Hydraulic actuation systems
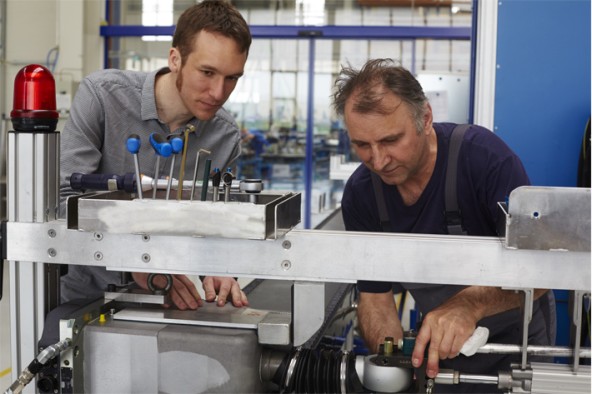
Liebherr is a major supplier of hydraulic control systems such as leveling systems, active lateral steering systems, bogie steering systems and anti-kink systems for rail transportation applications.
The product line reaches from simple passive dampers up to complex safety systems. They are installed on the latest high-speed trains and locomotives, other long-distance and local trains, subways, city and suburban rail transit systems and tramways.
With its comprehensive technical know-how from the field of transport technologies, aviation and construction machines, Liebherr-Transportation Systems is a company that can transform the most challenging customer’s requirements into innovative solutions.
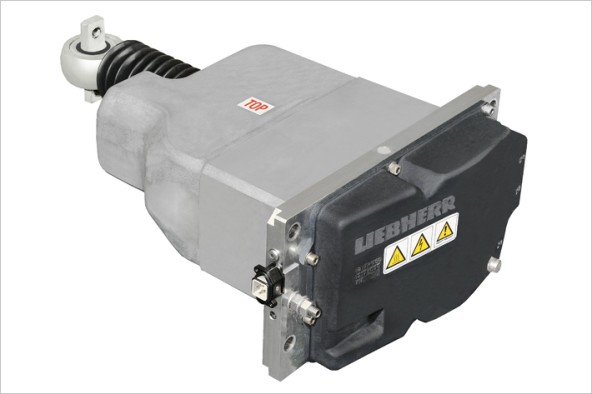
Smart hydraulic actuator
Electrohydraulic actuators work like compact, highly capable “power houses” on the rail vehicles and are tailor made solutions for several application areas. The current application areas in rail vehicle construction reach from yaw damping, active lateral positioning, car positioning systems and active radius steering to tilting technology.
Electrohydraulic actuators fulfil demands of the future development of rail infrastructure – especially in reducing environmental burden, minimizing wear and noise while improving the performance of the rail vehicle.
Increased riding comfort
Electrohydraulic actuators are designed to position loads of several tons at train speeds up to 350 km/h into the pre-set position predetermined by an intelligent control unit or counter vibrations on the vehicle.
Electrohydraulic actuators play an important role in fulfilling the requirements for high train speeds and provide increased riding comfort.
An additional and essential advantage of this technology lies in the massive reduction of vehicle and infrastructure wear. Initially higher investment costs are offset by considerably reduced overhaul expenses, reduced energy expenses und increased transport capacity within short time.
Easy and low-cost installation
Electrohydraulic actuators are closed hydraulic systems.
Liebherr carries through the assembly, filling and final inspection at very high purity conditions, thus ensuring a trouble-free and long-living operation under the harsh conditions of rail traffic. The car builder therefore only needs to mount the electrohydraulic actuators into the rail vehicle and connect the power supply and the control unit. Thus, costly and time-intensive installation works that are necessary for classic hydraulic systems with hydraulic pipe laying and filling and bleeding the systems can be reduced.
Therefore, the risk to pollute the hydraulic channel by improper installation and to possibly damage the actuator is eliminated.
Electrohydraulic actuators - a “plug and play” solution
Electrohydraulic actuators are essentially maintenance-free. In the very unlikely event of a failure, the complete unit can be replaced without any hydraulic knowledge in a short time. Due to this simple way of installation, long downtimes can be excluded.
These innovative systems are controlled by a microprocessor controller also developed by Liebherr specifically for rail applications. The software can be programed, depending on requirements, to Security Level SIL2 acc. EN 50128. Liebherr’s electrohydraulic actuators can be adjusted for almost all customer requirements and support a quick, comfortable and above all safe arrival at the destination.
By clicking on “ACCEPT”, you consent to the data transmission to Google for this video pursuant to Art. 6 para. 1 point a GDPR. If you do not want to consent to each YouTube video individually in the future and want to be able to load them without this blocker, you can also select “Always accept YouTube videos” and thus also consent to the respectively associated data transmissions to Google for all other YouTube videos that you will access on our website in the future.
You can withdraw given consents at any time with effect for the future and thus prevent the further transmission of your data by deselecting the respective service under “Miscellaneous services (optional)” in the settings (later also accessible via the “Privacy Settings” in the footer of our website).
For further information, please refer to our Data Protection Declaration and the Google Privacy Policy.*Google Ireland Limited, Gordon House, Barrow Street, Dublin 4, Ireland; parent company: Google LLC, 1600 Amphitheatre Parkway, Mountain View, CA 94043, USA** Note: The data transfer to the USA associated with the data transmission to Google takes place on the basis of the European Commission’s adequacy decision of 10 July 2023 (EU-U.S. Data Privacy Framework).On the move – without barriers
Contacts
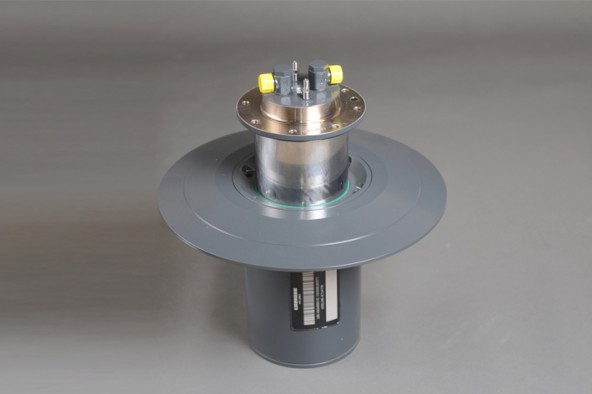
Leveling actuator
The level control system adjusts the vehicle’s floor during the arrival at the station to height-level of the platform. This enables a barrier-free entrance.
There is a possibility to integrate a hydraulic wheel rim wear out compensation.
Typically a system consists of the following components: hydraulic power unit, levelling actuator, position sensor (optionally integrated into a vertical damper) and controller.
By clicking on “ACCEPT”, you consent to the data transmission to Google for this video pursuant to Art. 6 para. 1 point a GDPR. If you do not want to consent to each YouTube video individually in the future and want to be able to load them without this blocker, you can also select “Always accept YouTube videos” and thus also consent to the respectively associated data transmissions to Google for all other YouTube videos that you will access on our website in the future.
You can withdraw given consents at any time with effect for the future and thus prevent the further transmission of your data by deselecting the respective service under “Miscellaneous services (optional)” in the settings (later also accessible via the “Privacy Settings” in the footer of our website).
For further information, please refer to our Data Protection Declaration and the Google Privacy Policy.*Google Ireland Limited, Gordon House, Barrow Street, Dublin 4, Ireland; parent company: Google LLC, 1600 Amphitheatre Parkway, Mountain View, CA 94043, USA** Note: The data transfer to the USA associated with the data transmission to Google takes place on the basis of the European Commission’s adequacy decision of 10 July 2023 (EU-U.S. Data Privacy Framework).On the move – without barriers
Contacts
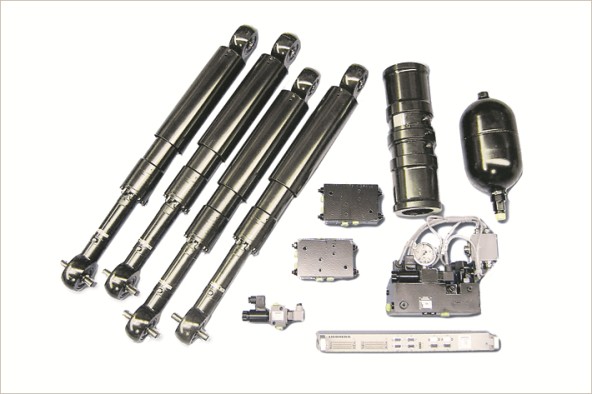
Anti-buckling system
The damper optimises the operational behavior of the vehicle and also reduces the forces within the vehicle structure.
In order to provide improved and simplified maintenance and diagnostics facilities the damper can be equipped with an optional monitoring system.
For the application in modern articulated buses (semi active damper) an electronically controlled damping system was developed. The damper offers a very high damping force continuously variable up to 240 kN in a very compact design package. An integrated sensor system monitors the pre-set damping values continuously. The system’s design ensures a minimum damping capability even in cases of electronic system failure. For cost optimized applications, a two-stage damping system is also available.
By clicking on “ACCEPT”, you consent to the data transmission to Google for this video pursuant to Art. 6 para. 1 point a GDPR. If you do not want to consent to each YouTube video individually in the future and want to be able to load them without this blocker, you can also select “Always accept YouTube videos” and thus also consent to the respectively associated data transmissions to Google for all other YouTube videos that you will access on our website in the future.
You can withdraw given consents at any time with effect for the future and thus prevent the further transmission of your data by deselecting the respective service under “Miscellaneous services (optional)” in the settings (later also accessible via the “Privacy Settings” in the footer of our website).
For further information, please refer to our Data Protection Declaration and the Google Privacy Policy.*Google Ireland Limited, Gordon House, Barrow Street, Dublin 4, Ireland; parent company: Google LLC, 1600 Amphitheatre Parkway, Mountain View, CA 94043, USA** Note: The data transfer to the USA associated with the data transmission to Google takes place on the basis of the European Commission’s adequacy decision of 10 July 2023 (EU-U.S. Data Privacy Framework).