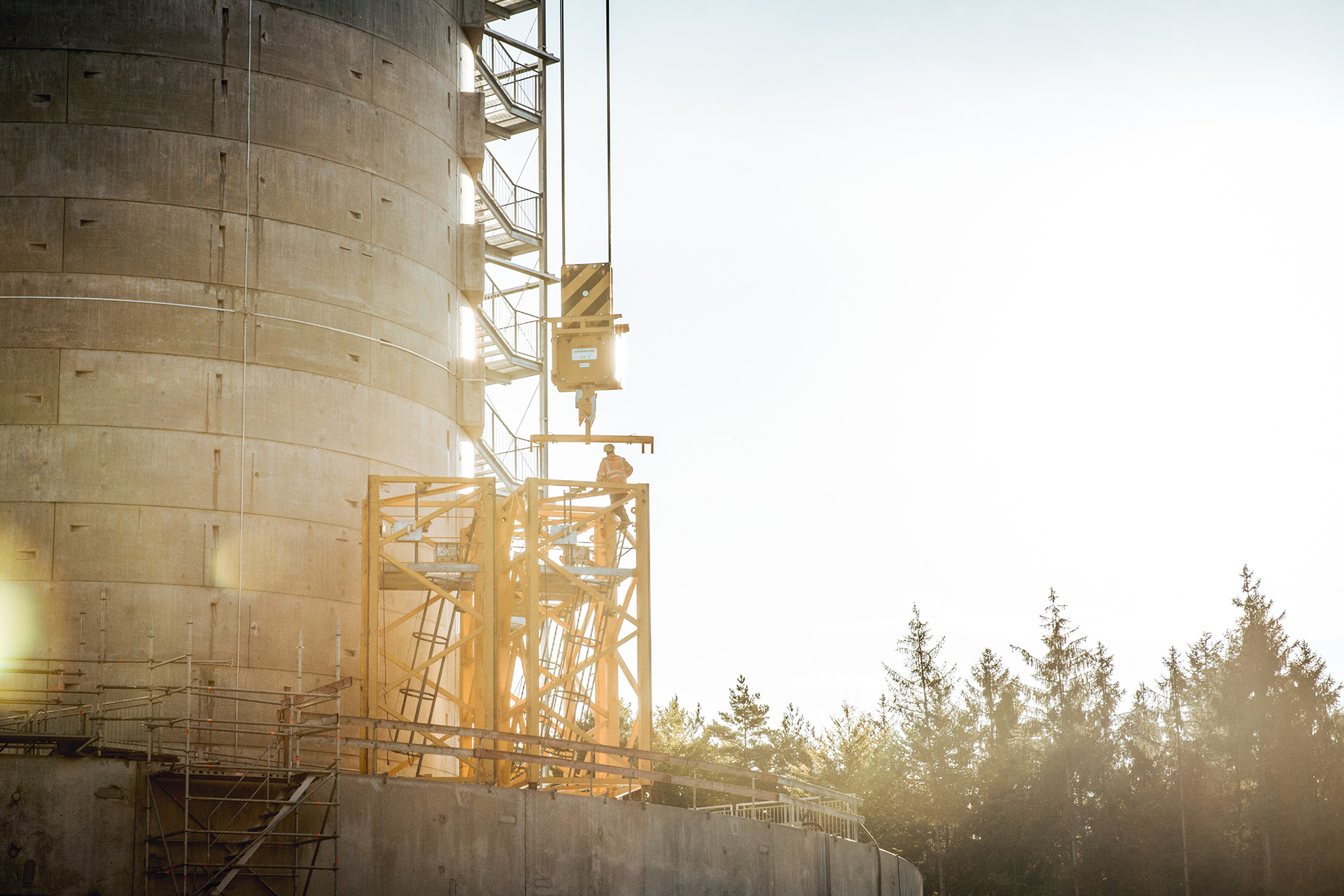
Click RELEASE VIDEO and follow the data protection notices.
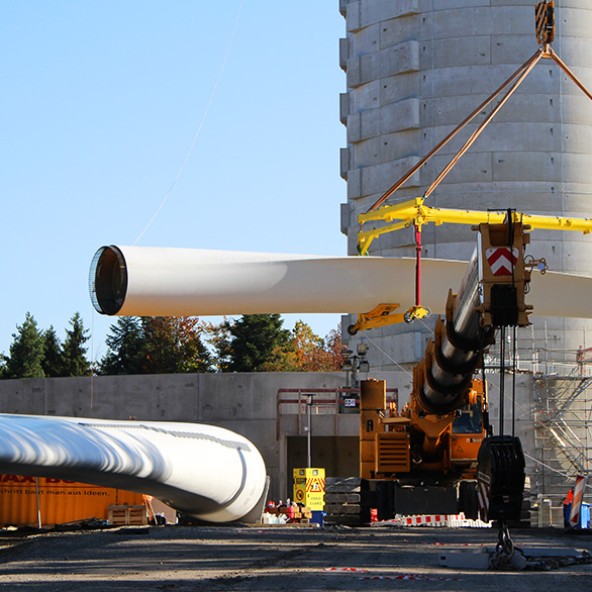
The Naturstromspeicher Gaildorf: a green energy storage facility
Total concentration. Everyone is looking up. It is so quiet on the construction site that you could hear a pin drop. The Liebherr 630 EC-H 70 Litronic tower crane is lifting the suspended rotor blade, which measures almost 70 metres in length and weighs 17 tonnes. Very slowly. Right up to the hub of the wind turbine, 178 metres above the ground.
A wind turbine of this size has never been built before. That is why, up in the tower crane, crane drivers Wilhelm Lepertz and Georg Brodwolf are tackling this challenge in tandem. Four eyes see better than two. They are in radio contact with Thomas Ziegenbein. The wind installation project manager for international construction company Max Bögl is the crane drivers' direct link with the ground crew who, from the forest below, are using ropes to control the suspended component and hold it in position. They are all totally focussed on the job in hand. The only sound to be heard is the echo of the radio messages which are being sent back and forth between the construction managers and the cockpit, reverberating across the construction site. There is a feeling in the air that a piece of technological history is being written here today.
We now know how to go about assembling components at these great heights. After this, it will keep getting easier and faster.
Globally acclaimed pilot project
In Gaildorf, located in the Limpurg Hills range of the Swabian-Franconian Forest, Germany's energy transition is being taken to a whole new level. Here the wind division of international construction company Max Bögl is building the world's tallest (246.5 metres) onshore wind turbines. The water battery with its four wind turbines – a completely new decentralised storage technology – is also a world first. This globally acclaimed pilot project, the Naturstromspeicher Gaildorf, is supported by the Federal Ministry for the Environment, Nature Conservation, Building and Nuclear Safety.
By clicking on “ACCEPT”, you consent to the data transmission to Google for this video pursuant to Art. 6 para. 1 point a GDPR. If you do not want to consent to each YouTube video individually in the future and want to be able to load them without this blocker, you can also select “Always accept YouTube videos” and thus also consent to the respectively associated data transmissions to Google for all other YouTube videos that you will access on our website in the future.
You can withdraw given consents at any time with effect for the future and thus prevent the further transmission of your data by deselecting the respective service under “Miscellaneous services (optional)” in the settings (later also accessible via the “Data protection settings” in the footer of our website).
For further information, please refer to our Data Protection Declaration and the Google Privacy Policy.*Google Ireland Limited, Gordon House, Barrow Street, Dublin 4, Ireland; parent company: Google LLC, 1600 Amphitheatre Parkway, Mountain View, CA 94043, USA** Note: The data transfer to the USA associated with the data transmission to Google takes place on the basis of the European Commission’s adequacy decision of 10 July 2023 (EU-U.S. Data Privacy Framework).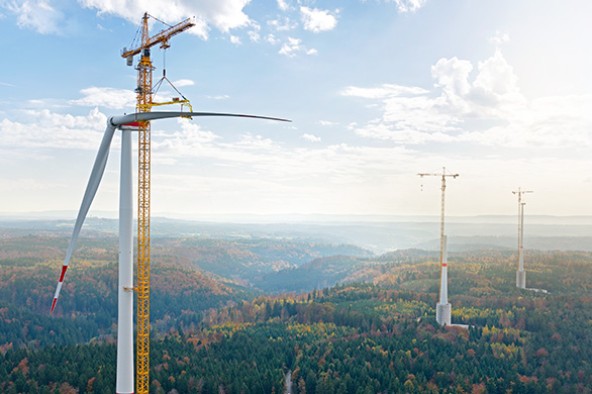
Precision work 178 metres above the ground
The rotor blade has now reached the height of the hub and has to be rotated by the crane so that it can be bolted into position. And this has to be done with millimetre precision. The tension among the crane and ground crews is at its peak. At the dizzying height of 178 metres above the ground, specially secured workers are waiting to bolt the metal spindle of the rotor blade to the hub. "This is a critical moment," says Thomas Ziegenbein. "Now, everything has to fit perfectly." As the sound of the rattling of the electronic torque wrenches echoes below, the tension eases. Mission accomplished. "Due to some strong gusts of wind in the early morning, we started a little later than planned today. Lifting the rotor blade, which was secured only with ropes, would otherwise have been too dangerous," says Ziegenbein, visibly relieved. "Tomorrow, the work will continue. We now know how to go about assembling components at these great heights. After this, it will keep getting easier and faster."
The Naturstromspeicher is a combination of a wind farm and a pumped-storage power plant. This allows the wind-generated electricity to be stored, regulated and above all supplied precisely when it is actually needed in the electricity grid.
A "battery" made of water
The wind turbine which has just been assembled at the "WEA 3" site is no ordinary design. "The water battery is a combination of a wind farm and a pumped-storage power plant. This allows the wind-generated electricity to be stored, regulated and above all supplied precisely when it is actually needed in the electricity grid," explains overall project manager Johannes Kaltner.
Storage is provided by the active and passive reservoirs at the base of the wind turbine. These will later be connected via a pressure pipe to the lower reservoir of water in the valley, as well as to the pumped-storage power plant located between them. "Work on laying the water pipelines will commence in the spring," says Kaltner.
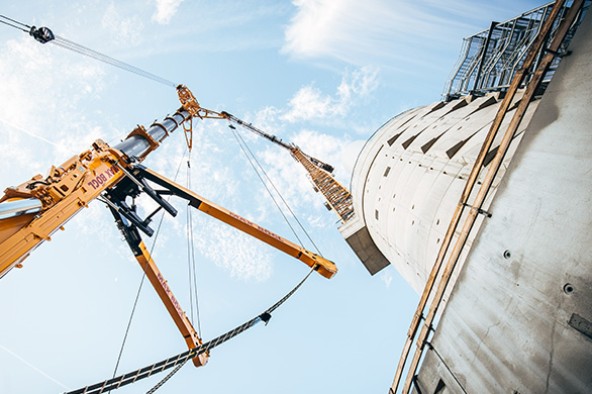
Not run-of-the-mill even for wind power professionals
Since the foundation stone was laid in April 2016, overall project manager Johannes Kaltner has been continuously based at the Gaildorf site with around 35 specialist workers. He says it is the enthusiasm for innovations and what is technically feasible that constantly drives his team on to develop new ideas. "The fact that this construction site is opening a new chapter in Germany's energy transition means that it is not run-of-the-mill work, even for experienced wind-power professionals," stresses Kaltner.
One of these wind-power professionals is Ralf Karras. The Berliner is a crane driver out of sheer passion. Using the joystick, he operates his powerful LTM 11200-9.1 crane, which he has reverentially given the name "Hercules". And with good reason. The 9-axle mobile crane from Liebherr has a 100-metre telescopic boom, one of the longest in the world, and delivers a maximum load capacity of 1,200 tons.
Crane for crane – which is the strongest
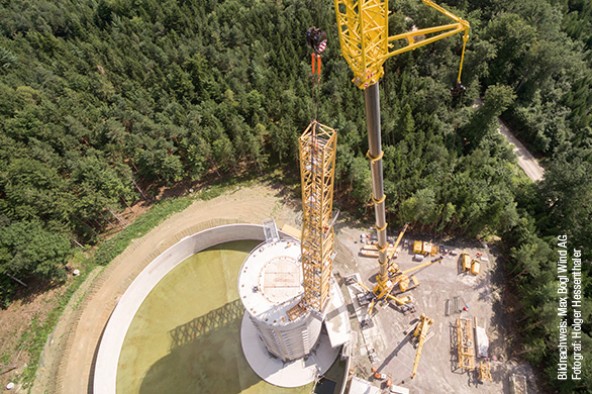
Real skill: cranes perform a one-two
The mobile crane performs a clever one-two with the tower crane in Gaildorf. However, initially Karras' crane had to start the work single-handedly. For him, that meant lifting the concrete quarter shells for the base, each weighing 22 tons, from the low loaders, bringing them together on the crane platform and fitting them into the installation with an 88-ton lift. Not until the 40-metre-high active reservoir was in place could the tower crane be mounted on this foundation. Karras had to take delivery of 22 truckloads, including six heavy loads. "I had to lift the first crane modules with my LTM, and after that the tower crane, with its special hydraulic design, erected itself using its self-climbing function," says Karras. Now that the crane is operational, Karras "merely" has to position the large, bulky components so that his colleague up in the crane can lift them up to a great height.
By clicking on “ACCEPT”, you consent to the data transmission to Google for this video pursuant to Art. 6 para. 1 point a GDPR. If you do not want to consent to each YouTube video individually in the future and want to be able to load them without this blocker, you can also select “Always accept YouTube videos” and thus also consent to the respectively associated data transmissions to Google for all other YouTube videos that you will access on our website in the future.
You can withdraw given consents at any time with effect for the future and thus prevent the further transmission of your data by deselecting the respective service under “Miscellaneous services (optional)” in the settings (later also accessible via the “Data protection settings” in the footer of our website).
For further information, please refer to our Data Protection Declaration and the Google Privacy Policy.*Google Ireland Limited, Gordon House, Barrow Street, Dublin 4, Ireland; parent company: Google LLC, 1600 Amphitheatre Parkway, Mountain View, CA 94043, USA** Note: The data transfer to the USA associated with the data transmission to Google takes place on the basis of the European Commission’s adequacy decision of 10 July 2023 (EU-U.S. Data Privacy Framework).The pilot project Naturstromspeicher Gaildorf
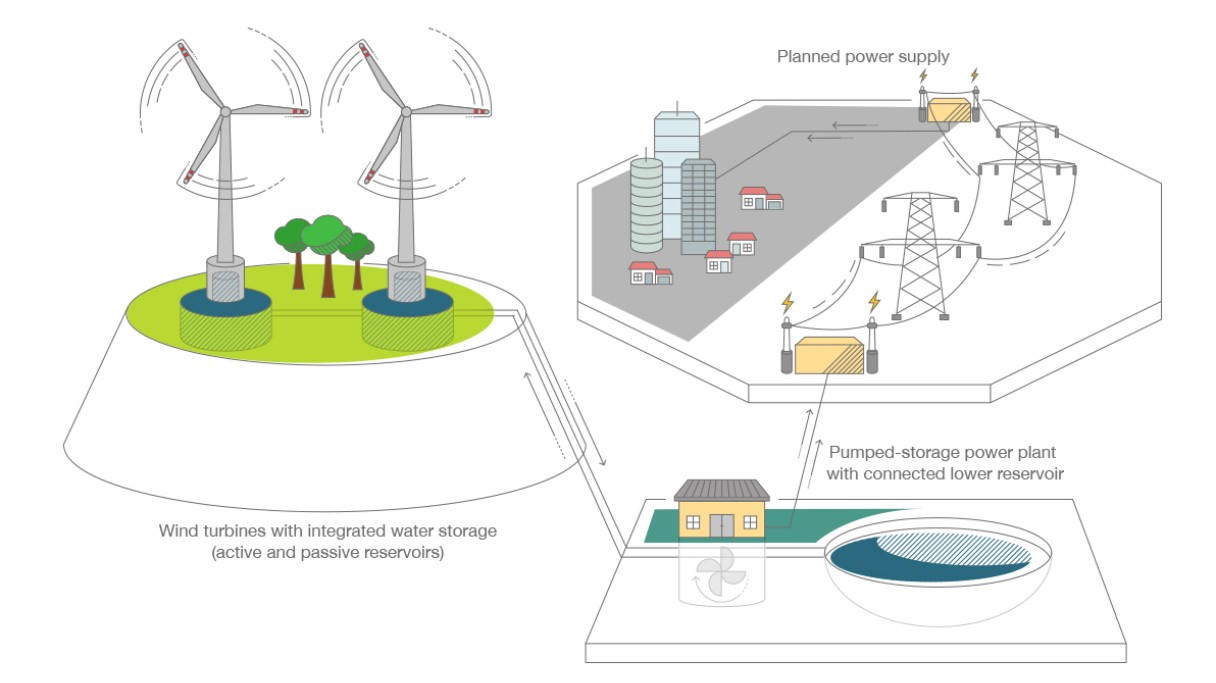
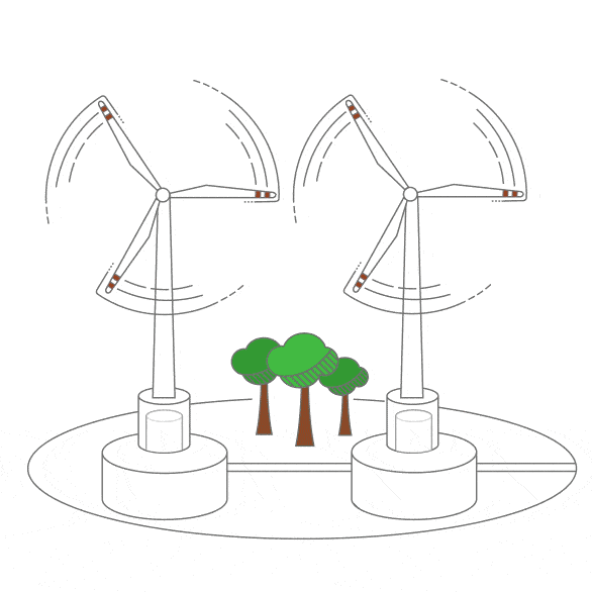
Wind turbines with integrated water storage
The power output of the wind turbines is 3.4 megawatts per turbine. The wind turbines stand on foundations formed of integrated water storage tanks with up to 30 metres of headroom in the active reservoir. A total of 160,000 cubic metres of water are used for storing energy in the active and passive reservoirs. The water storage tank is connected to the generator in the pumped-storage power plant via underground pressure pipes. The height difference between them is 200 metres.
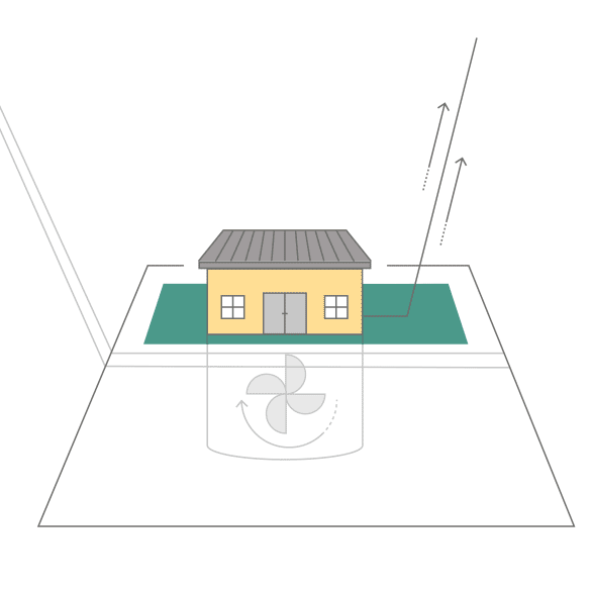
Pumped-storage power plant with connected lower reservoir
The water battery works with a variety of power sources and is therefore suitable for a modular concept, with a wind farm as at Gaildorf as well as with a solar power installation or a combined heat and power plant. Three output classes are available: 16, 24 and 32 megawatts.
In Gaildorf, a 16-megawatt plant is going onstream. The principle behind it is simple: When the wind blows, the surplus power that cannot be taken up by the electricity grid is used to pump water from the lower reservoir to the wind turbines' integrated water reservoirs, using the pumped-storage plant. The switchover from production to storage can be carried out in less than 30 seconds. That's why it's referred to as a "flexible power plant". During periods of calm, the water flowing down from above drives the turbines in the pumped-storage plant. The wind farm can thus continue to generate electricity reliably and predictably and feed it into the grid.
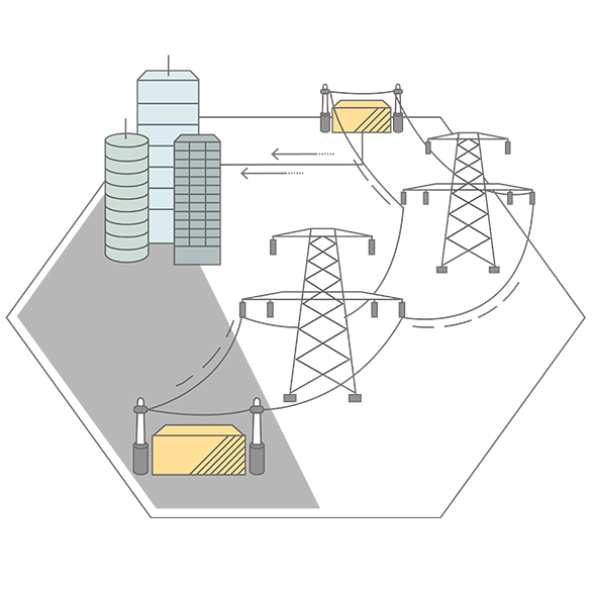
Planned power supply
The combination of wind and hydroelectric power ensures that households, businesses and industry are supplied with green electricity in an even and systematic way. In Gaildorf, annual electricity generation from wind can amount to as much as 42 gigawatt hours.
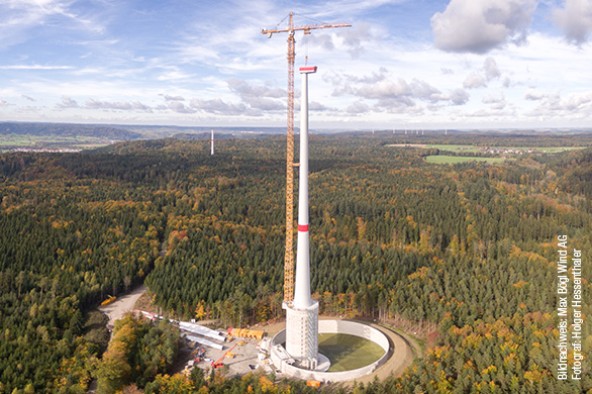
On close terms with nature
Erecting four wind turbines in the middle of the forest is not only a technical challenge, but also a logistical one. "Just try putting three 70-metre-long rotor blades down in the middle of the forest," says project manager Johannes Kaltner with a wink. "And without clear-felling." He himself is passionate about harmonious interaction between people, nature and large-scale technology: "When organising a construction site like this one here in Gaildorf, we wind people always need a bit of humility and respect for nature." A huge advantage of the tower crane is that it takes up significantly less space than other types of crane. This means that a smaller area has to be cleared in the forest. The fewer traces the construction site leaves in the natural environment, the better," says Kaltner.
For this reason, geologists, biologists, geo-ecologists and sound insulation experts had tested the environmental compatibility of the turbines beforehand. The inhabitants of Gaildorf were involved in the planning from an early stage and were given extensive information about the individual steps in the process. And what does all this mean for the 70-metre-long rotor blades in the forest? "We have made the construction site as compact and the gravel access roads as narrow as possible. Our logistics must therefore deliver components just-in-time, as we do not have large storage facilities in the forest. At the base of the turbine, there is only room to lift one rotor blade at a time," says Thomas Ziegenbein. After that, the mobile crane has to be brought in again to lift the next heavy blade over the treetops from the site access road and place it in the right position. It's worth the effort," says Ziegenbein. "After we've gone, nature will quickly reclaim the building site."
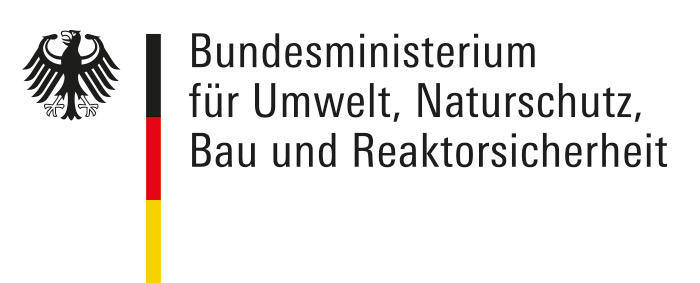
A symbol for the environment
The Federal Ministry for the Environment, Nature Conservation, Building and Nuclear Safety (BMUB) is supporting the Gaildorf project with funds from the Environmental Innovation Programme to the tune of 7.15 million euros. This is a clear symbol of recognition of this innovative technology, which is being tested out in a large-scale application for the first time.