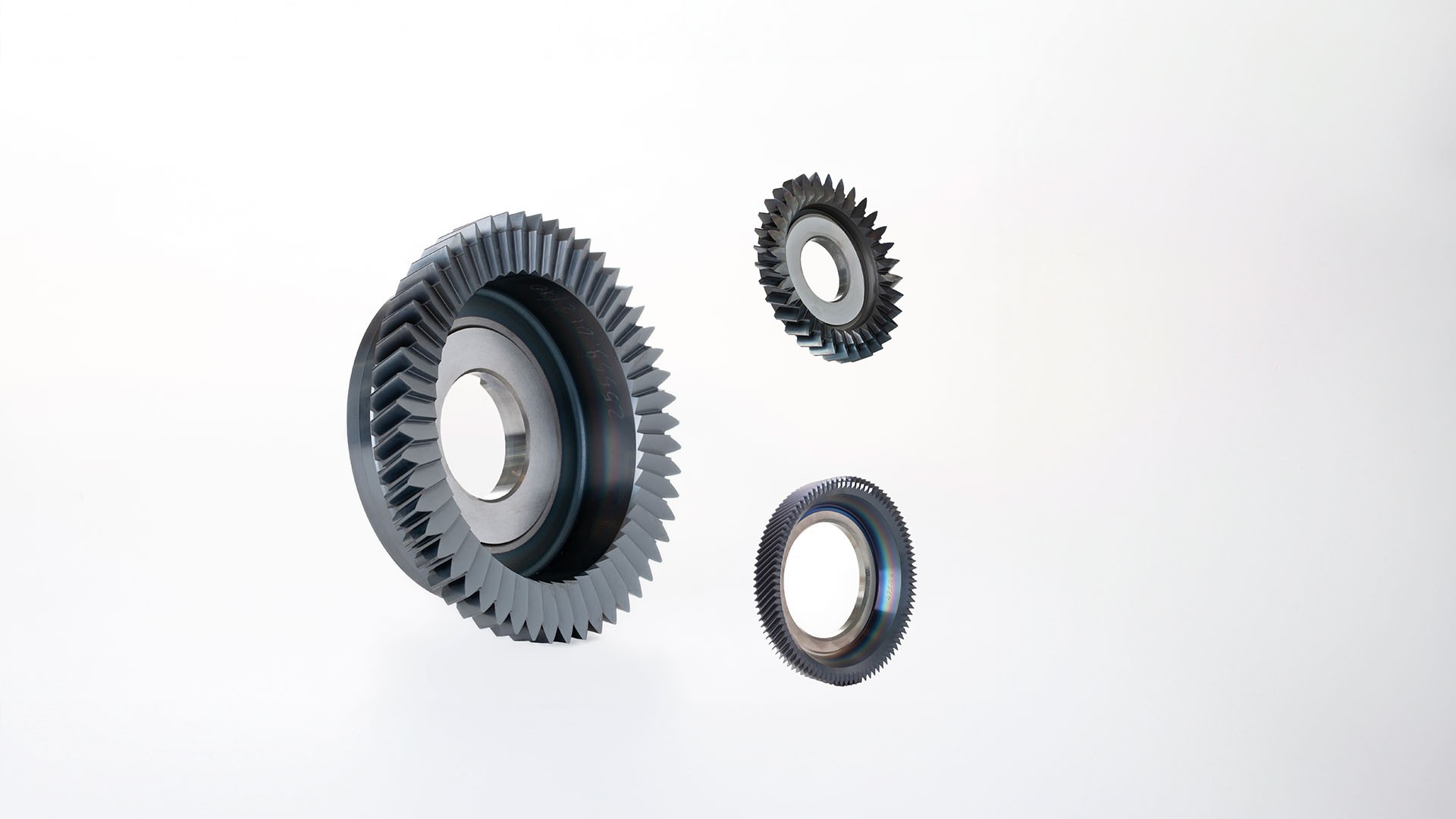
From “Plug & Pray” to “Plug & Play”
Gear skiving used to be a gear cutting method that was difficult to control due to its complex kinematics, but it now offers a genuine alternative to shaping or broaching. The synergy between machines, tools and processes provided by Liebherr-Verzahntechnik GmbH’s Skiving³ technology package makes it possible to efficiently and flexibly machine an extremely wide variety of workpieces, including in small batch sizes. Skiving³ therefore crucially boosts productivity, quality and cost-effectiveness levels not just in series production, but in contract gear manufacturing as well.
Gear skiving: productive and cost-effective
Liebherr-Verzahntechnik GmbH is a pioneer in this sector and offers users the expertise they require through the Skiving³ technology package (“Cubic Skiving”). After all, successful gear skiving is built on the synergy between machines, tools and processes. The company is also increasingly turning to gear skiving instead of shaping in its own contract manufacturing work, such as spline, or mating gear production applications. “As a result of skiving, our manufacturing rates are much faster and we are providing a higher standard of quality and deliverability while also boosting output and reducing prices,” reports Marcel Sobczyk, a gear cutting tool applications expert at Liebherr-Verzahntechnik.
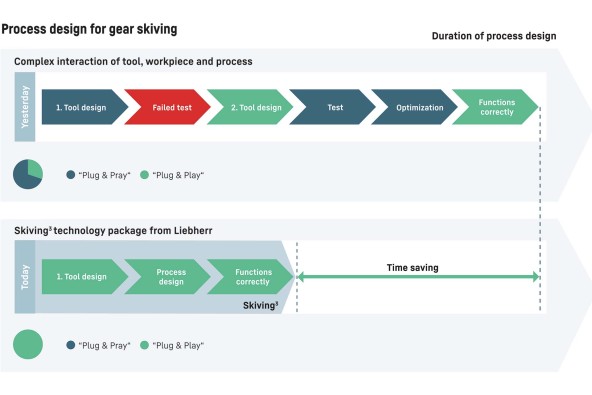
Series production and small batch sizes
Up until now, gear skiving was mainly limited to series production. However, Skiving³ is making it compatible with small batch sizes and a wider variety of parts. The technology package is making it possible to reliably manufacture a variety of gears in different batch sizes. Using simulations carried out early on in the process and tool design phase and automatic corrections, the right parameter values can be set so that the very first part is manufactured correctly and the process runs smoothly, virtually “at the touch of a button.”
This technology is therefore proving successful in e-mobility, where speed, precision and productivity are of the essence. However, Skiving³ also offers clear advantages for small series, as demonstrated by Liebherr’s own contract gear manufacturing. “Only a few run-in parts are required to start the process and deliver quality,” explains Sobczyk. This really benefits job shops and users who machine different workpieces and manufacture medium batch sizes or small series with just 20 to 30 parts.
Skiving³ is the key to successful gear skiving
Service is also a priority: “We are not simply a supplier. We provide assistance to our customers on all matters as a skilled partner. This is particularly vital for job shops,” explains Marcel Sobczyk. Haider Arroum concludes: “With Skiving³, we have drastically simplified gear skiving. Having shifted from ‘Plug & Pray’ to ‘Plug & Play’, it’s now simple and practical even for smaller batch sizes!”