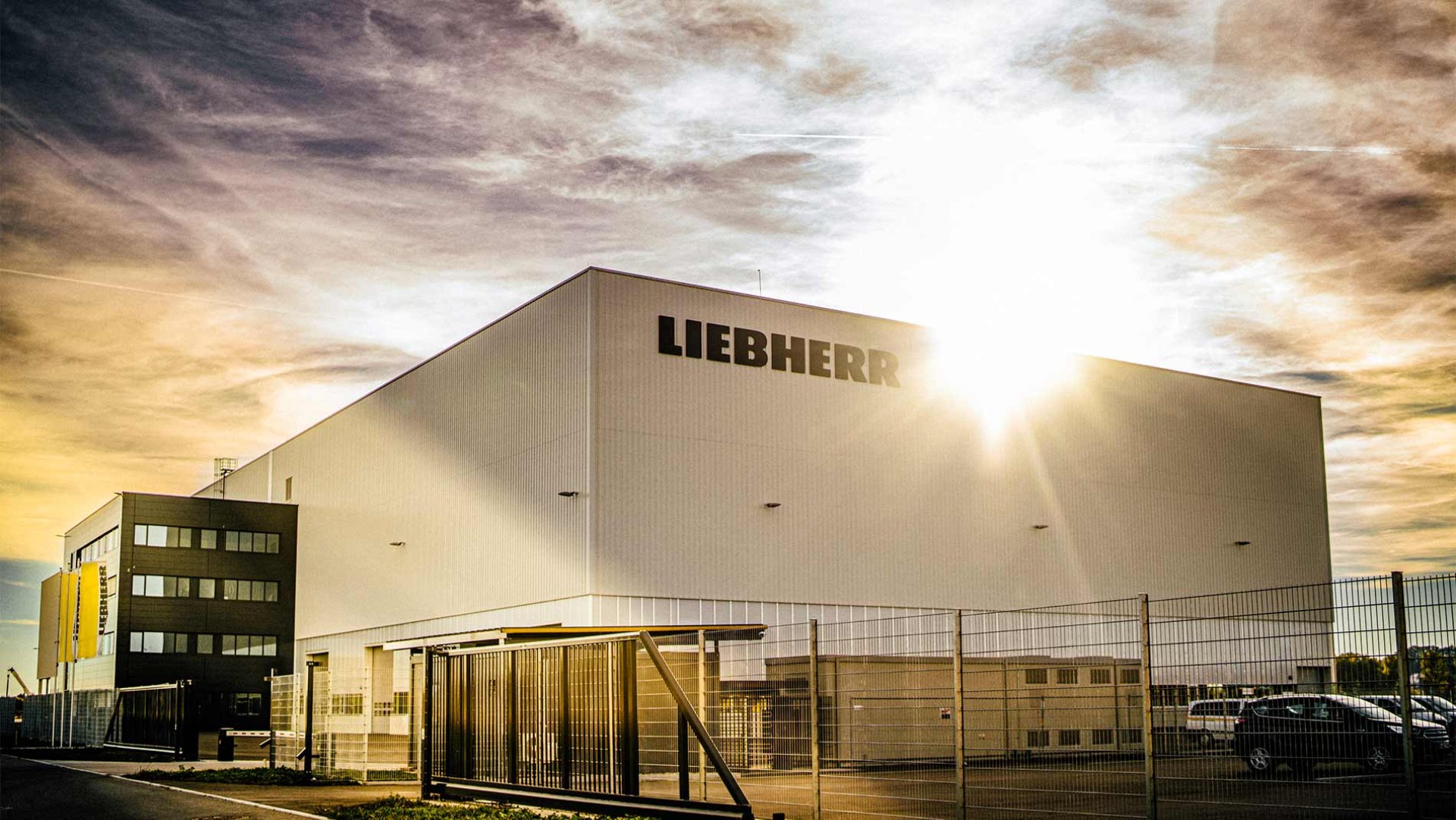
10 minutes - magazine 01 | 2023
Berg Repair Centre – what’s new? What’s different?
It’s not just cars, cranes also require a regular check-up to ensure that everything is still in perfect condition and works smoothly.
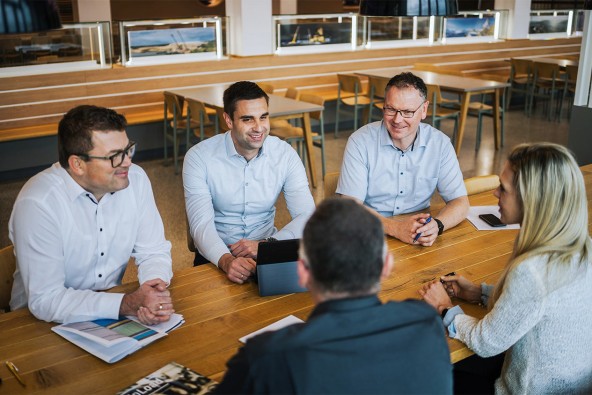
Bernd Rechtsteiner, Andreas Leicht and Harald Hummel (left to right) talking to UpLoad Editors, Wolfgang Beringer and Carmen Kley.
Second hand but first class
Now and again, something jams or ageing machines are given a well-deserved general refurbishment before they make their way to a new owner. We have been carrying out this service, repair and maintenance work of all kinds for mobile and crawler cranes at our repair centre in Ehingen for 40 years. As the number of cranes we sell rises, the number of machines that require specialist maintenance, repair or refurbishment work for resale naturally increases as well. This meant that our repair department had reached the limits of what it could do. It was time for a new, significantly larger repair centre.
And after being under construction for around a year, it is now complete – our repair centre in Ehingen-Berg. What’s new? What’s different? And what are the benefits for our customers as a result? That is exactly what we talked to our Berg Repair Centre Manager, Andreas Leicht, our Used Cranes Manager, Bernd Rechtsteiner and our Service Department Manager, Harald Hummel.
What was the reason for relocating the repair centre from the main plant to Ehingen-Berg?
Andreas Leicht: We have significantly more space available at our new repair centre in Ehingen-Berg. Previously, when we handled around 200 customer and used machines per year, we were working at the limit. Now, however, we can also accept emergency repair work at short notice. That means massive benefits for our customers, as we can get their cranes up and running again quickly.
Harald Hummel: It means that the Service Department is now generally more flexible and more targeted. The previous location of the repair centre at the main plant will be used to build a new spare parts warehouse. That will increase the availability of spare parts massively.
Bernd Rechtsteiner: It also means that we can now repair large cranes without any problems. We now have the space and manpower to provide the capacity we need. The large test yard immediately next to the repair centre is another major factor in this respect.
Andreas Leicht: One of the major benefits is that despite us being in a new location, we are only five kilometres away, which means we are really still very close to our main plant in Ehingen. We will be receiving material from there every day. Also, our experts from the design and production departments can be consulted quickly if we have any questions. That creates perfect conditions for us – even if we are facing complex repair work. Another benefit for our customers is the short distance from the road straight into the workshop. They no longer have to drive all round the massive plant to get to the repair centre.
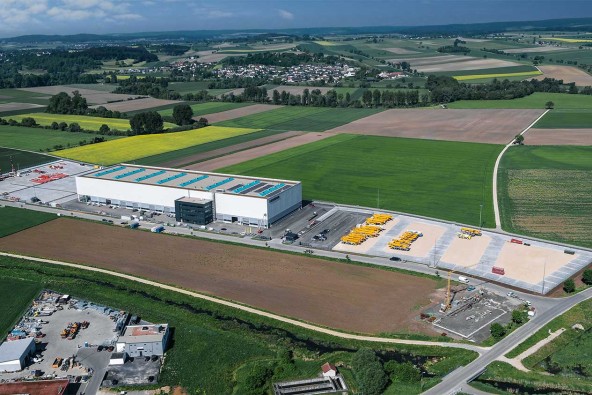
The repair centre at the Ehingen-Berg site.
How did the relocation go?
Andreas Leicht: Very well. Overall, the relocation phase lasted around three months. We were able to maintain operations during this time, despite all the challenges we faced. Naturally we moved all our experienced personnel with us to Ehingen-Berg, so capacity can now gradually be increased at the new site due to the infrastructure.
How well equipped is the new repair centre?
Andreas Leicht: Our new repair centre is even better equipped than the old one. Thanks to our new structural steelwork area with two straightening plates, we can now also carry out major structural steelwork repairs. Our boom test rigs and the special angled cranes enable us to repair and refurbish telescopic booms from cranes extending right up to our LTM 11200-9.1.
Harald Hummel: We also have the facility to weld large equipment and lattice sections in almost identical conditions as we use in our production plant. That’s a very special feature.
Andreas Leicht: Safety will also be improved due to the greater space. The workstations have been designed to comply with the latest ergonomic findings. For example, this includes personal lifting trucks for working safely and ergonomically at all heights within the assembly pits. We also have a TÜV-certified testing area with a brake test rig, steering play tester and a headlight adjustment area. That means we can comply with every single statutory requirement. Outside the repair area, the new site also has an office block, training and meeting rooms, a canteen and a lounge area for our customers.
In addition to repairs, crane maintenance is another major segment for the repair centre. Are there any new features in this area?
Harald Hummel: We have established a special service area in the shed for maintenance work. The installation of a filling and disposal facility means that we have state of the art equipment that complies with the very latest environmental regulations. It also means that we can accept maintenance work at short notice for our customers without them having to arrange appointments months in advance.
Andreas Leicht: We have already had customers who, after carrying out a job, for example at Legoland in Günzberg or at the Stuttgart Volksfest, have called in here on their way back to base. That saves our customers time and money, maintains the value of their cranes and also protects the environment.
How does the new repair centre affect the repair process?
Andreas Leicht: In general, we decide where a crane should be taken for repair on the basis of capacity, the complexity of the damage and the size of the crane. Some cranes require repairs which aren’t technically possible at other sites or require a really large volume capacity and resources. These are now brought from all over the world to us at Ehingen-Berg, even though our focus here is on customers in Europe.
And some cranes are also repaired outside Ehingen...
Harald Hummel: That’s true, we have two other timetested repair and service sites in Germany at Oberhausen and Alt-Bork. We also have service outlets all over the world. We have a presence in all our main markets, for example in the USA, where we recently opened another repair workshop in Newport News – and we are still striving to improve our global service.
Andreas Leicht: It’s not always necessary to deliver the complete crane for repair. After initial assessment and inspection by our specialists on site, sometimes we are able to repair just specific components and parts.
Bernd Rechtsteiner: Since early summer, we have also had 20,000 square metres of storage space very close to the port in Bremerhaven where we can store part-exchanged large cranes or parts of them temporarily. When we resell them, we ship them directly from there. That helps to prevent “crane tourism”, which relieves the strain from both the roads and the environment. And it also means that we have reduced transport costs for our customers.
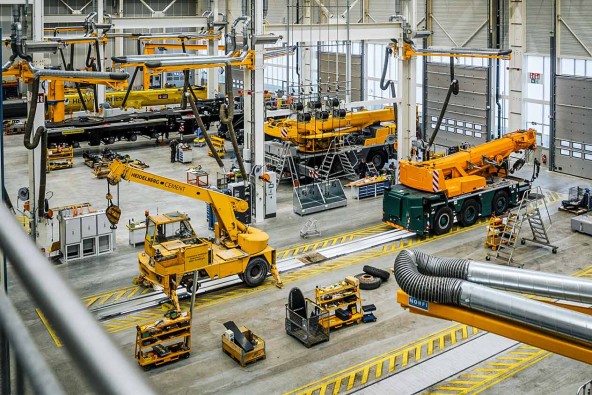
Another new feature is the internal restructuring of the repair centre from Production to Customer Service within the Sales Department. How did this come about?
Harald Hummel: At Customer Service, we have a direct line to our customers. That makes the repair process significantly easier and faster for everybody concerned by reducing the number of internal interfaces. For repair work after accidents, too, it is a massive benefit that the repair centre is now actually part of sales. Our crane experts can provide our customers with extensive advice. The preparation of reports often takes a great deal of time during which the cranes have to be stored. We can now take our time without obstructing production processes.
- Area: 7.3 ha
- Shed: 200 x 60 x 24 m | 120,000 m²
- Photovoltaic system and roof greening: 135 kwP
- 64 employees
- Customer and used cranes per year: Around 220
Bernd Rechtsteiner: It also means that the customer has time to talk to us and decide whether the crane should be repaired or whether he would prefer to use it as partexchange. If the customer buys a new Liebherr crane, we then take care of all the procedures with the insurance company. That is naturally the most convenient option for the customer.
The used crane market is another important segment for Liebherr. How does the new repair centre affect it?
Bernd Rechtsteiner: We are the largest used crane dealer in the world with 250 to 300 units annually. We are observing a trend that is moving significantly towards large cranes being used in part-exchange. Over the last ten years, we have bought, refurbished and resold more than 130 large machines. And by that, I mean telescopic cranes over 750 tonnes and lattice boom cranes of 350 tonnes and over. At the same time, we have had to increase our manpower for repairs by 24 %. That also meant that we had reached the limit of what the old repair shed could offer. The new repair centre will deliver major relief in this respect. Used cranes open up completely new markets for us. Used machines are quickly available and also cost less than new cranes. Quality, lower prices and immediate availability as well as sustainability are some major arguments in favour of buying a used crane. The first three large cranes we accepted in part-exchange have already been refurbished at the same time at the new repair centre and delivered to new customers. These cranes will mainly be used in Brazil, Australia and the USA in the wind industry. And we plan to significantly expand this segment in the future. And for that reason, we’d like to appeal to our customers: Contact us, regardless of whether you want to send us a damaged crane for repair, refurbishment or a used crane in part-exchange.
This article was published in the UpLoad magazine 01 | 2023.