„Bei der Hochpräzisionsbearbeitung von Schaufeln für Turbinen kommt es auf höchste Genauigkeit an“, erläutert Marc Weiß, Leiter Flexible Fertigungssysteme bei der MTU Aero Engines in München. Das Unternehmen gehört zur Spitzengruppe der Hersteller von zivilen und militärischen Luftfahrtantrieben aller Leistungsklassen sowie von stationären Industriegasturbinen. Bei Turbinenschaufeln handelt es sich um Gussteile aus schwer zerspanbaren Nickelbasislegierungen mit hochkomplexer Geometrie, die mit äußerster Präzision bearbeitet werden müssen. Im Betrieb müssen die Schaufeln extremste Bedingungen – enorme Fliehkräfte, Temperaturen nahe am Schmelzpunkt und starke Vibrationen – aushalten. Ein Bruch könnte zur Zerstörung des Triebwerks führen. Für alle Schritte der Herstellung gelten daher äußerst strenge Qualitätsanforderungen. Für die Entwicklung einer neuen, hoch automatisierten Fertigungsanlage kamen daher nur Zulieferpartner infrage, die höchste Qualität und Zuverlässigkeit gewährleisten konnten.
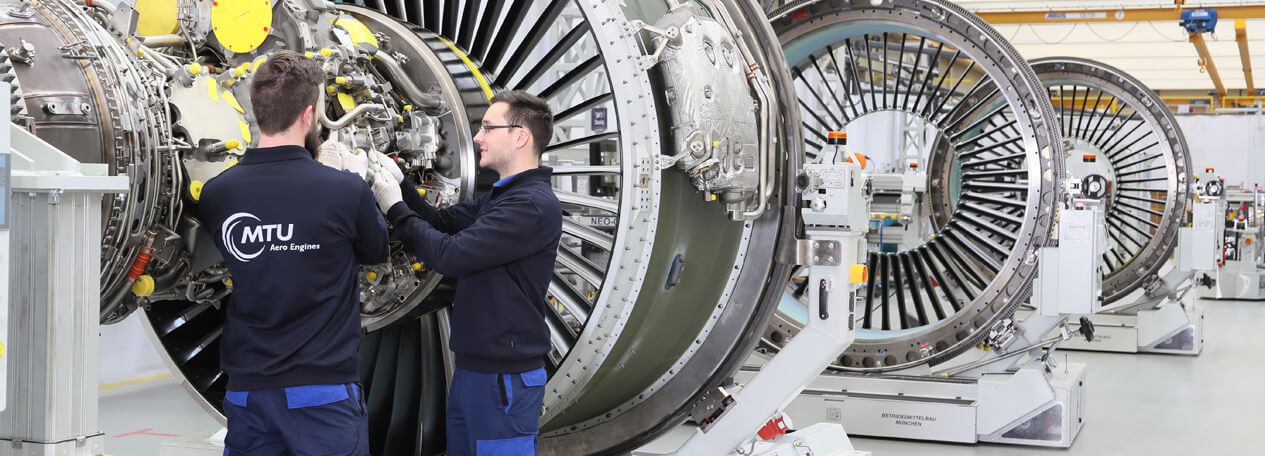
Liebherr und MTU Aero Engines: Partner bei der automatisierten Bearbeitung von Turbinenschaufeln
Heutige Flugzeugantriebe sind Wunderwerke der Technik. Vor allem die Schaufeln im Heißgasbereich müssen Belastungen aushalten, die noch vor nicht allzu langer Zeit als nicht beherrschbar erschienen. Da das weltweit steigende Luftverkehrsaufkommen zu einer rapide wachsenden Nachfrage führt, muss die bisherige Fertigungstechnologie modernisiert werden.
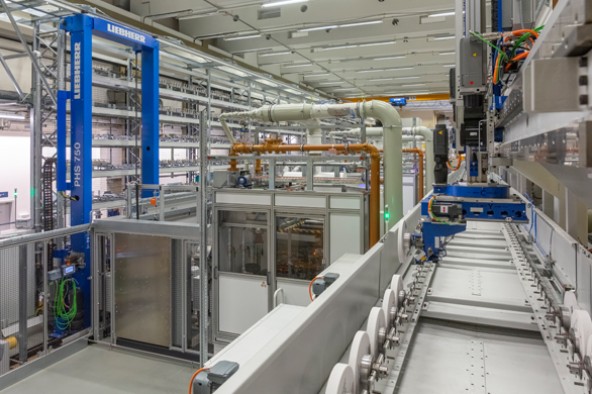
Ein Quantensprung bei der Automatisierung
„Die Anforderungen der MTU waren enorm und liefen auf eine mehr als zehnfache Steigerung der Mitarbeiterproduktivität hinaus“, erinnert sich Michael Appel, Gebietsverkaufsleiter Automationssysteme bei Liebherr-Verzahntechnik GmbH in Kempten. Um die enorm steigende Nachfrage bedienen zu können, sollte die Produktivität massiv gesteigert werden. Bisher war jeweils ein Mitarbeiter erforderlich, um eine bis zwei Maschinen in einer Fertigungskette aus einzelnen Stationen manuell zu bedienen. Bei der neuen Lösung reicht dagegen ein einziger Mitarbeiter aus, um eine sehr hohe Bearbeitungstiefe an vier parallel arbeitenden, vollautomatischen Schleifbearbeitungszellen zu erreichen. Jede Zelle besteht aus einem 6-achsigen Schleifbearbeitungszentrum PROKOS XT von BLOHM, das von einem Roboter der Firma AMT versorgt wird. Der Roboter erhält Werkstücke, Spannvorrichtungen, Abrichtwerkzeuge und Greiferzangen von einem vollautomatischen Liebherr-Palettenhandlingsystem (PHS). Dank seiner 250 Palettenplätze kann es die Bearbeitungszentren für mindestens 66 Stunden mannlos versorgen, so dass die Anlagen auch bei Bedienung in Gleitzeit ein komplettes Wochenende durcharbeiten können. Auf der anderen Seite der Fertigungszellen verläuft ein ebenfalls von Liebherr geliefertes Ladeportal (LP), über das die Maschinen mit Werkzeugen und Schleifscheiben versorgt werden. „Gehirn“ des Ganzen ist ein Leitsystem von SOFLEX, das alle Anlagen miteinander vernetzt und eine weitestgehend selbstorganisierte Produktion ermöglicht. Dieses neue Flexible Fertigungssystem (FFS) kann rund 15 verschiedene Bauteiltypen gemischt in beliebigen Stückzahlen bearbeiten. Der Arbeitsplatz für Maschinenbediener wurde zudem behindertengerecht ausgelegt.
Das System, das wir zusammen geschaffen haben, ist sehr komplex und dem bisherigen Stand der Technik weit voraus
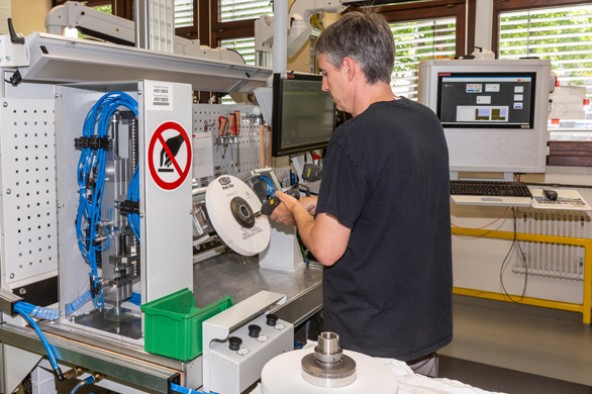
Enge Partnerschaft beim Engineering
„Die eigentliche Herausforderung bestand für Liebherr darin, unsere modularen Automatisierungskomponenten so auszuwählen und mit den übrigen Systemen zu verknüpfen, dass ein reibungsloses Zusammenspiel zustande kam“, ergänzt Michael Appel. Zudem übernahm Liebherr auch die Verantwortung für die CE-Zertifizierung der kompletten Anlage. Die Zusammenarbeit im sehr kleinen, dafür aber auch sehr effizienten Engineeringteam wurde von der MTU koordiniert. Im Team arbeiteten die Partnerunternehmen, die in ihren Märkten jeweils zu den Top-Anbietern zählen, auf Augenhöhe zusammen, tauschten Ideen aus und entwickelten im Dialog die entscheidenden Merkmale des Systems. Das umfasste selbst Details wie eine Hilfsfunktion für den Bediener, bei der ein Laserpointer auf die Stelle zeigt, wo das nächste einzusortierende Teil hingehört.
Kriterien für die Partnerwahl
„Das System, das wir zusammen geschaffen haben, ist sehr komplex und dem bisherigen Stand der Technik weit voraus“, freut sich M. Weiß. Hierbei habe Liebherr nicht nur durch passende Produkte im Automatisierungsbereich überzeugt: Ebenso wichtig war die Tatsache, dass die eingesetzte Technologie sehr ausgereift ist und sich im Praxiseinsatz bei zahlreichen Anwendern bestens bewährt hat. Besonders hervorzuheben sei auch die Kompetenz des Vertriebs. Herr Appel habe sich als technisch äußerst versierter Partner erwiesen, der sich intensiv beteiligte und zahlreiche gute Ideen einbringen konnte. Das Ramp-Up der Gesamtanlage sei erfolgreich angelaufen und die bisher erzielten Ergebnisse entsprächen den Planvorgaben. Mit der neuen Anlage sehe sich die MTU für die Anforderungen der Zukunft bestens gerüstet.