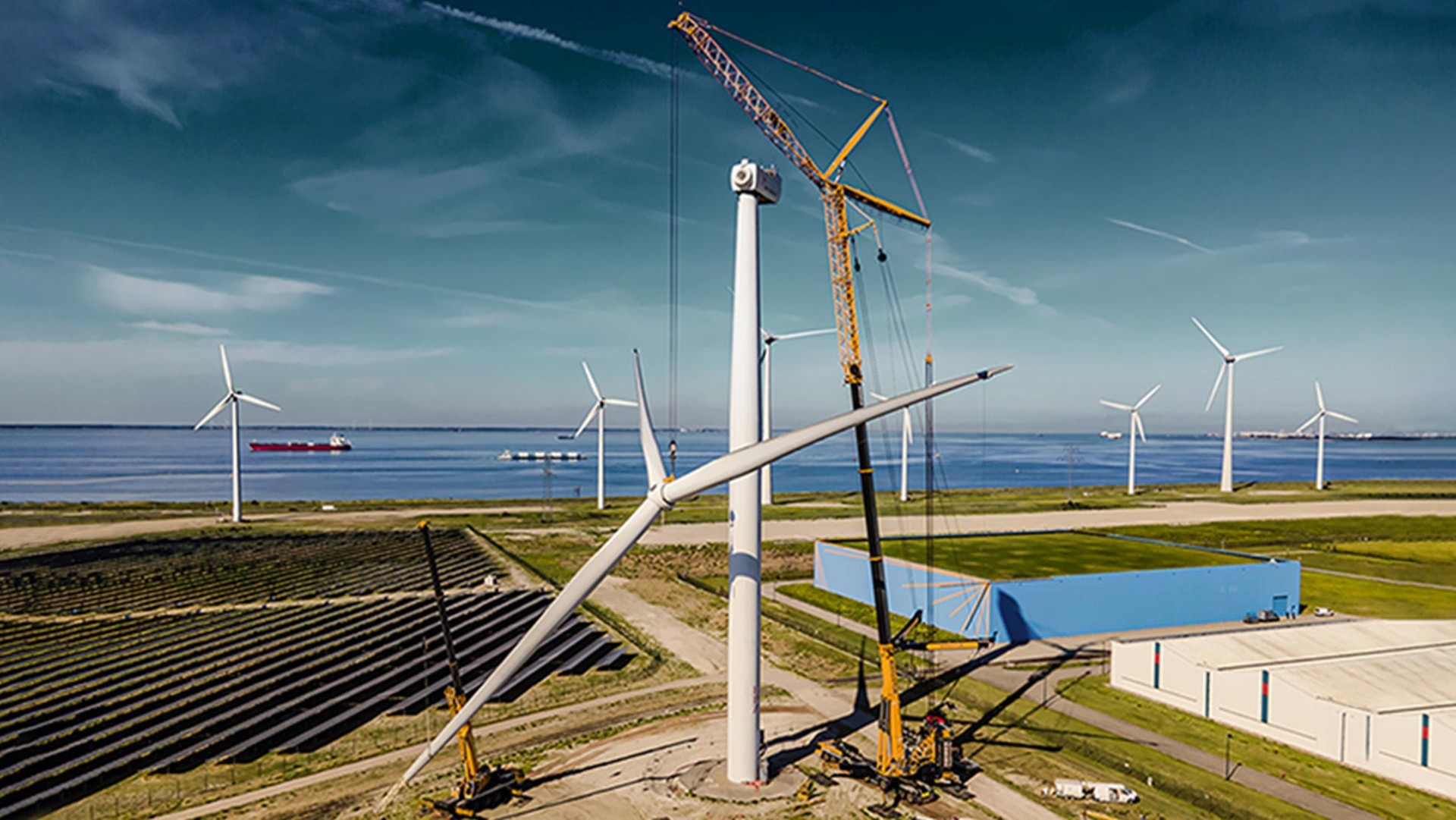
7 minutes | magazine 01/2021
More power – LTM 1750-9.1 with 800 t upgrade
Almost exactly one year ago, we announced that we would be upgrading our LTM 1750-9.1. We completely recalculated the 9-axle model, which was first launched in 2012, and actually made it into an 800 tonne crane.
The use of refined static calculation methods meant that lifting capacity values could be increased across almost its entire working range. We created a new luffing jib configuration to achieve additional performance increases for wind power applications, enabling the LTM 1750-9.1 to break into a higher lifting capacity class.
We tested the new lifting capacity values extremely carefully at our acceptance test site before the first cranes left the plant to prove themselves in the rugged everyday life of a crane. That makes us all the more delighted now to receive positive feedback from our customers and interesting photographs of jobs using the upgraded crane.
Performance offensive in the Netherlands
Our Dutch customer Kraanverhuur D. Boekestijn B.V. has been using its LTM 1750-9.1 with the 800 t upgrade, for example, to dismantle a 2.75 MW wind turbine at the port of Vlissingen. It removed a generator with a gross load of 87.8 tonnes and using a hook height of 90 metres from a 78 metre tower. In the past, these jobs would have required an LTM 11200-9.1 or even two LTM 1500-8.1 cranes operating in tandem. But this is now possible for the new 800 tonne crane and it even had a little over four tonnes of lifting capacity to spare. Perfect evidence that the LTM 1750-9.1 now really has advanced into a higher lifting capacity class.
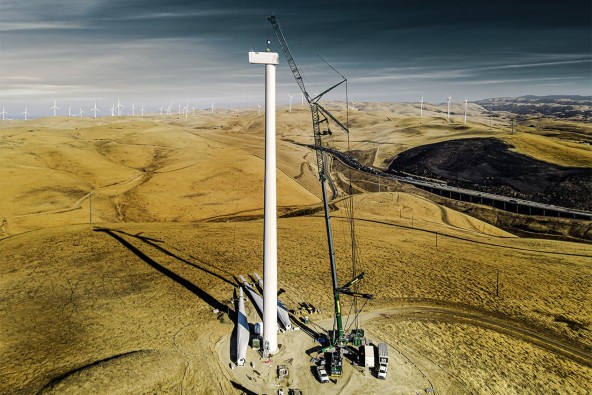
The 800 t upgrade made it possible to use the LTM 1750-9.1 at a wind farm in California.
Wind turbine erection in California
Our customer Mountain Crane, who were one of the first to receive the upgrade for its LTM 1750-9.1 in the USA, is also delighted: “The beginning of something great,” it posted on Facebook with photographs of the crane erecting a generator on a 90 metre tower at a wind farm in California. “Without the 800 t upgrade, our latest wind project would have been impossible. A constricted site and steep hills meant that a crawler crane could not be used. The LTM 1750-9.1 not only enabled us to move quickly and easily from one turbine to the next, but also saved a significant amount of money as we avoided road restrictions and we had no need for any civil engineering work,” explains Wind Director Travis Horton.
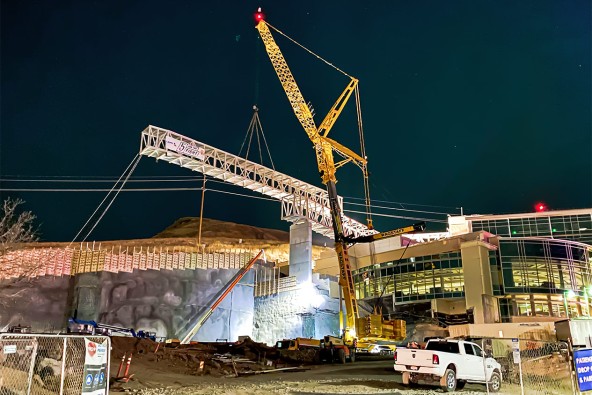
The upgraded LTM 1750-9.1 delivers sufficient power in reserve for the job in Utah.
Reducing costs in Utah
Power to spare was the order of the day for installing a pedestrian bridge at the Huntsman Cancer Institute at the University of Utah. The 50 metre steel bridge is part of a wide-ranging extension of the clinic complex. However, the site posed several challenges – it was in a busy traffic area, the space for the crane was limited, close to power lines and the clinic could not be closed. The clinic authorities therefore requested a crane with plenty of power to spare.
Ronnie Wagstaff, Project Manager at Wagstaff Crane Service, explains: “We planned this hoist a year ago with a range of different crane configurations. The fact that the LTM 1750-9.1 would have required 93 percent of its total capacity made several people a little nervous. We then even considered using a large crawler crane. But of course that would have been significantly more expensive. Then, fortunately, came the power upgrade. The new lifting capacity tables showed that the crane capacity utilisation was reduced to a maximum of 85 percent. That immediately gave the green light for completing the hoist with the LTM 1750-9.1!”
Wagstaff regards the 800 t upgrade as very positive for all the jobs tackled by the LTM 1750-9.1 and has particularly enormous improvements for jobs in the wind power industry. “The option to select additional maximum wind speeds in the crane control system is another helpful function. It can be used for every type of job. I love the fact that Liebherr continuously invests in improving its existing crane models”, says Wagstaff.
We are also interested in your experience of how innovations or special technical solutions have improved crane use. Please write to us at [email protected]. And, of course, we are always delighted to receive suggestions for improvements.
The best solution for our customers
As a crane manufacturer, we naturally have nothing against using larger cranes or even two cranes in tandem for certain jobs. We are quite happy to build them and sell them. But we also feel an obligation to find the best, most economical solution for our customers. When we manage to accomplish this, as with the jobs described in this article, not only are we pleased by the fact but it also encourages us to continue along this route.
This article was published in the UpLoad magazine 01 | 2021.