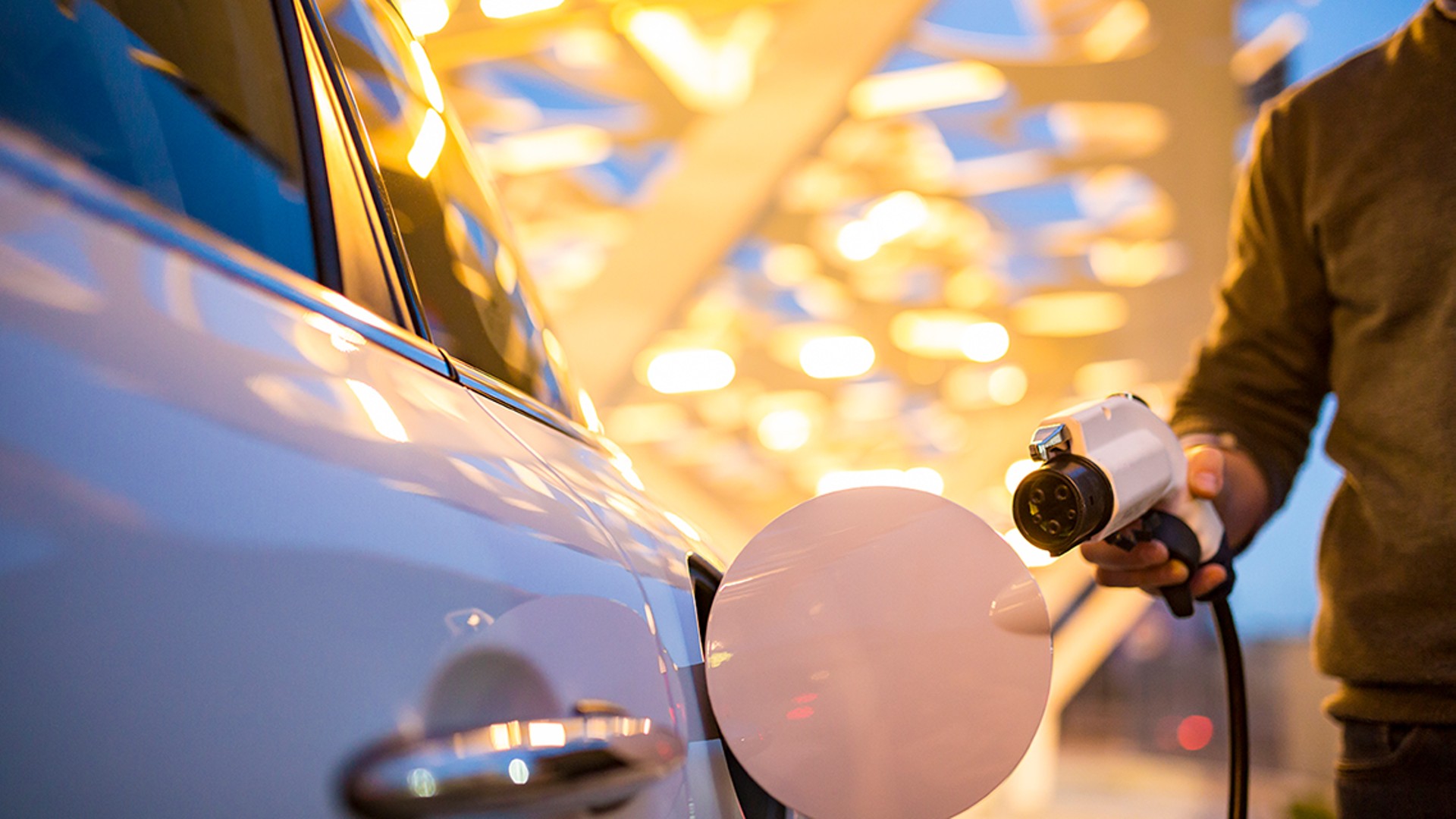
7 Minuten Lesezeit
Unter Strom
Aus Ideen Lösungen zu machen, gehört zu den klassischen Ingenieurstugenden. Liebherr bringt mit interdisziplinärem Wissens- und Erfahrungsaustausch Prozess- und Produktinnovationen für das neue Zeitalter der E-Mobilität voran.
Wenn Ingenieure auf Tiefgang gehen
Bei Tiefgang und dem Entdecken von Welten, die einem nicht völlig vertraut sind, sind Taucher im Vorteil. Sie bringen Routine im Umgang mit bewährter Technik mit und wissen um den Wert, sich hundertprozentig auf seine Tauchpartner verlassen zu können. Der Lohn: „Unter Wasser sieht man durch die Taucherbrille klarer und seine Umgebung und ihre faszinierenden Möglichkeiten viel größer“, sagt Jürgen Appel. Der begeisterte Sporttaucher ist gelernter Maschinenbauer und führt seit gut einem Jahr bei Liebherr im Zentralbereich Corporate Technology verschiedene Zukunfts- und Entwicklungsprojekte der Produktsegmente in eigens geschaffenen Expertengruppen zusammen.
Einen Schwerpunkt bilden dabei neue Antriebskonzepte, die E-Mobilität und die Herausforderungen und Chancen, die sich daraus für die Industrie ergeben. „Viele Produktsegmente sind auf unterschiedliche Weise mit Innovationen befasst und bearbeiten dazu mitunter ganz ähnliche Themen und Fragestellungen. Dies führen wir in Expertengruppen zusammen und teilen in regelmäßigem Austausch das Wissen“, erklärt Appel. „Das bringt alle Beteiligten gleichermaßen voran.“
Automatisierung für eine ganz neue Autoproduktion
Zum Beispiel bei der Automatisierung der Montage von Batteriepacks von E-Autos. Viktor Bayrhof vom Market Sales & Product Management des Liebherr-Produktsegments Verzahntechnik und Automationssysteme arbeitet in Kempten (Deutschland) an neuen Produktionsformen für den Automobilbau von morgen.
1
Herr Bayrhof, wie verändert gerade der Umstieg auf die E-Mobilität die Herstellung von Autos?
Viktor Bayrhof: Ohne das Verbauen von Verbrennermotor und Getriebe haben wir es bei E-Autos mit einer ganz neuen Architektur des Fahrzeugs zu tun. Für viele Kunden ist das Neuland. So unterscheidet sich beispielsweise die Montage der Batteriepacks fundamental von der konventioneller Antriebstechnologien wie Motorblocks, Kurbelwellen oder Zahnrädern. Denn hier handelt es sich um ein Werkstück, das unterschiedlichen Montage- und Technologieprozessen unterliegt. Das hat Auswirkungen auf den gesamten Prozess. Ein fertig montiertes Pack im Automobilbereich wiegt bis zu 800 Kilogramm. Das ist wie gemacht für die Handlingssysteme von Liebherr.
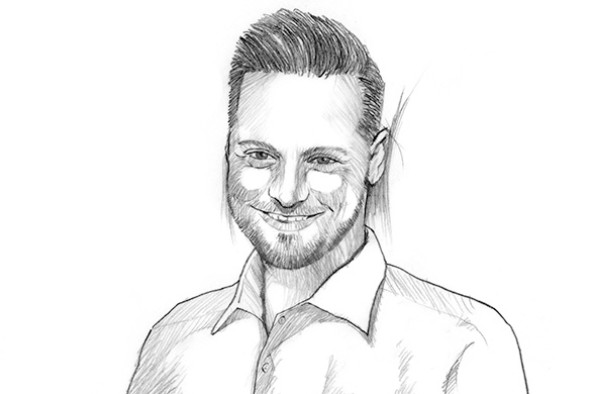
Viktor Bayrhof, Marktvertrieb & Produktmanagement Automationssysteme bei der Liebherr-Verzahntechnik GmbH
2
Die Automobilindustrie denkt bei ihren Produktionslinien für gewöhnlich in langen Zyklen. Wieviel Zeit bleibt da für neue Entwicklungen?
Wir erleben gerade einen hohen Veränderungsdruck. Die Ära der Verbrenner geht zu Ende. Mit dem European-Green-Maßnahmenplan für ein klimaneutrales Europa bis 2050 werden die CO2-Emmissionswerte stark reglementiert. Da die EU-Klimaziele mit Verbrennern, als auch mit Hybrid-Fahrzeugen allein, nicht zu erreichen sind, fördert die EU gezielt Elektrofahrzeuge. Einige Hersteller wollen die Produktion von Verbrennern schon bis 2025 einstellen, Studien prophezeien das vollständige Aus der Verbrenner innerhalb der EU um das Jahr 2040. Die Corona-Pandemie hat diesen Trend noch einmal verstärkt. Zudem führen die großen Investitionen in die Batterieforschung zu zahlreichen Innovationen, die Batterien leistungsfähiger, langlebiger und kostengünstiger machen. Für uns heißt das, wir müssen mit der Entwicklung unserer Automatisierungslösungen immer schneller werden und in unseren Projekten schlank aufgestellt bleiben, um auf diese extrem hohe Dynamik am Markt reagieren zu können.
3
Wo setzt Liebherr dabei an?
Ausgangspunkt war ein Entwicklungsprojekt unter wissenschaftlicher Begleitung der KIT Campus Transfer GmbH, einer Ausgründung des Karlsruhe Institut für Technologie, und der PEM Motion GmbH, die aus dem Lehrstuhl für Produktionstechnik für Elektromobilitätskomponenten an der RWTH Aachen hervorgegangen ist. Gemeinsam haben wir uns umgeschaut, welche Veränderungen in der Produktion von E-Autos wir mit unserem Know-how aktiv mitgestalten können. Das war ein unglaublich intensiver Lernprozess. Daraus ist ein modularer Baukasten für die automatisierte Montage von Batteriepacks für die Fahrzeugindustrie entstanden. Mit ihm können wir je nach Kundenanforderung eine ganz individuelle Anlage konfigurieren. So können teilautomatisierte Anlagen für kleine Stückzahlen oder vollautomatisierte Linien für die Großserienproduktion skalierbar ausgelegt werden. Und das immer unter Berücksichtigung der speziellen Eigenschaften der verarbeiteten Gefahrstoffe, möglicher Brennbarkeit und elektrischer Ladung.
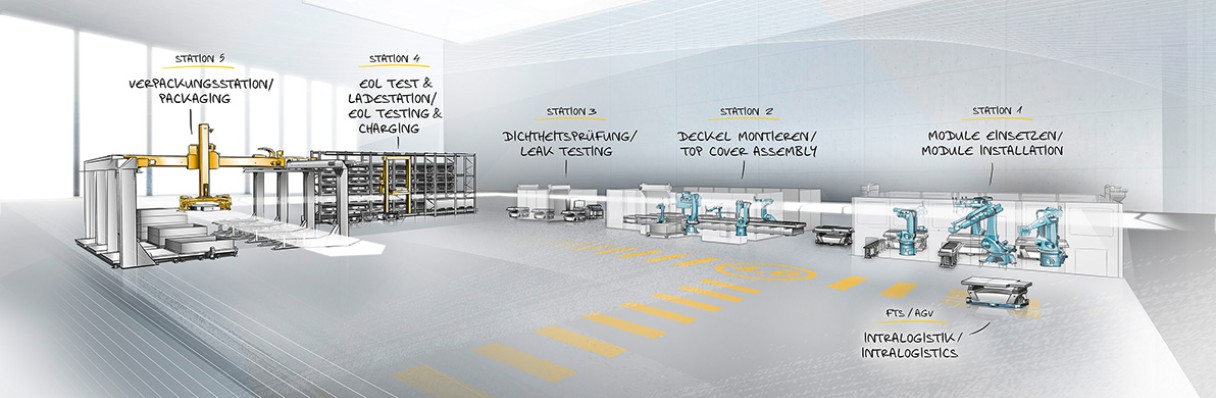
4
Was ist das Neue daran?
Wir haben bei der Suche nach bedarfsgerechten Lösungen für das erforderliche Prozess- und Werkstückhandling einen modularen Ansatz gewählt, der beliebig skalierbar ist. Dabei setzen wir auf platzsparende Linearportale, die sich für einfaches Handling schwerer Gewichte von Batteriepacks eignen. Diese können ganz nach Bedarf gezielt mit Industrierobotern kombiniert werden, die die komplexeren Handlings- und Prozessaufgaben übernehmen.
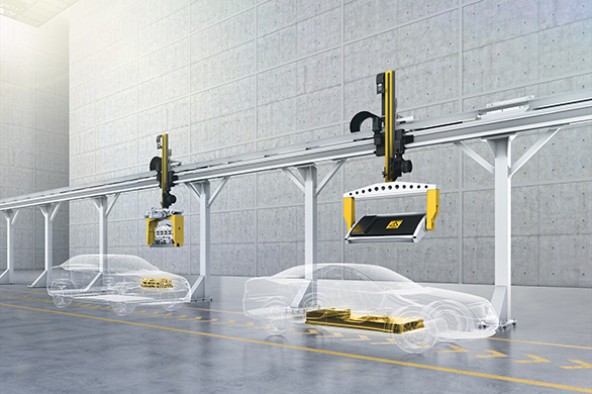
5
Was macht den modularen Ansatz aus?
Wie der Kunde ein Batteriepack zusammenbauen will, entscheidet er selbst. Wir liefern das Know-how und die Systemkompetenz für die Realisierung der Anlage und der Prozesse. Dabei steht Sicherheit ganz oben auf der Agenda. Vor allem der Brandschutz hat in der Fertigung Priorität. Brennt ein Pack erst einmal, ist es nicht zu löschen. Um das zu verhindern, müssen entsprechende Schutzmaßnahmen ergriffen werden. Kommt es trotz aller Vorkehrungen zu einer Selbstentzündung der Batteriezellen, man spricht hier vom Thermal Runaway, müssen entsprechende Notfallstrategien bestehen um das brennende bzw. bald brennende Pack aus der Produktionsanlage auszuschleusen und in eine sichere Ausbrennbox zu befördern.
6
Sie sprachen von „Neuland“ in der Produktion. Wie wollen Sie dieses den Kunden näherbringen?
Im Sommer geht die neue Testanlage in unserem Tech Center an den Start. In dieser Hightech-Anlage können wir den technologisch anspruchsvollsten Teil der Prozesskette für die Montage von Batteriepacks abbilden. Hier können sich unsere Kunden „live“ ein Bild davon machen, wie sie ihre Fertigungslinien mit uns als Generalunternehmer automatisieren können. Bevor sich ein Kunde eine Anlage für die Großserienfertigung bestellt, können wir im Tech Center gemeinsam die Kernprozesse wie automatisiertes Schrauben oder Dosieren am Kundenwerkstück erproben. Für das elektrische Kontaktieren der Batteriemodule bieten wir als Alternative zu geschraubten Busbars auch eine innovative Automationslösung für steckbare Hochvolt-Modulverbinder an. Alles wird wie unter einem Brennglas zu erleben sein: Exponate und Prototypen, Dauerläufe und Belastungstests – wie auf einer Messe, nur dass wir hier auch Mitarbeiter und Kunden direkt an den Anlagen schulen können. Das wird richtig spannend und begeisternd.
Aus der Praxis für die Praxis
Für Jürgen Appel liegt der besondere Reiz der interdisziplinären Innovations- und Produktentwicklung im unkomplizierten Teilen von Erfahrungen. „Wir tauschen uns intensiv aus, ohne dass dabei die einzelnen Produktsegmente ihren eigenständigen Ansatz aufgeben. Das ist maßgeblich für den Erfolg aller.“ An Innovationsthemen und Ideen bestehe kein Mangel. „Wir müssen vielmehr gemeinsam priorisieren, womit sich die Arbeitskreise beschäftigen und wo der Wissensaustausch gerade besonders wichtig ist“, sagt Appel. Dabei seien aktuelle Erfahrungen aus der Praxis besonders wichtig. Zum Beispiel, wie sich der LR 1250.1 unplugged, der weltweit erste batteriebetriebene Raupenkran, bei seinem Einsatz in Norwegen macht. Oder wie netzbetriebene Materialumschlagmaschinen oder die Elektrifizierung von Mining-Trucks voranschreiten. Die Lösungen liegen dabei – wie immer – in den vielen kleinen Details.
Coole Kabel
Zum Beispiel beim effizienten Ladevorgang von batteriebetriebenen Fahrzeugen. Das ist eine Spezialität von Dirk Junghans, Geschäftsführer Vertrieb, Marketing & Kundendienst bei der Liebherr-Transportation Systems GmbH & Co KG. Der 58-jährige Elektroingenieur rückt auf dem Weg zu intelligenterer und grünerer Mobilität neue Kühlungssysteme für Ladestationen für Elektrofahrzeuge in den Fokus.
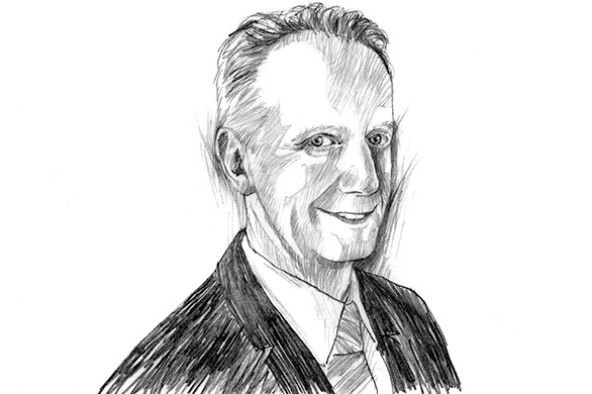
Dirk Junghans, Geschäftsführer Vertrieb, Marketing & Kundendienst bei der Liebherr-Transportation Systems GmbH & Co KG
1
Herr Junghans, E-Mobilität, Batterien und Kühlungssysteme: Wie passt das zusammen?
Hochleistungs-Lithium-Ionen-Batterien, wie sie heute zunehmend auch bei Bussen und Bahnen eingesetzt werden, sind nicht nur vergleichsweise teuer, sondern auch anspruchsvoll. Sie müssen dauerhaft in einem eng begrenzten Temperaturbereich betrieben werden, um die gewünschte Langlebigkeit und damit die Rentabilität der Investition sicherzustellen: im Sommer gekühlt und im Winter beheizt. Hier kommen unsere Thermal Conditioning Units (TCU) zum Einsatz – ein Kühlkreislauf hält die Temperatur der Batterie gradgenau im vorgegebenen Bereich.
2
Welche Erfahrungen und Kompetenzen bringt Liebherr-Transportation Systems für die Batteriekühlung mit?
Wir befassen uns schon seit mehr als drei Jahrzehnten mit der Entwicklung von anspruchsvollen Klimasystemen für Schienenfahrzeuge und haben in dieser Zeit breit gefächerte Kompetenzen in Bezug auf das Heizen, Lüften und Kühlen von Fahrgasträumen und Führerstandkabinen erworben. Da lag es nahe, unser Know-how auch für das Temperaturmanagement von Hochleistungs-Batterien einzubringen. Mit anderen Worten: Wir stützen uns bei der E-Mobilität auf ein breites Erfahrungsfundament.
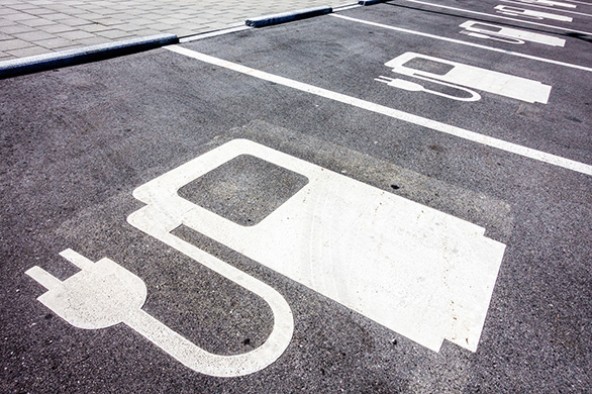
3
Der kritische Punkt bei der E-Mobilität ist noch immer die Reichweite. Ist die Batterie leer, will man so schnell wie möglich weiter. So einfach wie beim Sprittanken ist das aber nicht.
Wenn es um die Akzeptanz der neuen Technologie durch die Nutzer geht, ist insbesondere die Ladedauer die harte Währung. Die Stromstärke, mit der die Batterie geladen wird, entscheidet darüber, wie kurz oder lang die Wartezeit an der Ladestation ist. Beim Fast-Charging wird daher mit hohen Stromstärken gearbeitet. 350 Ampere sind dabei heute schon Standard. Zum Vergleich: Einfamilienhäuser sind üblicherweise mit einem Stromanschluss von 40 Ampere ausgestattet. Eine Steigerung ist aber bereits absehbar: Schnellladestationen mit 500 oder gar 690 Ampere Nennstrom sind schon in der Vorbereitung.
4
Dann ist doch alles auf einem guten Weg.
Strom durchs Kabel zu schicken, ist immer mit Wärmeentwicklung verbunden. Einfach gesagt: Je höher der Strom ist, desto heißer wird es. Dem kann man begegnen, indem man den Querschnitt des Ladekabels erhöht, was jedoch zugleich eine Zunahme des Gewichts bedeutet. Das Kabel ist aufgrund der steigenden Kapazität der Ladestationen irgendwann so schwer geworden, dass es für viele Kunden einfach nicht mehr zu handhaben war. Die Lösung ist die aktive Kühlung des Kabels und des Steckers beim Ladevorgang. Erst recht, wenn immer höhere Ladeströme ins Spiel kommen. Vielleicht bald schon mit bis zu 1.000 Ampere.
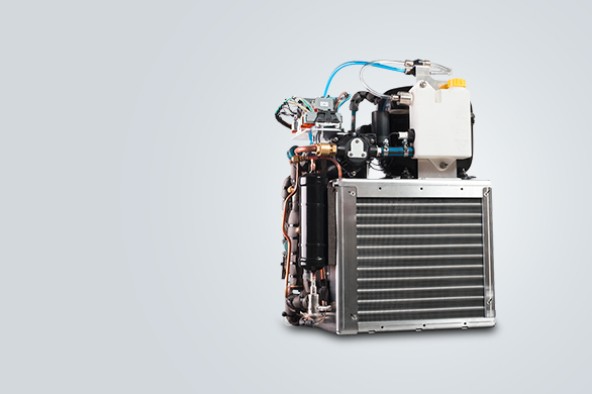
Die aktiven Kühleinheiten, auch als „Thermal Conditioning Units“ (TCU) bezeichnet, wurden speziell für e-Mobilitäts-Ladestationen entwickelt
5
Womit kann Liebherr beim Ladevorgang punkten?
Wir statten Schnellladestationen für E-Autos mit unseren Thermal Conditioning Units (TCU) aus, die dafür sorgen, dass sowohl das Kabel als auch der Ladestecker auf einem optimalen Temperaturniveau gehalten werden und überschüssige Wärme wirksam abgeführt wird. Das von uns erstmals in diesem Bereich eingesetzte hocheffiziente Kühlmedium wird dazu in der TCU auf eine vorbestimmte Temperatur gebracht und anschließend mit hoher Geschwindigkeit durch den hermetisch geschlossenen Kühlkreislauf gepumpt, der um die stromführenden Elemente des Kabels und des Steckers gewunden ist. Wir arbeiten hier mit einer aktiven Kälteerzeugung, das heißt die TCU funktioniert ähnlich wie eine Klimaanlage, nur dass in diesem Fall nicht die Luft konditioniert wird, sondern das verwendete Kühlmedium. Und auch ganz wichtig: Die Liebherr-Organisation kann den Service und die Wartung solcher anspruchsvollen Kühlsysteme jederzeit mit ihrem weltweiten Service-Netz sicherstellen.
6
Bringt sicheres, hochleistungsfähiges Laden den endgültigen Durchbruch der E-Mobilität?
Unsere effizienten Kühlungssysteme können dazu sicher einen wichtigen Beitrag leisten. Um den hohen Klimazielen zu entsprechen, kommt es aber auch darauf an, die Ladestationen mit Strom aus erneuerbaren Energien zu versorgen. Klar ist allerdings auch, dass batteriebetriebene E-Mobilität allein noch nicht die Lösung aller Klimafragen sein kann. Ich denke beispielsweise an Baumaschinen mit hoher Ausgangsleistung, für die es keine reine Batterielösung gibt. Da werden sicherlich noch andere Technologien wie Brennstoffzellen oder Wasserstoffantriebe in Zukunft eine wichtige Rolle spielen. Auch da bleiben wir dran.
Zurück zur Basis und zu den Ingenieurstugenden
Wenn Jürgen Appel an die Zukunft denkt, wird ihm nicht bange. „Wenn Liebherr wüsste, was Liebherr weiß…“, lautet ein geflügeltes Wort im Unternehmen. „Wir strukturieren gerade unser gesammeltes Wissen neu. Dieses Wissen ist unheimlich groß, aber auch weit verteilt. Im Austausch und Miteinander steckt jede Menge Zukunft und Potenzial“, sagt der Maschinenbauingenieur. „Wir leben in Zeiten, in denen klassische Ingenieurstugenden wieder in den Vordergrund rücken. Themen wie die Digitalisierung sind enorm wichtig – damit allein ist es aber noch nicht getan. Wir müssen unser Wissen strukturiert sammeln, für die Produkt- und Technologieentwicklung gezielt tiefer eintauchen und am Ende etwas bauen. Darum geht es. Am Ende muss ein Produkt oder eine Technologie rauskommen, die wirklichen Fortschritt bringt. Für unsere Kunden und für die Gesellschaft. Teil davon zu sein, ist eine großartige Aufgabe. Für jeden und jede Einzelne.“