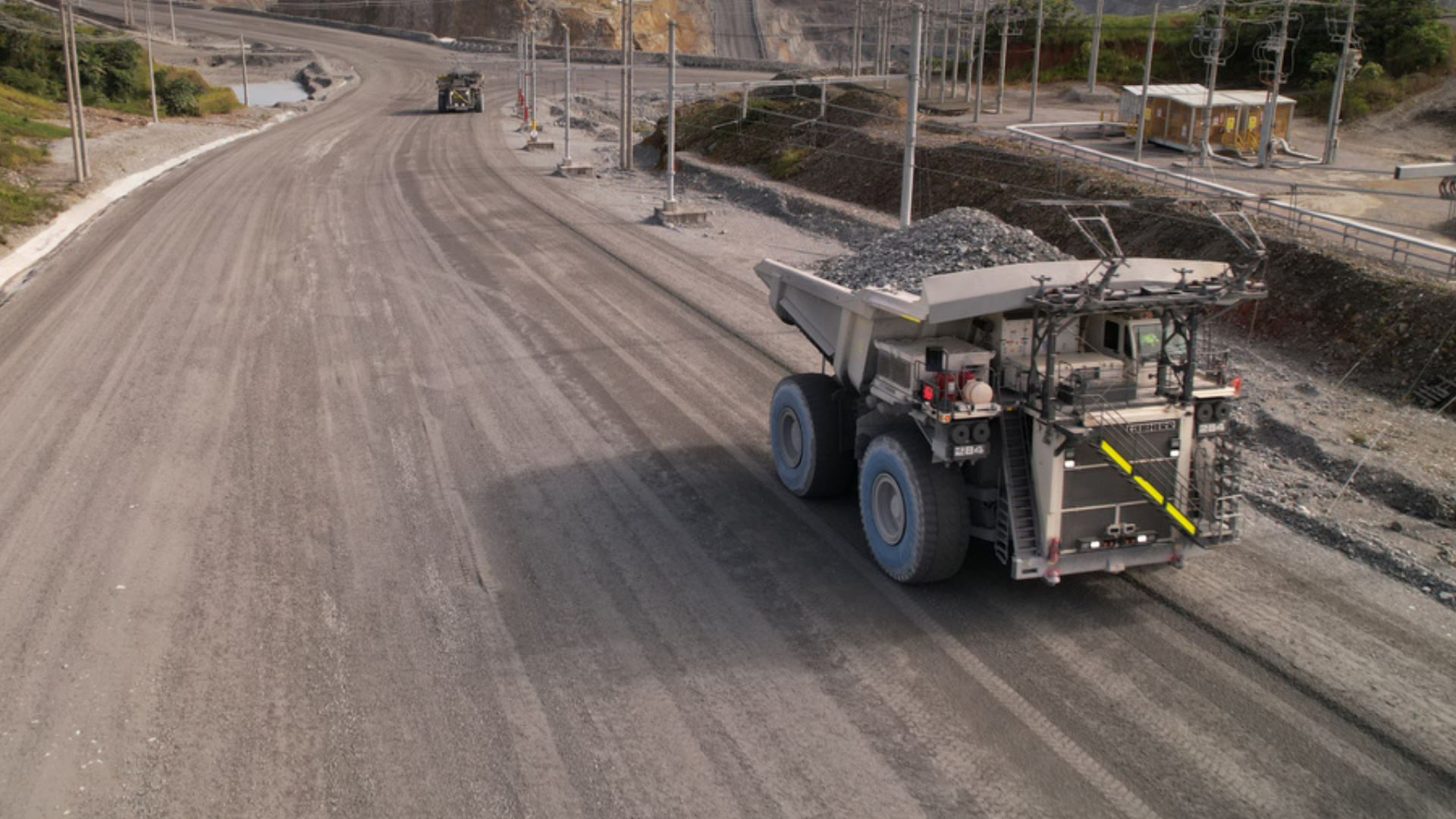
Working towards a more sustainable future
Over the past few years, the decarbonisation of mining activities has become a primary focus for the entire mining industry. In fact, the most recent mining outlook reports have stated that concerns about the environmental and social impacts of mining have eclipsed commodity prices as the sector’s primary concern. This change reflects the current attitudes of the international community. In 2015, 196 countries adopted the Paris Agreement at COP 21. The Paris Agreement is a legally binding treaty focused on climate change and the reduction of greenhouse gas (GHG) emissions. The main objective of the Paris Agreement is to cap global warming at less than 2 °C (3.6 °F), with 1.5 °C (2.7 °F) the ultimate target. Achieving this goal will require the global cooperation of both the public and private sectors.
Liebherr takes its environmental responsibilities incredibly seriously and considers contributing to the decarbonisation of the mining industry as one of its obligations as an original equipment manufacturer (OEM).
“Liebherr Mining has already embarked on our path towards decarbonisation so that we can hand over a world with a future to our children. As an OEM, we have all required competencies and it is our responsibility to push, drive, and realise decarbonisation,” said Oliver Weiss, Executive Vice President of R&D, Engineering, and Manufacturing for Liebherr Mining.
To support these efforts, Liebherr announced its , pledging to offer low GHG emission solutions for all trucks and excavators by 2022 and fossil fuel free solutions for most applications by 2030.
Liebherr is exploring many different pathways to meet its zero emission targets. These pathways include conducting investigations into future zero emission technologies, updating its equipment offerings, and partnering with major players in the industry to develop zero emission solutions for the wider mining industry. Liebherr would like to share its projects and achievements in the zero emission space with customers to demonstrate its dedication to decarbonising the mining industry.
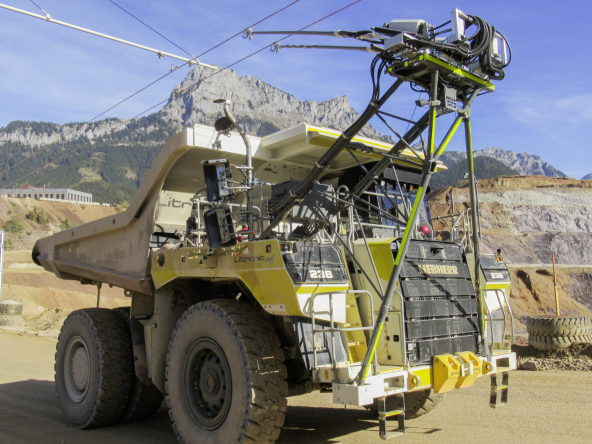
Agnostic and upgradable: The Liebherr Mining approach
To ensure the success and longevity of Liebherr’s zero emission plans, the company conducted a feasibility study to investigate the viability of a variety of zero emission technologies that could be used as complements to its mining equipment. The study, which was finalised in early 2022, examined four drivetrain technologies that represent potential relevant technologies for large mining machines: battery electrification, including trolley solutions and the ability to undertake stationary or dynamic charging; ammonia internal combustion engines; methanol internal combustion engines; and fuel cell electrification, utilising a hydrogen fuel cell/battery hybrid in a truck running on a trolley line or using dynamic charging.
The feasibility study ran simulations of these four drivetrain technologies in a number of different scenarios, including how each would work in different locations and in a range of haul profiles. Predictions for 2030 were also used in these simulations – including forecasts of alternative fuel prices provided by alternative fuel expert ENGIE – to determine the workability of the proposed technologies and their associated costs.
“Thanks to the Liebherr Zero Emission Mining feasibility study we were able to define a clear and strong zero emission strategy and roadmap,” said Dr.-Ing. Isabelle Ays, Head of Zero Emissions for Liebherr Mining. “We were able to define all zero emission projects which, if implemented, will lead us to certain success.”
The results of this study, coupled with Liebherr’s understanding of its customers and the wider mining industry, have paved the way for the beginning of a number of different zero emission mining projects within Liebherr and many of these are well underway. Each of these projects will help Liebherr to meet its target of offering zero emission mining equipment by 2030.
Tools of the trade
In recent years, Liebherr has provided updates for its range of digging, loading, and hauling products so that these machines can help customers to meet the low and zero emission technology requirements of today, while also being prepared for the zero emission technologies of the future.
Lining up for trolley power
Liebherr has offered trolley solutions for its range of mining trucks since 2016 through its Trolley Assist System. This system allows customers to power diesel-electric trucks by connecting them to overhead electric powerlines.
“We have recognised that, in the future, electricity will continue to be the cheapest alternative to today’s diesel. For this reason, every mine should try to use as much electricity as possible,” said Ays. “Dynamic charging with trolley overhead lines offers an optimal way to use electricity without interrupting the mining process. Also, future Liebherr trucks with zero emission drives will have this Trolley Assist option so that our customers can keep their energy costs as low as possible.”
Trolley solutions are usually installed on the up-grade section of a haul route as this is when the most energy is consumed by the machines. When trucks are operating under the Trolley Assist System, they can achieve higher speed on grade and faster acceleration which can in turn lead to increased productivity, decreased energy costs per tonne, and a reduced carbon footprint of the mine.
Today, Liebherr’s global fleet of trucks that operate on the Trolley Assist System exceeds 50 machines spread across Panama, Zambia, and Austria, with further units to be commissioned for a new site in South America in 2023. Customers prefer Liebherr’s mining trucks for trolley solutions because of the company’s semi-autonomous Assistance System offerings for these machines. The range consists of the Crusher Guidance System, which helps operators to reverse safely into crushers; and the Trolley Guidance System, which helps trucks to connect and disconnect from the trolley line while also helping the truck to maintain a consistent travel path.
A closer look at COP
The COP, or the Conference of Parties, is the predominant decision-making body of the United Nations Framework Convention on Climate Change, commonly referred to as the “Convention”. The primary goal of the Convention is to prevent perilous human influence and interference with the climate.
Since the Convention came into force in 1994, it has been ratified by 198 countries. These 198 countries are referred to as Parties to the Convention and each one is represented at each COP meeting. During these meetings, the COP reviews the impacts of actions taken by each Party in their efforts to meet the Convention’s primary goal and evaluate how much progress is being made. It is from these meetings that well-known international climate action treaties, such as the Kyoto Protocol of COP 3 and the Paris Agreement of COP 21, are adopted.
COP meetings take place annually, unless circumstances lead the Parties to decide otherwise. For example, COP 26 was originally due to take place in 2020, but due to the COVID-19 pandemic, it was postponed until 2021.
The next COP, COP 28, is to be held from late November to early December 2023 in the United Arab Emirates.
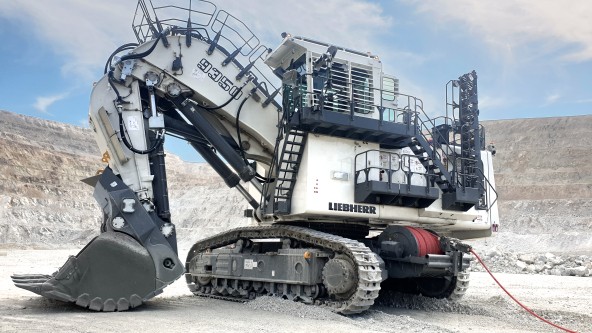
30 years of E-xperience with electric excavators
Liebherr has offered electric-drive excavators to its customers for over 30 years. Over that time, Liebherr has been able to develop electric digging solutions that can significantly reduce a customer’s GHG emissions.
“We develop our mining machines in a modular way so that we can constantly upgrade or retrofit them with alternative drives. Our excavators are no exception to this philosophy. In Australia, for example, we retrofitted an R 9400 diesel excavator produced in 2010 with an electric drivetrain, turning it into an R 9400 E,” explained Weiss.
The rate of GHG emissions reduction that customers receive from using an electric-drive excavator on site will differ depending on the characteristics of the mine site where it is being used. However, if customers are able to power their sites with electricity from renewable sources, these excavators become a zero emission solution for their mine.
As electric excavators must be connected to their power source throughout operation, ensuring the mobility of these machines was a priority for Liebherr. Thus, Liebherr leveraged its decades of experience to develop the cable reeler system for its entire range of mining excavators. The cable reeler can be integrated into the undercarriage of an excavator to provide up to 300 metres of autonomous cable reeling without reducing the machine’s ground clearance. This solution helps operators to manage the excavator’s cable while the machine is in operation, which not only improves the mobility of the machine but increases the safety of those working alongside it.
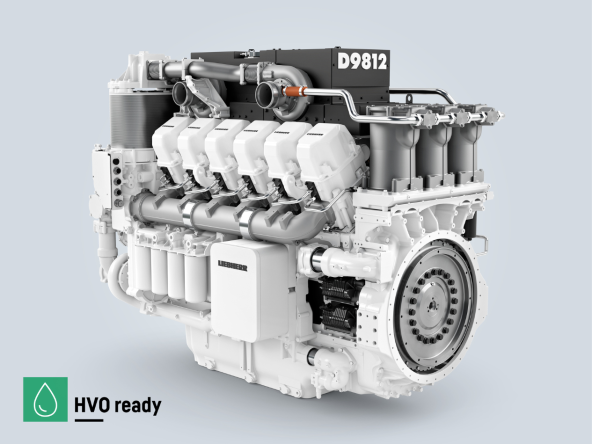
The powerhouse of mining
Liebherr’s D98 engine series is designed specifically for mining applications. With its modular design, this engine can be used in equipment produced by Liebherr and by other OEMs. When designing these engines, Liebherr took advantage of every opportunity to reduce GHG emissions. One such opportunity was including selective catalytic reduction (SCR) in the design of the D98 engine to comply with the latest emission regulations. SCR is an active emissions control system that reduces the nitrogen oxides (NOx) produced by the engine to near zero. A chemical reaction within the system converts NOx to nitrogen, water, and minute amounts of carbon dioxide (CO2) before running the transformed gases through a particulate filter and emitting them from the exhaust pipe.
Despite being originally designed as a diesel engine, the D98 series can also work with certain alternative fuels. Due to the engine’s larger volume displacement, the D98 series can use synthetic renewable fuels such as hydrotreated vegetable oil and up to 10% biodiesel. The D98 series is also being used as the basis for developing internal combustion engines that can operate using other kinds of alternative fuels, with multiple factories from within the Liebherr Group participating in different projects.
At the Bauma 2022 exhibition, Liebherr demonstrated its expertise in hydrogen engines by winning the in the climate protection category for its first hydrogen-powered excavator, powered by Liebherr’s H966 hydrogen engine. Liebherr began developing hydrogen combustion engines in 2019 and now, following the H966 engine’s success at Bauma, Liebherr is further exploring the capabilities of these engines with ammonia. Testing this fuel source in an internal combustion engine is expected in early 2023.
Partners in success
Liebherr has also entered strategic partnerships with customers and industry experts alike to explore options for the development of zero emission solutions that can be offered to customers in the future.
Fortescue Metals Group
Liebherr's with Fortescue Metals Group (FMG) was announced in June 2022. The collaboration between these two companies will focus on the delivery of zero emission mining trucks to the wider mining industry. Liebherr will work closely with two FMG businesses – Fortescue Future Industries and WAE – to install battery technology into the T 264 mining truck.
“This project provides us with an excellent opportunity to accelerate the integration of alternative drive systems into our mining equipment, supporting our vision and strategy to offer zero emission machines with the most suitable drive technologies in the future. Along the way, we will support our customers in choosing technology options from our wide range of products that are most suitable to them,” said Weiss.
The process of integrating these zero emission technologies into the T 264 will take approximately two years, with supply of these fossil fuel free machines commencing once the development phase had concluded.
Trolley solutions
Over the past few years, Liebherr has partnered with a number of trolley service and infrastructure suppliers to be able to offer customers the best possible trolley solutions for their specific site requirements. Working with a variety of suppliers has helped Liebherr to provide customers with the best performance option for their sites at the lowest cost. The first trolley system defined through the collaboration between customer, Liebherr Mining, and trolley service and infrastructure suppliers will be deployed in 2024, to a customer in South America.
“Liebherr has, and will continue to build up, know-how for dynamic and stationary charging. Our application engineers use specific simulation software to identify the optimal trolley system design for each customer. All elements – such as potential locations to place trolley line hardware, length of lines, ramp design, and other important elements – will be looked at to optimise cost, maximise production, and minimise total emissions. This information results in clear recommendations for the best trolley system, based customers’ mine layouts,” said Weiss.
Weiss is also aware of the challenges that customers can face when including zero emission technologies in their mining practices.
“Zero emission technology is new to our customers and can require some adjustments on their part. But if this technology is used correctly, emissions will be reduced while optimising both energy consumption and total cost of ownership,” said Weiss.
“As we convert our products to zero emission, we will offer our customers additional advisory services. These services aim to assist our customers by providing specific know-how so that they can make the best use of Liebherr’s mining solutions and get the maximum performance out of their machines. As a result, customers’ mining processes and performance will be improved through optimal use of our technology products,” Weiss continued.
ENGIE
At MINExpo 2021, to research different pathways to fossil fuel free mining solutions. Specifically, the two companies have been evaluating the workability of different renewable energies – with a focus on hydrogen and hydrogen-derived fuels such as ammonia – to be used in well-to-wheel solutions for the mining industry.
Part of this collaborative effort involved ENGIE supporting Liebherr during its feasibility study investigating the most effective zero emission technologies for mining equipment. The information gained from this study has been crucial as Liebherr works towards offering zero emission mining solutions by 2030.
“We have teamed up with ENGIE so we can work together to reduce our customers’ risks when investing in zero emission mining equipment. Liebherr Mining can guarantee the performance of our machines while ENGIE guarantees the availability of the fuel,” said Weiss. “With the support of both companies, customers can be sure that they have a full solution as well as transparency about the well-to-wheel emissions and energy costs associated with their chosen solution for reaching their zero emission targets.”
Meeting Paris objectives
The Paris Agreement of 2015 was the first time that Parties to the Convention agreed to take ambitious steps to both combat climate change and to adapt to the effects of a warming world. To do this, Parties are expected to submit their nationally determined contributions (NDCs) to the Coalition of Parties (COP) every five years. These NDCs encompass the Parties’ goals, policies, and proposals for reducing greenhouse gas (GHG) emissions and for adapting to the current effects of climate change.
For international efforts to continue to be impactful, Parties must present more ambitious NDCs every five years to ensure continued progression towards the ultimate goals of the Paris Agreement. Each of the Parties’ NDCs are documented in a registry that is maintained by UN Climate Change.
Since the Paris Agreement came into effect, zero emission solutions have become competitive in a range of sectors that collectively represent 25% of global GHG emissions.
Looking ahead
“Our series of zero emission mining projects contribute to different layers of our decarbonisation approach, including consulting, development, deployment, and support. Our goal is to provide a Liebherr zero emission mining solution, thereby simplifying the transition process for our customers while facilitating their progression to zero emission mining,” explained Ays.
When discussing the future of Liebherr’s zero emission solutions, Weiss reflected on how Liebherr’s current technology offerings can help customers both now and in the future.
“The energy and powertrain agnostic approach of the Liebherr Group, combined with all Liebherr in-house core competencies and the significant level of vertical integration in our mining products, enables us to identify and realise the best solutions for open-pit mining machines. The combination of today’s proven low and zero emission products with our zero emission mining development roadmap for future solutions, makes us very confident that we will meet the requirements of our customers,” said Weiss.