The impulse generator.
High flexibility
Wet and dry machining
Energy and resource efficiency
Machine concept
The new LC 180 / 280 machine platform allows for a modular design. This means many different technological applications or customer-specific requirements can be implemented. Liebherr gear hobbing machines are optimally customized to the requirements of universal usability. The high-performance gear hobbing machines are productive and manufacture in the highest quality with maximum availability.
- Optimized base frame rigidity thanks to FEM simulation
- Thermosymmetric machine design and integrated temperature compensation ensure consistent high quality
- Fundamentally optimized chip removal system
- High flexibility for various processes:
- Gears, shafts, worm gears
- Cluster gears
- Skive hobbing/finish cutting
- Position dependency
- Milling of special profiles
- Wet and dry machining
- Hook-ready machine with a low space requirement, suitable for easy transfer
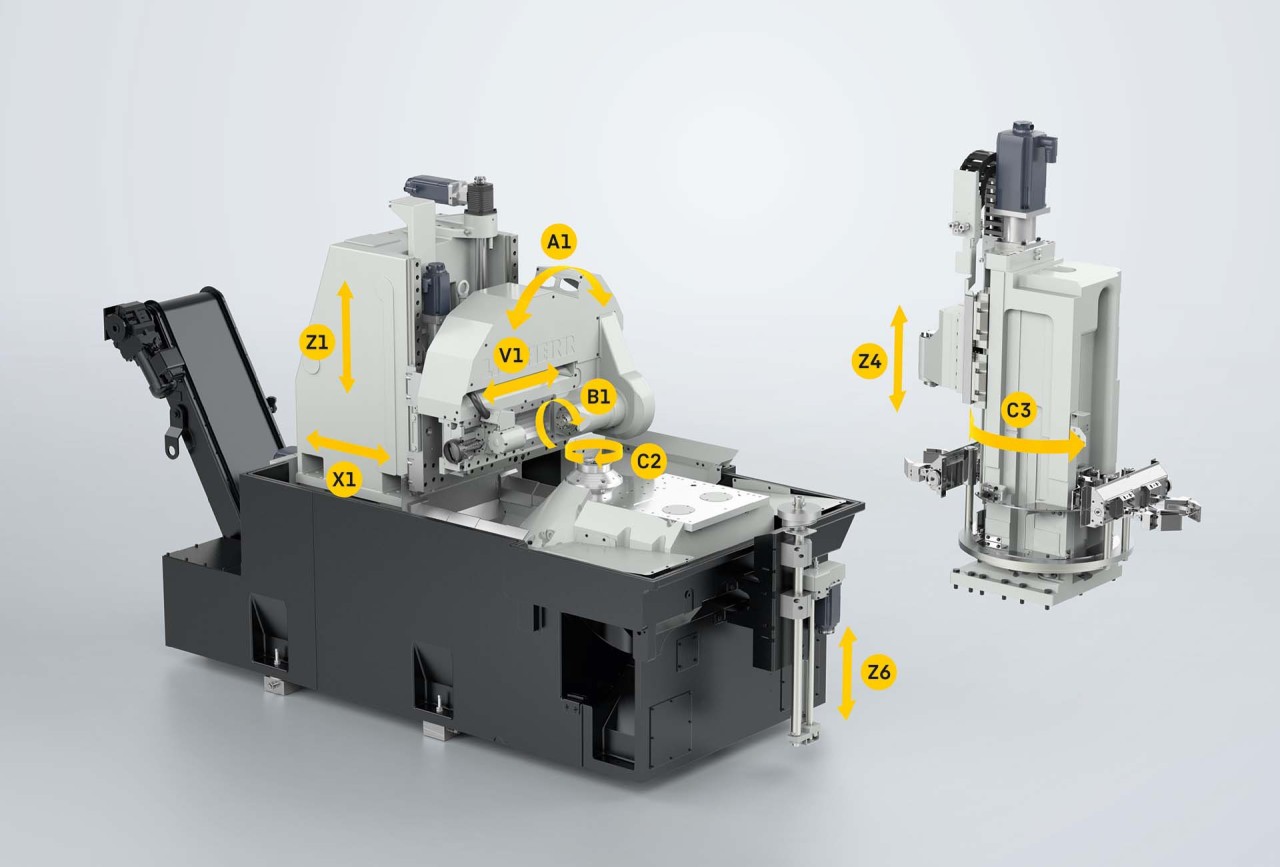
Axes
X1: Radial movement column slide | B1: Rotary movement tool | Z4: Vertical travel counter column | V1: Tangential movement tool | C2: Rotary movement workpiece| C3: Rotary movement ringloader| Z1: Axial travel cutter head | A1: Swivel movement tool
Gear hobbing machine LC 280 α
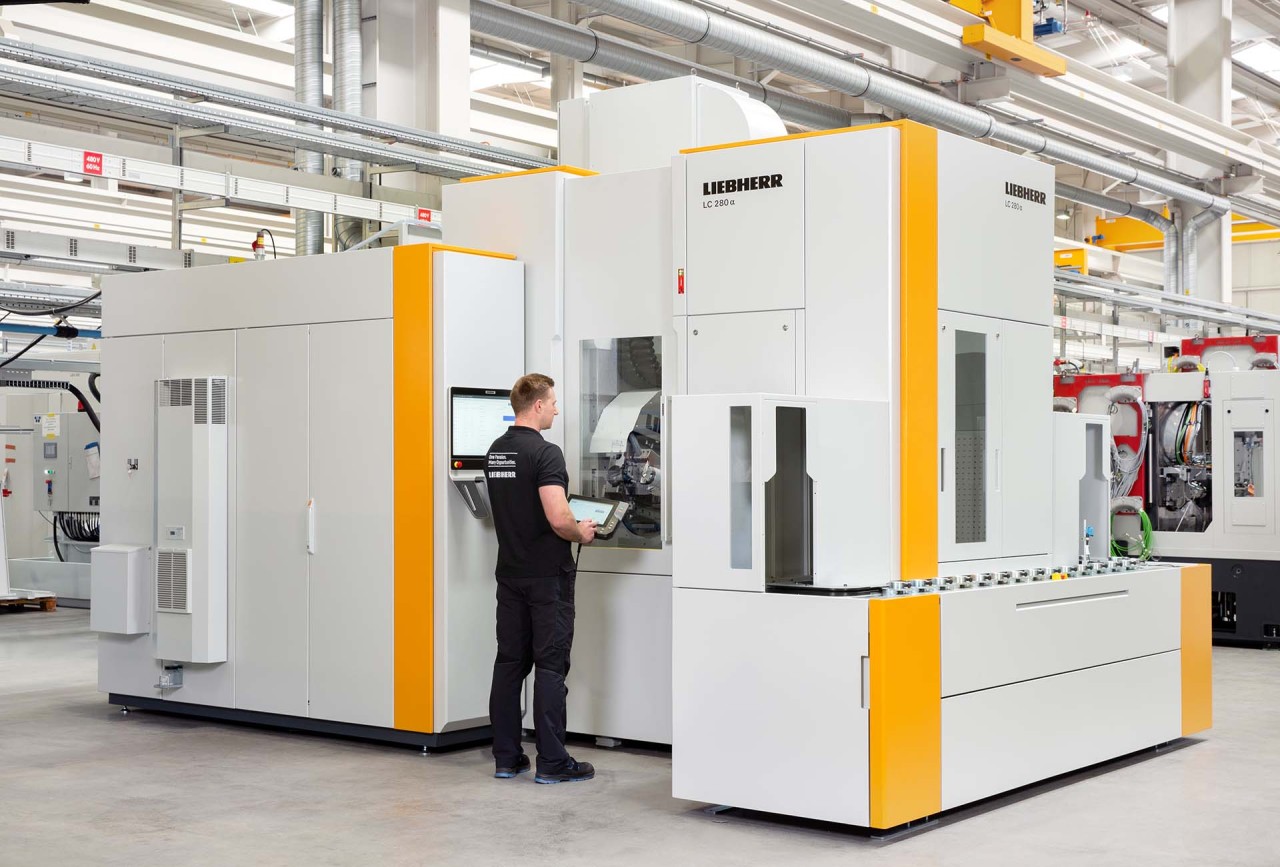
Your entry point into gear cutting
The LC 280 α is the perfect way for getting started with gear cutting. It offers maximum flexibility thanks to a diverse range of workpieces, well-known Liebherr quality, and low machine investment.
Thanks to the reduced scope of options, these machines can be produced and delivered at short notice. The more standardized machine can be manufactured and delivered quicker, which allows you to start with your production sooner. The entry-level model comes with the touch-based LHGearTec user interface and a ringloader concept for loading and unloading workpieces up to 25 kg. For the Alpha machines, Liebherr uses the same high-quality components as for the universal and customized machines.
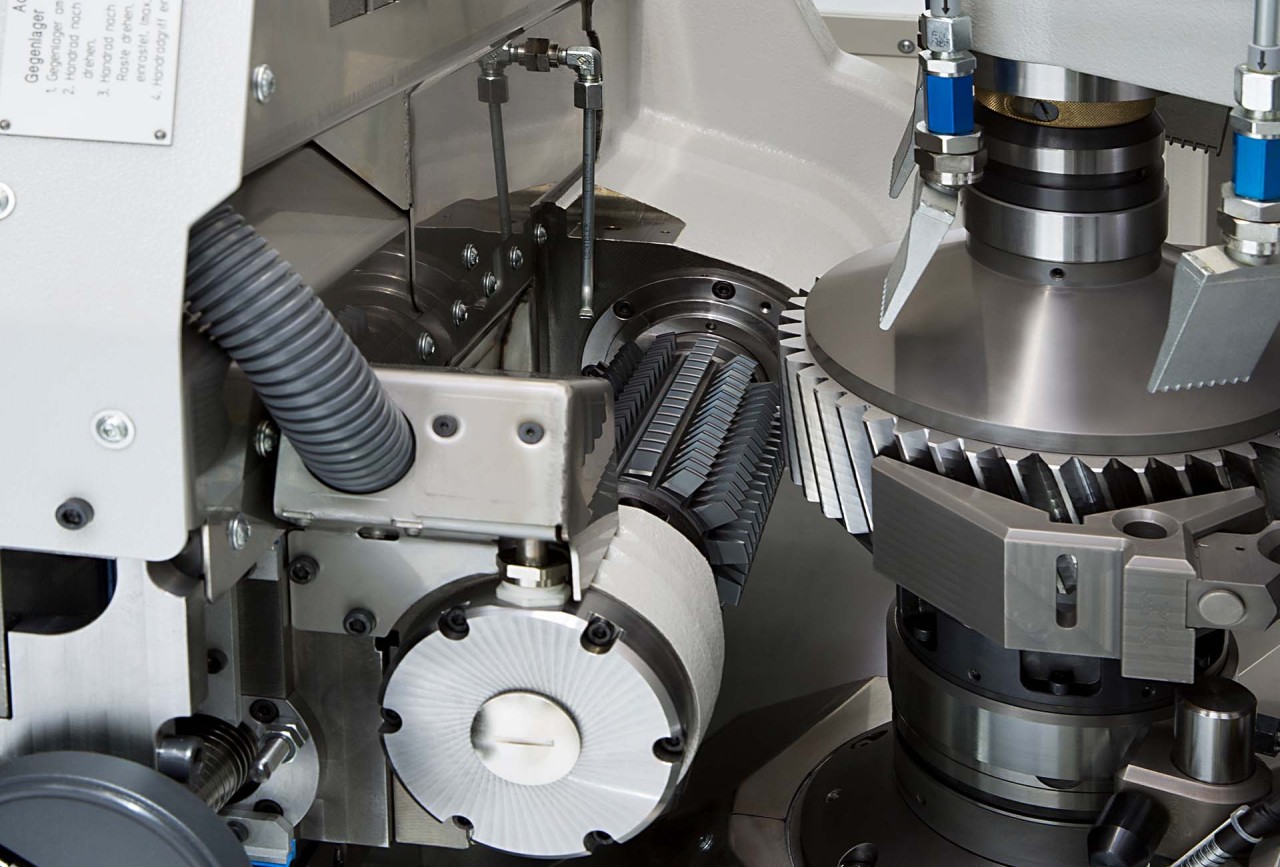
Machine
- Machining workpieces with max. 280 mm diameter and shafts with a length of up to 500 mm
- L-doors for better accessibility
- Thermally stable machine bed
- Wet and dry machining
- High rigidity ensures best machining quality
- Optimized chip removal
- Hook-ready machine for fast installation and commissioning
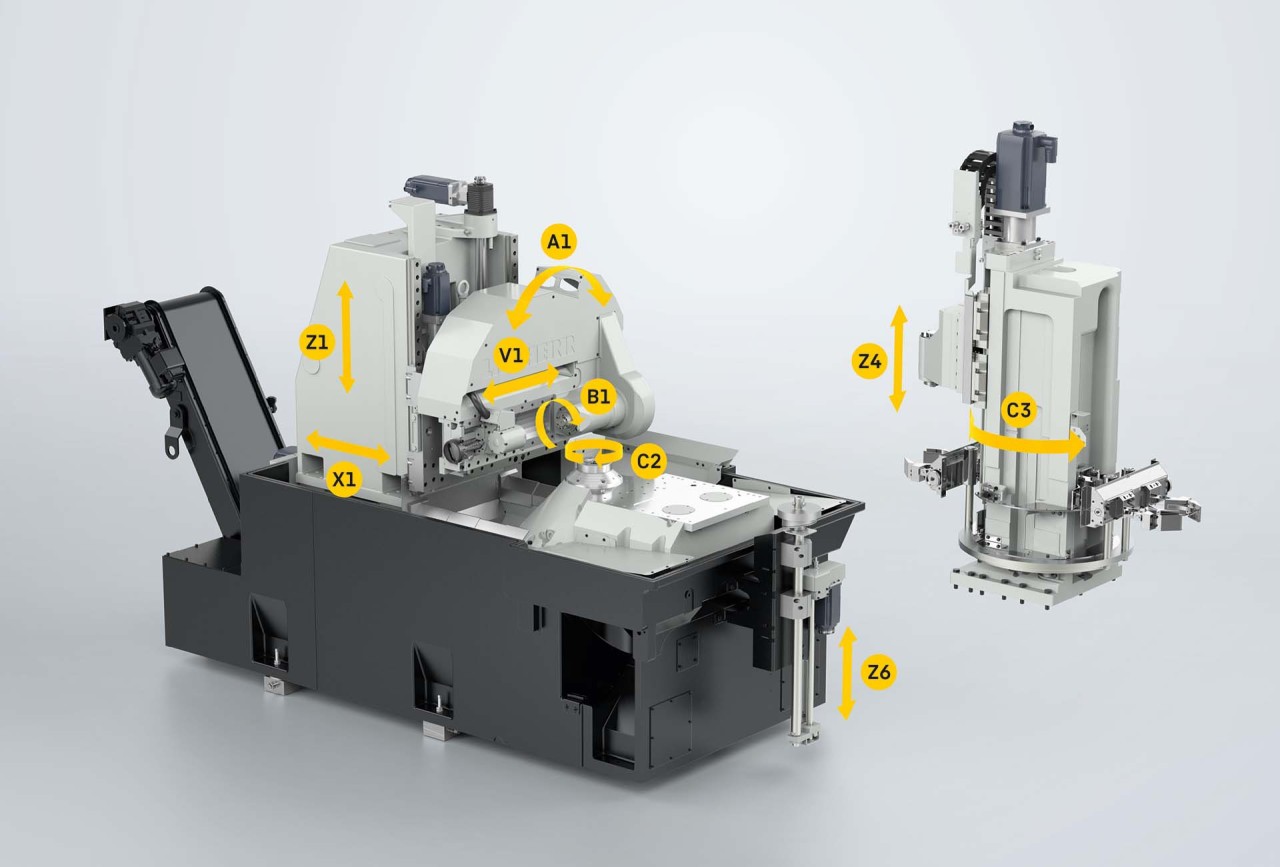
Automation
- Plastic chain conveyor KKB
- Storage capacity 20 workpieces à 25 kg / 30 workpieces à 10 kg
- Suitable for fast ringloader loading (up to 25 kg workpiece weight) for maximum productivity
Axes
X1: Radial movement column slide | V1: Tangential movement tool | Z1: Axial travel cutter head | B1: Rotary movement tool | C2: Rotary movement workpiece | A1: Tilting movement tool | Z4: Vertical travel counter column | C3: Rotary movement ringloader
Gear hobbing machines 180 / 280 (DC)
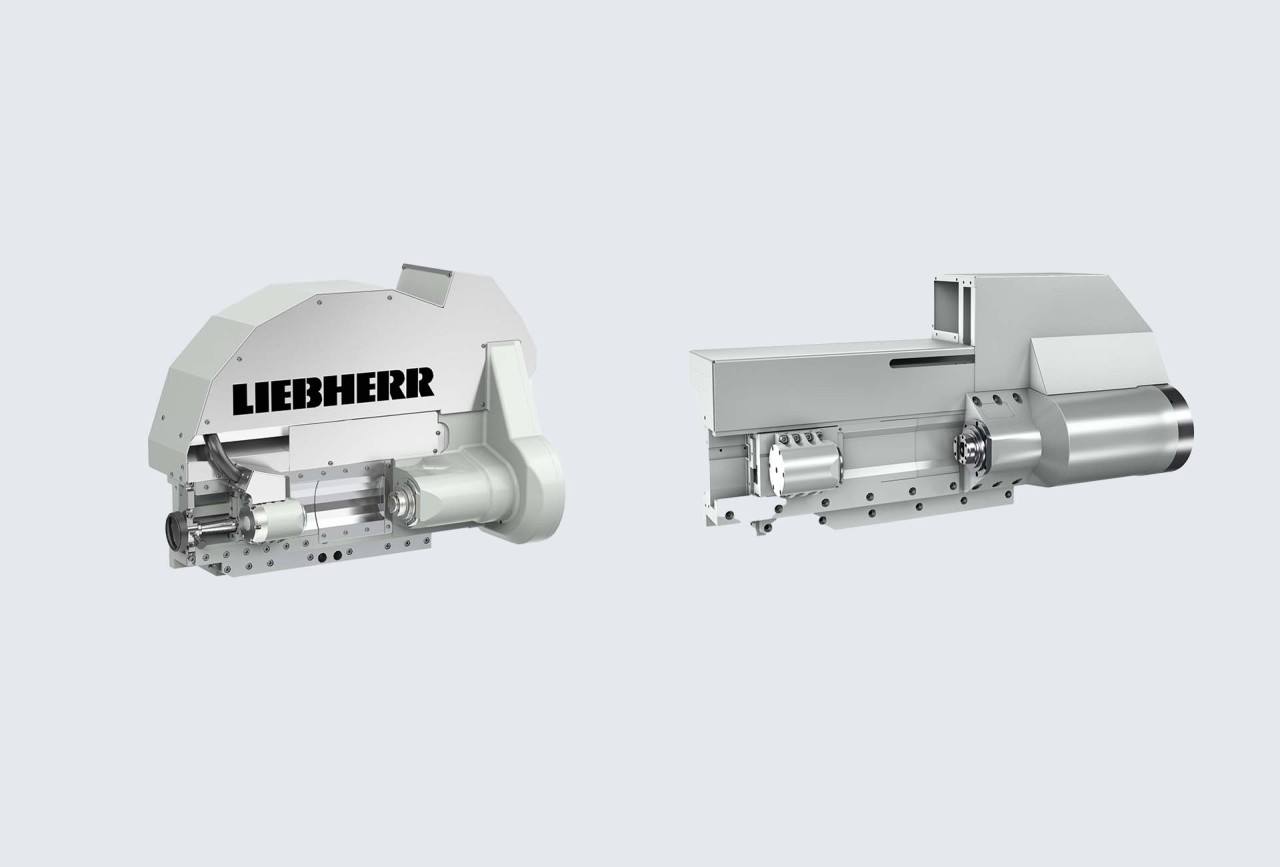
Hobbing heads
Different gear ratios are available for the hob head to cover most high torque and high RPM applications. Hollow shank tapers, steep tapers and straight shank tools are available as the interface for holding the tool. For very high spindle speed requirements, a hob head with direct drive is also available.
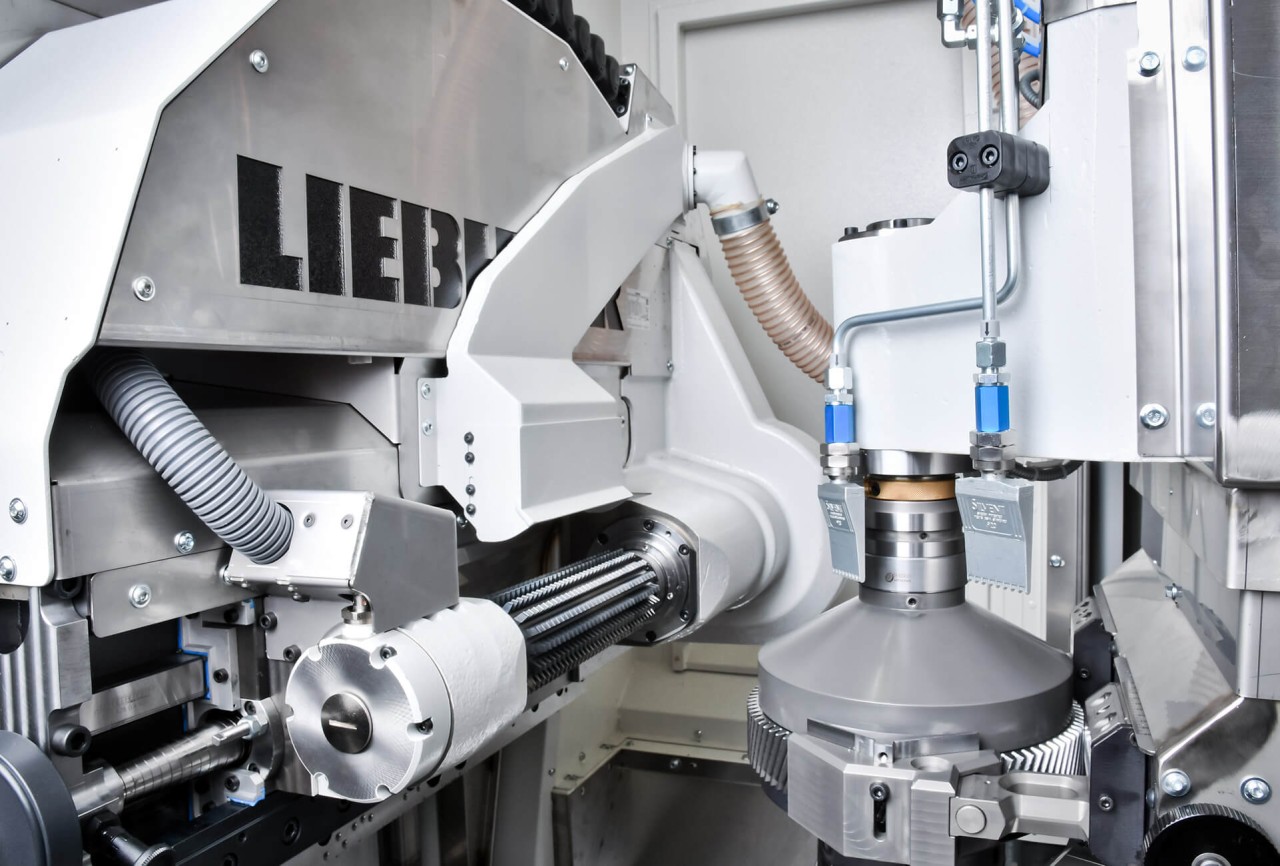
The hob head provides greater flexibility and productivity. Workpieces up to a module of 5 millimeters can be machined. The spindle speed has been increased by 50% to 2,250 revolutions per minute compared to the previous model. At the same time, the shift distance has been extended by 11 % to 200 millimeters, and the maximum tool diameter has been increased by 67 % to 150 millimeters.
- Drive power: 13 kW
- Speed of cutter spindle: 2,250 rpm
- Max. module: 5 mm
- Shift distance: 200 mm
- Max. hob diameter: 150 mm
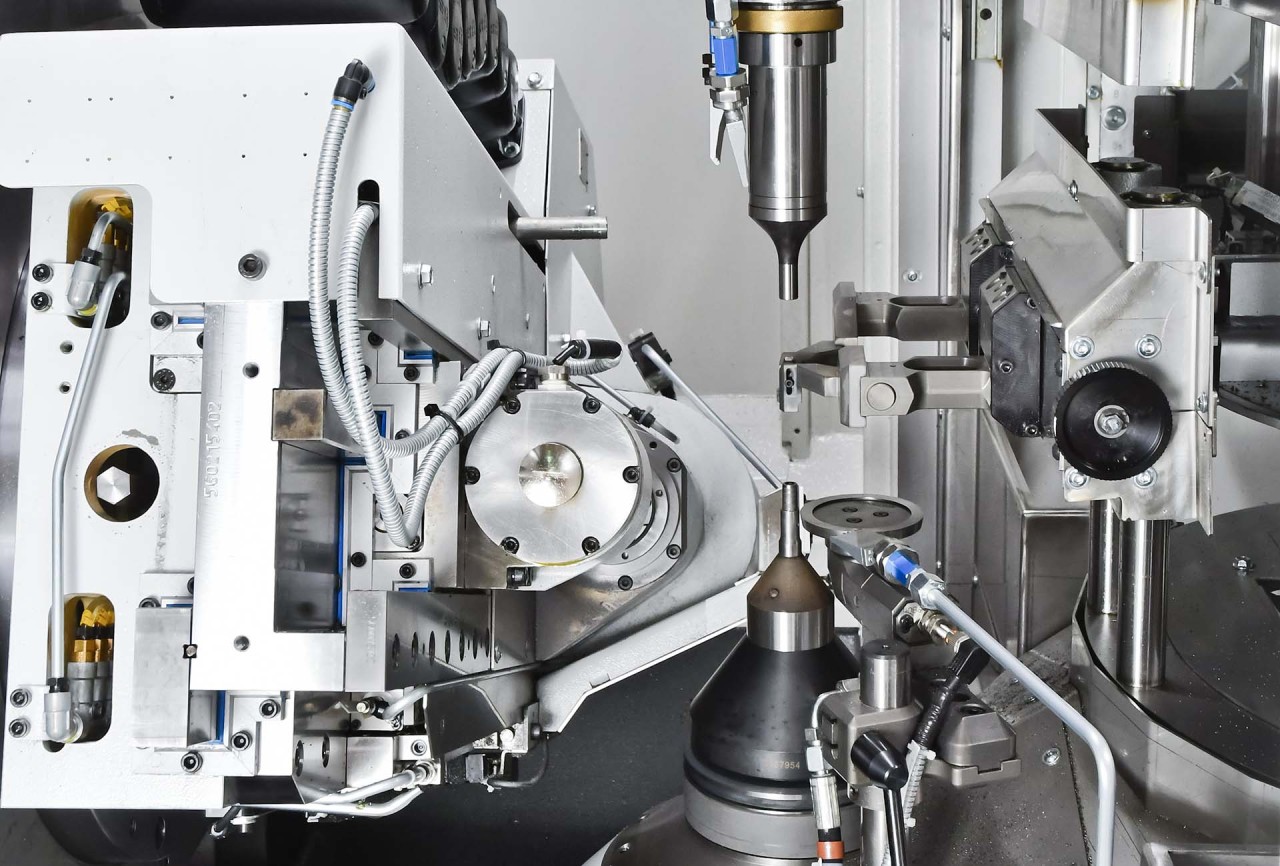
Alongside the default gear cutter head, a directly driven cutter head is also available as an option. The directly driven cutter head features high speeds of up to 6,000 rpm and high drive power of 23 kW. It offers sufficient reserves for future tool developments.
- Drive power: 23 kW
- Speed of cutter spindle: 6000 rpm
- Max. module: 3 mm
- Shift distance: 180 mm
- Max. hob diameter: 90 mm
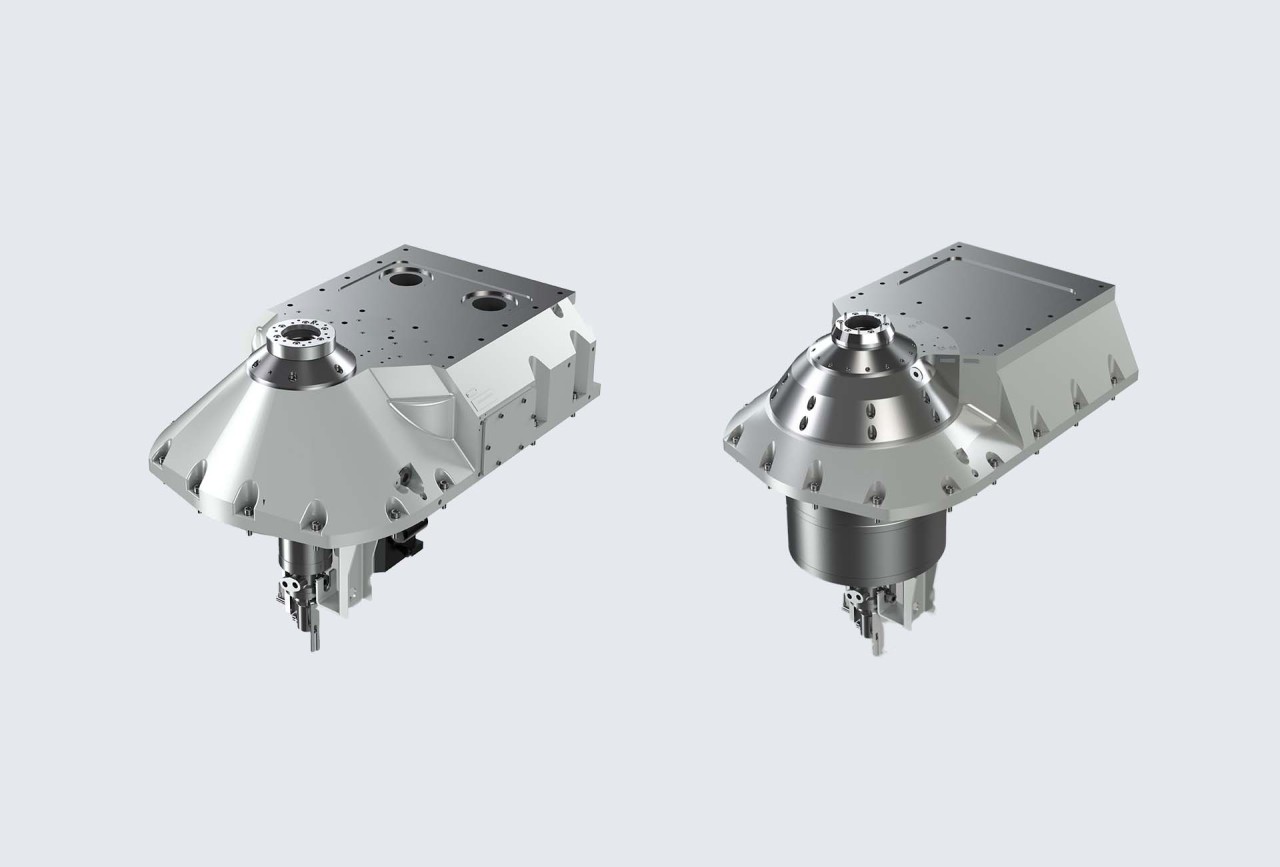
Table drive
For gear manufacturing machining, a workpiece drive with absolutely zero backlash is required. The table drive with spur gears is available when using conventional technology. For high performance cutting (HPC) an ultra-dynamic direct drive is available which satisfies all requirements with respect to speed and precision.
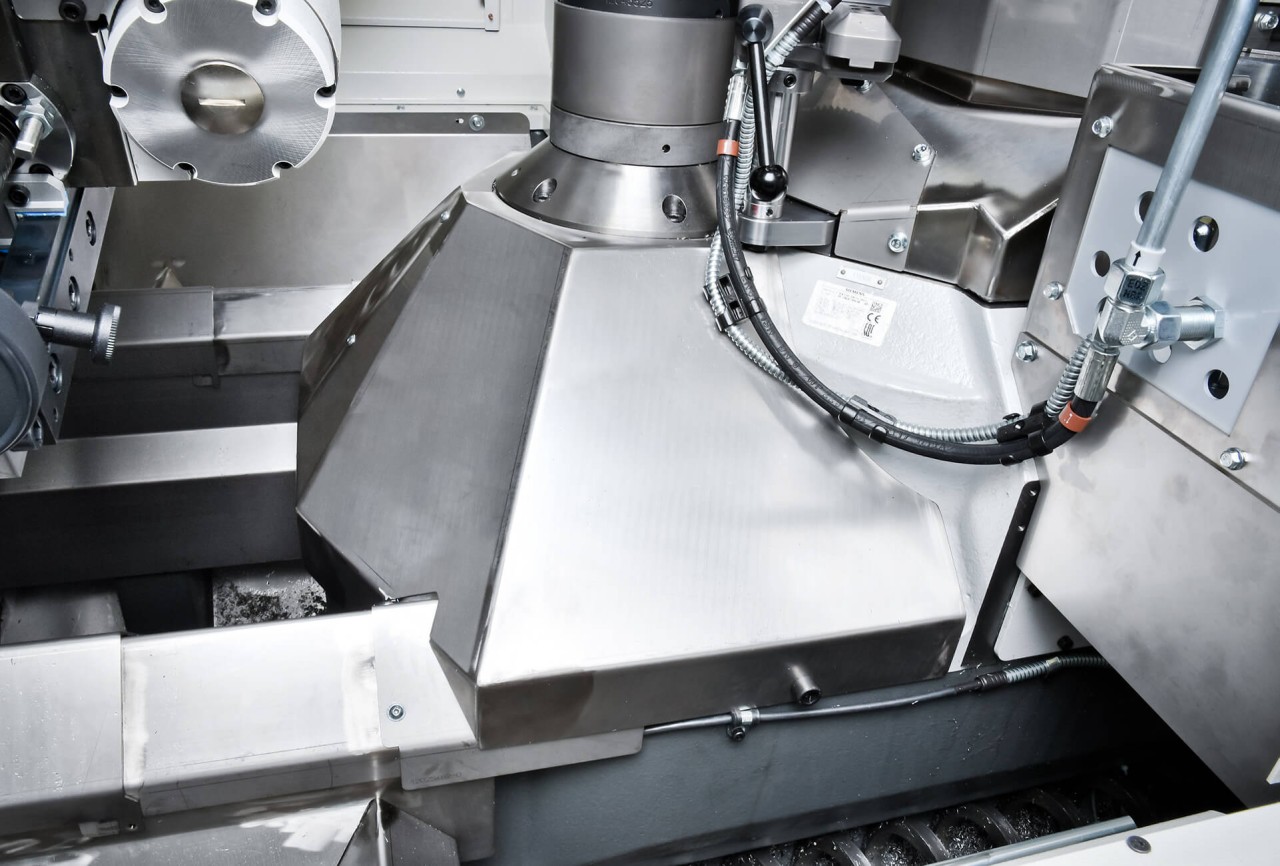
Dry machining with stainless steel covers
Thanks to an integrated complete stainless steel housing (optional), thermal influences that normally occur in dry machining can be minimized. This ensures consistent machining results and exceptionally high process reliability. In addition, chip accumulation can be prevented. The easy and fast cleaning of the machine is another benefit.
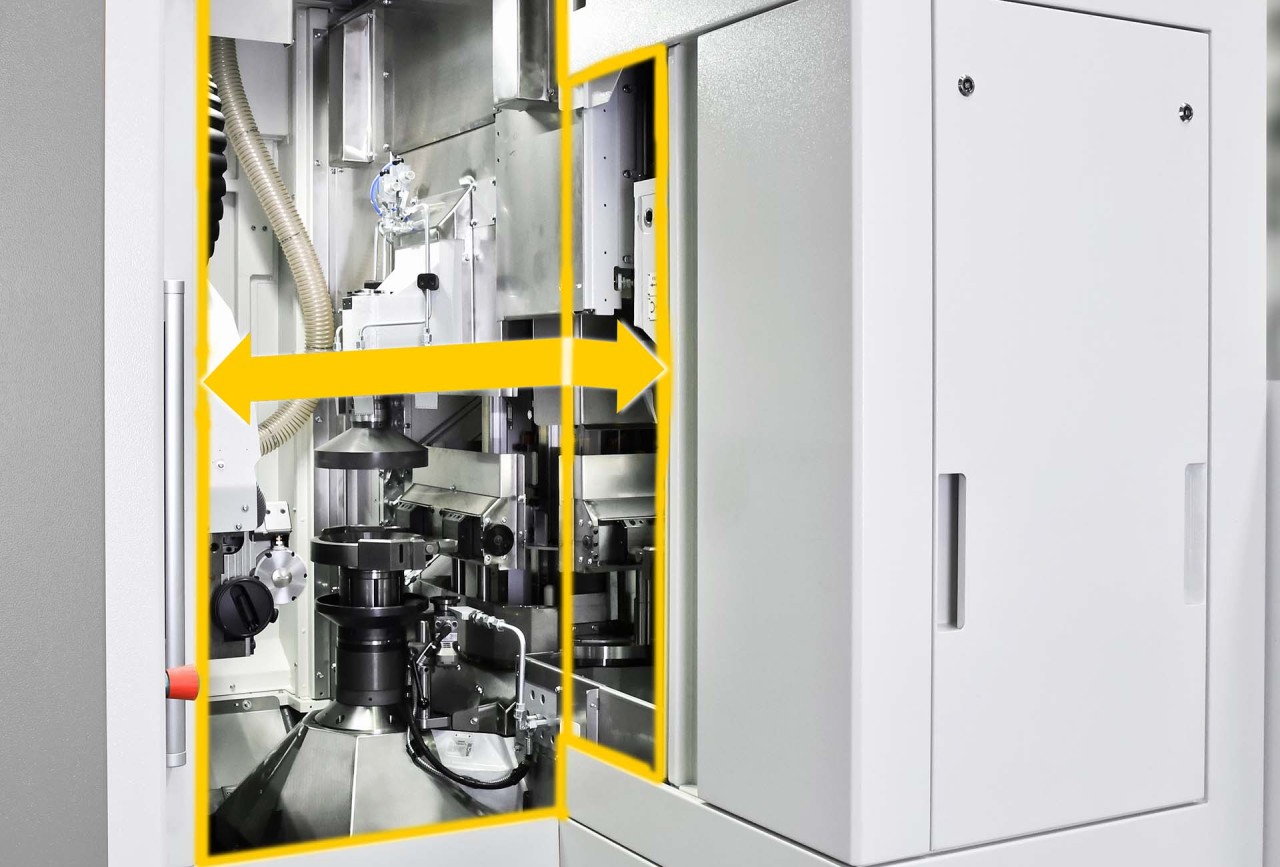
Chamfering during the machining process with ChamferCut or FlexChamfer (LC 180 / 280 DC)
With the LC 180/280 DC, the ChamferCut device is integrated on the operator side. This device has been enhanced in terms of user-friendliness. As such, the machine operator has unobstructed accessibility to both machining positions. Chip removal has also been significantly improved. Using the proven Liebherr ringloader concept, the workpiece can be transferred quickly and efficiently between the gear hobbing and chamfering machining positions. Chamfering by ChamferCut or FlexChamfer therefore takes place parallel to gear hobbing. The special feature of the chamfering unit is that it is controlled using 6 CNC axes as standard. Settings or corrections and adjustments for varying lead corrections can be executed quickly and easily using the user-friendly software.
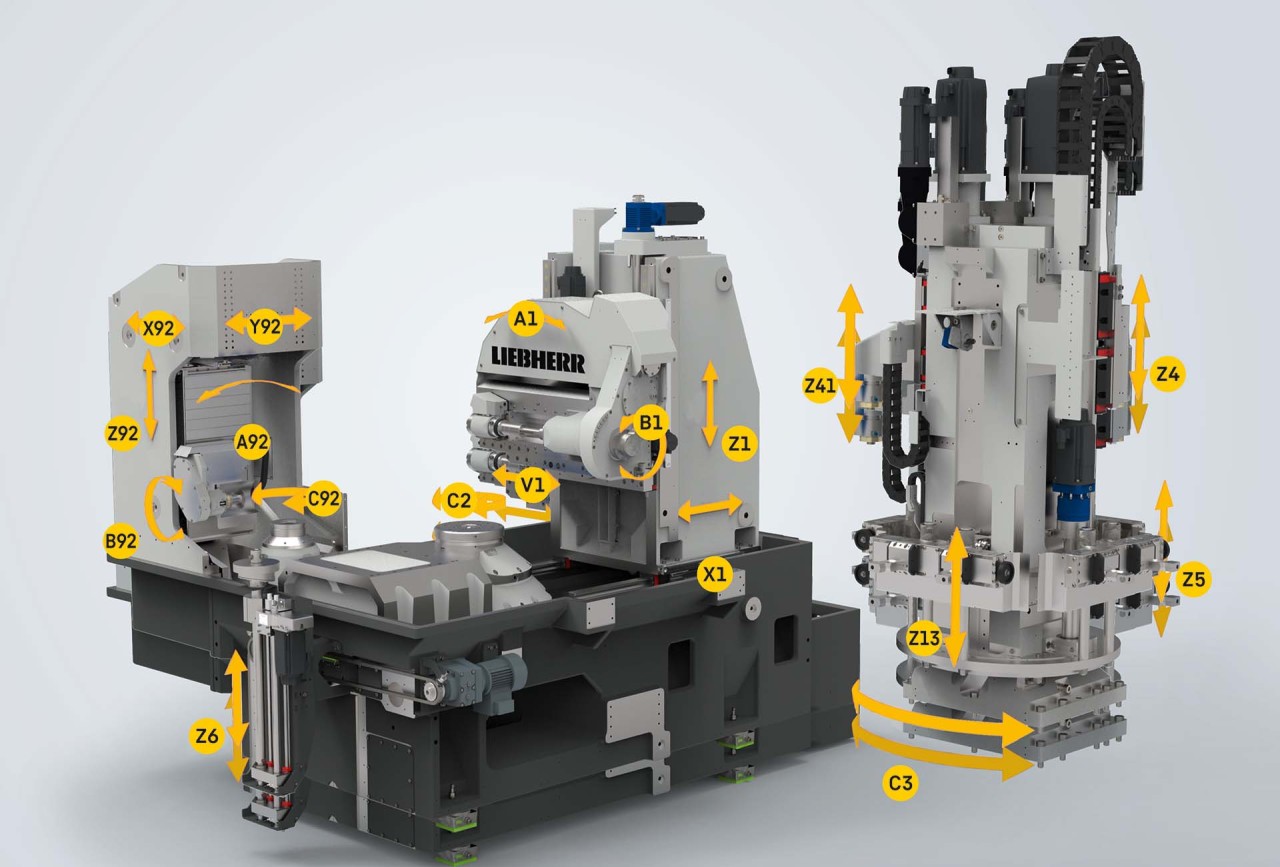
LC 180 / 280 DC with integrated ChamferCut device
Axes
X1: Radial movement column slide | B1: Rotary movement tool | Z4: Vertical travel counter column | V1: Tangential movement tool | C2: Rotary movement workpiece| C3: Rotary movement ringloader| Z1: Axial travel cutter head | A1: Swivel movement tool
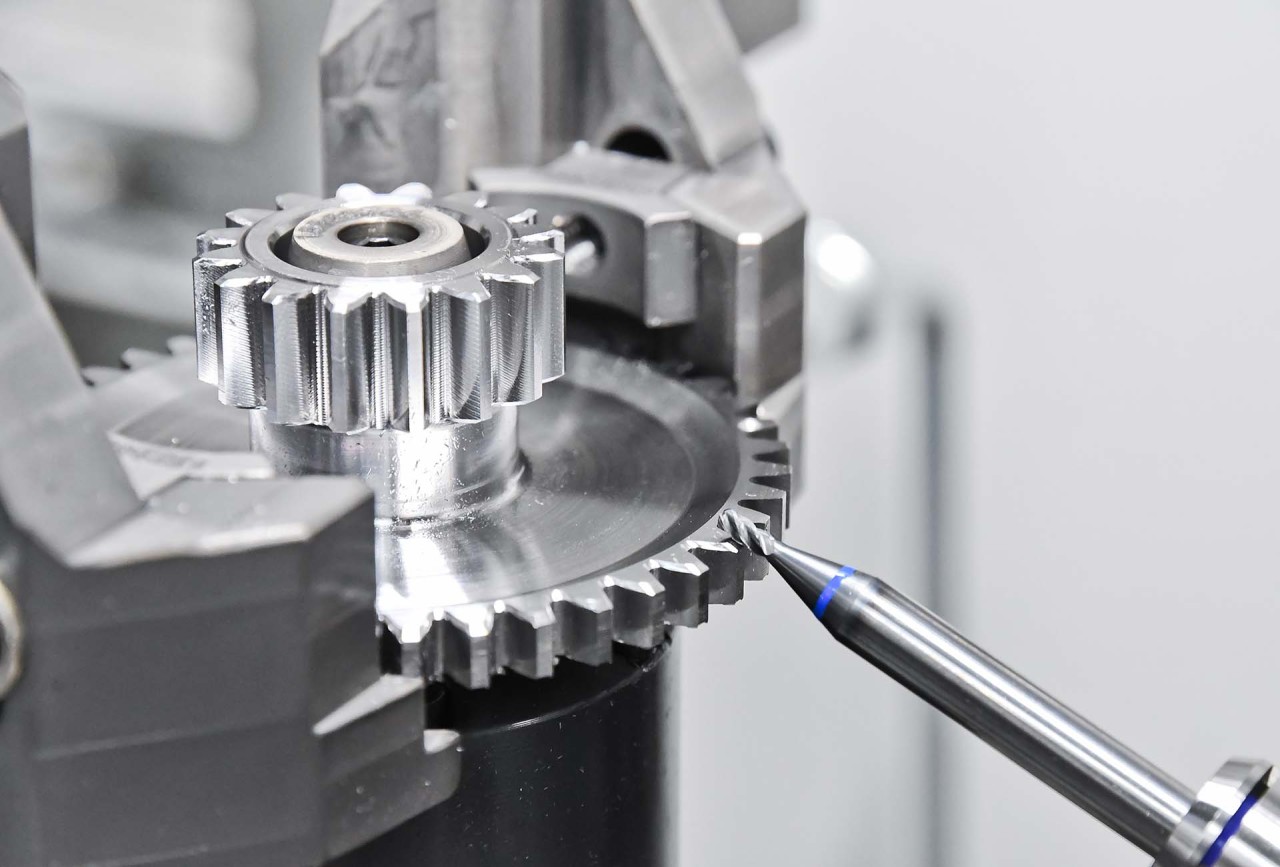
FlexChamfer
As an alternative, we offer the new FlexChamfer technology. The gears can be chamfered quickly and efficiently using a standard milling tool. The movements of the tool are also fully NC-controlled, ensuring high repeatability and chamfer quality. This process is ideal for workpieces with interfering contours or when there is a very large part variance and small batch sizes.
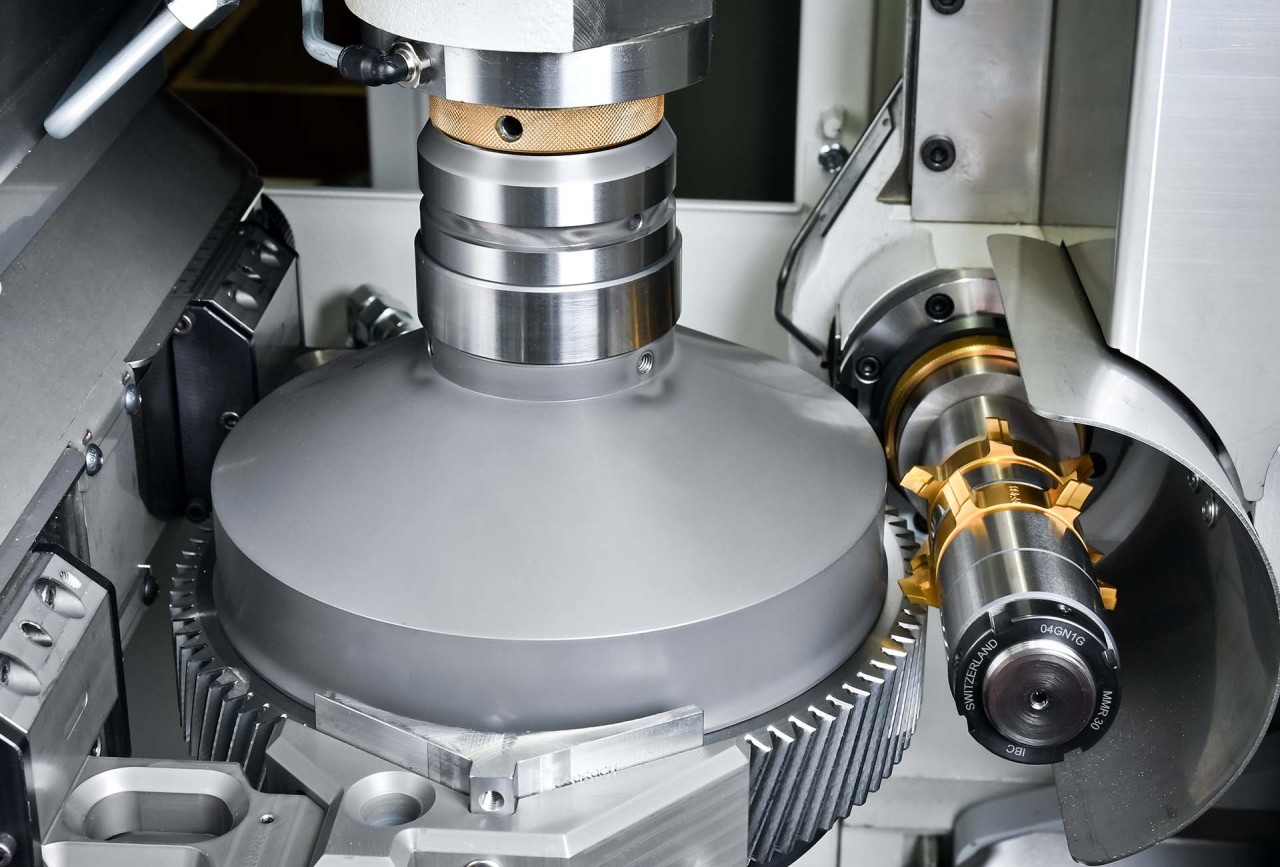
ChamferCut advantages
- Parallel gear hobbing and defined deburring / chamfering
- Dry and wet machining possible
- Precision chamfering geometry
- Highest chamfer quality and repeatability
- No bulging or material deformation
- Tooth root chamfering as standard
- Very long tool life ChamferCut tools can be easily reground 15 to 20 times at low cost
- Lowest tool costs per workpiece compared to traditional processes
- Short amortization period thanks to low tool costs per workpiece
- wide module range from 0.8 to 42 mm
- 2nd cutting during gear hobbing is unnecessary thereby increasing tool life quantity at the gear hob
- Short setup times
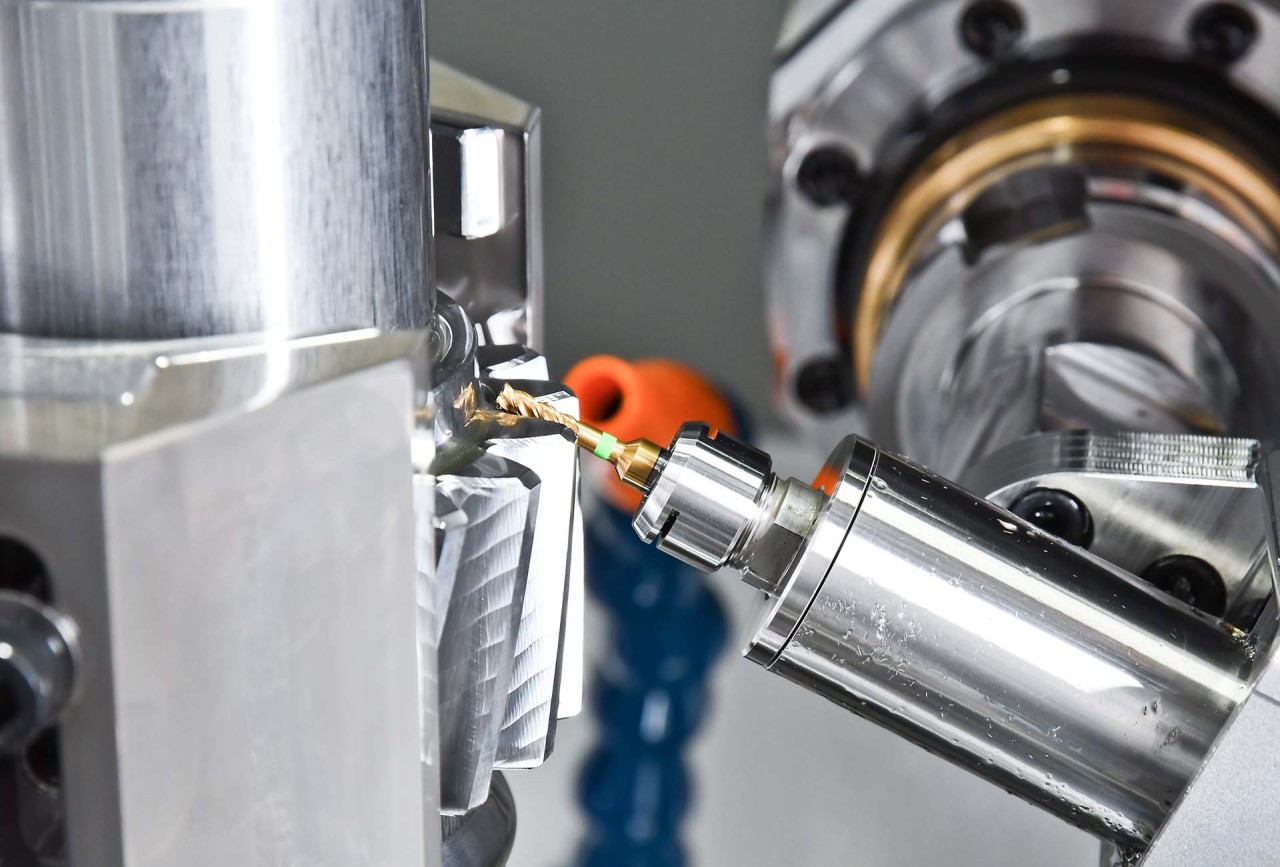
Advantages FlexChamfer
- Flexible and universally applicable
- Ideally suited for workpieces with interfering contours
- Precision chamfering geometries
- Highest repeatability
- Simple NC corrections possible
- Use of standard tools (quickly available from stock)
Technical data
Variants | LC 180 α | LC 280 α | LC 180 | LC 280 | LC 280 DC | LC 280 DC |
---|
Insights
Automation & Features
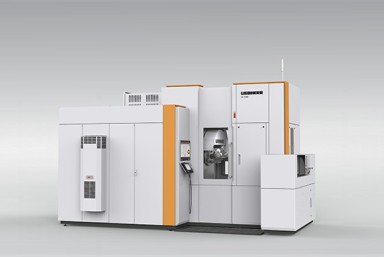
Chain conveyor storage (KSR)
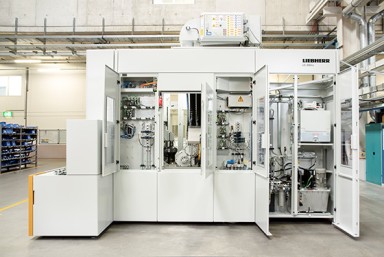
Easy to maintain
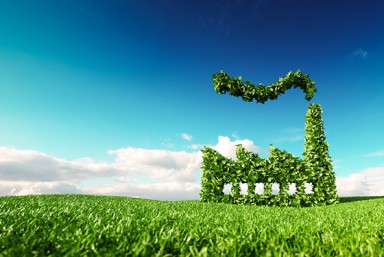
Energy and resource efficiency
- Regenerative drive technology
- Use of efficient control cabinet coolers
- LED lighting
- Coolant supply and
- preparation with speed-controlled pumps