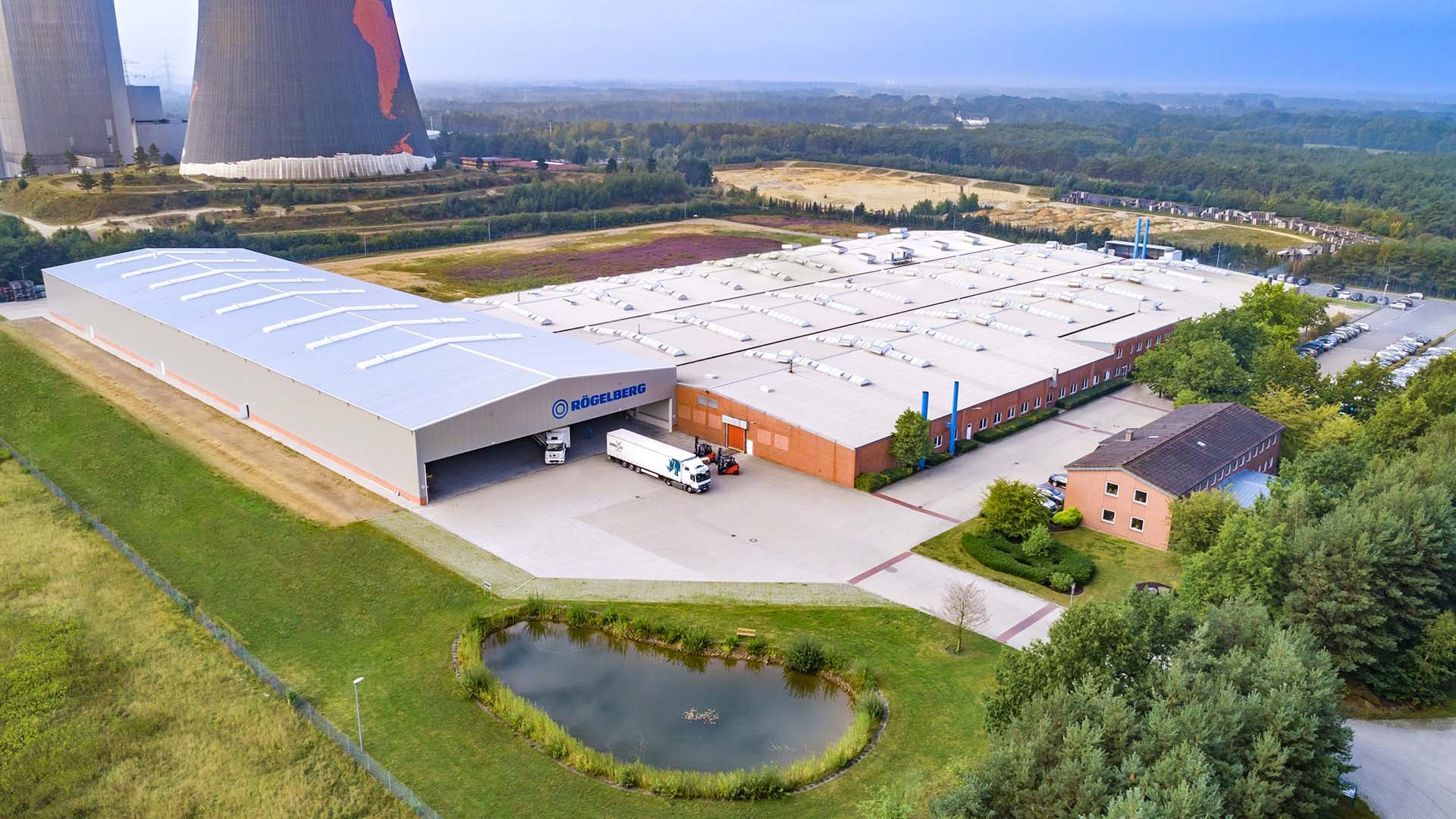
Trustworthy partnership over decades
The special gearbox manufacturer Rögelberg has relied on machines and tools by Liebherr-Verzahntechnik GmbH for many years now. The crucial factor is not just the high quality but also the good service – and above all, profound trust in the expertise of the Liebherr experts.
In Meppen, Emsland, Rögelberg Getriebe GmbH & Co. KG, with its 250 employees, manufactures special gearbox solutions for agricultural machines, forklift truck and municipal technology, and other areas of mechanical engineering. The company was founded in 1948; its special features are the in-house development of customized special solutions and a high level of vertical integration. Rögelberg sees itself as a system partner which advises its customers at the same level, develops the best possible solution together with them, and manufactures it economically.
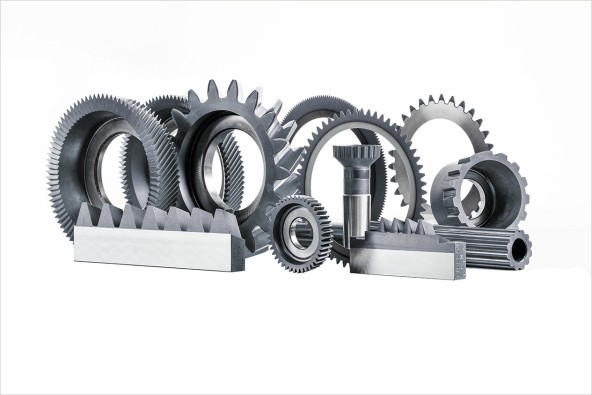
Liebherr gear cutting tools
Reliable machines, reliable partners
The company sets very high standards in terms of quality. Process reliability and flexibility are decisive factors for this. It requires reliable machines and tools of high precision, great flexibility and – if necessary – fast availability. Just as important is a good relationship with partners and suppliers. A trustworthy partnership has existed with Liebherr-Verzahntechnik GmbH for decades. “We already had such good results with the first gear shaping machine that we have continually expanded the cooperation since then”, reports Hermann Pleus, Head of Equipment Planning at Rögelberg. There are now four gear shaping and three gear hobbing machines by Liebherr in production in Meppen.
Tools and tool reconditioning
Rögelberg also uses almost the entire range of shaping tools from Liebherr’s product range and regularly makes use of the tool sharpening service in Ettlingen. “Our quality standards for tool reconditioning are extremely high, and fast response times are crucial for us”, says Pleus. Since the shaping tools are duplicated in Meppen and in Ettlingen – and can be sent back and forth in a very short time – Rögelberg also saves a considerable amount of time.
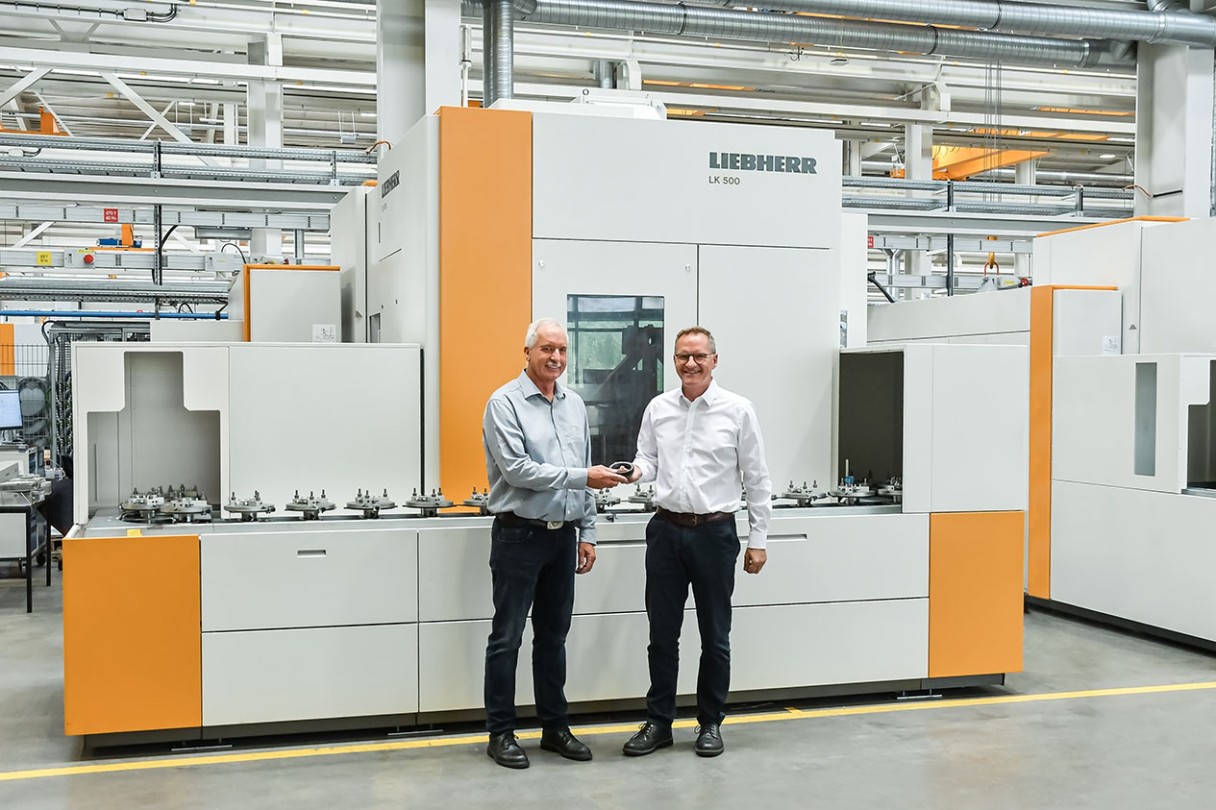
Satisfied customers: Hermann Pleus, Head of Equipment Planning at Rögelberg with tool expert Marcel Sobczyk, Liebherr-Verzahntechnik GmbH
When things have to happen quickly: “Fast Lane”
Flexibility and response times play an increasingly important role. This is also confirmed by Haider Arroum, Head of Sales for Gear Cutting Tools at Liebherr-Verzahntechnik GmbH: “The time pressure in manufacturing is increasing. That’s why we have a “Fast Lane” for particularly urgent commissions: In a very short time, we can grind customized tools from a whole piece, i.e. directly from the hardened blank. Rögelberg has also already used this service.”
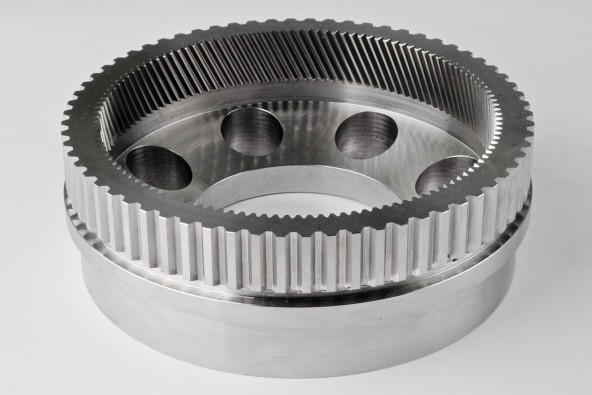
Demanding workpiece: Internal gear with internal helical teeth
Contract manufacturing with Skiving³
Rögelberg has even put the production of a particularly demanding workpiece, an internal gear with internal helical teeth, in Liebherr’s hands. “Because of our high vertical integration, we only outsource a few operations. But we can rely 100% on Liebherr”, Pleus explains. In contract manufacturing, Rögelberg is now relying on efficient and productive gear skiving in addition to classic gear shaping. The technology package Skiving³ pools Liebherr‘s expertise with regard to coordination between the machine, tool and technology in this complex process. Pleus summarizes the unique collaboration as follows: “It is rare to have such a trustworthy and comprehensive collaboration with a supplier over so many years. But the Liebherr team is always there with guidance and support, and knows what is important. We communicate on an equal footing.”
Rögelberg Getriebe GmbH & Co. KG
Industry:
Mechanical engineering / gear manufacturing
Company headquarters:
Meppen
Employees:
Around 250
Founded:
1948
Website: