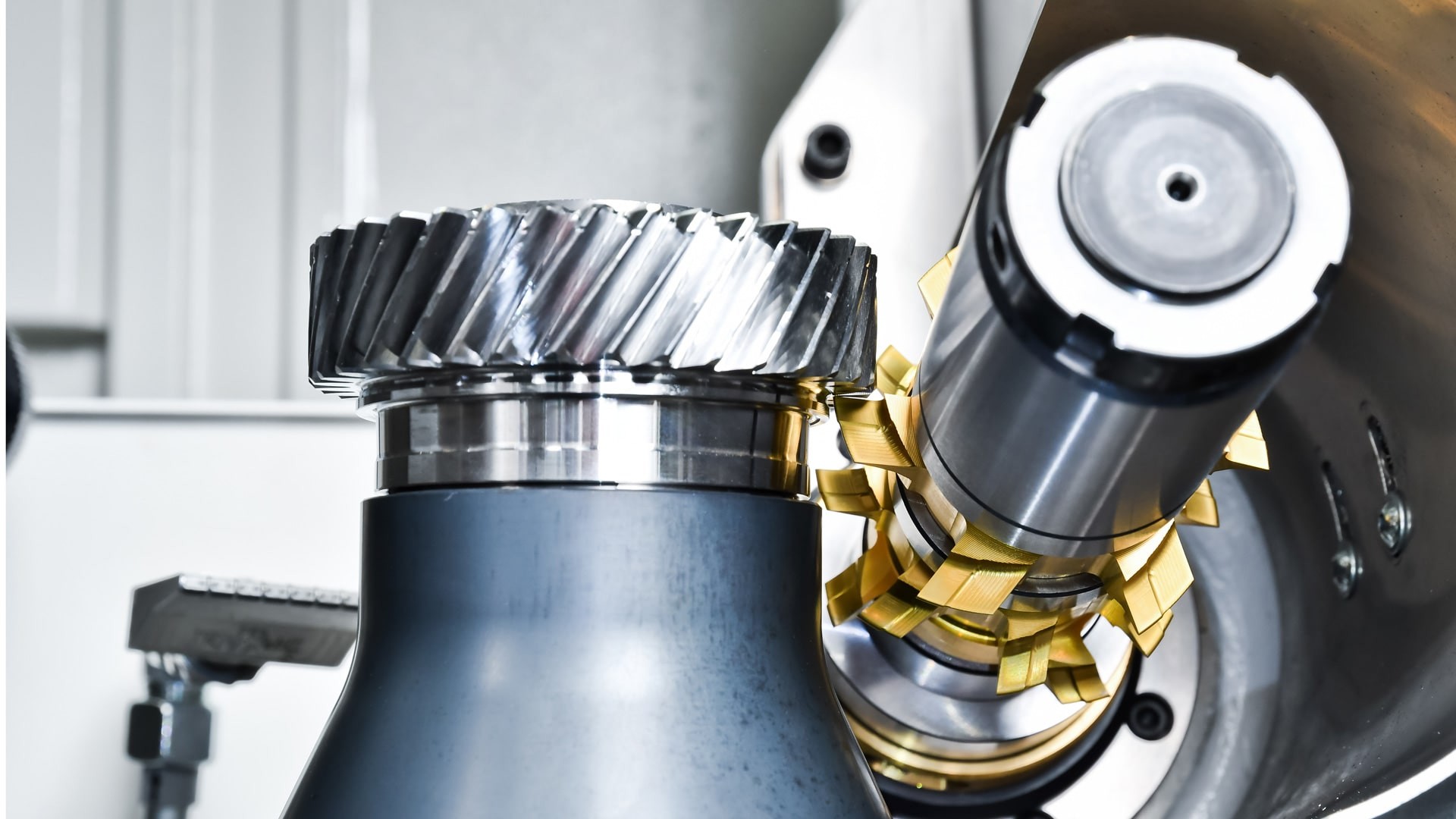
CNC chamfering with ChamferCut or FlexChamfer
Chamfering processes at Liebherr
Chamfering gears prevents the edges of the teeth from becoming brittle during heat treatment and reduces transportation and installation damage. Multiple processes can be chosen for this. Classic technology such as press deburring or chamfering with end mills are increasingly being superseded by CNC controlled processes such as ChamferCut and FlexChamfer.
These are extraordinarily economical and guarantee an excellent chamfer quality which can be reproduced very precisely. CNC controlled processes are easy to operate and minimize set up cost.
Liebherr knows the advantages and the limits for the various processes and individually advises customers with their selection. Requirements for an optimal chamfering process can be individually arranged by batch size, chamfer shape, subsequent machining or component geometry. Liebherr specializes in particular in the ChamferCut technology from LMT-Fette.
As a pioneer in introducing this process and its development to being production-ready, Liebherr is determined to take this further in the future: By consulting with clients, both companies are working to improve precision, productivity and usability.
ChamferCut
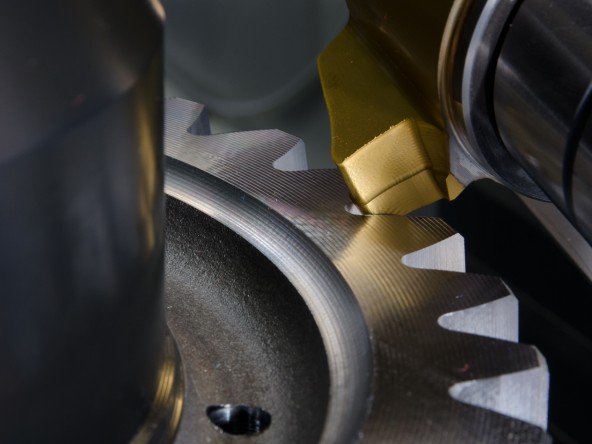
Precise, quick and reliable
- Precise chamfering geometry and quality, no material deformation
- Can be reproduced very precisely
- Easy operation, short setup times due to CNC control system
- Single-cut strategy: No additional finishing cut required to remove bulging on the lead
- Low investment cost and long tool life
- Ideal for subsequent finish machining
- Integrated chamfering device or standalone machines from Liebherr enable parallel machining
- Application range module 0.5 - 36
FlexChamfer
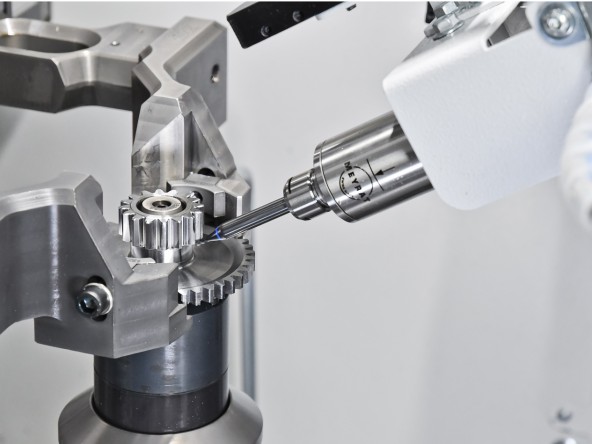
Maximum flexibility for external and internal gears
- CNC controlled advanced development of chamfering with end mills
- Development of variable chamfering forms with standard catalog tools
- Particularly suitable for external gears with or without interfering contours as well as shafts and internal gears
- Use in hobbing, shaping and gear skiving machines
- Parallel to machining (depending on the main machining time)
- Ideal for small and medium batch sizes
- Examples of use: Stage planetary gears, double internal gears
ChamferCut-CG (Collision Gear)
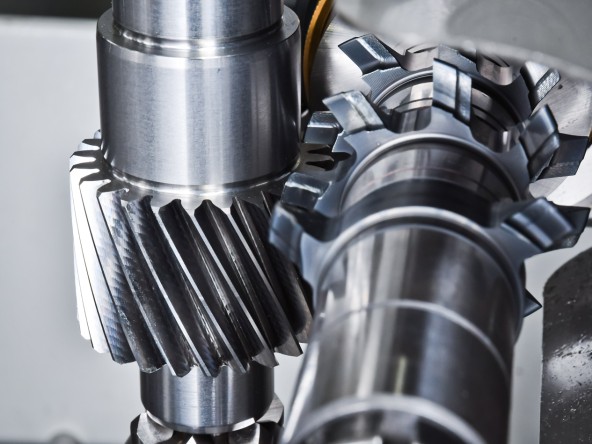
Chamfering despite interfering contour
- Chamfering including the root, even for collision critical gears
- More degrees of freedom with the chamfer divided between the left and right profile
- Can be implemented on Liebherr machines with a simple software update
- Batch sizes: Suitable for medium and large-scale production
- Application examples: Truck shafts, passenger vehicle idle gears and ring gears, industrial gearboxes
ChamferCut-IG (Internal Gear)
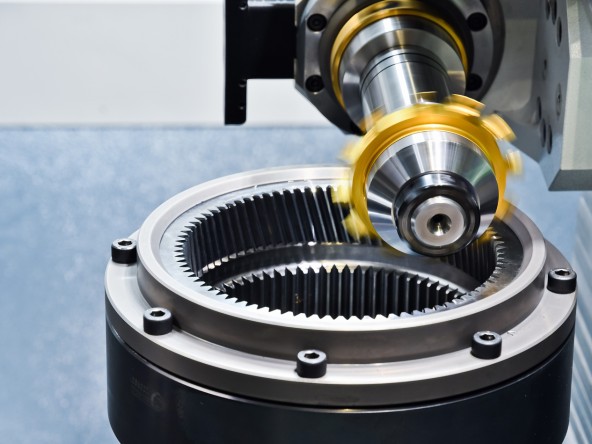
Chamfering of internal gears
- Chamfering of internal gears on both flanks in one cut
- Machining on compact standalone machine, e.g. LD 180 C
- Application examples: Internal gears of plantenary and e-motive gearboxes