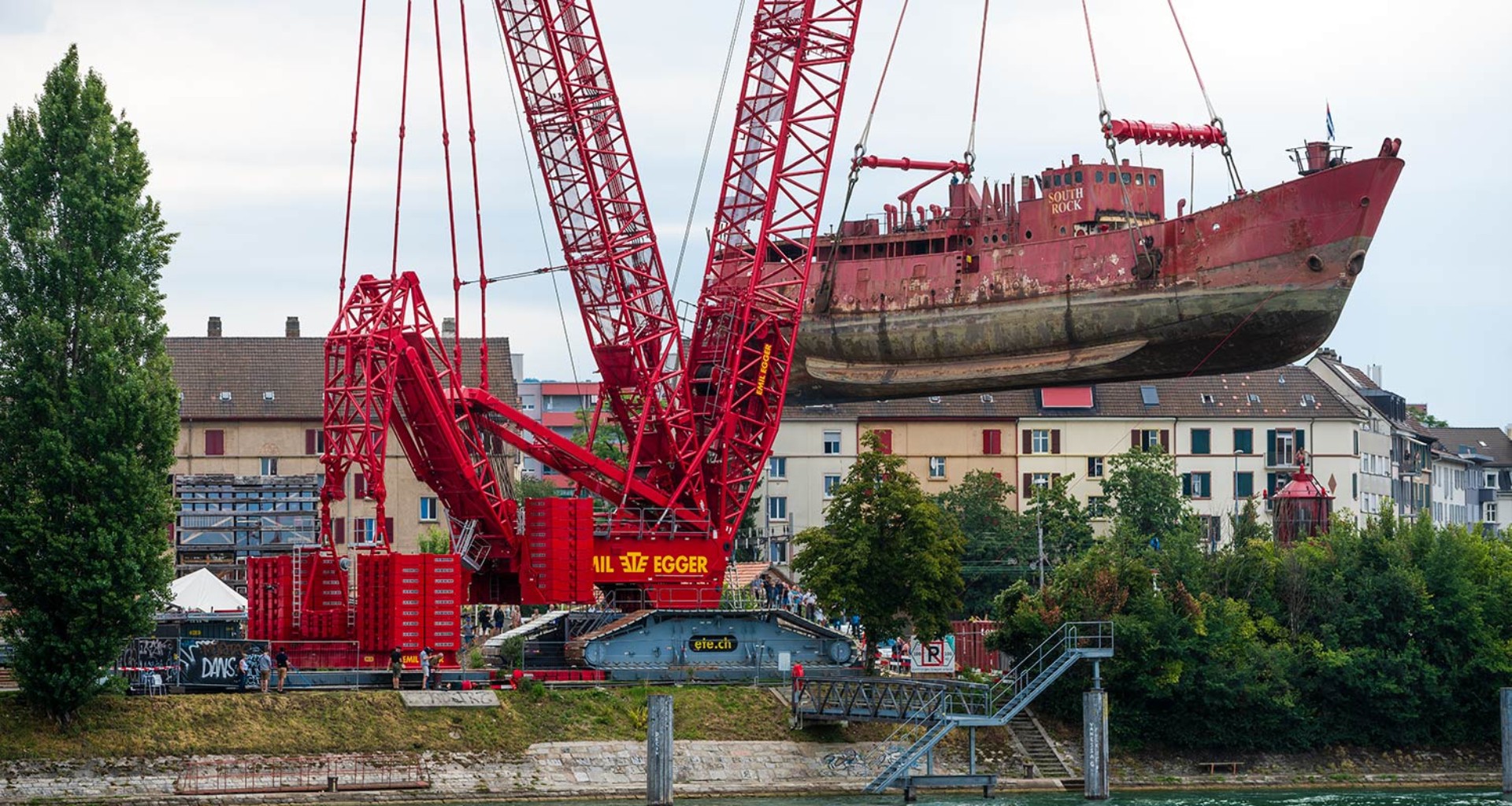
8 minutes | magazine 02/2019
V-frame proves itself in practice
Our LR 11000 has successfully completed its first jobs using the innovative, highly flexible “V-frame” ballasting system. The 1000-tonne crane operated by Swiss crane logistics contractor Emil Egger AG completed a spectacular bridge hoist near Lausanne and also removed an old lightship from the River Rhine in Basel.
Bridge site in Moudon
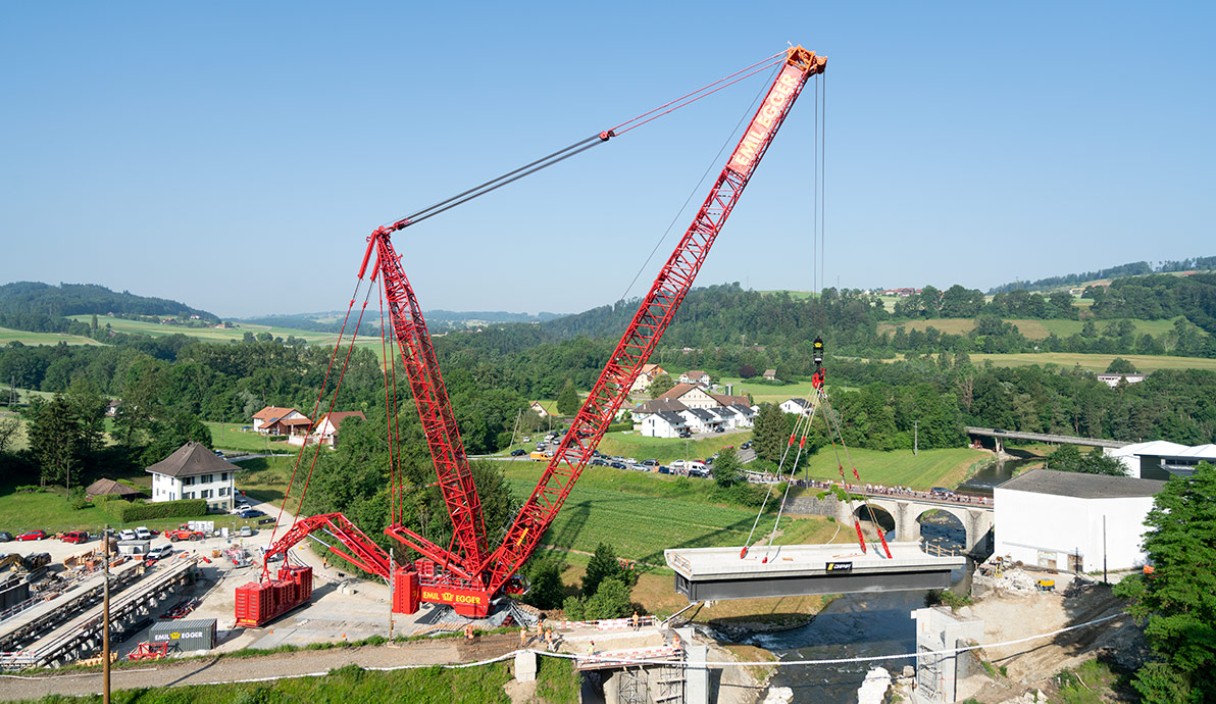
Almost there – the two large hydraulic cylinders extended the derrick ballast to a radius of 28.5 metres for positioning the railway bridge. The maximum possible radius is 30 metres.
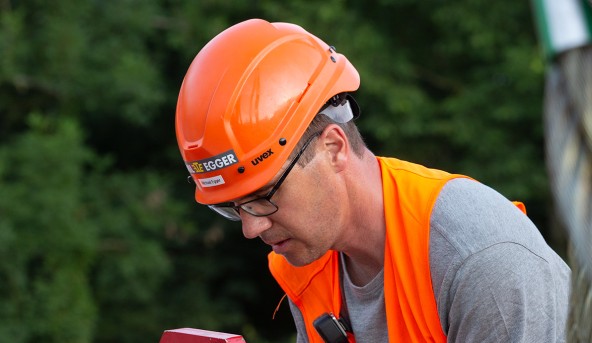
Right at the heart of things – Managing director Michael Egger securing the attachment equipment.
The bridge site is Moudon in western Switzerland was a real challenge – extremely restricted space, protected trees and a heavy bridge which had to be positioned over a river with a 180 degree slewing process by the crane with a large radius and therefore also a large suspended ballast radius. The demanding requirements on site therefore created perfect conditions for a stiff practical test for the first use of the new V-frame on the LR 11000. “Without the hydraulically adjustable ballast radius, hoisting the bridge would have been significantly more expensive,” is how Managing Director and crane enthusiast Michael Egger explains the solution he provided for this job. “Firstly, it would have required much more expensive work on the embankment to get closer to the abutments with a crawler crane. And then we would also have required a much longer crane track to complete the bridge immediately in front of the abutment.”
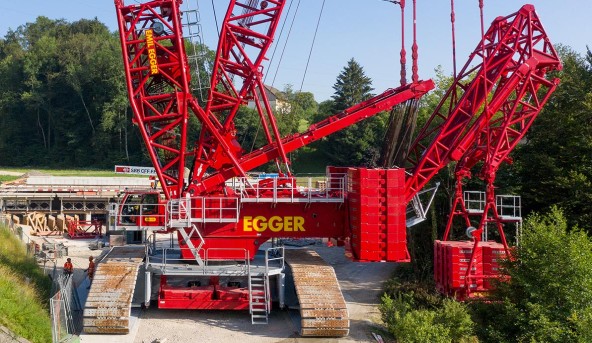
The benefit of the VarioTray – with the central section of the ballast disconnected from the derrick boom, the crawler crane can position its suspended ballast pallet itself.
Variable ballast radius from 13 to 30 metres creates flexibility
However, the V-frame made this expensive additional work superfluous on this site. The new development from the Liebherr Plant in Ehingen made it possible to reduce the radius of the suspended ballast to just 13 metres once the 380 tonne load had been hoisted. As a result of this small radius, the ballast pallet could be carefully guided past a small row of protected trees during the slewing process. When the railway bridge was placed on its abutments at a radius of 38 metres, the hydraulic ballasting device pressed the 440 tonne derrick pallet at a distance of 28.5 metres. “Another benefit of using the V-frame for jobs,” continues Egger, “is that the derrick ballast pallet has a maximum ground pressure of 150 kilonewtons per square metre thanks to the integral load distributor plates. The ground pressure from a ballast trailer is at least three times higher and therefore often requires expensive work to prepare the ground.”
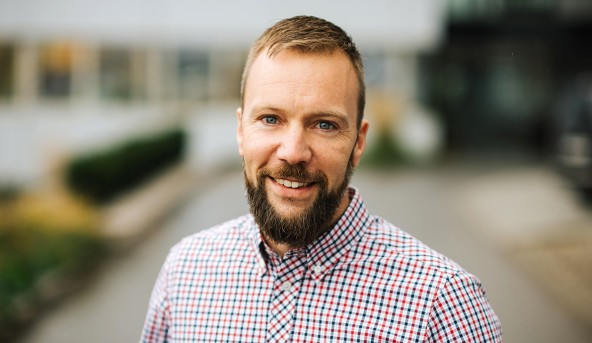
Clemens Norz
Michael Egger has long been convinced by the benefits of a hydraulically adjustable folding frame for the suspended ballast. That is why he discussed this solution when he ordered his LR 11000 with Liebherr at the start of 2017. The design of the V-frame for the LR 1800-1.0 was in full flow at that time and Liebherr unveiled it at the Customer Days in 2018. As a result of Egger’s request, the decision was made to design a similar system for the 1000-tonne crane. Clemens Norz, Designer in the Crawler Cranes department at Liebherr, remembers it well: “Mr Egger had a very clear idea of what he wanted and we were then able to make even the details into reality. The important things for him were a large adjustment range for the ballast radius and the ability to retrofit it to his LR 11000, in other words, a crane we have had in our range for several years. That was a challenge for us. The suspended ballast radius had to be significantly reduced to hold the ballasted pallet without a load on the hook in the air. On the other hand, the maximum ballast radius of 30 metres had to be achieved so that the entire lifting capacity of the crane can be used. The V-frame on the LR 11000 has two joints to achieve this enormous adjustment range from 13 to 30 metres.”
The V-frame on the LR 11000 has two joints to achieve the enormous adjustment range from 13 to 30 metres.
The design and the structural calculation of the V-frame saw Liebherr enter a whole new world. Norz explains: “We had to recalculate the complete erection concept and the new loads for the crane. Another important point was that the LICCON crane control system enables the V-frame to be adjusted automatically during crane operation so that the crane operator can concentrate on the load. We also came up with a few snazzy details. For example, the available oil volume for the extension cylinders is limited by the capacity of the oil tank. To counter this, we use an extraordinary cylinder design in which the rod volume of the cylinder is used as an additional tank.”
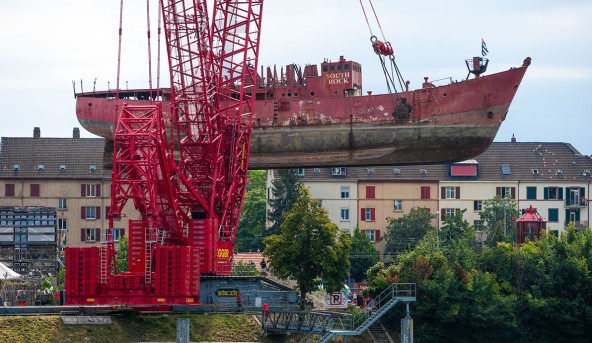
The adjustable ballast allowed the load to be slewed past buildings and obstacles.
VarioTray makes auxiliary crane for ballasting superfluous
Another clever feature on Egger’s crawler crane ensured that the job on the bridge site in Moudon was completed quickly – the VarioTray detachable ballast system. The facility to simply unbolt the central section of the suspended ballast means that there is no need for a mobile crane to stack and destack the ballast slabs. “Because of the situation on the site, we would have needed a large crane for this job – we would have lost an enormous amount of time and required a great deal of space,” says Egger. “In most cases, our LR 11000 can position the derrick ballast pallet, or at least the outer section, itself since the central section of the ballast remains on the crane and therefore only around 300 to 350 tonnes have to be moved.”
By clicking on “ACCEPT”, you consent to the data transmission to Google for this video pursuant to Art. 6 para. 1 point a GDPR. If you do not want to consent to each YouTube video individually in the future and want to be able to load them without this blocker, you can also select “Always accept YouTube videos” and thus also consent to the respectively associated data transmissions to Google for all other YouTube videos that you will access on our website in the future.
You can withdraw given consents at any time with effect for the future and thus prevent the further transmission of your data by deselecting the respective service under “Miscellaneous services (optional)” in the settings (later also accessible via the “Privacy Settings” in the footer of our website).
For further information, please refer to our Data Protection Declaration and the Google Privacy Policy.*Google Ireland Limited, Gordon House, Barrow Street, Dublin 4, Ireland; parent company: Google LLC, 1600 Amphitheatre Parkway, Mountain View, CA 94043, USA** Note: The data transfer to the USA associated with the data transmission to Google takes place on the basis of the European Commission’s adequacy decision of 10 July 2023 (EU-U.S. Data Privacy Framework).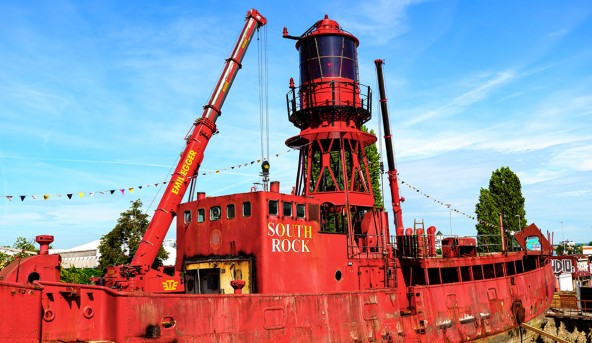
The light tower will be used as a radio transmitter.
Lightship becomes event location
Just a few weeks later, the V-frame was able to show its strengths yet again when it hoisted a 550 tonne ship onto the banks of the River Rhine in Basel on the same crawler crane. The adjustable ballast system was used for this job because there were buildings and obstacles in the way of the derrick ballast during the slewing process.
"Gannet", a 42 metre lightship will be used as an event location for up to 300 people in an event and culture park in the port district of Basel. Before its decommissioning in 2010 it showed seafarers the way for around 70 years near South Rock in Ireland. In spring it was towed over the English Channel to the River Rhine via Rotterdam. The light tower had to be dismantled so that it would pass under bridges. Once it arrived at its new location, the light tower was reinstalled on the ship to be used as a radio transmitter.
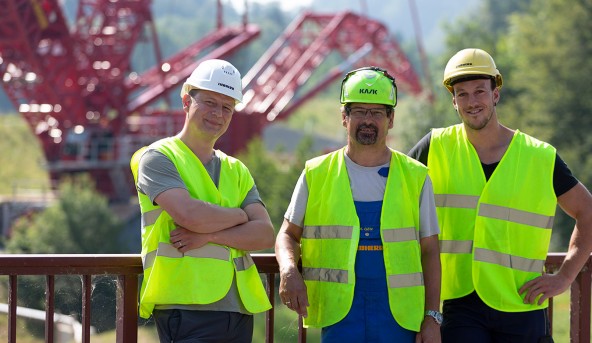
Customer proximity literally – Software Developer Matthias Ströbele, Service Technician Albert Götz and Machine Tester Dominik Gemeinder (from left to right) monitored the first job completed by the V-frame closely.
Support from the manufacturer
Liebherr monitored and supervised the first use of the innovative V-frame technology closely from the very outset. During the hoist on site, three members of the team from the Ehingen crane factory where present to provide support, just in case. A service technician, a machine tester and the programmer of the software for the hydraulically adjustable folding frame were involved in the whole process from setting up the crane to positioning the bridge in Moudon. But that's not all: “First of all, we used an identical crane on our test site in Ehingen with the same set-up configuration, the parameters from the Swiss site and of course a load of the same weight to simulate this hoist”, says Dominik Gemeinder, who works at the acceptance testing site for crawler cranes in Ehingen.
Crane operator Michael Egger is a person who appreciates this service and customer proximity from Liebherr. “We had never worked with the V-frame before and it was really great that Ehingen offered us this superb support for its first job. Perfect.”
This article was published in the UpLoad magazine 02 | 2019.