To be more precise, two mini-machines were actually manufactured at the Liebherr-Verzahntechnik GmbH training center. With an edge length of about one meter each and weighing around 250 kilograms, they don’t exactly fit in your purse! But you can hob real plastic gears on them and even machine the plastic gears completely – all controlled by LHGearTec software. “The suggestion originally came from the development department,” says Head of Training Matthias Fendt. “They wanted a handy machine model to better illustrate axis movements and kinematics. This led to the idea of building this sort of machine at the training center because we are always looking for projects that are as practical and interdisciplinary as possible.”
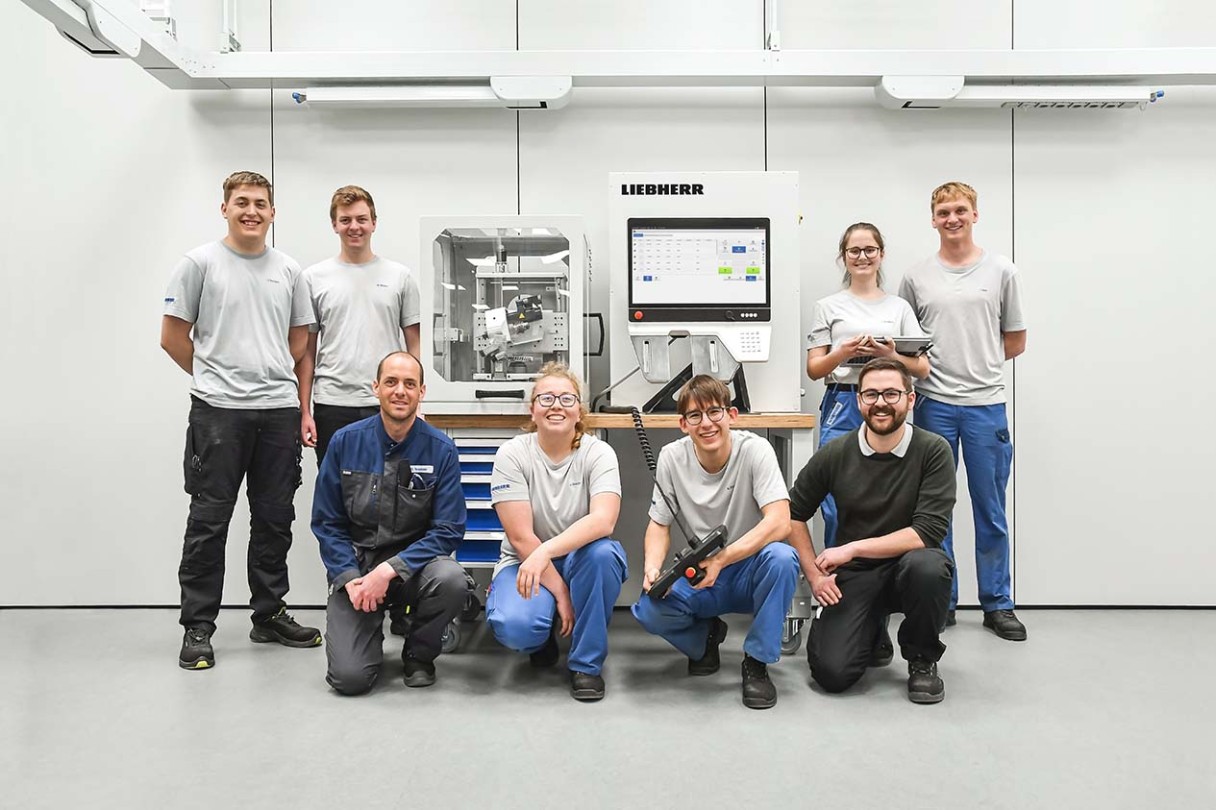
Meeting challenges! The industrial mechanics apprentices and trainers with the miniature gear cutting machine they built themselves
An illustrative model machine
Our apprentices also benefit from the model machine. “At the beginning of their training, the apprentices do not get a really comprehensive look into the various gearing technologies,” Fendt continues. “Therefore, especially with multiple machine axes, axis movements are sometimes difficult to visualize. Many different aspects can be demonstrated well with the model machines.” Even though the miniature machines are not a one-to-one copy of the “real” machines, they are reduced to their essential functions and are therefore easier and more versatile to use for training and simulation purposes. It therefore also doesn’t matter that the finished gears are made of plastic – it‘s about teaching the basics. “In this way, we can integrate the understanding of our products into the training program at an even earlier stage and in a more dynamic way,” explains Fendt.
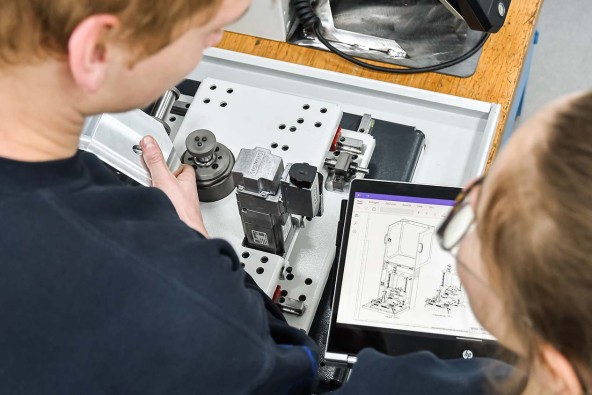
Challenge: From design drawing to reality
Independent and interdisciplinary
Liebherr places great emphasis on working in an independent and interdisciplinary way – even during training. The project was a collaboration between the apprentices in industrial mechanics, product design, electronics, and the combined study program. “We largely left the planning to the apprentices. They faced a challenge or two in designing and building the prototype. We trainers were always available in the background as learning coaches, but the apprentices organized themselves independently and always found a suitable solution,” Fendt reports proudly. The trainers also place great importance in craftsmanship – everything that did not have to be bought in was made by the apprentices themselves.
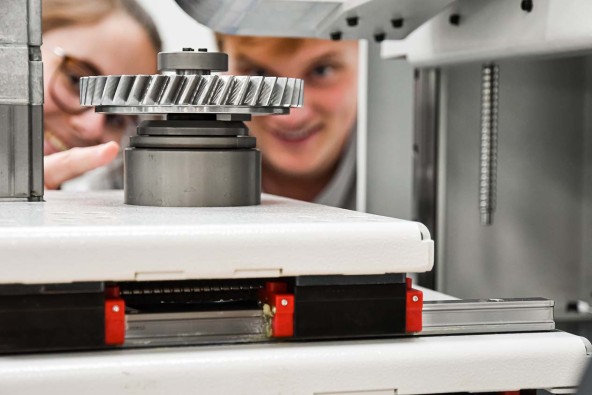
Vivid gear cutting process
“It sometimes made you want to tear your hair out... but it was very educational!”
And what do the apprentices have to say about it? Everyone found it very informative to work together in a team and see other points of view and expertise. “This project encouraged you to really get involved and try things out,” says industrial mechanics apprentice Michael Weixler. “It was a real challenge to implement a new design and then develop the idea and plan out the things that did not work in reality. Sometimes it was really frustrating,” recalls Rebekka Dietrich, another industrial mechanics apprentice. “But it has definitely been one of the best projects we have done and we got a lot out of it. We really learned a great deal because we didn‘t have to ask the trainer about every little thing and yet still always had support.” This has made the entire gear cutting process much more tangible for the apprentices. And it is not only their mechanical understanding that has grown, but also their awareness of how important it is to have good cooperation and collaboration between the different disciplines.