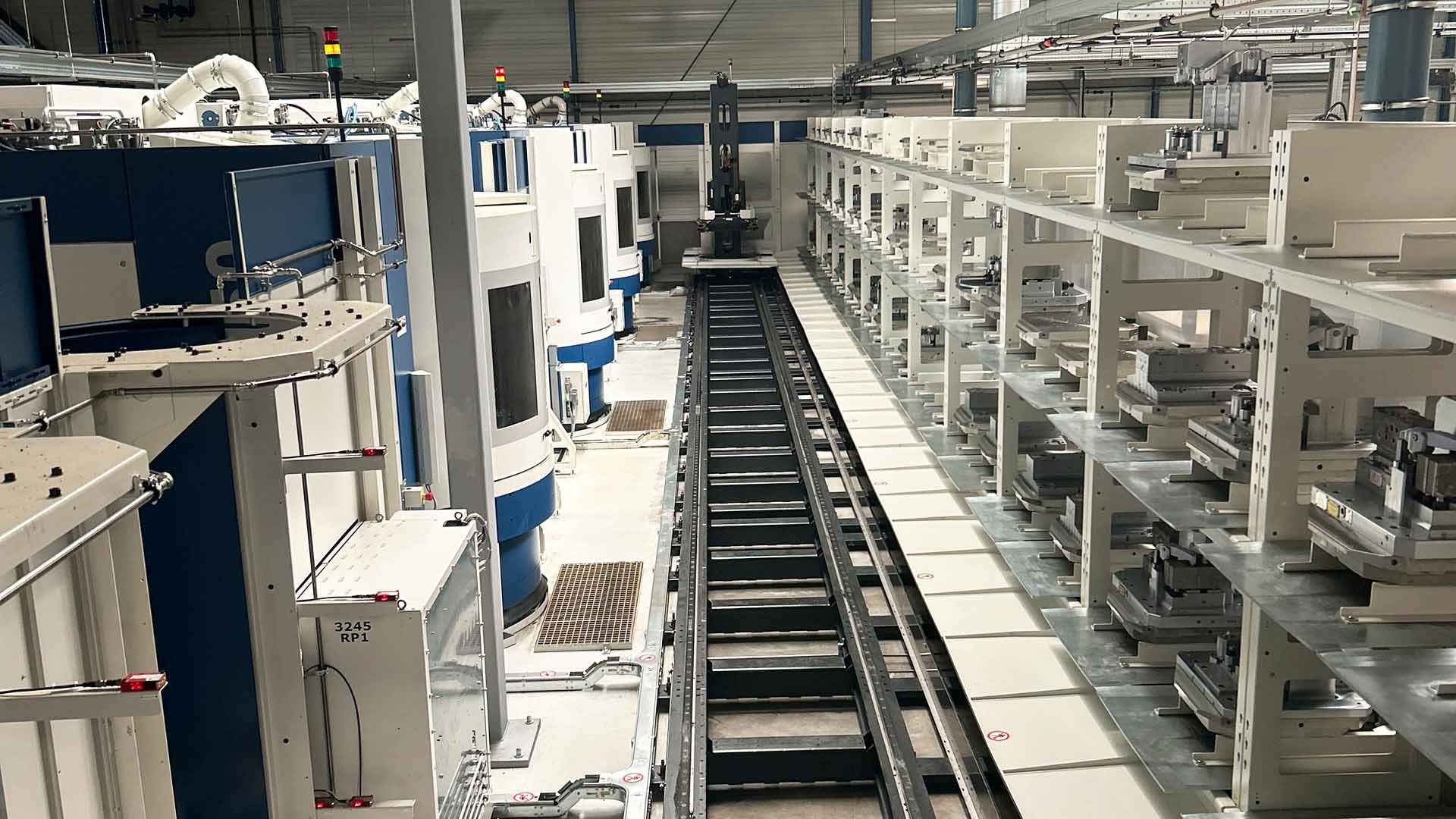
Modern pallet handling in historic halls
For the manufacturing of valves and valve kits, Linde Hydraulics GmbH & Co. KG invested in a production plant at the Ballenstedt site with five 5-axis machining centers from Grob, which are interlinked via the PHS 1500 Allround pallet handling system from Liebherr-Verzahntechnik GmbH. This enabled the company to increase the output of this manufacturing line by 30%. The planning was quite a challenge: due to the high demand, not only did additional machines have to be integrated, but an alternative location for the plant in the historic production halls also had to be found during the project.
As part of its strategy of site security and competitiveness, Linde Hydraulics GmbH & Co. KG decided to invest in the modernization and expansion of the site at Ballenstedt. Valves and valve kits for mobile hydraulic applications are manufactured at this site and production takes place in former farm buildings around the residential palace. In order to increase the production volume of control valves for mobile excavators, two new 5-axis machining centers from Grob were originally planned to be purchased and linked to a linear storage system. The choice of Liebherr-Verzahntechnik GmbH was an obvious one: two PHS Pro pallet handling systems were already being successfully used in combination with Grob machines at Linde Hydraulics’ Aschaffenburg site.
Plan changes during the project
However, due to a rapid increase in demand, the plan for Ballenstedt was “completely overhauled during the project period,” explains Heiko Reckziegel, Head of Industrial Engineering at Linde Hydraulics in Ballenstedt. Additional 5-axis machining centers had to be purchased and linked accordingly, and this meant that the originally planned location would not be sufficient. In order to be able to set up the system with linear storage automation with a total length of 30 m, the search for a suitable location began all over again. “The issue with space was very challenging due to the individual structures of our location,” explains Reckziegel. In the end, the only suitable space was identified in the neighboring hall – but an existing facility had to make way for it. Tailor-made solutions were required to adapt to the new conditions.
Linde Hydraulics GmbH & Co. KG
Sector:
Hydraulic technology
Company headquarters:
Aschaffenburg (D)
Employees:
approx. 1,400 employees
Founded:
1904
Website:
lhy.com
5-axis machining of control valves
Various families of parts are manufactured on the system, but it is a control block for mobile excavators that is particularly high in demand: it is “a highly complex component with five functional axes for controlling the excavator,” explains Reckziegel. Machining is just as complex: the parts have a raw weight of 115 kg, after machining on the G552 5-axis machining centers from Grob this weight is reduced to around 90 kg. In addition to these “large” control blocks, housings are manufactured for medium-pressure control valves that control the function of the lift mast in forklift trucks.
PHS 1500 Allround with pallet changing system and variable clamping pressures
The PHS 1500 Allround from Liebherr-Verzahntechnik GmbH manages the parts. The modular system essentially consists of a linear storage system, a movable lift module with a single loader that transports the workpieces into the machines, and two setup stations. Three shelf levels offer space for 70 work-piece pallets. A pallet changing system ensures even greater efficiency, allowing workpieces to be removed from the machine’s work area more quickly. A master computer from Procam not only controls the distribution and loading of the machines, but also sets the parameters for automatic workpiece clamping with variable clamping pressures using proportional valve technology. “This is not insignificant, as the weight of the workpieces changes significantly during machining,” explains Knut Jendrok, Head of Sales Pallet Hand-ling Systems at Liebherr-Verzahntechnik GmbH.
“The collaboration was more than just a customer-supplier relationship – it was a partnership of equals.”
Higher quantities, shorter throughput times
Heiko Reckziegel has been very satisfied with the per-formance of the system: “The throughput time for the large control block has been reduced by 40%, which significantly increases the quantity for this family of parts. With the new system, we are now able to meet the increased customer demand from 200 to 300 MD control valves per day.” In addition to the 30% increase in productivity, the partially unmanned operation ensures higher system availability. The linear storage system allows a complete shift to be run unmanned. In the future, the machines will also be able to run unmanned at weekends, thanks to the fully stocked shelf positions in the linear storage system. The aim is to operate the system 24/7. Another plus point of the facility is its cleanliness. Even in the machining centers, swivel rotary tables ensure clean chips and cooling lubricant removal. The oil drip tray integrated in the lift module of the PHS 1500 Allround supports this as well. This was not an insignificant aspect, as the site directly borders a nature reserve.
Synergy effects ensured a smooth process
The fact that the project ran so smoothly despite the planning changes is attributed to the well-coordinated and experienced supplier team at Linde Hydraulics. “Time was a real issue, so we couldn’t afford delays or teething troubles. However, based on our experience at the Aschaffenburg plant, we had full confidence in the project partners,” explains Reckziegel. Liebherr also benefited from the synergy effects of the previous projects: “The pre-acceptance and commissioning of the system was extremely efficient because we already knew exactly what the requirements and expectations were,” reports Christopher Nigg, Project Manager at Liebherr-Verzahntechnik GmbH.
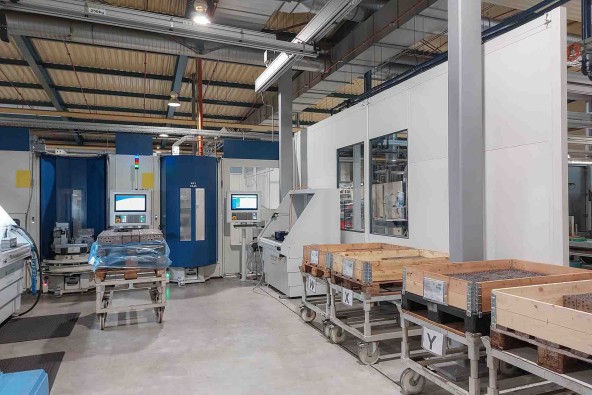
Genuine partnership on an equal footing
Heiko Reckziegel has been impressed with the good cooperation and the corporate culture of the companies involved. “I find Liebherr to be a reliable and extremely committed partner, and this includes after-sales service. The collaboration was more than just a customer-supplier relationship – it was a partnership of equals. This project has set a precedent,” he praises.