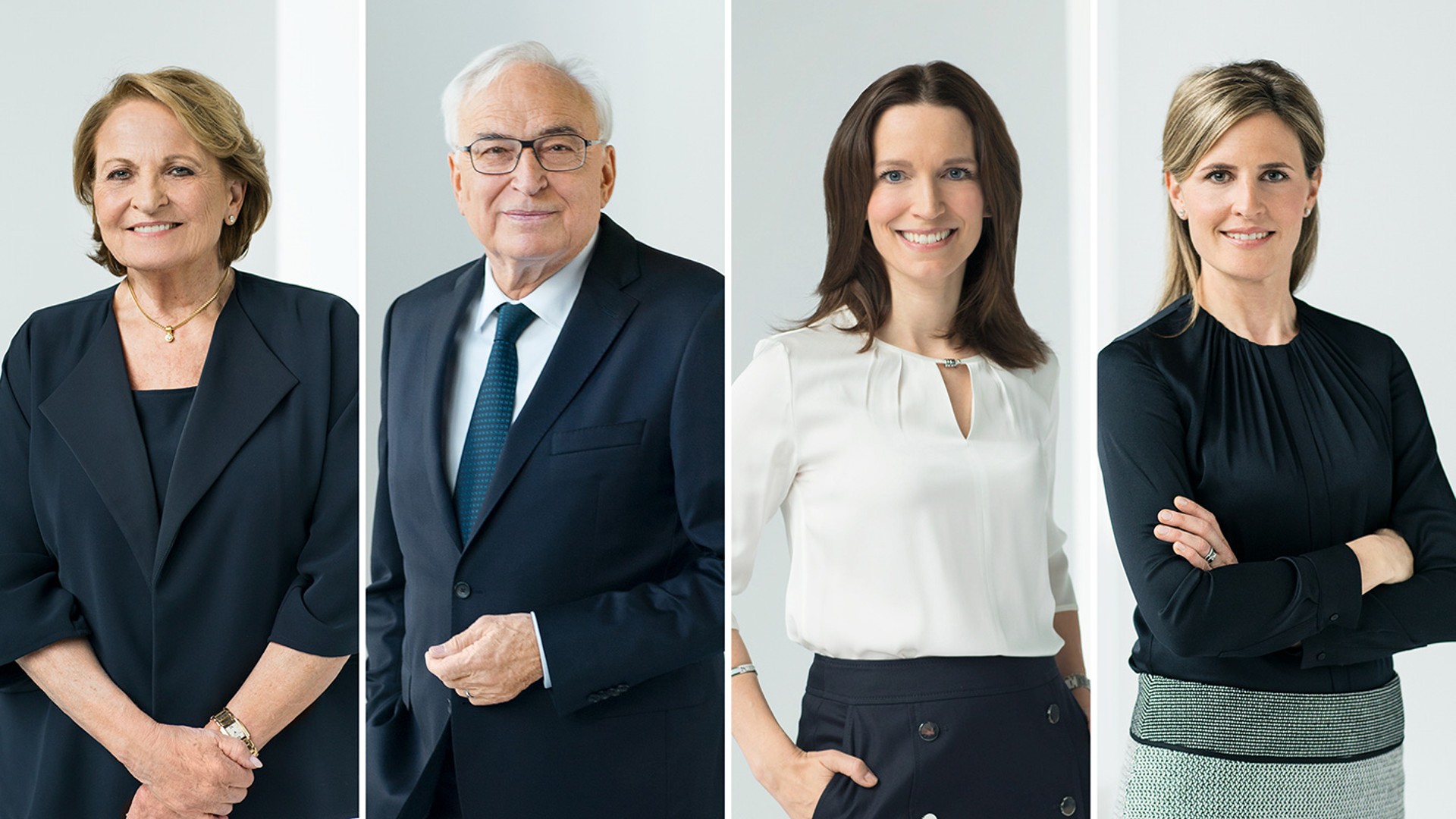
7 minutes reading time
“We will emerge stronger from this phase, too”
In conversation with Dr. h.c. Isolde Liebherr, Vice President of the Administrative Board of Liebherr-International AG, Dr. h.c. Willi Liebherr, President of the Administrative Board of Liebherr AG, and Sophie Albrecht and Patricia Rüf, members of the Administrative Board of Liebherr-International AG.
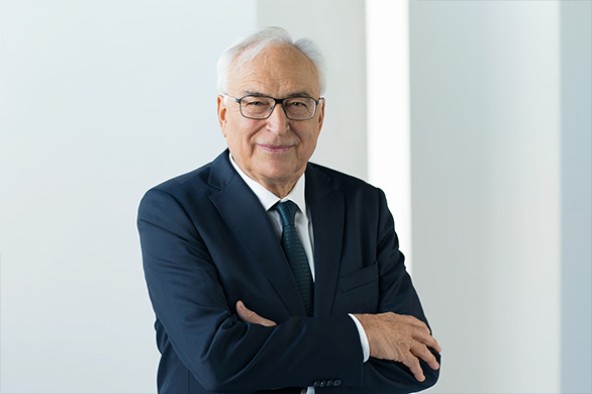
1
It was roughly one year ago that we were sitting together and discussing the upcoming financial year. And soon after this, the coronavirus started to change the world in ways we could never have imagined. Can you describe what it was like for you at the beginning of the pandemic?
Willi Liebherr: We received reports that a virus was spreading around China from staff based at Liebherr’s Chinese subsidiaries. And this was subsequently confirmed by the media. At the beginning of February, we had to shut down our Chinese manufacturing companies, and our employees working in China switched to remote working. We only really realised the global extent of the virus at the beginning of March when the situation in Europe started to look more serious.
Sophie Albrecht: I can remember it really well. I was visiting Conexpo, the construction machinery trade fair in Las Vegas. The atmosphere was very different — you could sense a general feeling of uncertainty. We had been looking forward to meeting our customers from Asia, but they were unable to travel. On some stands, machinery was on display but there were no personnel. And people had also stopped shaking hands when they greeted each other. Whilst I was at the trade fair, the situation in Europe changed dramatically. The borders were closed shortly after I returned and we had to partially or completely shut down production at many of our sites. It was really surreal and difficult for us all to comprehend at first. But it soon became clear that we needed to learn how to adapt to the situation as quickly as possible.
2
How did the outbreak of the pandemic affect you personally?
Isolde Liebherr: It affected us the same way as it did many other families. Our lives were suddenly very different. We had to practice social distancing and were continually worried about contracting the virus or passing it on to others. We also kept contact with our children and grandchildren to a minimum. It is difficult not seeing them very often.
Patricia Rüf: Having to suddenly adjust to living every day within the much narrower confines of our homes and having to dramatically reduce our contact with others is a big change. Face-to-face contact with our customers and employees as well as regular to customer and our companies and offices all around the world are an important part of our jobs. This all disappeared overnight. Fortunately, we were able to keep the communication lines open thanks to digital technology. However, I can’t wait to meet people in person again and speak to them face-to-face.
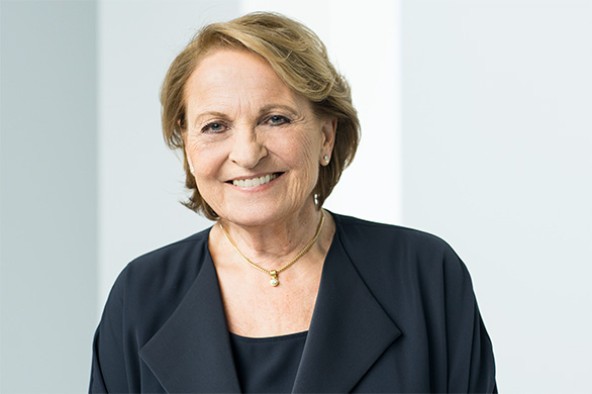
3
What were the biggest challenges from a business perspective during this time?
Willi Liebherr: This unprecedented situation has unquestionably had an impact on the entire Liebherr Group. We had to strike a balance between protecting every Liebherr employee and ensuring that our factories and company offices continued operating. As a family-owned business, the health and well-being of our employees is our top priority. We responded quickly to facilitate remote working wherever possible. We modified shift patterns, converted cantines, implemented the ‘Hands. Face. Space’ rule and provided face masks and disinfectants. And we also listened. We appreciated every suggestion for improvement that we received from members of staff.
Isolde Liebherr: At the beginning, the economic uncertainty, global lockdowns and supply chain disruptions thankfully only resulted in a few cancelled orders and our companies only had to be closed on a temporary basis. Looking back, it’s fair to say that we quickly got the situation under control. The Group’s decentralised structure has once again worked to our advantage. We were able to manage the Group at a central level, whilst allowing our companies to respond as they saw fit and take into account requirements based on the country, region and specific legal situation.
4
What conclusions do you draw from this?
Patricia Rüf: The pandemic and its effect on conditions in general must not stop us from looking positively into the future. We’ve learned that unforeseeable circumstances can quickly turn everything on its head. But we’ve also learned that we are capable of dealing with these kinds of situations. We are a strong, financially independent company. Our job is to make sure this continues to be the case. And it became apparent one again that we are flexible. We are able to react quickly to changing circumstances. To put it briefly, we have proven that we are an adaptable company. We have been able to progress during the pandemic. We have digitalised numerous processes and found new ways to collaborate with our customers and partners. We are working on new development projects and processes and will continue to do so. All of this allows us to look forward to a bright future. We will emerge stronger from this phase, too.
5
Some product segments were more severely affected by the pandemic than others. Can you tell us a little more about that?
Sophie Albrecht: Many product segments continued to perform well, however, the Aerospace and Transportation Systems product segment was hit particularly hard. Our hotels were also badly affected. It is difficult to say when these segments will begin to recover, we firmly believe that they will.
Willi Liebherr: Unfortunately, we had to introduce a number of HR policy measures in the aerospace segment. We’ve done everything to minimise the impact of this and have tried, wherever possible, to find solutions that take into account the needs of the people at the heart of our business. We also need to direct our focus towards the future and continue driving forward our research and development roadmap. This is why our R&D budget remains high. Our customers know that this is a priority for us and continue to regard us as important partners for joint R&D projects. This will strengthen our position over the long term.
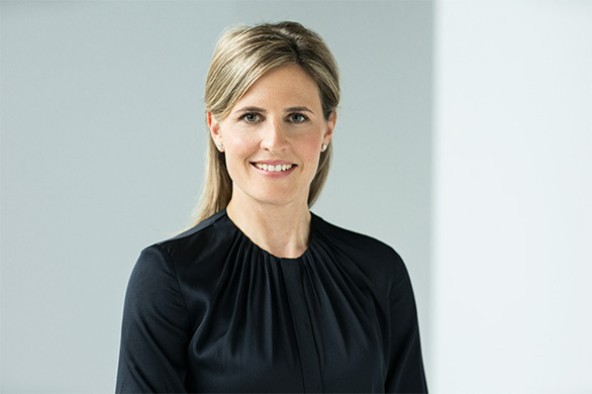
6
Nearly 48,000 people work for Liebherr all around the world. What measures are you currently taking to safeguard jobs?
Patricia Rüf: Anyone who experienced the financial crisis whilst working at Liebherr back in 2008 and 2009 will remember that the Group introduced every possible type of measure to safeguard jobs. The same applies to the current situation. We are very happy that we could keep our headcount stable throughout 2020. We’ve introduced some measures to cushion the impact of the pandemic on our employees. For example, we have introduced short-time working, temporarily reduced working hours and have ensured that we continue to pay wages at all times. We’ve also boosted certification programmes and enabled employees to transfer to other departments. In addition, we’ve temporarily redeployed staff at different sites in order to balance out capacity fluctuations between our manufacturing facilities.
7
Let’s turn to some of the Group’s key figures. Liebherr achieved a turnover of € 10.341 million. What does this mean to you?
Isolde Liebherr: We already knew during the spring of 2020 that we would not meet our sales forecast for the year and we soon realised that we would have to factor in a substantial drop in sales. However, as the year went on, we were able to make up for the lost months in some of our product segments. We are very satisfied with the results, considering the circumstances.
8
How would you assess the operating result?
Sophie Albrecht: We are pleased that we were able to achieve a small positive operating result. Despite difficulties in the currency markets and tax accounting challenges, we were able to report a moderately positive result after tax.
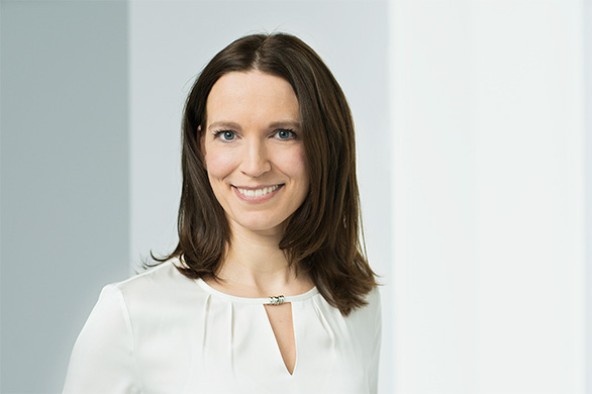
9
How has the situation looked across the different markets?
Patricia Rüf: Sales have grown substantially in China, Japan, Australia and Austria in some areas. Our service and after-sales business has been particularly strong in Australia, for example. We also benefited from the rollout of large infrastructure projects and the strong mining and wind power sectors. There was also positive growth in China, primarily because the Chinese economy recovered so quickly from the crisis. The Components and Mining product segments have also received some great orders.
Sophie Albrecht: Sales declined most notably in the UK, France, Canada and the USA due to a range of factors. The decline in the Aerospace and Transportation Systems segment could be clearly felt. Other key factors include currency fluctuations and the fact that construction projects were in parts halted or postponed. Supply chain disruptions during March and April also prevented us from delivering some of our products on time. For some product segments, it was impossible to offset the effects of this over the course of the year.
Our employees have shown an amazing amount of commitment, creativity and loyalty. We would not have gotten through the year without them.
10
What were the key milestones and highlights of 2020 for you?
Isolde Liebherr: I think an overwhelming feeling of togetherness is what will stay with me the most. We have all had to deal with an extremely challenging year on a personal level. And despite this, our employees have quickly adapted to new ways of working and shown an amazing amount of commitment, creativity and loyalty. We would not have gotten through the year without them.
The performance of our Refrigeration and Freezing product segment has also been a particular highlight for me. For the first time in our company’s history, we posted a net turnover of 1 billion euro for this segment.
I was also delighted when I found out that some of our chefs had received prestigious awards from Gault&Millau Austria. Our head patissier at the Interalpen-Hotel Tyrol was awarded ‘Patissier of the Year’ and our head chef at the Löwen Hotel in Montafon won his third Gault&Millau toque. These are truly remarkable achievements.
We are able to provide our customers with high-quality products and services, even during difficult times.
Willi Liebherr: I was particularly pleased that despite a fall in sales, the order book for Earthmoving was much healthier by the end of the year compared to its starting position in January. We were also able to continue developing new technologies such as electric drive concepts in our Materials Handling Technology segment. I think we can draw very positive conclusions from this which apply across the entire Group.
2020 also marked an important anniversary — our 50th year in the USA. We celebrated this special event at Conexpo in Las Vegas with the slogan “50 Years United by Success”. It was great to celebrate this event with some great machinery on show.
Our Concrete Technology segment also reached an important milestone in 2020 when it delivered its 100,000th truck mixer manufactured since 1967.
Liebherr Aerospace was also awarded the “Best Supplier Award” by Comac and Embraer. We were very pleased to be honoured with such an accolade, which demonstrates that we are able to provide our customers with high-quality products and services, even during difficult times.
I was pleased to see the strides we are continuing to make in digitalisation across the Group.
Patricia Rüf: I was pleased to see the strides we are continuing to make in digitalisation across the Group. This was particularly evident in the first-ever remote assembly of a mobile harbour crane. Our team of technicians based in Germany assisted with the construction of the crane in Argentina using our digital service app.
We are also very excited to be one of the founding members of the “Center Construction Robotics“ project. The project is being run by a consortium of companies from Europe and an interdisciplinary team of researchers at RWTH Aachen University who are working together to develop “the construction site of the future”.
Another highlight was that we were able to maintain our position as the global market leader of duty cycle crawler cranes within our Deep Foundation Machines segment.
A number of innovations were also premiered by our Gear Technology and Automation Systems segment, including the LGG 500 gear grinding machine, the LK 280 DC gear skiving machine and an innovative automated assembly concept for battery packs.
Sophie Albrecht: I was very pleased that despite the conditions last year we were able to present several products to the world in the digital space. This included the LR1250.1, which is the world’s first battery-powered crawler crane, the TA 230 Litronic articulated dump truck and a new addition to our mobile crane fleet, the LTM 1150-5.3. We are also very pleased that sales remained high for our Mobile and Crawler Cranes segment and that we could efficiently resume crane deliveries following the difficult period in March and April.
Our Mining segment also achieved great things in the customer service arena. The team pulled out all the stops to provide each customer with the best possible solutions. The 1,000th mining excavator also rolled off the production line — an achievement we are particularly proud of.
We also learned that Asia continues to be an important market for the Components division, particularly the wind energy sector. This is why we are investing in new facilities in China and India.
We are promoting new ways of working through our new digital technologies.
11
You have already touched on the fact that Liebherr is working on a wide range of digital technologies. But a lot is also happening in the area of product stewardship. Could you outline what is happening on this front?
Sophie Albrecht: Product stewardship means ensuring that our products are safe, efficient and environmentally friendly. Workplace safety and emission reduction are therefore key components of our development work. You only need look at the many innovations that are mentioned in the 2020 Annual Report. These include the electrification of the T 236 mining truck and the fully-electric and hybrid construction machines, such as the LR 1250.1 unplugged crawler crane and the ETM 1005, our fully electric truck mixer. We are also working on fuel cell systems for mobile equipment in Aerospace and Transportation Systems.
And we are promoting new ways of working through our new digital technologies. Our condition monitoring solution allows our customers to monitor the life cycle of their machinery and components at any time. Our augmented reality tools and Remote Service App enable us to provide excellent customer service and maintenance solutions which help to avoid multiple visits. Our digital services, such as the Crane Planner and MyJobsite, also help our customers to carefully plan on-site activities before they even use any construction machinery.
12
Finally, can you give us your outlook for the current financial year?
Willi Liebherr: We are certain that this year is going to be better, and our sales forecasts are looking promising.
We also have good reason to feel more optimistic due to changes in the geopolitical situation, now that there no longer appears to be a major trade war on the horizon and renewable energy solutions are becoming increasingly relevant. This opens up many opportunities in the future, and we are certainly in a good position to offer plenty of excellent solutions.
We strongly believe that the technical projects we have already initiated have put us on the right track for the future. And this is why investing in the future is and will remain so important to us. We believe that investment is a critical factor for healthy growth and for the future of our company. This also applies to the current financial year.
Thank you very much for your time and for providing such interesting insights.