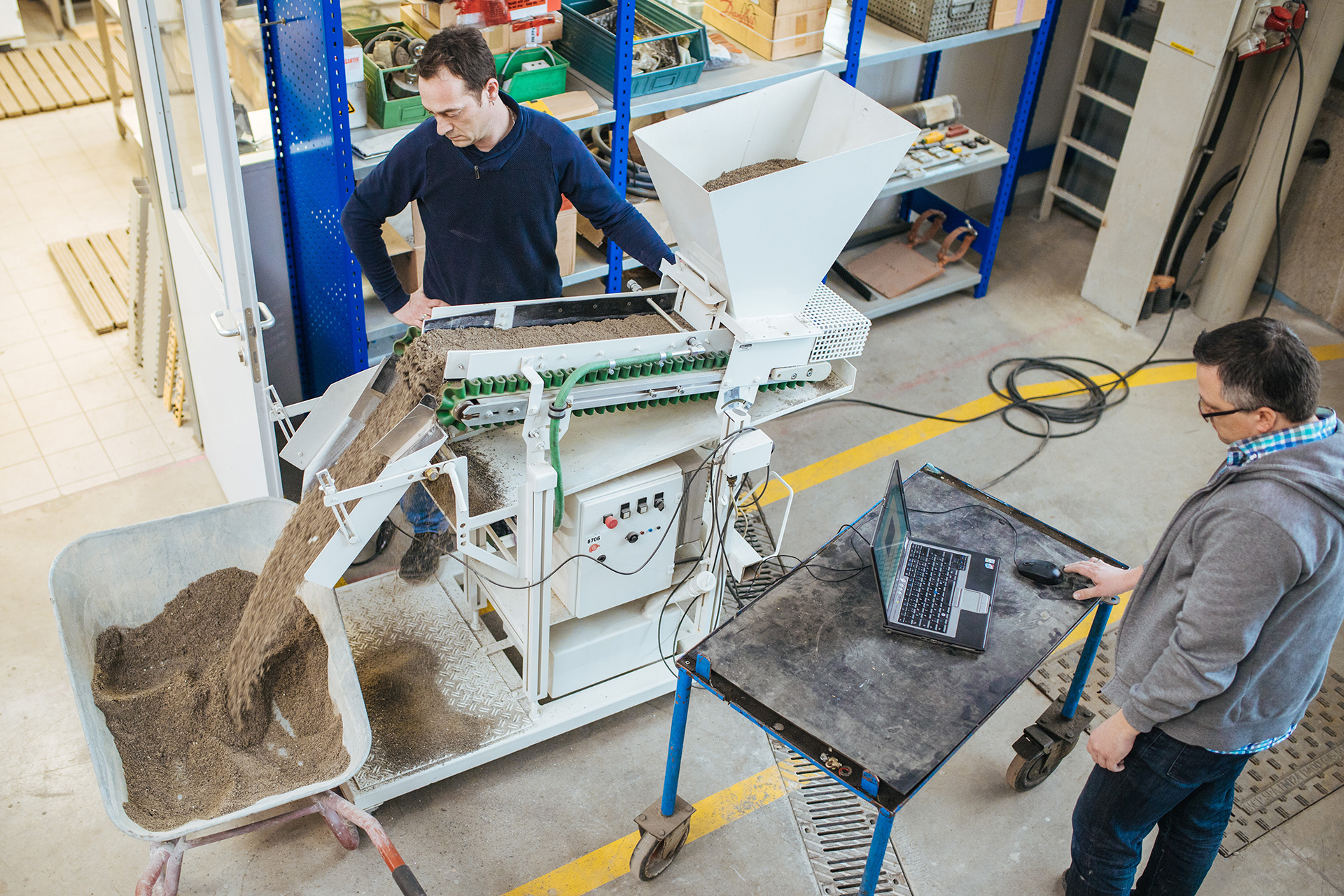
Click RELEASE VIDEO and follow the data protection notices.
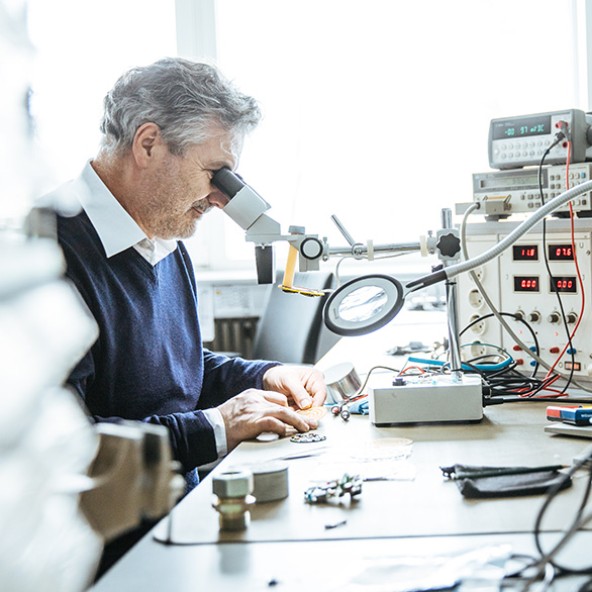
Solid as concrete
Concrete is a unique material: it starts with the right balance of cement, sand and gravel. Then, water is added, triggering a chemical reaction with the binding agent which turns the mixture into a durable, solid building material with practically limitless applications. Naturally, Liebherr's Concrete Technology division has always kept a close watch on the critical role of water and moisture in concrete production. Since 1985, Liebherr-Mischtechnik GmbH has been developing measurement systems for industrial automation at its production site for truck mixers, mixing plants and concrete pumps in Bad Schussenried, Germany. "It all started with sensors for measuring the moisture content of sand in our concrete mixing plants," explains Thomas Maier. A Liebherr employee since 1991, Maier is now head of global distribution for moisture sensors and related analytical systems.
"Today, Liebherr moisture measurement systems are used in production plants in every conceivable area of industry, from an automotive supplier in the USA to a paper mill in the Netherlands and a sugar manufacturer in Guadeloupe," says Maier.
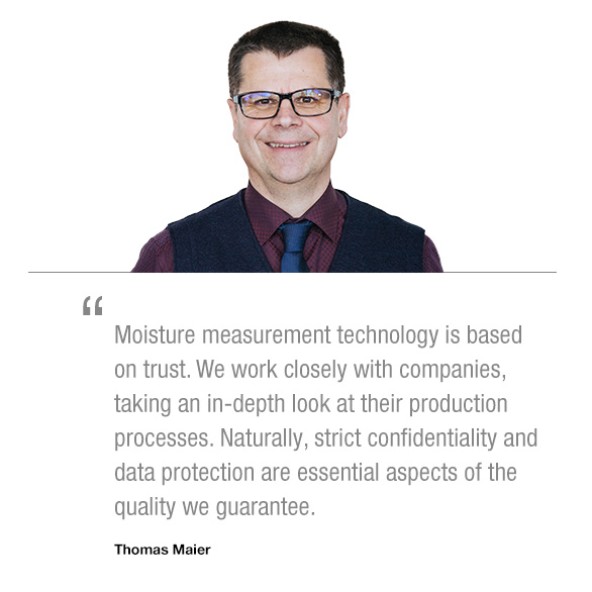
Small sensors, big technology
Customers are often surprised at first to discover that Liebherr is active in this specialised segment of measurement electronics, says Maier. "Our company’s reputation for high-performance products in the construction machinery sector is a big advantage for us", he explains.
In Bad Schussenried, developers take a remarkably hands-on approach to working with the machinery. Their laboratories and electrostatically shielded workstations are located directly above the assembly hall, where truck mixers and gigantic concrete mixing plants are manufactured. "Our team is small, specialised and highly skilled. There are three developers, one test engineer, one production employee and three sales employees. Together, we are a leading force in moisture measurement worldwide," says Maier with pride.
At the entrance to the laboratory are models which Maier uses during presentations at trade fairs and conferences, and during meetings with prospective clients, to demonstrate how the seemingly unremarkable rod and planar sensors and related analysis technology work.
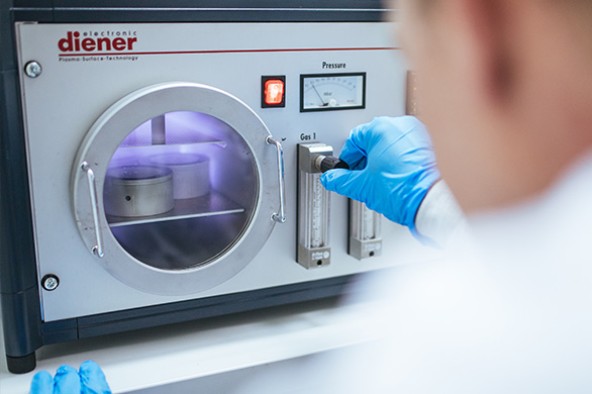
“Live” moisture management
"The sensors perform up to 40 measurements per second while a process is running," explains Maier. In the past, it would have been necessary to measure moisture in additives through random samples in the laboratory in order to determine the correct consistencies and to intervene in production to make any adjustments required. "Today, our technology lets us carry out moisture management 'live' and in real time, with the utmost precision", says Maier.
By clicking on “ACCEPT”, you consent to the data transmission to Google for this video pursuant to Art. 6 para. 1 point a GDPR. If you do not want to consent to each YouTube video individually in the future and want to be able to load them without this blocker, you can also select “Always accept YouTube videos” and thus also consent to the respectively associated data transmissions to Google for all other YouTube videos that you will access on our website in the future.
You can withdraw given consents at any time with effect for the future and thus prevent the further transmission of your data by deselecting the respective service under “Miscellaneous services (optional)” in the settings (later also accessible via the “Privacy Settings” in the footer of our website).
For further information, please refer to our Data Protection Declaration and the Google Privacy Policy.*Google Ireland Limited, Gordon House, Barrow Street, Dublin 4, Ireland; parent company: Google LLC, 1600 Amphitheatre Parkway, Mountain View, CA 94043, USA** Note: The data transfer to the USA associated with the data transmission to Google takes place on the basis of the European Commission’s adequacy decision of 10 July 2023 (EU-U.S. Data Privacy Framework).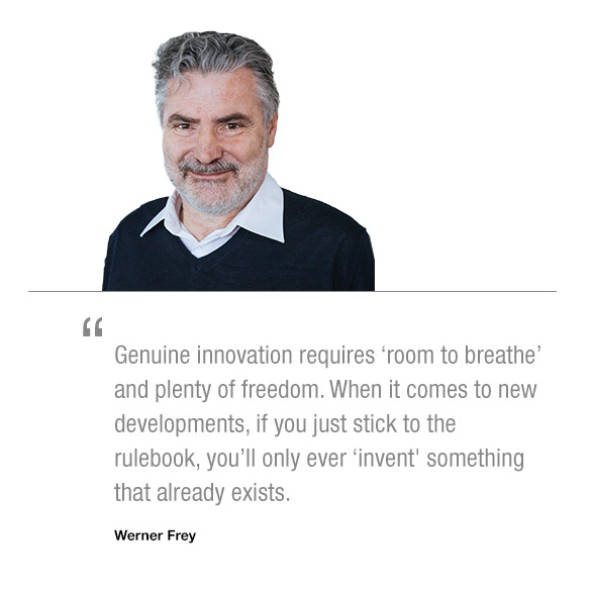
The inventor's mantra: Never stop thinking
Moisture measurement sensors are hardly noticeable at first glance. In fact, when testing sand or emulsions, scanning glass cullet or doing their work in a combine harvester, they are hardly even visible to the naked eye. They would be unlikely to win a design prize. Fortunately, moisture measurement at Liebherr has its own friendly face, Werner Frey. He has overseen the development of sensors for over 30 years. His inventions have had a major impact on modern industrial moisture measurement ever since he started working for Liebherr in 1987.
"At that time, my job was to set up an electronics laboratory and develop an analysis device for moisture measurement," he recalls. While completing this task, he became increasingly concerned about the poor quality of the moisture sensors he was given to work with. The supplier promised improvements, but these never materialised. "In the end, I started working on the side myself to develop and build the first microprocessor-controlled smart sensor for concrete-mixing plants," says Frey with a mischievous smile.
Soon, it became clear that what works for concrete can also work for other applications: for example, bulk materials, mining, agriculture, food, pharmaceuticals or petrochemicals.
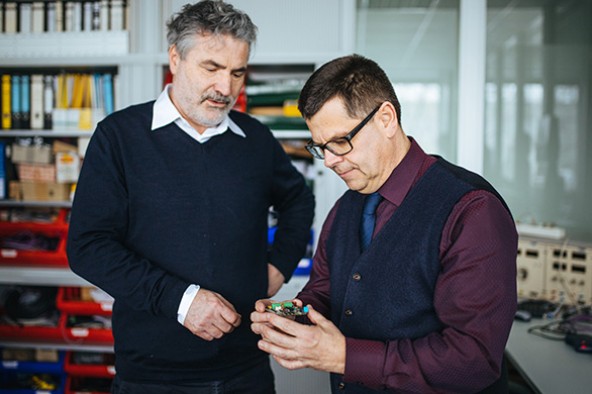
Readily reproducible systems
Measurement by Liebherr sensors is based on short waves. "No one else has figured out how to do it," says Frey. Other methods work with microwave technology, which is much more complex and prone to interference. In addition to their high precision and robustness, the measurement instruments from Bad Schussenried excel in terms of reproducibility. "Once the system has been calibrated, we can use it as a basis for configuring additional measuring points or renewing devices at any time with minimum effort. So, the equipment is always reliable, regardless of its age or service life to date," emphasises Frey.
By clicking on “ACCEPT”, you consent to the data transmission to Google for this video pursuant to Art. 6 para. 1 point a GDPR. If you do not want to consent to each YouTube video individually in the future and want to be able to load them without this blocker, you can also select “Always accept YouTube videos” and thus also consent to the respectively associated data transmissions to Google for all other YouTube videos that you will access on our website in the future.
You can withdraw given consents at any time with effect for the future and thus prevent the further transmission of your data by deselecting the respective service under “Miscellaneous services (optional)” in the settings (later also accessible via the “Privacy Settings” in the footer of our website).
For further information, please refer to our Data Protection Declaration and the Google Privacy Policy.*Google Ireland Limited, Gordon House, Barrow Street, Dublin 4, Ireland; parent company: Google LLC, 1600 Amphitheatre Parkway, Mountain View, CA 94043, USA** Note: The data transfer to the USA associated with the data transmission to Google takes place on the basis of the European Commission’s adequacy decision of 10 July 2023 (EU-U.S. Data Privacy Framework).The term ‘industry 4.0’ may be somewhat overused, but increasing automation in production is definitely increasing the demand for smart sensors. Moisture measurement is also in greater demand than ever.
View on the big picture
Frey is pleased that his one-man development operation has grown into a small, specialist team. "In our five-person development team, we can share the tasks. At the same time, everyone has a hand in everything: electronics- and physics-related issues, pre-development, production and documentation. We have a great time together, but it also means everyone has a lot of personal responsibility," says Frey.
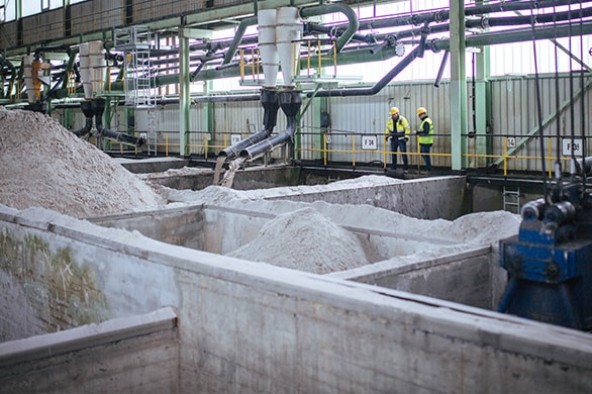
In tune with production needs
As much as Frey values the creative atmosphere of his development laboratory, he also enjoys how closely his work brings him in contact with customers. "We are constantly driving out to users and getting in touch with installation engineers and plant managers. This direct feedback from practical experience is part of our formula for success," he explains. One customer is the Quarzwerke Group. Its moist sand processing plant in Frechen, Germany, near Cologne, currently uses five Liebherr sensors. On his way to Filtech 2018, the international exhibition and conference for filtration and separation technology in Cologne, Frey's colleague Thomas Maier will take the opportunity to pay the customer a visit.
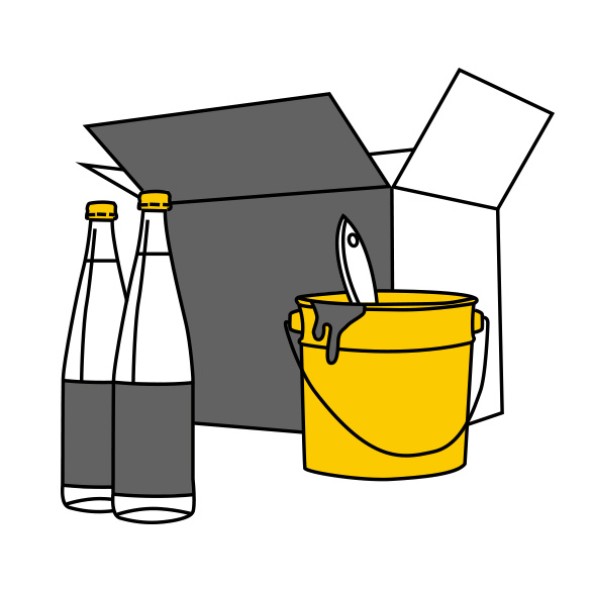
The wide world of moisture measurement
Liebherr moisture measurement technologies are used in numerous industries, including the processing of:
- concrete
- sand and other rock or mineral aggregates
- glass
- paper and cardboard
- diesel, oil and other emulsions
- coolants and lubricants
- paints and varnishes
- agricultural products
- foodstuffs
Rod- or disc-type planar sensors are typically found in silo outlets, chutes, baffle plates, belts, transfer points, drying systems, screw conveyors, pipes, tanks and many other locations.
The Liebherr moisture measurement in detail
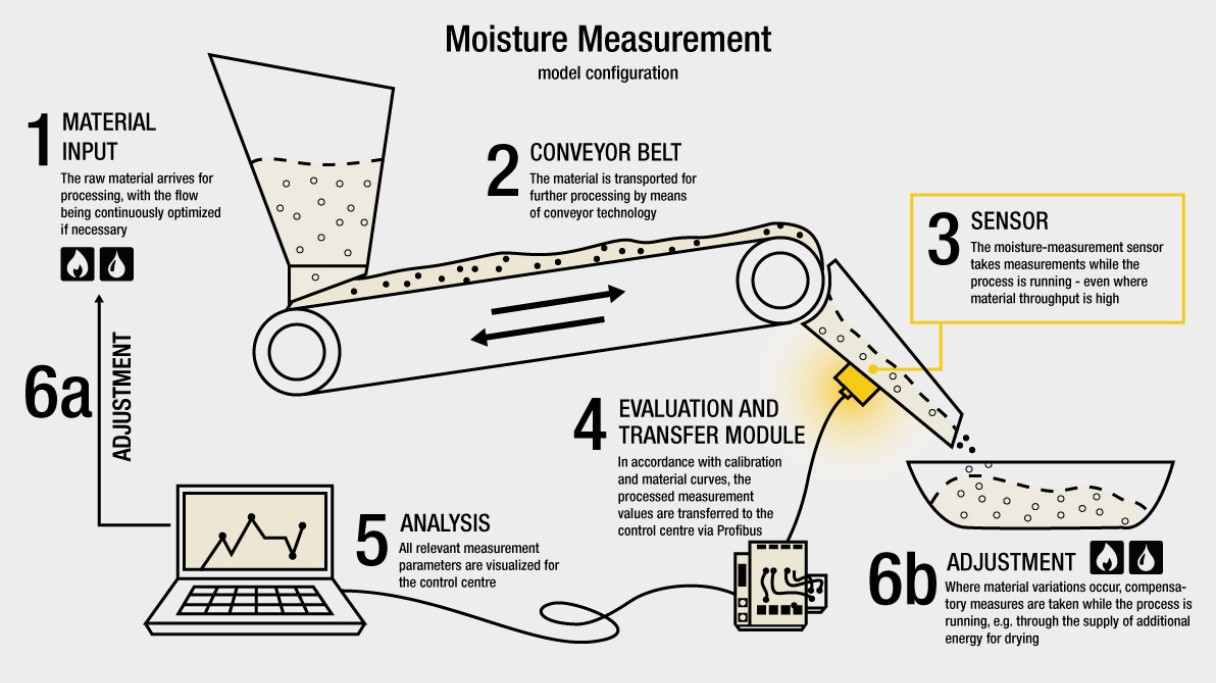
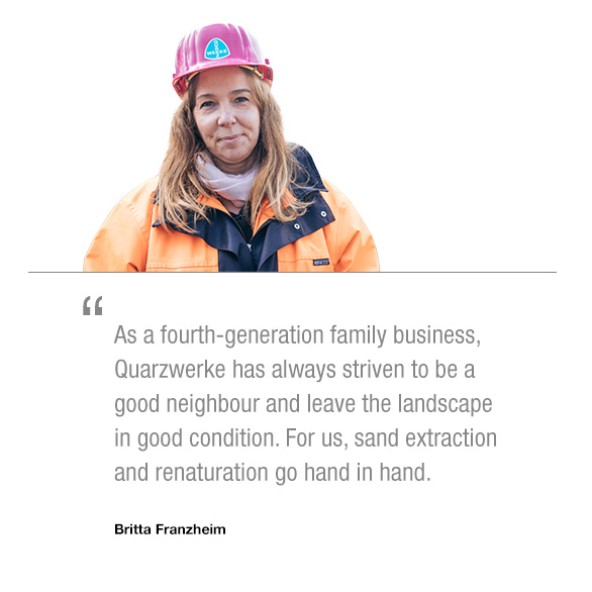
Quartz & Co.
Thomas Maier is welcomed to Frechen by Britta Franzheim, spokesperson for the international Quarzwerke Group. From a small viewing platform, Maier has an impressive view of the entire Quarzwerke site. "Quartz sand was discovered here as early as Roman times and was used to make glass," Franzheim explains. For over 130 years, the family business has followed in the footsteps of its ancient predecessors. A trained biologist, Franzheim is quick to emphasise that the site’s operations are "state-of-the-art and environmentally sustainable and, most importantly, sustainably successful. The quartz sand that occurs here in Frechen has a purity of over 99 per cent, making it suitable for any imaginable industrial process."
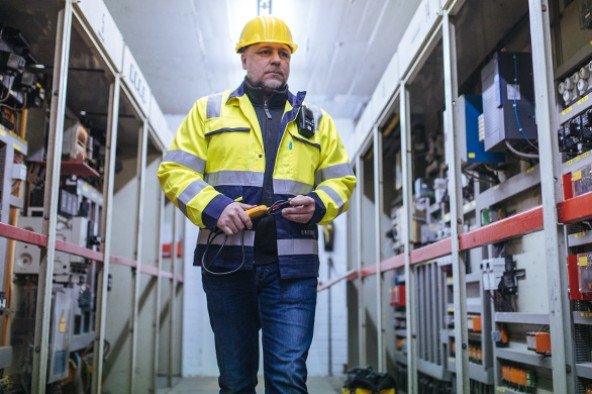
Sand for over 200 products
Quarzwerke processes the quartz sands excavated from its opencast mine into over 200 high-quality products sold in 50 countries. To do so, the company relies on state-of-the-art, efficient processing technologies. The plant’s equipment is under the watchful eye of Manfred Schaffgans, head of the e-workshop. He has worked for Quarzwerke for 32 years, starting his training here as an electrical fitter. Later, he qualified as a power plant engineer and finally received his certification to be an industrial supervisor in energy and electrical engineering.
Schaffgans knows the entire production plant like the back of his hand. He is familiar with even the smallest pieces of equipment and control units and keeps an eagle eye on every production step in the conveyor and drying systems. Occasionally, he glances at his phone to check the webcam feed of a peregrine falcon's nest that was discovered in one of the old silo towers.
By clicking on “ACCEPT”, you consent to the data transmission to Google for this video pursuant to Art. 6 para. 1 point a GDPR. If you do not want to consent to each YouTube video individually in the future and want to be able to load them without this blocker, you can also select “Always accept YouTube videos” and thus also consent to the respectively associated data transmissions to Google for all other YouTube videos that you will access on our website in the future.
You can withdraw given consents at any time with effect for the future and thus prevent the further transmission of your data by deselecting the respective service under “Miscellaneous services (optional)” in the settings (later also accessible via the “Privacy Settings” in the footer of our website).
For further information, please refer to our Data Protection Declaration and the Google Privacy Policy.*Google Ireland Limited, Gordon House, Barrow Street, Dublin 4, Ireland; parent company: Google LLC, 1600 Amphitheatre Parkway, Mountain View, CA 94043, USA** Note: The data transfer to the USA associated with the data transmission to Google takes place on the basis of the European Commission’s adequacy decision of 10 July 2023 (EU-U.S. Data Privacy Framework).Liebherr's online sensor technology and analytics form the basis of our active moisture management. They enable us to optimise sand-drying with surgical precision while also maximising energy efficiency.
Water everywhere
It is Friday morning and Manfred Schaffgans and Thomas Maier are going over the individual production steps and the five areas in which moisture measurement is used. The quartz sand extracted from the opencast mine is first washed, then dehydrated in the wet sand silo. "Water is everywhere here,"Schaffgans explains to his visitor. It is impossible not to hear the hissing and bubbling sounds in the background. The degree of moisture is critical when processing quartz sand, whether the end product is moist sand, quartz flour or filter sand. "The more precisely we measure, the faster and more efficiently we can monitor quality," says Schaffgans.
In the control centre, the moisture measurement data is fed into the system and displayed on a dozen monitors in real time. "Whenever fluctuations in quality occur in our natural product, we can intervene immediately, either by drying or by wetting it," explains Schaffgans.
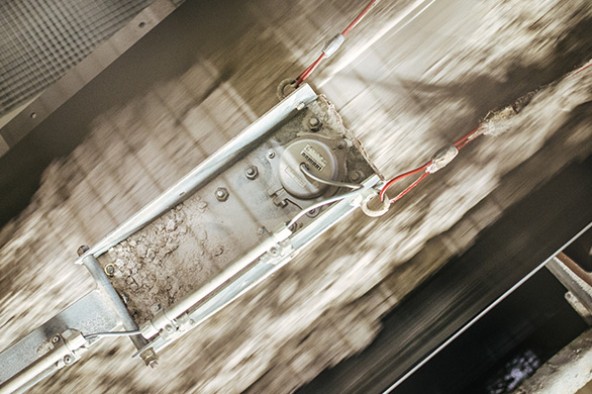
Quality makes the difference
Next, the two experts inspect the five measuring points. Here, the Liebherr sensor "surfs" on a metal sled on top of the sand, which the conveyors move in a continuous stream into the dryers and silos. The rushing sand acts like sandpaper against the metal sled, says Schaffgans. "That’s why we chose a particularly hard, durable metal," explains Maier. "To optimise the 'hardware' even further, we are keen to hear about experiences with day-to-day operations." Manfred Schaffgans is pleased to hear that. "It’s quality that makes the decisive difference – down to the smallest details of production," Schaffgans says. Standing still is not an option. "Development has to keep going." This is exactly what the researchers in Bad Schussenried like to hear.