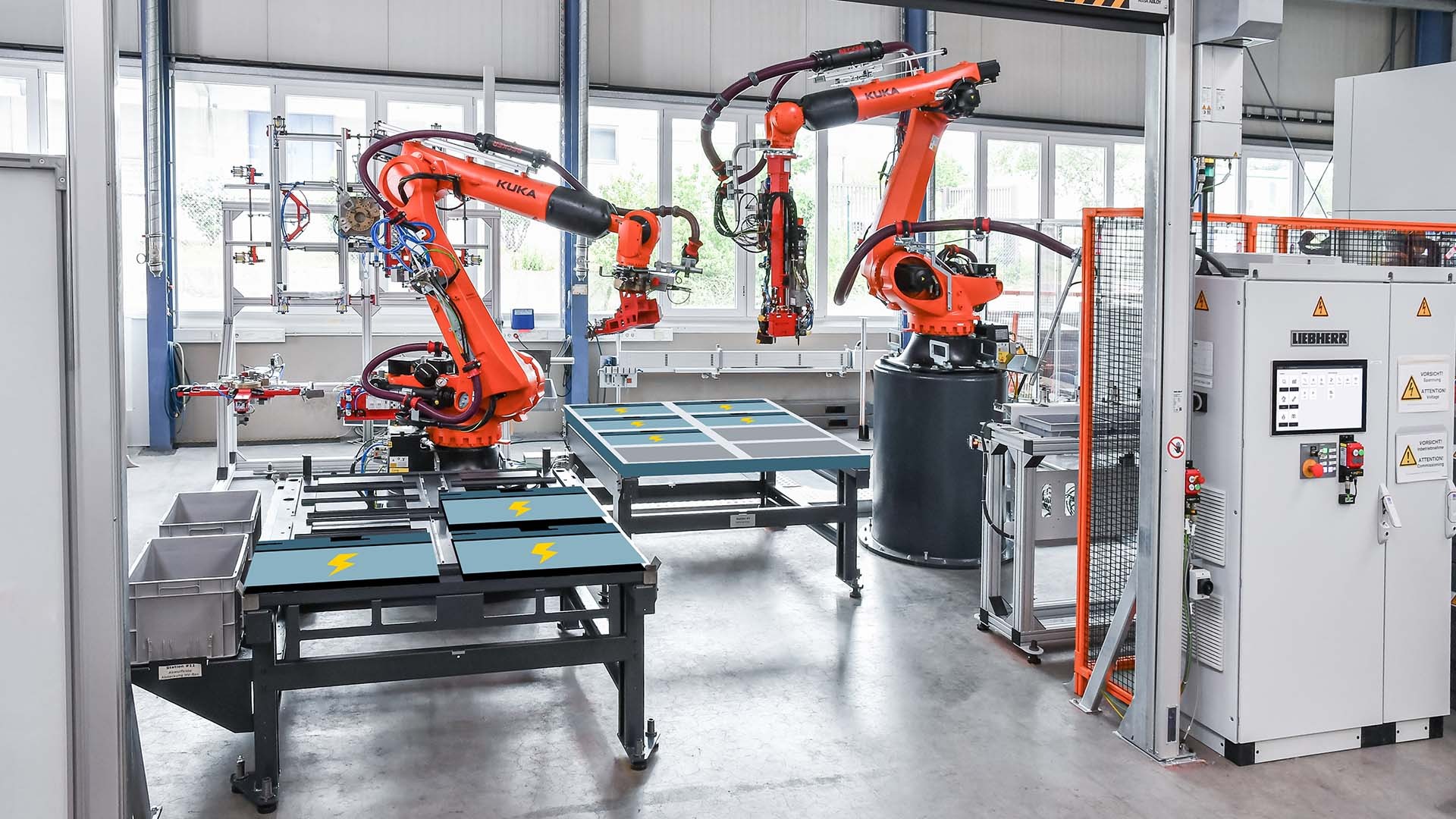
Liebherr automates disassembly of high-voltage battery systems
The increasing prevalence of battery-electric vehicles leads to questions about the environmental footprint of vehicle batteries, but also about the safety and availability of raw materials and therefore the competitiveness of the German and European industry. In this context, local battery recycling and the recycling of raw materials is an important building block for the European circular economy. In 2030, the batteries of an estimated four million electric vehicles could reach the end of their useful life. The lithium-ion batteries contain valuable raw materials, and recycling them makes both ecological and economic sense. Regardless of whether battery parts are to be reused or recycled, the disassembly of the battery systems is the first step required in all common process routes. Up to now, however, the disassembly of the battery system has been complex and expensive as the separation of the components is usually done manually. To combat this, Liebherr-Verzahntechnik GmbH is developing strategies and processes for the automated disassembly of high-voltage battery systems and is a partner in the research project "ZIRKEL", funded by the German Federal Ministry of Research and Education (BMBF), which explores the entire circular economy of traction batteries.
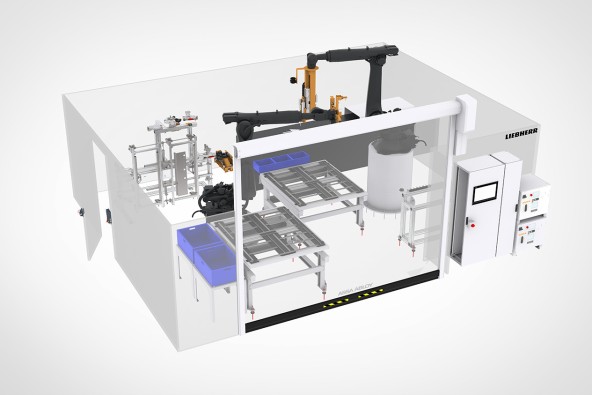
3D layout of the partially automated prototypes process station
As they increase in age, degradation processes occur in lithium ion batteries. These processes can lead to a significant reduction in range depending on the battery and vehicle. Most vehicle manufacturers guarantee a service life of at least eight years or 160,000 kilometers with more than 70 percent of the original storage capacity (state-of-health). Some vehicle manufacturers are now even increasing these guarantees. Current studies and long-term tests show that the net capacity after the guarantee period is usually well above the values specified by the manufacturer. Vehicles with a reduced range can still be used for a long time even after the guarantee period has expired. Eventually, however, after a certain number of charging cycles depending on use, lithium-ion batteries will reach a state in which they no longer meet the requirements of the car. The majority of these batteries are recycled and the raw materials are returned to the material cycle for the production of new batteries. Depending on their condition, some of the old batteries could be eligible for reprocessing and reuse in battery-electric vehicles (remanufacturing) or in second-life applications such as stationary battery storage systems. When they have finally reached the end of their useful life, the new EU Battery Regulation stipulates recycling quotas and minimum quantities of reused raw materials in new production. The industry must find the most efficient solutions possible for returning them to the material cycle, especially since the volumes of batteries returned will increase significantly in the future. The aim is to achieve a sustainable, CO₂-neutral battery production along the entire process chain with unlimited reuse of materials in a closed product life cycle. This is intended to minimize waste products and dependence on important primary materials.
High recycling rates through automation
Due to the relatively low quantities and large number of variants from diverse manufacturers and product generations, many disassembly and remanufacturing processes still take place manually today. "We are almost talking about a batch size of one in the return flow of battery packs," explains Jan Pollmann, development engineer for automation systems at Liebherr-Verzahntechnik GmbH. In order to achieve a high recycling rate and to be able to process the increasing return volumes economically, it is necessary to automate the processes. Another aspect is occupational health and safety: automated disassembly ensures the health and safety of employees and excludes their exposure to high voltage, hazardous substances or fire risks.
Liebherr develops automated disassembly processes for high-voltage battery systems
The "ZIRKEL" research project, funded by the BMBF, brings together an interdisciplinary consortium from research and industry to explore the entire recycling circular economy of battery systems from the electromobility sector. As part of this project, Liebherr is developing strategies and processes for the automated disassembly of high-voltage battery systems and testing the automation capability of used battery systems. The aim is to recover and recycle the highest possible proportion of raw materials by mechanically disassembling and sorting the components. By removing valuable components or those containing pollutants at an early stage, the cost- and energy-intensive pyrometallurgical and hydrometallurgical processing of the black mass, i.e. the raw material mixture that remains after mechanical processing of the batteries, is reduced.
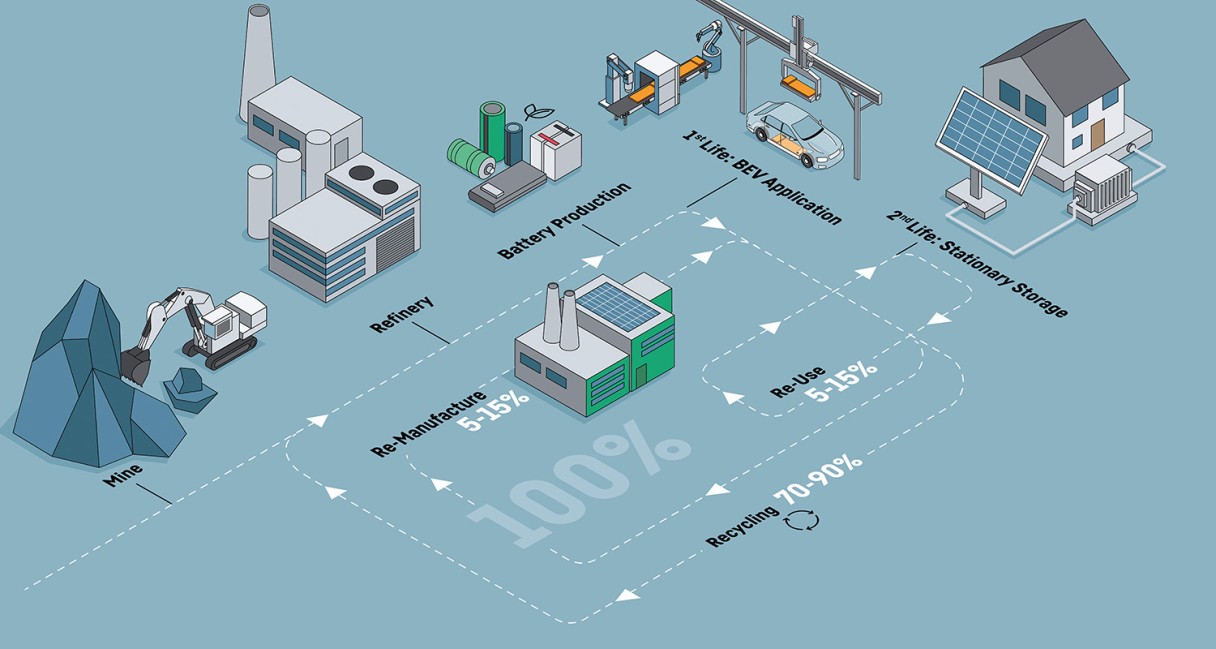
Life cycle, second life applications, remanufacturing, and recycling of high-voltage battery systems
Automation challenges
In addition to the wide variety of batteries, a number of other challenges exist for an automated disassembly process: used battery systems can be corroded, deformed or damaged. Contaminated components are sometimes difficult for vision systems to detect. Sealants and adhesives or heat-conducting pastes may be difficult or impossible to remove without leaving residues. Risks such as high voltage or hazardous substances must be taken into account. And finally, the disassembly of flexible parts such as cables or cooling hoses is difficult to automate. "In principle, the established assembly process runs in reverse here, but it is many times more complex," explains Viktor Bayrhof, Product Manager for Automation Systems at Liebherr-Verzahntechnik GmbH.
We are pleased to be able to contribute our process expertise in the field of automation to this future-oriented project
Pilot plant for the “ZIRKEL” joint project
Liebherr's first pilot plant for the disassembly of high-voltage battery systems will be installed at the Open Hybrid LabFactory research campus in Wolfsburg in November 2023. Liebherr will continue to support the project there and carry out further test series. The results and experience gained from the project will help to make the design of battery systems more suitable for dismantling and recycling. “We are pleased to be able to contribute our process expertise in the field of automation to this future-oriented project,” explains Jan Pollmann.