Few topics are currently so intensely discussed as climate and the question of future-viable mobility. Stress caused by car traffic, particularly air pollution and the associated driving bans, but also noise and increasing lack of space are becoming more and more problematic, particularly in cities. There is therefore an urgent need for innovative solutions. Electric mobility is highly regarded as a promising solution approach. It is viewed as the key technology for sustainable mobility concepts. As well as e-cars and electric buses, electric mobility also encompasses the currently booming market of electrically driven bicycles. This is understandable, since the e-bike is not only environmentally friendly and space-saving, but also scores highly for its riding pleasure and health benefits. This is also reflected in the growing sales figures: almost a million e-bikes were sold in 2018 in Germany alone, with an increasing tendency.
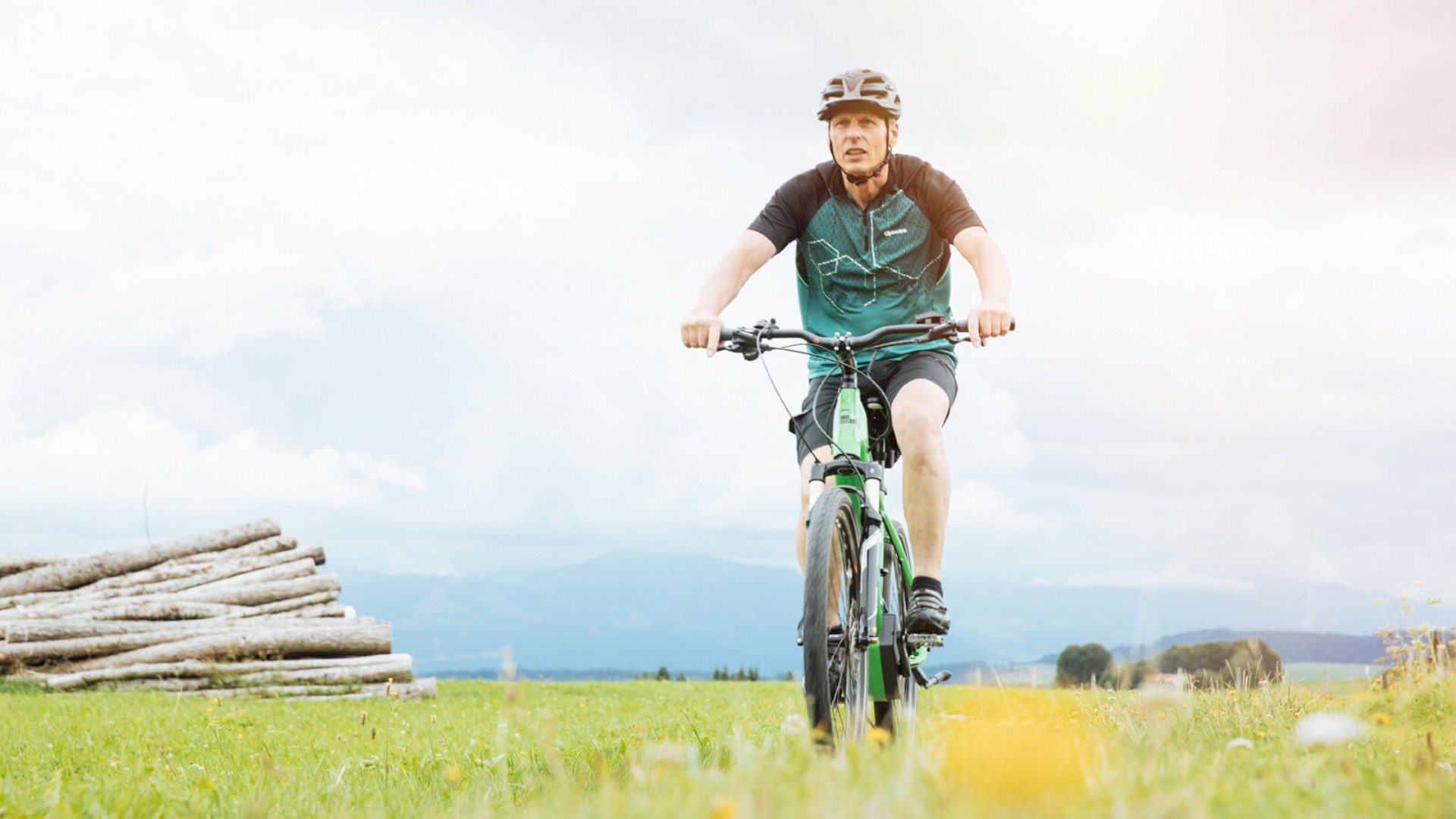
In the fast lane
For the mobility of the future, we need solutions today. Sometimes this means starting from scratch. With a new production line, new processes and new machines.
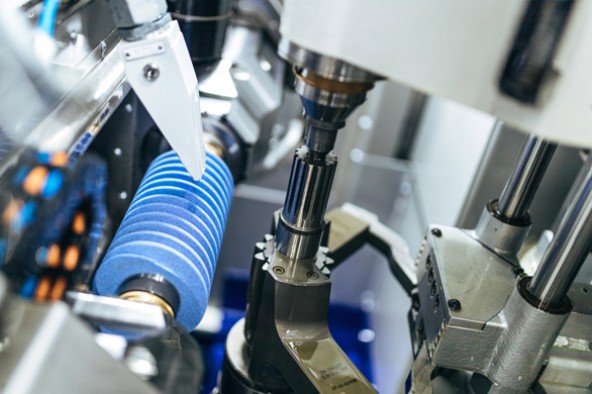
Everything new for future-viable drives
Morat Swoboda Motion GmbH is also counting on bio-electrical hybrids. The joint venture, comprising the Franz Morat Group and Swoboda, is passionately dedicated to the topic of electric mobility and develops and produces drive components for e-motive products. In 2017, the company received a nomination for a large-scale project and therefore decided to commission a new manufacturing hall in Nowa Ruda, Poland. In order to fulfil the high demands of the e-bike market, the production hall was planned and equipped completely from scratch, including all the machines and associated automation. The company recognised this future market and its potential early on. Stephan Mayer, project manager for the construction of the factory in Nowa Ruda, recalls: “We quickly decided that we wanted to construct a new factory in Nowa Ruda, directly adjacent to the already existing Franz Morat Group assembly factory. Planning of the manufacturing line began in 2017, and the ground was broken in July 2018. Our aim was to create a manufacturing hall in which to address the specific challenges of gear wheel production for e-motive drives. We wanted as much automation as possible and, above all, a machine landscape at the highest technological level”, Mayer explains. Building up a production line from A to Z has the advantage of being able to choose the right cooperation partners from the start, including for the gear cutting machines. Discussions were carried out with different providers, including Liebherr-Verzahntechnik GmbH, which installed three LC 60 gear hobbing machines and six LGG 180 generating gear grinding machines in the new plant in Nowa Ruda. The entire production is fully automated.
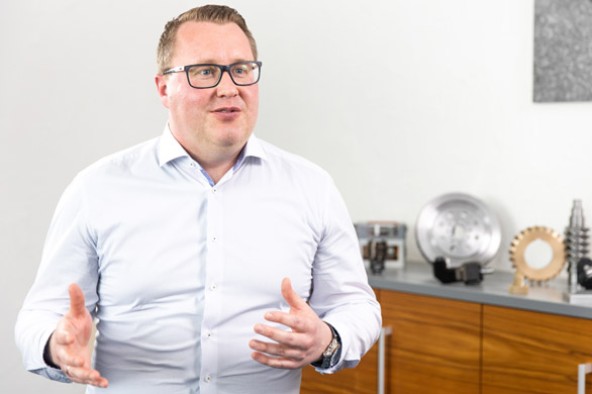
Highest demands made of gear technology
On the basis of the upcoming project, the most important requirements were defined: the basic prerequisites were high process stability, series suitability and the greatest possible efficiency by means of short machining times. But we also wanted to respond to the specific needs of the e-bike market. Because anyone who has ridden an e-bike knows that the wheel must run smoothly. So it’s not surprising that particularly high demands were made of the toothed gears. Stephan Mayer summarises: “The teeth interlock with each other, which is how the rotation of one toothed gear is transferred to the next one. The whole thing works like a clock mechanism. If the individual teeth do not lock in perfectly, the motor won’t work at all.”
With the e-bike, disturbing noises from the drive create an unnatural riding feeling. “After all, nobody likes a clattering noise that follows you around when you want to enjoy a tour through the forest”, says Mayer with a grin. “That’s why we have performed diverse modifications to the surfaces of the toothed gears and optimised the gear geometry. To do this, we worked together very closely with Liebherr’s technology application department. Together, we found a very successful method and adapted the process parameters so that the drive units produce no noise, and the e-bike rider hears a natural soundscape during the ride”, Mayer reports with satisfaction. Purchasing a total of nine Liebherr systems paid off. “The decisive factor when selecting machines was that, with Liebherr, we had a provider that covers both technologies, i.e. gear hobbing and generating grinding. We wanted a competent point of contact who would completely understand our process and deliver suitable solutions”, the 35-year-old project manager reports.
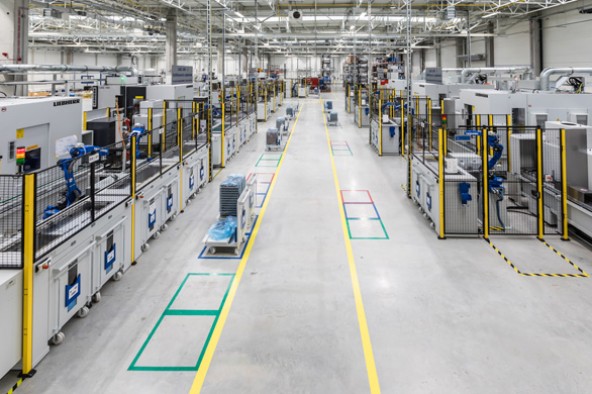
Reliable partners – in the long term
With the gear hobbing and generating gear grinding machines, Liebherr makes a significant contribution to toothed gear manufacturers’ ability to provide highest-quality components on a large scale. Quality is found not only in the machines but also in the employees: “The entire process development, up to acceptance, ran very smoothly”, Mayer explains. “We developed a lot of things jointly with the technology department. The installation and support also work flawlessly”, he adds. High value was placed on good supervision, since new staff also had to be simultaneously inducted at the new site. That makes it all the more important to have reliable contact partners. Mr Mayer is satisfied: “We are proud of what we have achieved with this project. Our results have borne us out. We aspire to be regarded as one of the main suppliers of the e-motive market. With Morat Swoboda Motion and the new production line, we are in an excellent position to fulfil future requirements.”