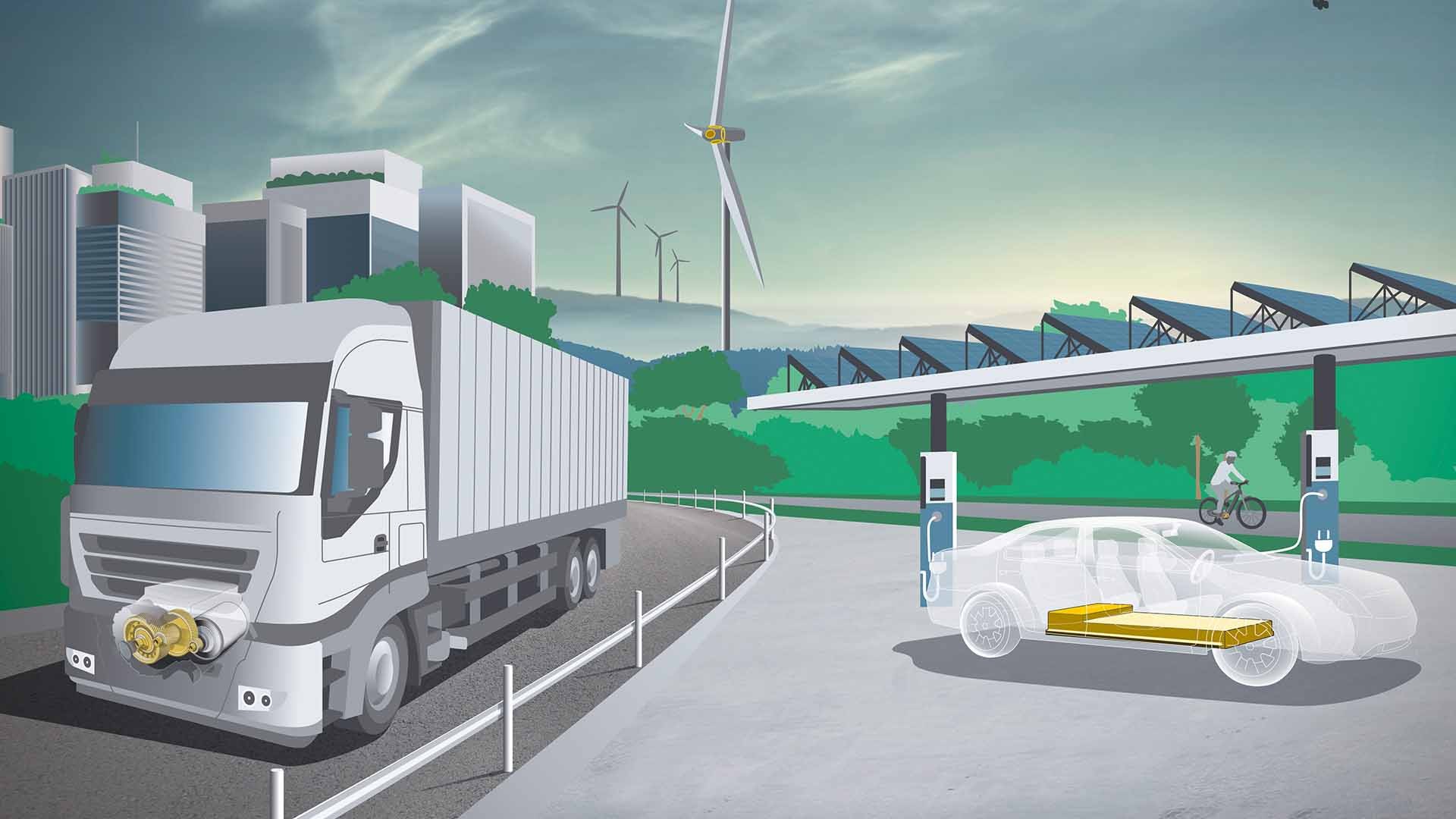
Evotion 2023 | Magazine
Evotion 2023 | Magazine
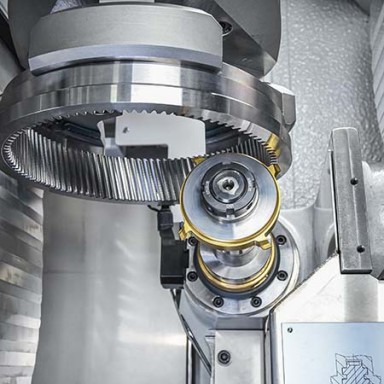
On the new LK 280 DC gear skiving machine from Liebherr-Verzahntechnik GmbH, internal gears can not only be produced efficiently, but also chamfered during the machining process thanks to an integrated ChamferCut device. This opens new opportunities for the industry to manufacture gearboxes with higher power density, giving them a competitive edge in the market for modernized or alternative drive technologies.
Most read
01
When looking for a gear hobbing machine to expand its production, Czech gear and transmission manufacturer Wikov found what it was looking for at Liebherr: on the LC 380 DC, it can now not only hob, but also chamfer gears during the machining process – thanks to efficient FlexChamfer technology. This has significantly enabled Wikov to reduce the machining time for each workpiece.
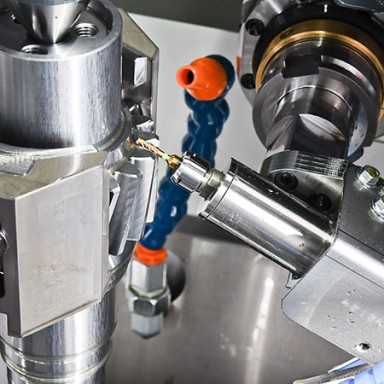
02
A range of different materials and methods are applied in dosing and adhesive bonding applications for battery pack assembly. Applying heatconducting paste in the battery tray and sealing the battery pack cover demands complete process reliability – any rejects at this stage become expensive. At the test facilities in the Kempten Tech Center, Liebherr-Verzahntechnik GmbH tests the automation for adhesive bonding and dosing applications and, from a single source, offers customer-specific applications providing process reliability.
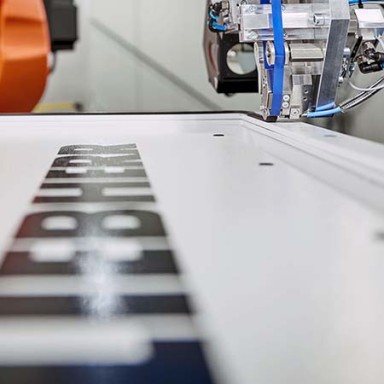
03
In future, generating grinding can also be used under certain conditions to produce double helical gears. This means Liebherr-Verzahntechnik GmbH is expanding its range of processes for hard-finishing for this gear type to meet the highest quality requirements. Compared to established processes such as profile grinding or hard milling, generating grinding is much faster and therefore also provides an interesting alternative from a commercial perspective.
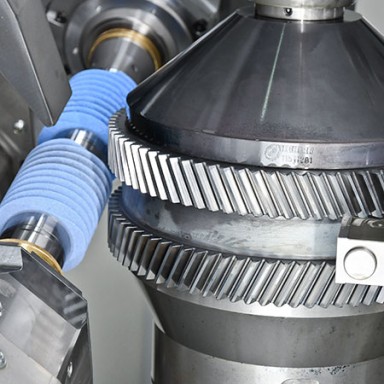
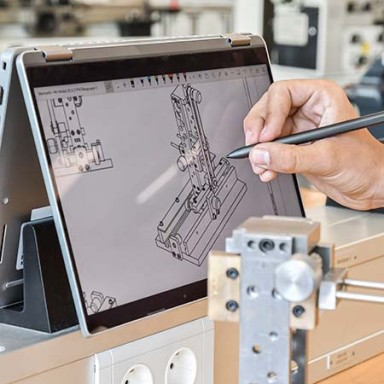
Skilled trades practice with an eye to the future
This year‘s industrial mechanics training graduates at Liebherr-Verzahntechnik GmbH are the second year to have completed all of their training entirely digitally. The future-oriented training model combines the advantages of digital technology with skilled trades practice and has been so successful that it is being extended to the electronics training. The company owes this to its trainer team‘s energy and willingness to experiment, the support from the IT department and the commitment of the apprentices.
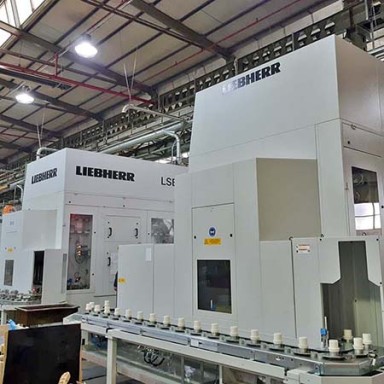
Liebherr machines at Italian job shop Zanetti
Italian contract gear cutting company Zanetti uses gear shaping and gear hobbing machines from Liebherr to manufacture gears and shafts. Machine reliability is the key factor here. But it‘s not just the machines that are reliable: right from the outset, the collaboration between the two companies was characterized by reliability and mutual trust. This has not changed to this day.
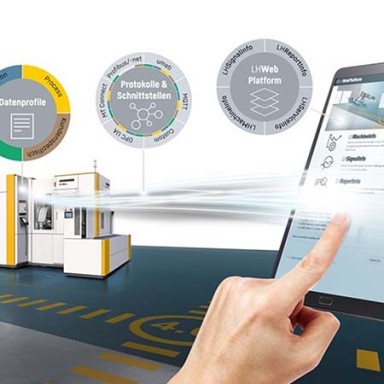
Psst, pass it on: Industry 4.0 made easy through retrofitting
How can you generate data from older gear cutting machines, which are needed for the processes of Industry 4.0? Liebherr has the answer, because the vast majority of digitalizing products found in gear technology can be retrofitted without a problem.
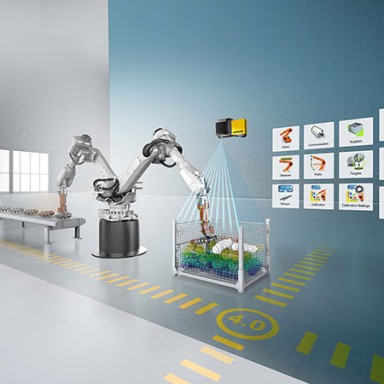
Bin picking software LHRobotics.Vision at Swiss integrator Wick AG
Wick AG, a leading integrator of robotics systems in Switzerland, was instantly so impressed by Liebherr’s bin picking software that they added it to their portfolio and they are exclusively distributing the software in Switzerland. The open concept of LHRobotics.Vision enables a flexible combination of camera systems and robots from different manufacturers, while also being intuitive and extremely easy to operate.
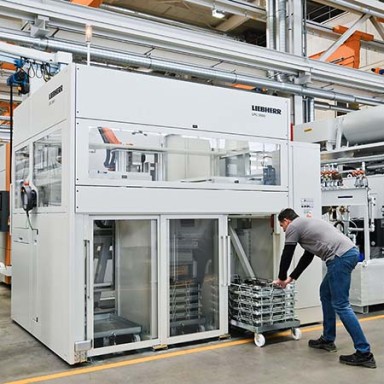
Virtual commissioning saves time and minimizes risk
The virtual commissioning of a palletizing cell with automatic loading of a gear skiving machine significantly shortened the project duration at a transmission manufacturer. The preliminary simulation via a “digital twin” helped save time and costs during the actual commissioning and ensured planning reliability for the start of production.
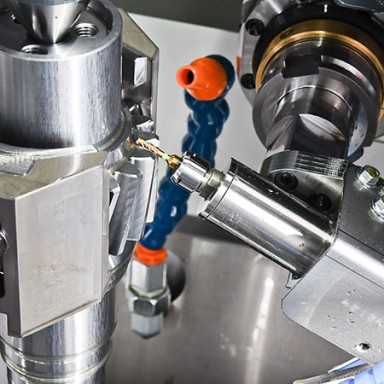
Wikov optimized manufacturing thanks to gear hobbing and FlexChamfer
When looking for a gear hobbing machine to expand its production, Czech gear and transmission manufacturer Wikov found what it was looking for at Liebherr: on the LC 380 DC, it can now not only hob, but also chamfer gears during the machining process – thanks to efficient FlexChamfer technology. This has significantly enabled Wikov to reduce the machining time for each workpiece.
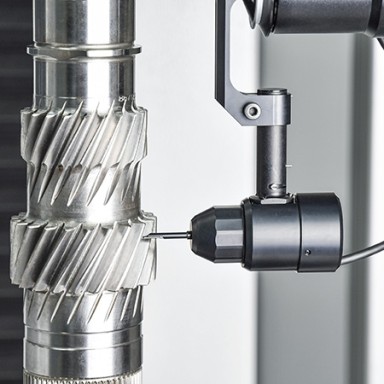
Liebherr measuring technology for e-mobility
Gearboxes for electric vehicles require a particularly high level of manufacturing accuracy for the gears which are used. The waviness and roughness of gear surfaces are important parameters in this. So Liebherr-Verzahntechnik GmbH have further developed their WGT measuring instruments and fitted them with the relevant features. The first of these instruments are already being used by an e-vehicle manufacturer in China.
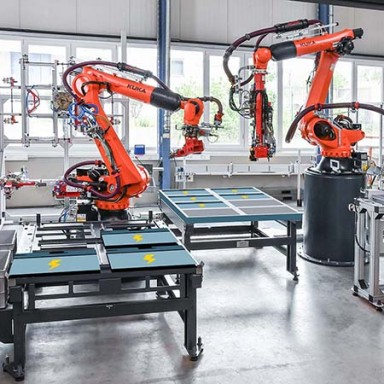
Recycling battery components from electric vehicles
The increasing prevalence of battery-electric vehicles leads to questions about the environmental footprint of vehicle batteries, but also about the safety and availability of raw materials and therefore the competitiveness of the German and European industry. In this context, local battery recycling and the recycling of raw materials is an important building block for the European circular economy. Up to now, however, the disassembly of the battery system has been complex and expensive as the separation of the components is usually done manually. To combat this, Liebherr-Verzahntechnik GmbH is developing strategies and processes for the automated disassembly of high-voltage battery systems and is a partner in the research project "ZIRKEL", funded by the German Federal Ministry of Research and Education (BMBF), which explores the entire circular economy of traction batteries.