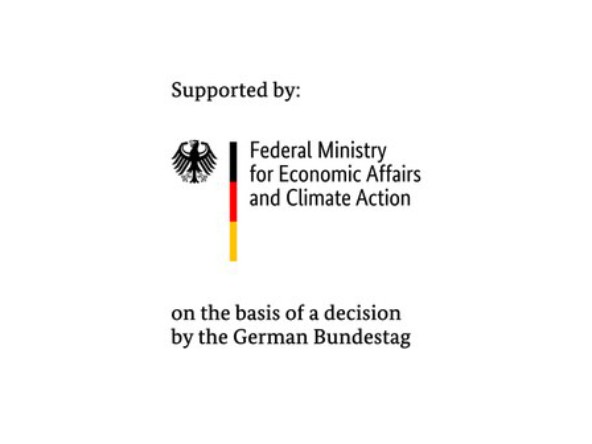
The ZIRKEL research project
Circular production for highly integrated electromobility components
This research project funded by the Federal Ministry of Education and Research is an interdisciplinary consortium of research and industry which analyzes the entire circular economy of battery systems from the electromobility sector to develop a sustainable design for recycling and disassembly in future battery production. As part of this project, Liebherr is developing strategies and processes for the automated disassembly of high-voltage battery systems and assessing the automation capability of used battery systems. The aim is to recover and recycle as many components and raw materials as possible by mechanically disassembling and sorting the components.
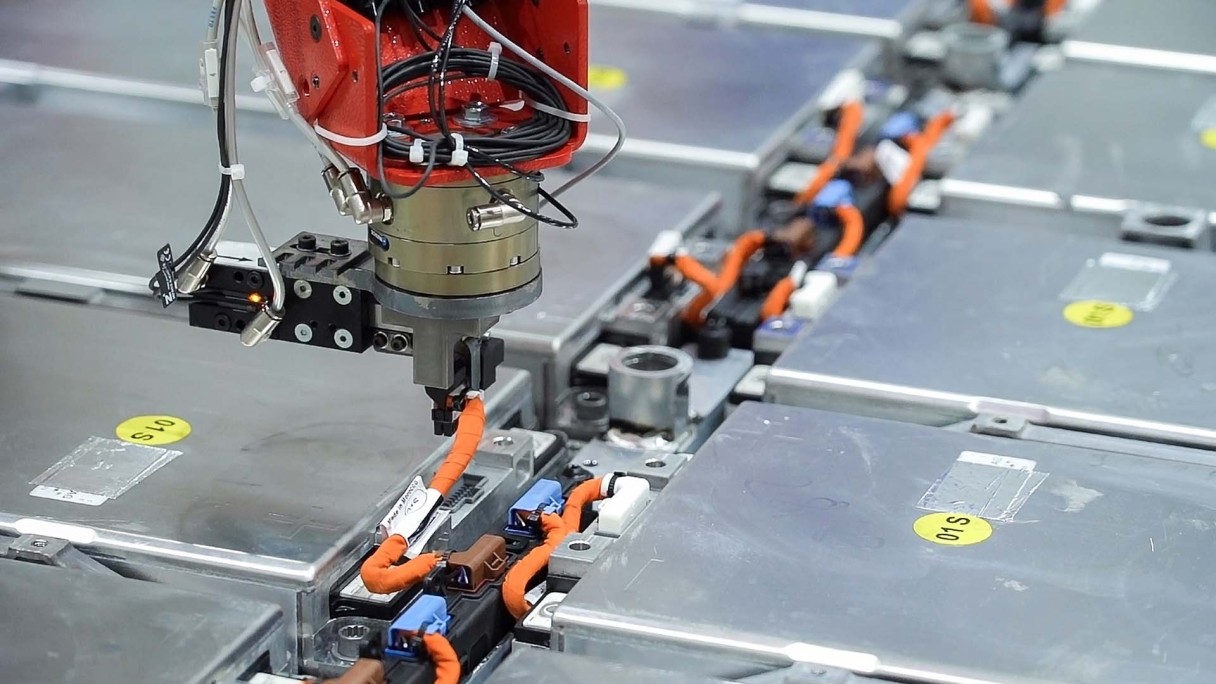
A special gripper separates the cell management controller (CMC) from the battery module by pulling out the plug.
Automated disassembly despite dirt and damage
The system automates several steps. First, a 2D camera identifies the battery pack. The lid is then opened by loosening the screws and a special gripper separates the lid from the housing. In the next step, the exact positions of the battery modules, cables, high-voltage connectors (busbars) and other electronic components are detected. In order to remove the busbars and eliminate the danger of high voltage, the system detects and removes the screws that keep them in place. It then removes the components of the battery management system, removing more screws, cutting cables and unplugging connectors. Finally, the modules are removed from the battery tray and placed in the exact order to ensure traceability. “What makes the system unique is that it can also disassemble dirty and damaged batteries,” explains Jan Pollmann, Head of Development for Automation Systems. He further emphasizes, “We are pioneers in the industry when it comes to automated dismantling of battery packs from electric vehicles.”
Scalable and flexible solutions
Liebherr-Verzahntechnik GmbH is intensely focused on these processes and is developing scalable and flexible solutions for automated disassembly. Depending on the requirements, the automation specialists from Kempten can individually configure systems ranging from individual robot cells to systems combining automated and manual operations and even entire dismantling lines. “We put together tried-and-tested system technology – in other words robots, gripping systems and software- into modules so that users can get exactly the components that they need," explains Viktor Bayrhof.
For automotive manufacturers and recycling companies
The solutions enable the Kempten-based automation specialist to cover a wide range of requirements: on the one hand, there is the highly automated large-scale dismantling of common vehicle platforms for automotive manufacturers (OEMs) – currently module-to-pack systems, which will in future be replaced by cell-to-pack battery generations. On the other hand, there are the highly varied requirements of recycling companies which manage diverse types of battery packs individually or in small batches. “We‘ve already received the first inquiries. As part of the network of research and industry, we are ideally equipped for the challenges of the future,” summarizes Daniel Reischmann.