Machine concept
Increased efficiency thanks to gear skiving
Gear manufacturers are seeking alternative processes that are more productive and cost-effective than the gear shaping method and more flexible than broaching.
Successful gear skiving by means of:
- Machine
- Tool
- Process
The foundation for successful gear skiving is the rigidity of the machine: The cast iron machine bed absorbs the occurring process forces. In the machining head, a high spindle rigidity is achieved by means of a special bearing concept, which means that longer tool holders can also be used. This is particularly important for machining internal gears.
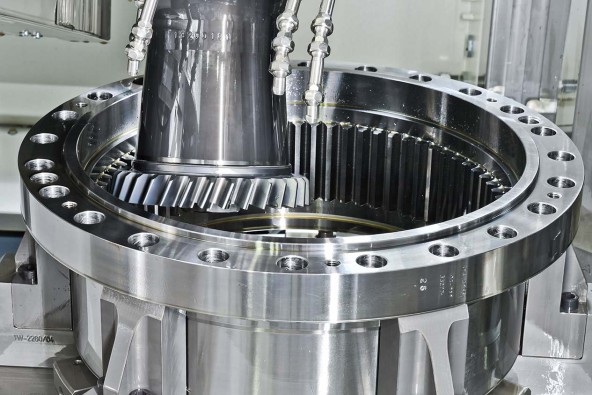
In combination with a burst-proof housing, the machine is suitable for both dry and wet machining with oil or emulsion.
In addition to the machine, the appropriate tool is crucial for a stable process. Our in-house tool development and manufacturing enables us to design the optimal tool for every workpiece assuming that the theory of skiving has been absorbed and understood.
The planned process must be taken into account when designing tools. Our intensive technological development and extensive tests on customer projects have given us a complete understanding of gear skiving and, with Skiving³, we offer a complete solution consisting of machine, tool and process.
The tailstock makes the machine suitable not only for external and internal gears but also for shafts.
Advantages of Skiving³
Machine
- Rigid machine design
- Ringloader concept for fast workpiece change
- Tailstock for shaft machining and optimum workpiece clamping
- Optional chamfering during the machining process
Tool
- Design and manufacturing of conical and cylindrical skiving wheels
- Process-optimized tool design
- Tools in PM-HSS & carbide versions
Process
- Process analysis and simulation for optimal cutting conditions
- Application technology for optimal customer support
- Collision analysis with calculation software
Technical data
Variants | LK 300 | LK 500 | LK 300 DC | LK 500 DC |
---|
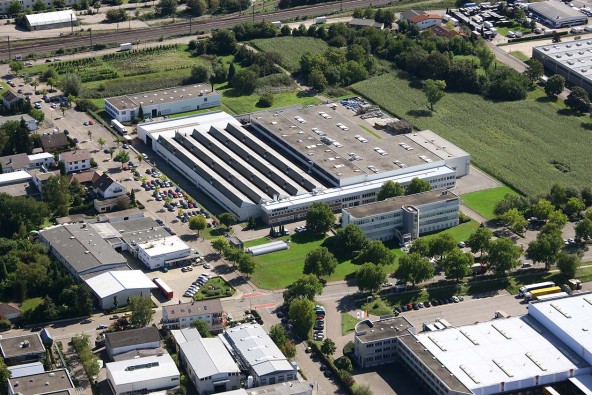
Liebherrs in-house tool production
Liebherr offers a comprehensive range of gear cutting tools, many years of experience in gear manufacturing, and the highest level of product quality down to the smallest detail. Our gear skiving tools are manufactured at our sites in Ettlingen, Germany and Collegno, Italy.