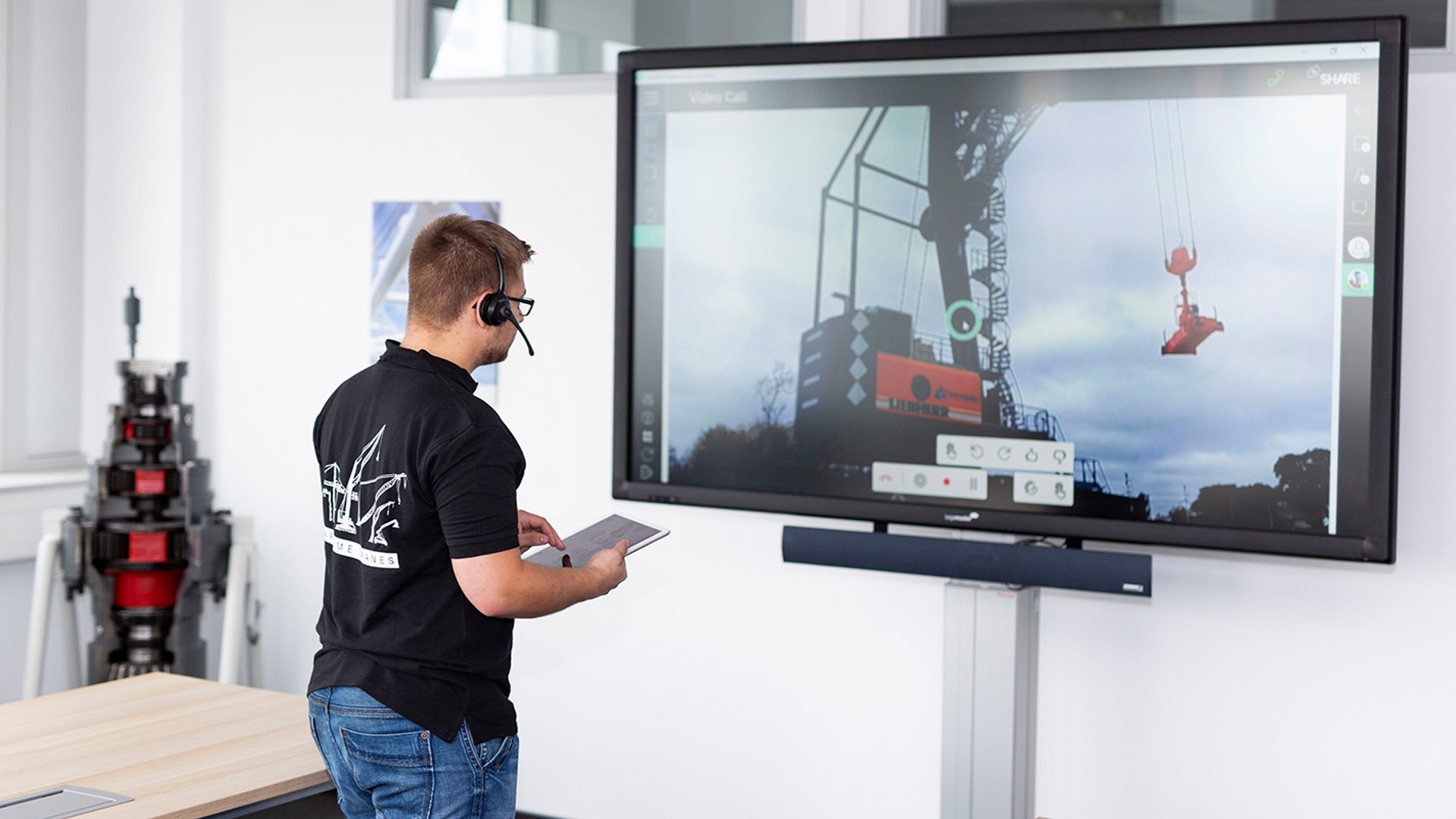
5 minutes reading time
New digital ways forward
Since the COVID-19 pandemic has made travel impossible, it's time to look for ingenious new ways forward. Nils Liesner, a service engineer for Liebherr-MCCtec Rostock GmbH, would normally be sent on site for the initial assembly of a mobile harbour crane. Instead, in May 2020, he supervised the assembly of a mobile harbour crane in Argentina from Germany, using the Remote Service tool for the first time.
Unusual circumstances for commissioning
The assembly of the LHM 420 mobile harbour crane for Euroamerica in Campana, Argentina, was marked by two firsts: not only was it the first crane of its type in this South American country, it was also the first mobile harbour crane to be assembled with the help of Liebherr's new Remote Service tool. This required detailed advance planning and the help of innovative thinkers. In this interview, Nils Liesner and his colleagues, Tony Johann, technical consultant for mobile harbour cranes, and Christian Lübke, customer service manager for Liebherr-MCCtec Rostock GmbH, report on the first remote commissioning completed during the COVID-19 crisis.
What is the normal assembly process for mobile harbour cranes, and how did the COVID-19 pandemic impact your original plans?
Tony Johann: We delivered the disassembled parts for the mobile harbour crane to Campana, Argentina, in May 2020. Under normal circumstances, two assembly mechanics would have travelled there from Rostock in order to supervise the unloading of the crane parts, and to complete the assembly in collaboration with our colleagues from Liebherr Argentina S.A., the local service agency, before delivering the operational crane to our clients in June 2020. The CODIV-19 crisis has made travel to Argentina impossible, so we needed a different solution. That's why we decided that our Argentinian colleagues Alan Irazoqui und Cristian Bovino would undertake the assembly on their own, for the first time, while we provided support and guidance remotely.
Nils Liesner: At first, many of our colleagues were very skeptical as to whether a remote commissioning process would work. I also had doubts when asked if I, in my role as service engineer, would coordinate the operation using the Remote Service tool. In the end, we had nothing to lose so we gave it a try. After all, the only other alternative was to let the crane remain disassembled for an indefinite period of time, until we could once again travel there in person. That is still not feasible today.
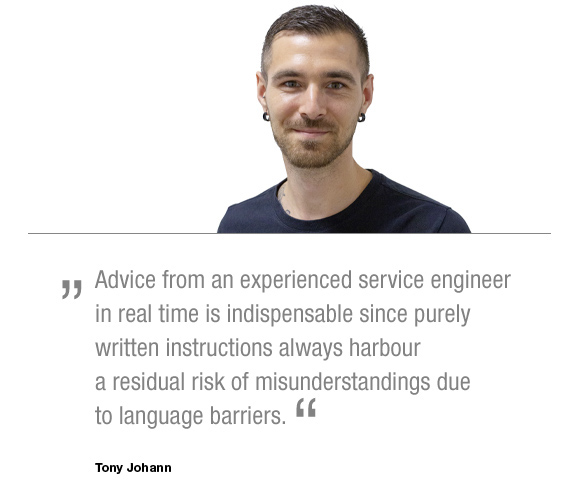
What kind of precautions did you take in order to make this remote assembly possible?
Christian Lübke: First, we needed to make sure that the technical equipment on site was in good enough condition to be supported using remote service via the app. For this reason, cameras were installed in the harbour and the Argentinian mechanics were equipped with mobile phones, whose high-quality cameras they could use to send Nils Liesner close-up photos over the app.
Tony Johann: Furthermore, we created a 60-page technical installation guide for the crane, which gives an overview of each step in the assembly process, and which our colleagues on site could use as a first point of reference. But that wasn't sufficient in itself. Advice from an experienced service engineer in real time is indispensable since purely written instructions always harbour a residual risk of misunderstandings due to language barriers.
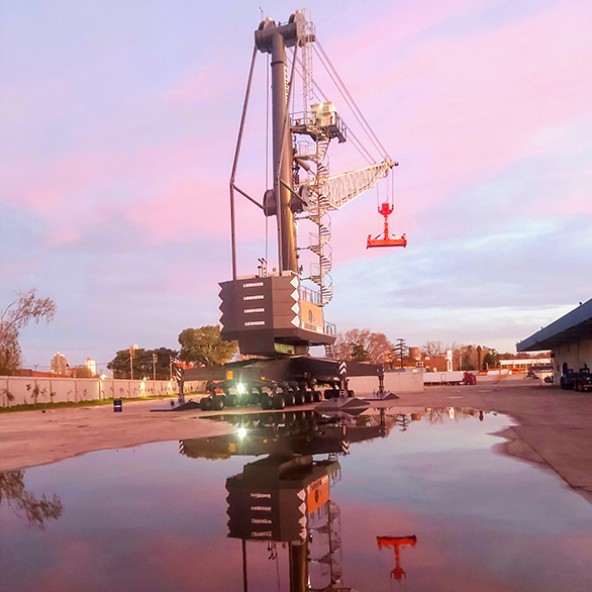
Mr. Liesner, after all these preparations, how did the crane assembly go?
Nils Liesner: My work began with the unloading of the crane parts. I advised our Argentinian colleagues about the placement of the crane's individual parts, in order to be able to assemble the crane as quickly and strategically as possible later on. At first, we encountered a few technical difficulties with the cameras, which is why I had to initially assess the situation using photos taken on site. Once a faster internet connection was installed, we were able to get started properly.
We had daily meetings in which I explained the details of the assembly guide to our on-site colleagues in more detail, and answered their questions. This was especially helpful when I was able to share tips I've learned over time, through years of experience building mobile harbour cranes. For example, when it was time to assemble the LHM 420 tower. This is one of the most laborious steps in the crane assembly. Above all, good time management is required to complete the work within a day.
Do you believe that operations like these, in which the Remote Service App played an important role, will become more common in the future?
Christian Lübke: Solutions like the Remote Service tool will certainly be part of our digitalized future. That said, we will probably be less reliant on the app for supervising commissioning. Instead, it will probably be used more often for troubleshooting machines that are already operational. The Remote Service App can be used to identify errors more quickly. Currently, if an assembly mechanic initially travels to a location and then realizes that a pump is damaged, he may need to make a second trip to replace that part. Digital troubleshooting would allow the assembly mechanic to arrive on site and meet the client with the required part in hand, and correct the problem straight away. This not only allows us to start troubleshooting faster, it also lowers travel costs – in the end, this may also reduce the amount of time during which the crane is not operational.
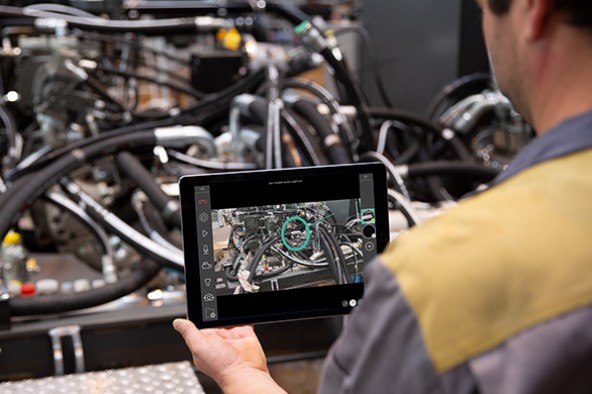
The Remote Service App
With the Remote Service App, Liebherr offers a new tool for improved remote service for maritime cranes, crawler cranes, rope excavators, and specialized deep foundation equipment. The tool includes a range of features such as audio- and video calls, a chat feature, screen sharing, image and document exchange, as well as a whiteboard features. This allows Liebherr's experts to provide fast and efficient support to our clients around the world, in real time. As a result of the current global pandemic, Liebherr has decided to bring the Remote Service App to the market faster using an extended test phase. This means all Liebherr clients now have the opportunity to use the Remote Service App for free until the end of 2020. The app only requires a laptop, tablet, or smartphone and an internet connection.
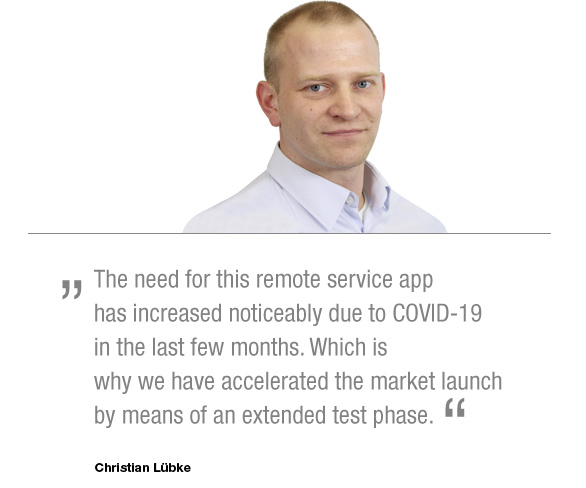
How has the COVID-19 crisis impacted customer service over the past few months?
Christian Lübke: Around 30 to 35 assembly mechanics work for Liebherr-MCCtec Rostock GmbH around the world. During the peak of the COVID-19 crisis in March 2020, we had to stop all service calls and bring the assembly mechanics that were currently abroad back to Germany, sometimes under challenging travel conditions. Now, around ten of our employees are back at work – in compliance with local hygiene and distancing regulations, of course.
Over the past few months, the demand for a Remote Service App because of the COVID-19 crisis has increased considerably, which is why we launched it onto the market faster than originally planned, using an extended test phase. Our customers can access the Remote Service App free of charge until the end of 2020. This year, we collected valuable experiences, which we are putting to use as we further develop the app.
Looking back at the first remote assembly, what conclusions can you draw today?
Nils Liesner: Personally, the remote assembly was an unusual situation for me. Normally, I travel to the site and work with them to tackle it in person – this time, I had to depend on my colleagues in Argentina. Looking back, it all worked out very well.
Tony Johann: It did, even though the situation was new to all of us and we had to improvise a lot because of COVID-19. In the end, everything went very well. After four weeks, we were able to deliver the crane to our clients on the date we had originally agreed on.