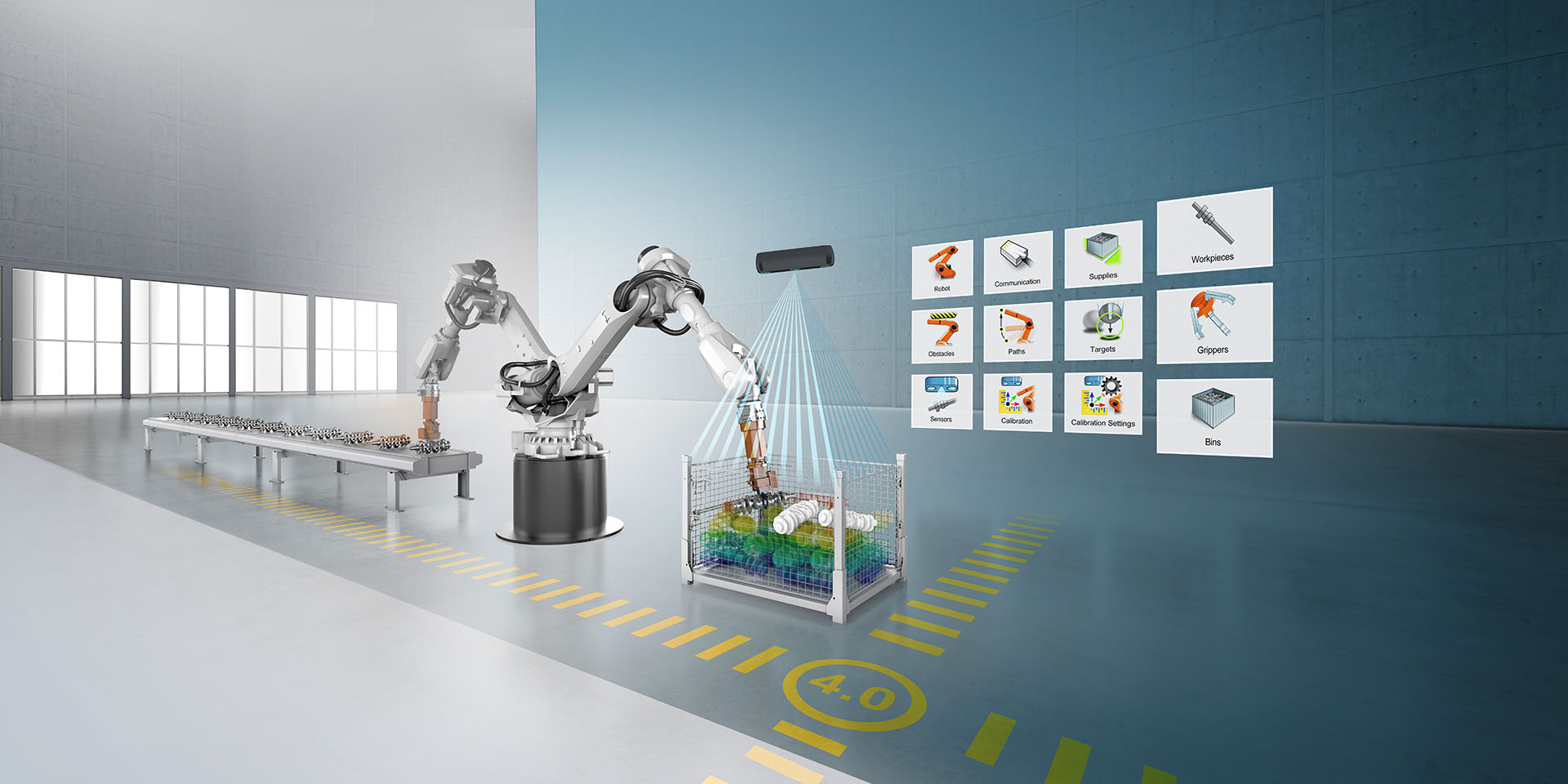
Robot vision technology packages - LHRobotics.Vision
An eye for detail
The technology package
The technology package includes LHRobotics.Vision Software, which makes both precise object identification and selection and collision-free part withdrawal possible. Optionally, the software can also manage robot path planning up to the deposit position. An additional project-based vision system is required for this application.
Project-based vision systems with numerous image field variants for any application
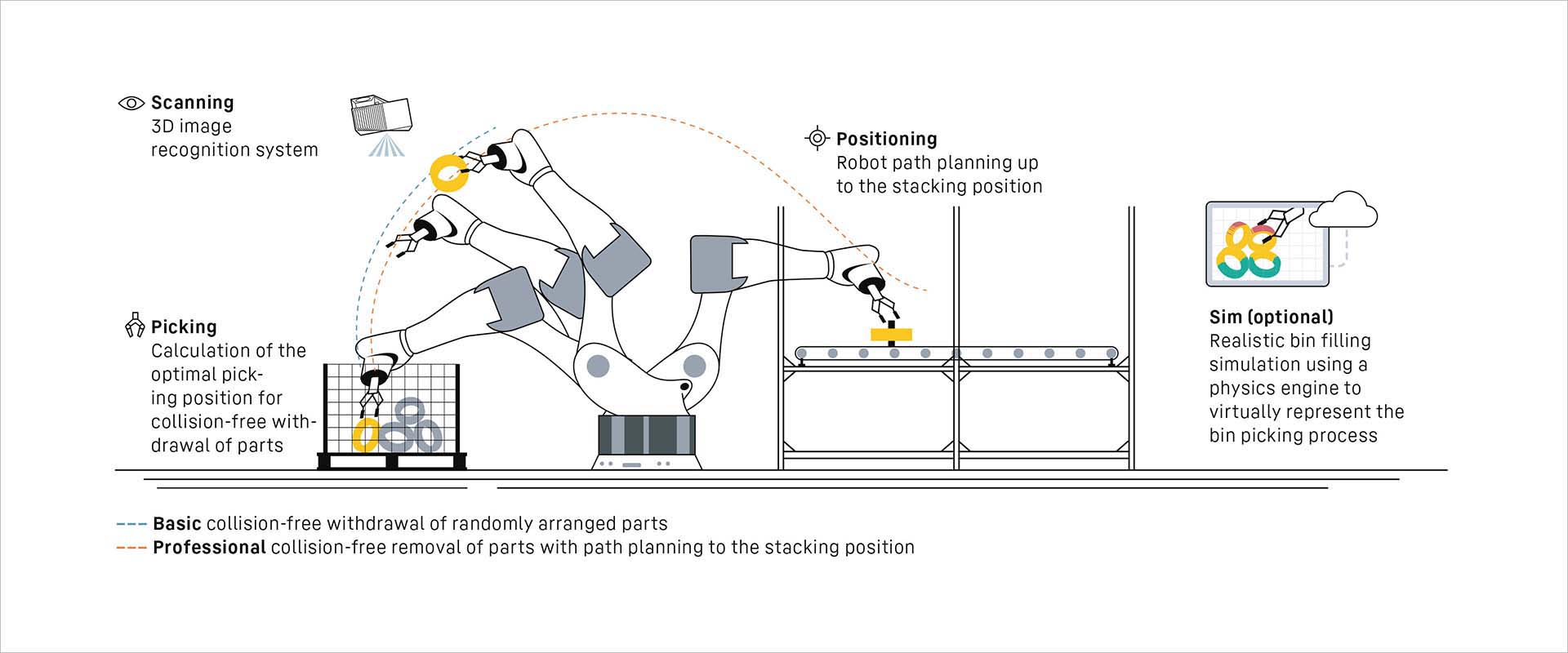
Software
Basic licence
The inexpensive basic licence includes workpiece recording as well as collision-free removal. This version is ideal for applications in which the deposit position and corresponding path planning should not be taken over by the LHRobotics.Vision Software. The collision check is limited to the gripper model and, in this version, the robot’s interfering contour is not taken into account. That makes this variant particularly suitable for flat cases or large grippers that plunge deep into the bin.
With the basic licence, LHRobotics.Vision cab be operated in a limited version. The following functions have been left out of the basic licence:
- Creation of deposit positions and therefore also path planning for deposits.
- Addition of obstacles
- Addition of a robot model
Pro licence
The pro licence offers the complete functional range of the LHRobotics.Vision Software. In addition to the basic licence features, the following data functions are available in this version:
- Creation of a robot model for collision checks
- Creation of deposit positions
- Path planning up to the deposit position
- Input of the complete cell environment for collision checks during path planning
This version is particularly suited to applications in which the deposit position of the workpiece once it has been removed is important for the process sequence
Artificial intelligence lights the way
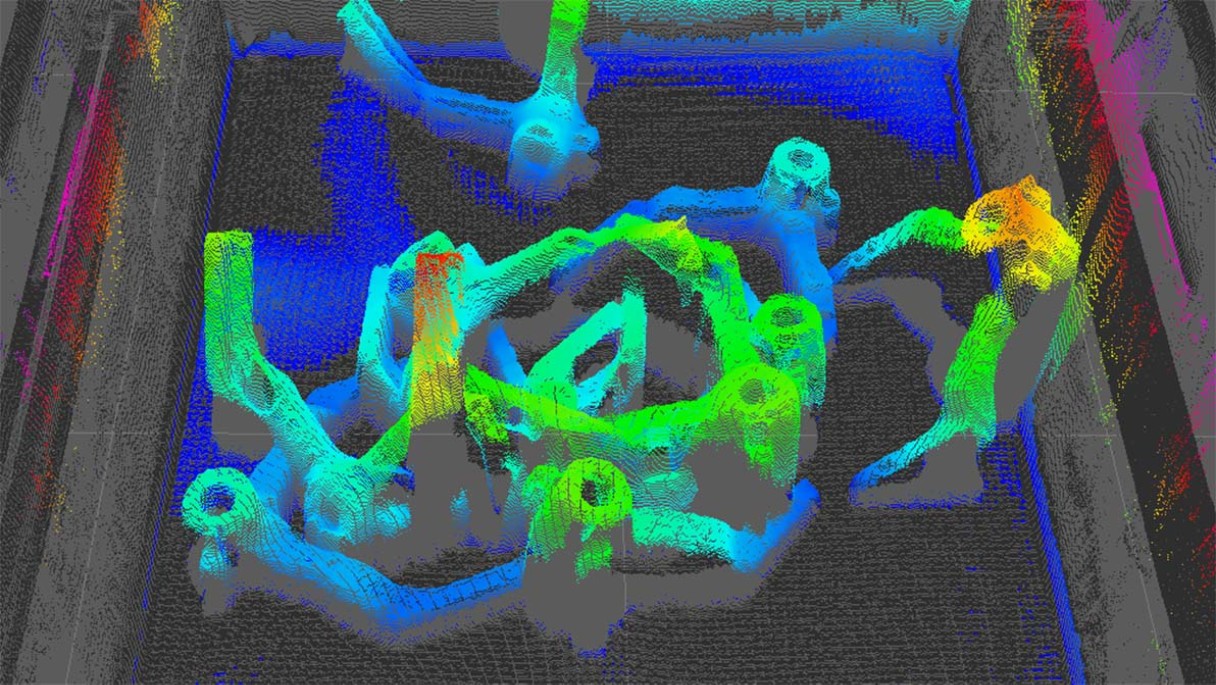
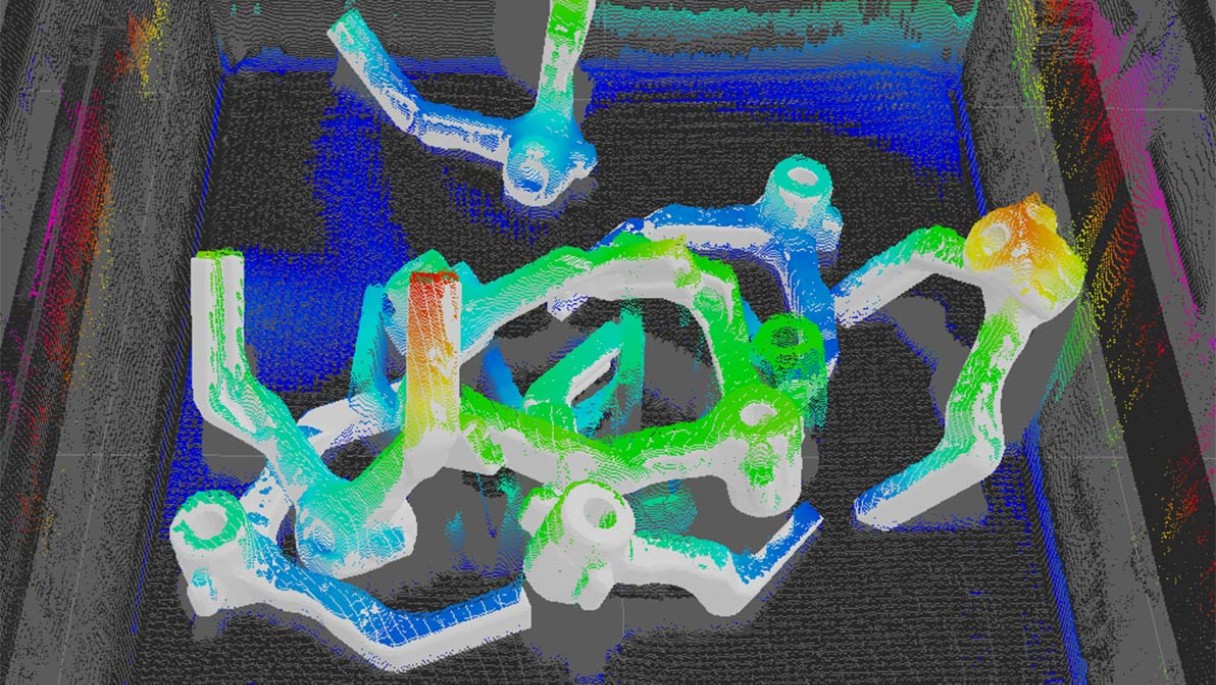
From Version 3.4 on, the optimisation of detection parameters is aided by means of AI.
The user creates a point cloud and classifies it by manually positioning actual workpieces within the point cloud. This points out to the software the areas where the workpieces should be looked for. The software then carries out several automatic scans and independently adjusts the detection parameters. After several iterations, the software determines the optimal settings for recognising workpieces.
Optimisation of workpiece detection with AI-supported point cloud segmentation
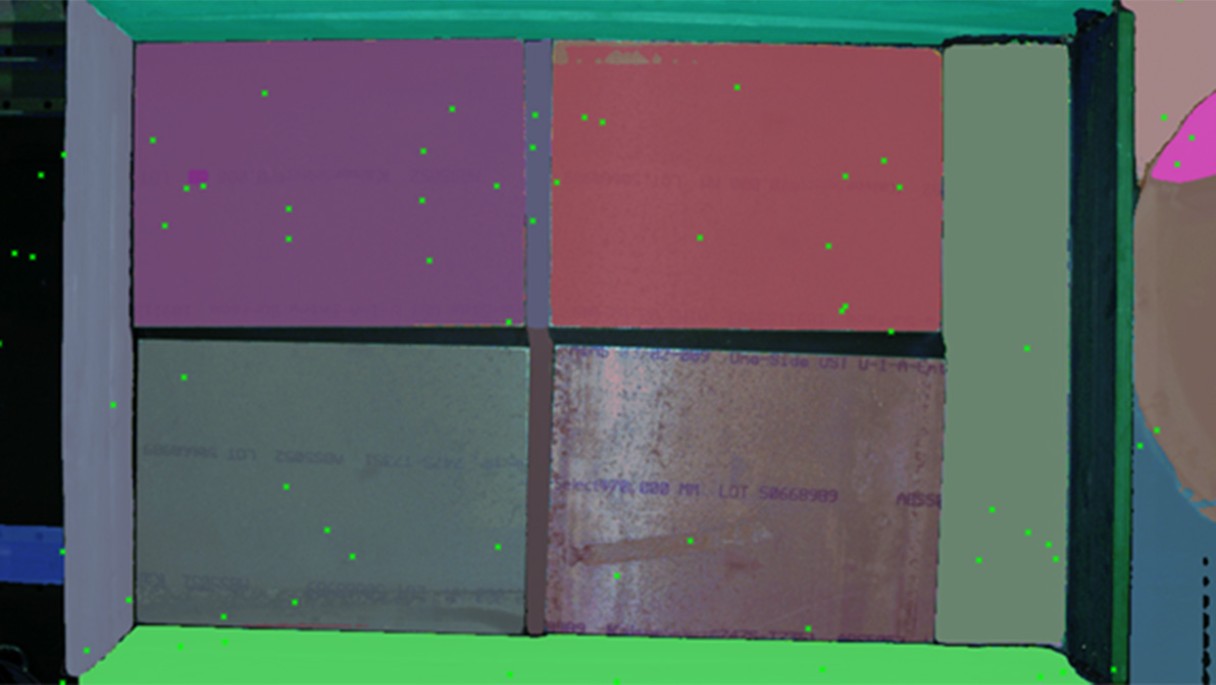
In order to more quickly and precisely detect workpieces, Liebherr also uses AI support for segmentation of the point clouds. With the help of AI, a point cloud is divided into partial segments before workpieces are matched to it. This means that the LHRobotics.Vision Software only looks for the workpieces in the defined areas. Segments that are not assigned to the workpieces, such as walls and the floor of the bin, are removed from the point cloud and ignored.
Liebherr - LHRobotics.Vision - How to achieve bin picking in four steps
By clicking on “ACCEPT”, you consent to the data transmission to Google for this video pursuant to Art. 6 para. 1 point a GDPR. If you do not want to consent to each YouTube video individually in the future and want to be able to load them without this blocker, you can also select “Always accept YouTube videos” and thus also consent to the respectively associated data transmissions to Google for all other YouTube videos that you will access on our website in the future.
You can withdraw given consents at any time with effect for the future and thus prevent the further transmission of your data by deselecting the respective service under “Miscellaneous services (optional)” in the settings (later also accessible via the “Privacy Settings” in the footer of our website).
For further information, please refer to our Data Protection Declaration and the Google Privacy Policy.*Google Ireland Limited, Gordon House, Barrow Street, Dublin 4, Ireland; parent company: Google LLC, 1600 Amphitheatre Parkway, Mountain View, CA 94043, USA** Note: The data transfer to the USA associated with the data transmission to Google takes place on the basis of the European Commission’s adequacy decision of 10 July 2023 (EU-U.S. Data Privacy Framework).Your partner for robot vision technology packages
We are happy to answer any question you have regarding robot visions applications.
Jürgen Groß
Sales Manager for Cells & Flexible Manufacturing Systems, Automation Systems, E-Mobility
Liebherr-Verzahntechnik GmbH
Kaufbeurer Straße 141
87437 Kempten
Germany
Tel.: +49 170 950 09 89
Email
Further information on our vision systems
Read exciting articles from our customer magazines as well as press releases