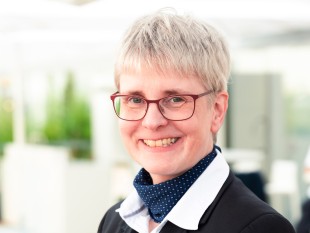
Ute Braam
Head of Corporate Communications
Liebherr-Aerospace & Transportation SAS
Pfänderstraße 50-52
88161 Lindenberg
Germany
- Phone+49 8381 4644-03
Liebherr-Aerospace has made the next major step regarding additive manufacturing of parts with increased complexity for aerospace application. The first-tier supplier has successfully integrated a 3D-printed flex shaft in the Airbus A350 high lift system. The unit has been approved by Airbus as well as by the European Union Aviation Safety Agency EASA for serial production.
Liebherr-Aerospace continues to consistently pursue its path in the 3D printing sector. The company has now celebrated a new milestone: a flex shaft, a component with an increased degree of complexity and produced from titanium powder using Additive Layer Manufacturing (ALM), has successfully made its way into aviation. Aircraft manufacturer Airbus as well as EASA, have both approved the flex shaft to enter series production.
Based on the new design options that ALM is offering, Liebherr was able to replace the assembly of seven parts, formerly conventionally manufactured, by just one single 3D-printed component. The lower number in parts leads to improved reliability and significant weight reduction. Compared to the 3D-printed parts previously developed and manufactured by Liebherr, the flex shaft has a higher complexity and represents a next step towards applications in highly integrated systems.
The flex shaft is part of the Airbus A350 high lift system, where it will be integrated in the active differential gearbox of the flap system. The flex shaft transmits the rotary movement to a position sensor and thus compensates for an angle and axis misalignment between gearbox and sensor.
The solution provider Liebherr-Aerospace can already look back at quite a range of its products manufactured by ALM. At the beginning of 2019, for example, Liebherr-Aerospace started the serial production of 3D printed parts with the introduction of a printed proximity sensor bracket for the A350 nose landing gear. This bracket was the first-ever introduced Airbus system part qualified for titanium additive layer manufacturing.
Here you can find the press release for download.
Head of Corporate Communications
Liebherr-Aerospace & Transportation SAS
Pfänderstraße 50-52
88161 Lindenberg
Germany