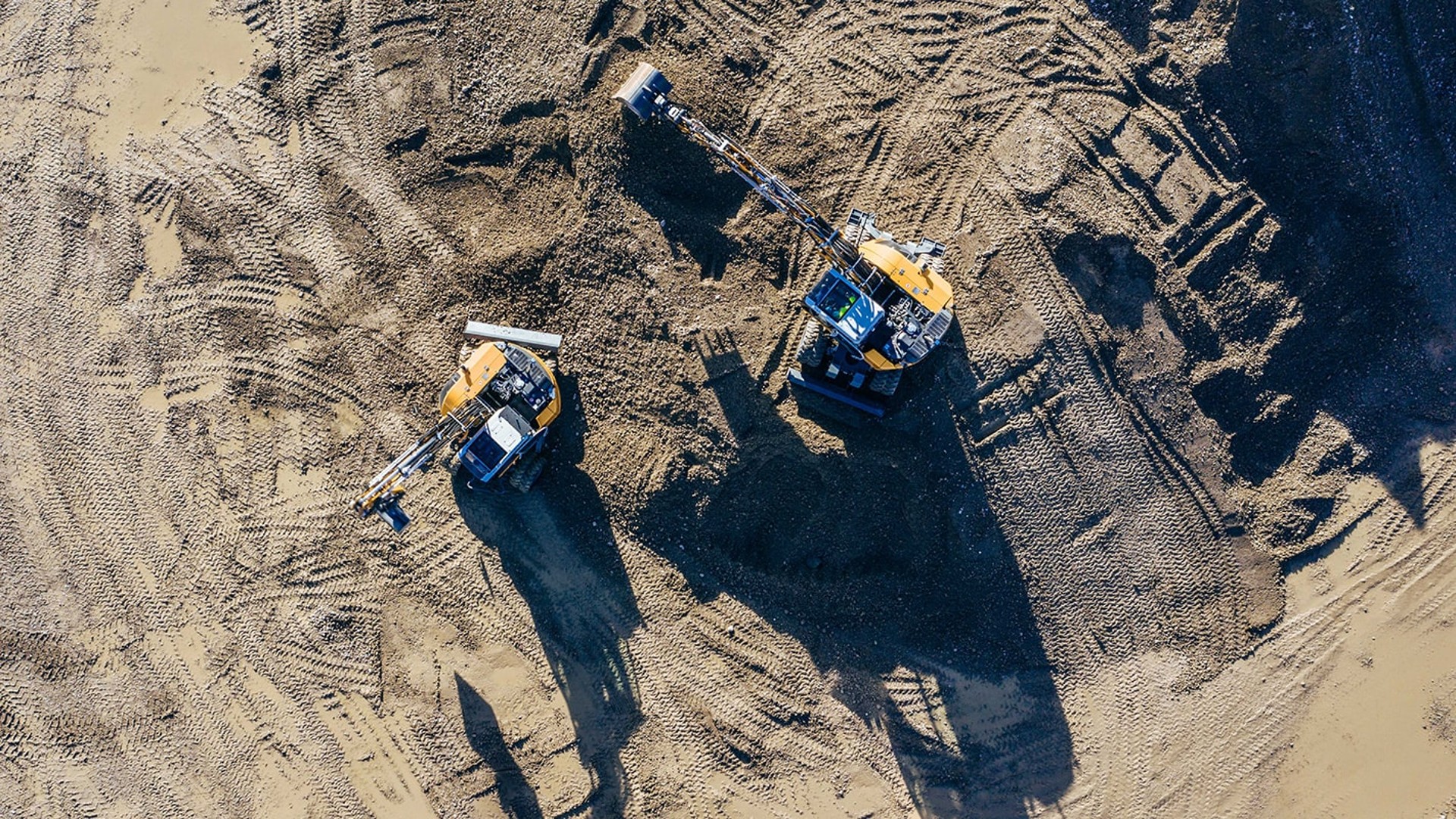
12 Minuten Lesezeit
Wenn Ideen Form annehmen
Komplexe Datenberechnungen, digitale Simulationen und viele hundert Stunden Graben und Fahren auf anspruchsvollem Testgelände: In Kirchdorf an der Iller perfektioniert Liebherr die Entwicklung der nächsten Generation von Erdbewegungs- und Materialumschlagmaschinen.
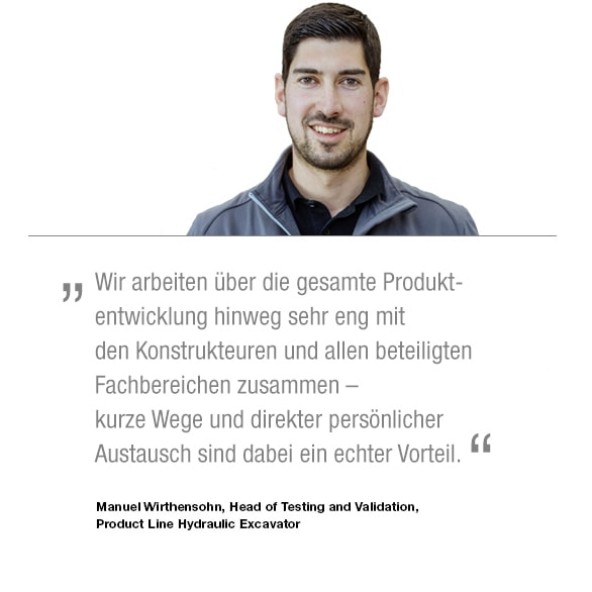
Feintuning auf der Zielgeraden
Die Schaufel gräbt sich tief in den Kies. Der A 913 Compact Litronic wendet auf engster Fläche, um den bereitstehenden, gigantischen knickgelenkten Muldenkipper zu beladen. Am Steuer des Mobilbaggers sitzt Manuel Wirthensohn, der an der Fracht nur am Rande interessiert ist. Ihm geht es vielmehr um die Maschine selbst, um die Wendigkeit und das Lastenspiel des neuen Hydraulikbaggers.
Wirthensohn ist Versuchsingenieur und als Gruppenleiter im Bereich Testing and Validation zuständig für Erdbewegungsmaschinen von 10 bis 24 Tonnen. Mit umfangreicher Messtechnik fühlen er und sein Team dem A 913 Compact Litronic, einem neuen, besonders kompakten Hydraulikbagger, seit Wochen ganz praxisnah auf den Zahn. „Was noch nicht perfekt ist, wird sofort verbessert – parallel zum laufenden Testbetrieb“, erklärt Wirthensohn mit einem Augenzwinkern.
Die Zeit drängt. Der Serienstart steht vor der Tür. Schon bald soll der A 913 Compact auf innerstädtischen Baustellen all seine Stärken ausspielen – ohne irgendwelche Kinderkrankheiten. Damit die Feinabstimmung der Maschine perfekt gelingt, können Manuel Wirthensohn und sein Team das neue, europaweit einzigartige Entwicklungs- und Vorführzentrum der Liebherr-Hydraulikbagger GmbH in Kirchdorf an der Iller nutzen. Entwickler, Konstrukteure und Tester arbeiten hier Hand in Hand zusammen. Nie lagen die unterschiedlichen Kompetenzen auch räumlich näher beieinander.
Indem Sie auf „AKZEPTIEREN“ klicken, willigen Sie für dieses Video gemäß Art. 6 Abs. 1 lit. a DSGVO in die Datenübermittlung an Google ein. Wenn Sie künftig nicht mehr zu jedem YouTube-Video einzeln einwilligen und diese ohne diesen Blocker laden können möchten, können Sie zusätzlich „YouTube-Videos immer akzeptieren“ auswählen und damit auch für alle weiteren YouTube-Videos, welche Sie zukünftig auf unserer Website noch aufrufen werden, in die jeweils damit verbundenen Datenübermittlungen an Google einwilligen.
Erteilte Einwilligungen können Sie jederzeit mit Wirkung für die Zukunft widerrufen und damit die weitere Übermittlung Ihrer Daten verhindern, indem Sie den entsprechenden Dienst unter „Sonstige Dienste (optional)“ in den Einstellungen abwählen (später auch aufrufbar über die „Datenschutzeinstellungen“ in der Fußzeile unserer Website ).
. Weitere Informationen erhalten Sie in unserer Datenschutzerklärung sowie in der Google-Datenschutzerklärung.Datenschutzerklärung von Google.*Google Ireland Limited, Gordon House, Barrow Street, Dublin 4, Irland; Mutterunternehmen: Google LLC, 1600 Amphitheatre Parkway, Mountain View, CA 94043, USA** Hinweis: Die mit der Datenübermittlung an Google verbundene Datenübermittlung in die USA erfolgt auf Grundlage des Angemessenheitsbeschlusses der Europäischen Kommission vom 10. Juli 2023 (EU-U.S. Data Privacy Framework).Das Entwicklungs- und Vorführzentrum
Auf einer Gesamtfläche von 12,8 Hektar befinden sich in dem europaweit einzigartigen Entwicklungs- und Vorführzentrum eine Versuchshalle mit Verwaltungsgebäude und ein großes Versuchsgelände mit einer 1,2 Kilometer langen Teststrecke.
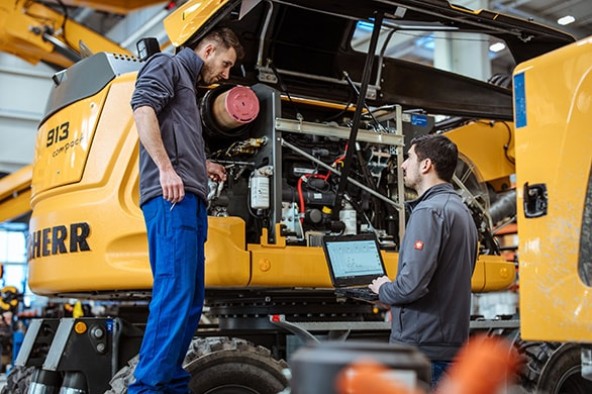
Forscher im Blaumann
Halle 18 des Entwicklungs- und Vorführzentrums: Was auf den ersten Blick wie eine sehr große Werkstatt aussieht, entpuppt sich bei näherem Hinsehen als ein gewaltiges Forschungslabor. Drehmomentschlüssel und Schraubendreher sind hier für die Techniker genauso wichtige Werkzeuge wie Messsensorik, Laptop-Anschlüsse und digitale Analysetools. „Wir vermessen die gesamte Maschine und alle Anbauten, um möglichst viele Erkenntnisse aus der Praxis zu gewinnen“, berichtet Manuel Wirthensohn.
Beim A 913 Compact sind es mehr als 60 Messpunkte, mit denen die Ingenieure bei den Prototypen das hydraulische Drucksystem und die Bewegungsumfänge bei den Arbeitsvorgängen erfassen. „Zwei Tage braucht es, um das Gerät einzurichten. Die Tests selber laufen dann über Monate. Verbesserungen setzen wir in dieser Zeit gleich um und beziehen sie ins Testgeschehen ein“, berichtet Wirthensohn. „Neben den Daten fließen in die Bestandsaufnahme auch die Erfahrungen der Fahrer ein, die sie beim Praxiseinsatz im Testgelände machen.“
Belastungen bis ans Limit
Hinzu kommen umfangreiche Dauertests auf den Prüfständen. Die Schwerpunkte liegen dabei auf der Untersuchung und Optimierung von hydraulischen Gesamt- und Subsystemen sowie den tragenden Strukturkomponenten, wie beispielsweise dem Unterwagen oder dem Fahrwerk. Gerade wird in der von kaltem Licht durchfluteten Halle der Schwenkarm eines Mobilbaggers einer Härteprüfung unterzogen.
„Das heißt Bewegungen und Belastungen ohne Rücksicht auf Verluste“, erläutert Wirthensohn. „Wir fahren im Nonstop-Dauerlauf über einige Wochen 4,5 Millionen Lastzyklen – der Mechanik wird nichts erspart.“ Ziel sei es, mit solchen aufwendigen Verfahren die Stahlbaustruktur strukturmechanisch zu testen, um die Konstruktion weiter zu optimieren.
Indem Sie auf „AKZEPTIEREN“ klicken, willigen Sie für dieses Video gemäß Art. 6 Abs. 1 lit. a DSGVO in die Datenübermittlung an Google ein. Wenn Sie künftig nicht mehr zu jedem YouTube-Video einzeln einwilligen und diese ohne diesen Blocker laden können möchten, können Sie zusätzlich „YouTube-Videos immer akzeptieren“ auswählen und damit auch für alle weiteren YouTube-Videos, welche Sie zukünftig auf unserer Website noch aufrufen werden, in die jeweils damit verbundenen Datenübermittlungen an Google einwilligen.
Erteilte Einwilligungen können Sie jederzeit mit Wirkung für die Zukunft widerrufen und damit die weitere Übermittlung Ihrer Daten verhindern, indem Sie den entsprechenden Dienst unter „Sonstige Dienste (optional)“ in den Einstellungen abwählen (später auch aufrufbar über die „Datenschutzeinstellungen“ in der Fußzeile unserer Website ).
. Weitere Informationen erhalten Sie in unserer Datenschutzerklärung sowie in der Google-Datenschutzerklärung.Datenschutzerklärung von Google.*Google Ireland Limited, Gordon House, Barrow Street, Dublin 4, Irland; Mutterunternehmen: Google LLC, 1600 Amphitheatre Parkway, Mountain View, CA 94043, USA** Hinweis: Die mit der Datenübermittlung an Google verbundene Datenübermittlung in die USA erfolgt auf Grundlage des Angemessenheitsbeschlusses der Europäischen Kommission vom 10. Juli 2023 (EU-U.S. Data Privacy Framework).Konstruktion und Testing gehen Hand in Hand
„Komm rüber, wir starten gleich den Motor und dann geht’s an die Arbeit im Gelände.“ Als Manuel Wirthensohn vor ein paar Wochen bei Mathias Graf angerufen hatte, machte dieser sich sofort auf den Weg. Der Entwicklungsingenieur hatte es ja auch nicht weit aus seinem Büro zur Halle 18, von wo aus der A 913 Compact zu seinen ersten Praxistests aufbrechen sollte. „Das war ein großer Moment“, erinnert sich Graf. „Da ist man als Konstrukteur sehr gern dabei.“
Er und seine Kollegen aus der Konstruktionsabteilung begleiten die Maschinen schließlich von den ersten Ideenskizzen auf einem Blatt Papier bis zur Fertigstellung. Und darüber hinaus sogar zu Testeinsätzen beim Kunden.
Ein Teil des systematischen Entwicklungsprozesses ist klassisches Ingenieurwesen, ausgehend von einer Zeichnung und dem Erstellen einer Stückliste. „Der A 913 Compact entstand aus unserer modularen Plattform, auf der wir unsere Innovationen mit bewährter Technologie verbinden“, erklärt Mathias Graf.
Dabei sei der konstruktive Alltag geprägt von regelmäßigen Abstimmungsrunden mit anderen Fachabteilungen. Das gehe dann schnell tief ins Detail, wenn etwa die Herstellungskosten oder die Schweißbarkeit eines einzelnen Bauteils kalkuliert werden müssten. „Wir sind dafür zuständig, dass alle Entwicklungsschritte zusammenpassen und am Ende ein in sich stimmiges Produkt in Serie gehen kann“, bringt es Graf auf den Punkt.
Indem Sie auf „AKZEPTIEREN“ klicken, willigen Sie für dieses Video gemäß Art. 6 Abs. 1 lit. a DSGVO in die Datenübermittlung an Google ein. Wenn Sie künftig nicht mehr zu jedem YouTube-Video einzeln einwilligen und diese ohne diesen Blocker laden können möchten, können Sie zusätzlich „YouTube-Videos immer akzeptieren“ auswählen und damit auch für alle weiteren YouTube-Videos, welche Sie zukünftig auf unserer Website noch aufrufen werden, in die jeweils damit verbundenen Datenübermittlungen an Google einwilligen.
Erteilte Einwilligungen können Sie jederzeit mit Wirkung für die Zukunft widerrufen und damit die weitere Übermittlung Ihrer Daten verhindern, indem Sie den entsprechenden Dienst unter „Sonstige Dienste (optional)“ in den Einstellungen abwählen (später auch aufrufbar über die „Datenschutzeinstellungen“ in der Fußzeile unserer Website ).
. Weitere Informationen erhalten Sie in unserer Datenschutzerklärung sowie in der Google-Datenschutzerklärung.Datenschutzerklärung von Google.*Google Ireland Limited, Gordon House, Barrow Street, Dublin 4, Irland; Mutterunternehmen: Google LLC, 1600 Amphitheatre Parkway, Mountain View, CA 94043, USA** Hinweis: Die mit der Datenübermittlung an Google verbundene Datenübermittlung in die USA erfolgt auf Grundlage des Angemessenheitsbeschlusses der Europäischen Kommission vom 10. Juli 2023 (EU-U.S. Data Privacy Framework).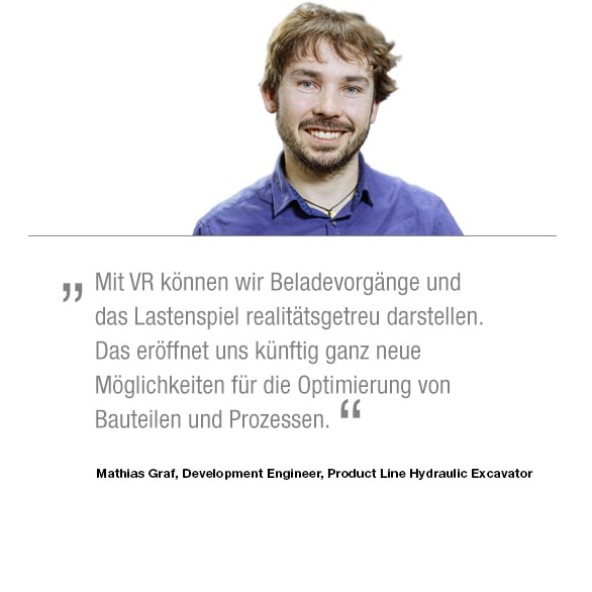
Mit Virtual Reality der eigenen Zeit voraus
Zirka 36 Monate dauert eine Entwicklung wie die des A 913 Compact. Um die Entwicklungszeiten kurz zu halten und bestmögliche Ergebnisse zu erzielen, arbeiten die Konstrukteure seit Kurzem auch mit Virtual Reality. „Damit können wir beispielsweise bereits am virtuellen Prototyp Sichtfelduntersuchungen durchführen“, so Graf. Damit werde sichergestellt, dass die Rundumsicht in alle Richtungen für jeden Fahr- und Arbeitszustand ausreichend Sicherheit bietet. Außerdem biete Virtual Reality die Möglichkeit, die Zugänglichkeit von Service- und Wartungsorten bereits im Vorfeld zu prüfen.
„Diese 3D-Simulationen ermöglichen es uns, Bauteile und Komponenten zu testen, die es noch gar nicht gibt. So können wir Fehler bereits ausmerzen, bevor der Prototypenbau überhaupt startet“, erläutert Mathias Graf die Vorteile der neuen Technologie. Oberstes Ziel sei es, bereits die erste Prototypenmaschine sowohl funktionell als auch qualitativ auf einem maximal hohen Level zu realisieren – dann sei der Weg zum bestmöglichen Mobilbagger in Serie nicht mehr weit.
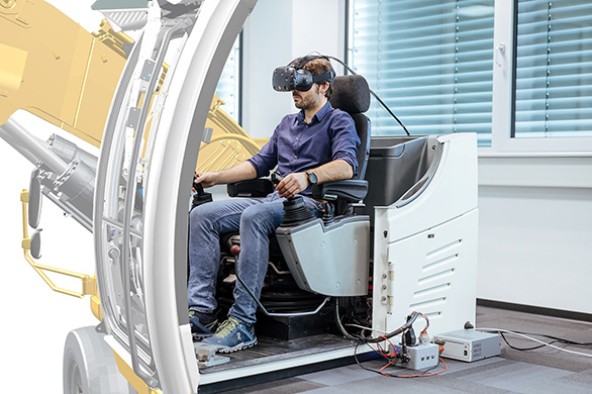
Durch die VR-Simulation verschmelzen virtuelle und reale Welt miteinander.
Virtual Engineering
Die Zukunft ist digital – zunehmend auch in der Konstruktion. Beim Virtual Engineering (VE) werden die Entwicklungsprozesse mit Hilfe digitaler, dreidimensionaler Modelle unterstützt und vorangetrieben. Mit Unterstützung der 3D-Visualisierungen und Virtual Reality (VR) wird die Wahrnehmung der Wirklichkeit über eine Datenbrille in Echtzeit mit einer interaktiven virtuellen Umgebung verbunden. So können etwa Produkte oder Fertigungsabläufe simuliert werden.
Aber so nah man mit digitalen Lösungen auch an die Realität heranrücken könne, das echte Baggern im Testgelände sei nach wie vor unverzichtbar. „Einen Mobilbagger und seine ganze Kraft bei der Arbeit zu spüren, ist und bleibt einzigartig“, schildert Graf. Das neue Entwicklungs- und Vorführzentrum verbindet damit optimal beide Welten – die virtuelle und die reale.