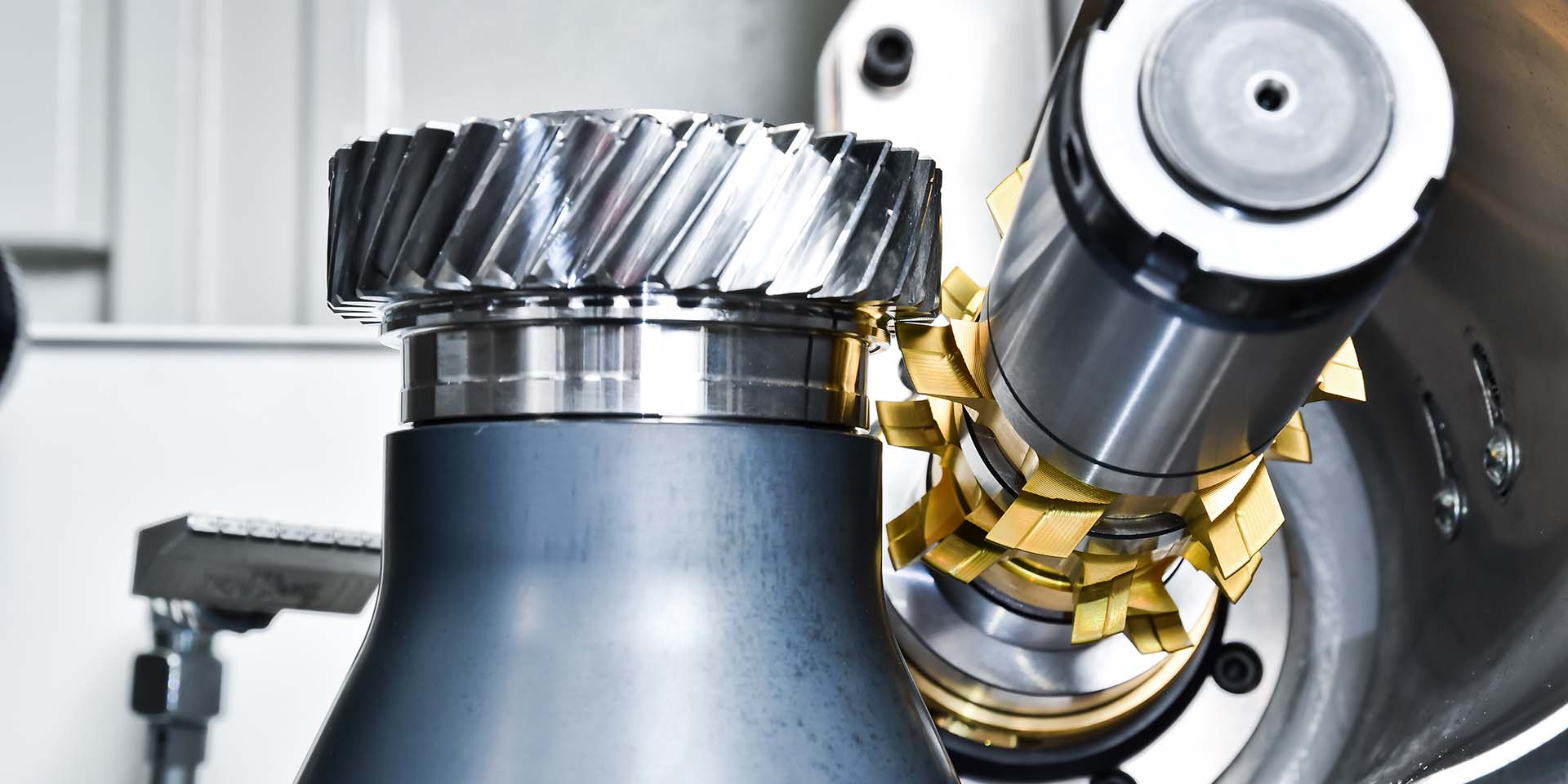
Precise – reliable – cost-effective
After chamfering with the patented ChamferCut technology, no additional machining is necessary. There is no need for a second cut, which is often required during the deformation-based deburring process for the removal of build-up material. With the chamfering process, the exact chamfer form is produced. In contrast to deformation-based processes, the material structure is not affected. An optimal starting point is created for the subsequent finishing of hardened gears, particularly gear honing. The quality of such chamfers defines a new standard – with maximum repetitive accuracy.
Advantages
By clicking on “ACCEPT”, you consent to the data transmission to Google for this video pursuant to Art. 6 para. 1 point a GDPR. If you do not want to consent to each YouTube video individually in the future and want to be able to load them without this blocker, you can also select “Always accept YouTube videos” and thus also consent to the respectively associated data transmissions to Google for all other YouTube videos that you will access on our website in the future.
You can withdraw given consents at any time with effect for the future and thus prevent the further transmission of your data by deselecting the respective service under “Miscellaneous services (optional)” in the settings (later also accessible via the “Privacy Settings” in the footer of our website).
For further information, please refer to our Data Protection Declaration and the Google Privacy Policy.*Google Ireland Limited, Gordon House, Barrow Street, Dublin 4, Ireland; parent company: Google LLC, 1600 Amphitheatre Parkway, Mountain View, CA 94043, USA** Note: The data transfer to the USA associated with the data transmission to Google takes place on the basis of the European Commission’s adequacy decision of 10 July 2023 (EU-U.S. Data Privacy Framework).The ChamferCut process
- Very precise chamfer geometry
- Premium chamfer quality and reproducibility
- No bulging or material deformation
- Standard tooth-root chamfering
- Established process in gear production
- Very long tool life
- ChamferCut tools can be re-sharpened approx. 20 times easily and cost-effectively
- Lower tool costs compared to alternative processes
- Short amortization period due to low tool costs
- Applications for gears with module 0.8-42 mm
- 2nd cut not needed for gear hobbing - longer tool life for the hobbing tool
- Short setup time
Videos
- ChamferCut
- LC 180 DC
- LC 300 DC
- LD 300 C
By clicking on “ACCEPT”, you consent to the data transmission to Google for this video pursuant to Art. 6 para. 1 point a GDPR. If you do not want to consent to each YouTube video individually in the future and want to be able to load them without this blocker, you can also select “Always accept YouTube videos” and thus also consent to the respectively associated data transmissions to Google for all other YouTube videos that you will access on our website in the future.
You can withdraw given consents at any time with effect for the future and thus prevent the further transmission of your data by deselecting the respective service under “Miscellaneous services (optional)” in the settings (later also accessible via the “Privacy Settings” in the footer of our website).
For further information, please refer to our Data Protection Declaration and the Google Privacy Policy.*Google Ireland Limited, Gordon House, Barrow Street, Dublin 4, Ireland; parent company: Google LLC, 1600 Amphitheatre Parkway, Mountain View, CA 94043, USA** Note: The data transfer to the USA associated with the data transmission to Google takes place on the basis of the European Commission’s adequacy decision of 10 July 2023 (EU-U.S. Data Privacy Framework).ChamferCut
By clicking on “ACCEPT”, you consent to the data transmission to Google for this video pursuant to Art. 6 para. 1 point a GDPR. If you do not want to consent to each YouTube video individually in the future and want to be able to load them without this blocker, you can also select “Always accept YouTube videos” and thus also consent to the respectively associated data transmissions to Google for all other YouTube videos that you will access on our website in the future.
You can withdraw given consents at any time with effect for the future and thus prevent the further transmission of your data by deselecting the respective service under “Miscellaneous services (optional)” in the settings (later also accessible via the “Privacy Settings” in the footer of our website).
For further information, please refer to our Data Protection Declaration and the Google Privacy Policy.*Google Ireland Limited, Gordon House, Barrow Street, Dublin 4, Ireland; parent company: Google LLC, 1600 Amphitheatre Parkway, Mountain View, CA 94043, USA** Note: The data transfer to the USA associated with the data transmission to Google takes place on the basis of the European Commission’s adequacy decision of 10 July 2023 (EU-U.S. Data Privacy Framework).ChamferCut
Economic efficiency
Workpiece (chamfering) | |||
Workpiece | speed gear | ||
Module | 2.7 mm | ||
Number of teeth | 41 | ||
Helix angle | 24.5° | ||
Press chamfering (with burnishing) | ChamferCut | ||
Press chamfering tool | 4,700 Euro | Chamfer cutter (set) | 3,600 Euro |
Number of re-sharpenings | 1 | 23 | |
Total workpieces | 95,445 | 468,293 | |
Tool costs/workpiece | 6.7 cents | 1.5 cents |