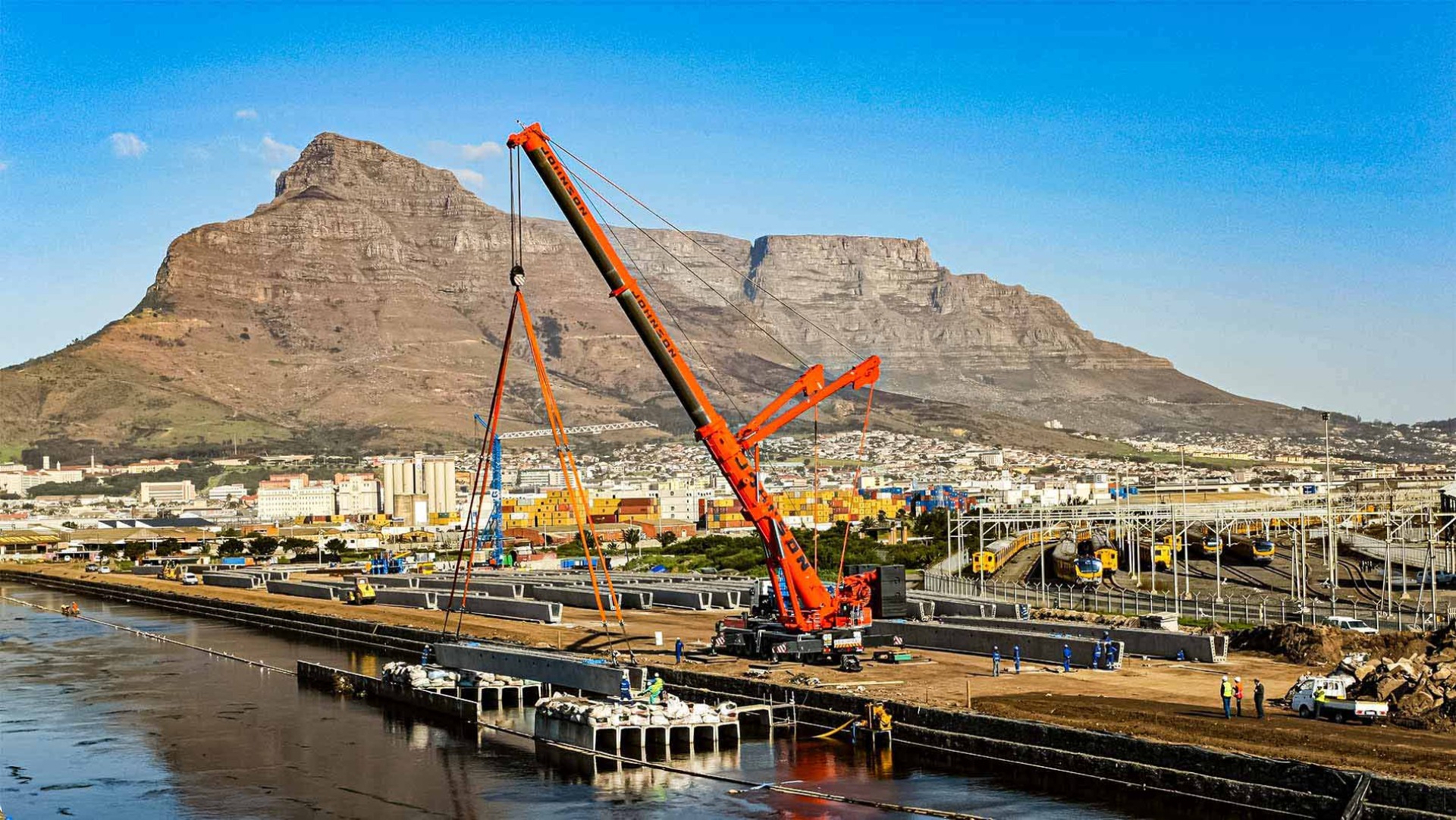
12 minutes | magazine 01/2020
Fantastic view
“This is the best crane in the world”, is how Uwe Langer described the LTM 1500-8.1, when he took delivery of the 500th crane of this model in March 2016 at the Liebherr plant in Ehingen.
A legend in its own lifetime
And there is every reason to believe that the Managing Director of crane and heavy haulage contractor Riga Mainz GmbH & Co. KG is absolutely correct. After all, he has decades of experience in the crane industry and already had several LTM 1500-8.1 units in his fleet. The success story of this Liebherr 500-tonne crane has carried on. Just four years later, in March this year, we handed over number 600 to its new owner. The crane was delivered to Korean crane contractor Crane Korea Co. Ltd.
There is no dispute that the LTM 1500-8.1 is the most successful large crane of all time. But, in fact, its predecessor was also a best seller – from 1988 to 1999, we delivered 140 LTM 1400 cranes. At the time, it set the bar high for eight-axle mobile cranes.
Twenty years later, we wanted to take a look back at crane history with some of the people behind its success. We talked to Yggve Richter, who dedicated several years of his life as a structural engineer to the LTM 1500*, Joachim Henkel, Head of the Structural Engineering Department, Norbert Leuze from the boom design team and Hans-Joachim Wenger from the Crane Control System Department.
* The LTM 1500 was renamed the LTM 1500-8.1 in 2004 when Liebherr started to include the number of axles and the version in the model name of all LTM cranes.
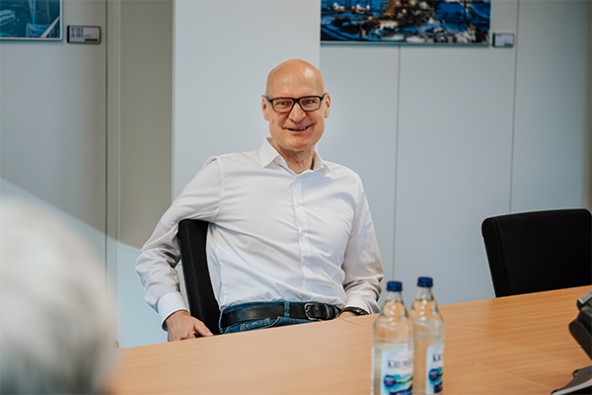
Joachim Henkel, Head of Structural Engineering
Did you have any idea at the time that we would deliver over 600 cranes?
Joachim Henkel: No, we had absolutely no idea that that would be the outcome. Although the LTM 1500-8.1 had everything going for it – the variability of two telescopic booms, measuring 50 and 84 metres in length, was a unique selling point for the new crane. But right at the start of the development work, we were not really very pleased with the lifting capacity values in telescope mode. The increase compared to the LTM 1400 was rather disappointing.
Yggve Richter: At the time we were using a new calculation program which was significantly easier to use than the previous software package. Because of it, I was really motivated to do my absolute best. But I can remember something that our Technical Director, Dr. Hamme, said when I showed him the first tables at the time: “Yes, but the lifting capacities are not exactly impressive …”. That sent me back to my desk to improve the whole thing again!
By clicking on “ACCEPT”, you consent to the data transmission to Google for this video pursuant to Art. 6 para. 1 point a GDPR. If you do not want to consent to each YouTube video individually in the future and want to be able to load them without this blocker, you can also select “Always accept YouTube videos” and thus also consent to the respectively associated data transmissions to Google for all other YouTube videos that you will access on our website in the future.
You can withdraw given consents at any time with effect for the future and thus prevent the further transmission of your data by deselecting the respective service under “Miscellaneous services (optional)” in the settings (later also accessible via the “Privacy Settings” in the footer of our website).
For further information, please refer to our Data Protection Declaration and the Google Privacy Policy.*Google Ireland Limited, Gordon House, Barrow Street, Dublin 4, Ireland; parent company: Google LLC, 1600 Amphitheatre Parkway, Mountain View, CA 94043, USA** Note: The data transfer to the USA associated with the data transmission to Google takes place on the basis of the European Commission’s adequacy decision of 10 July 2023 (EU-U.S. Data Privacy Framework).The product management specification at the time said that the average annual sales would be around 15. We really did not expect to exceed this target so massively.
What were your demands and expectations?
Joachim Henkel: The LTM 1500 was planned to be the successor to the LTM 1400. With a 50 m telescopic boom and classic TA guying, at the time this was the benchmark and until then it was the best-selling 8-axle crane in the world. Naturally, we wanted to do even more with the new LTM 1500 to make it the best crane on the market in the 8-axle class. The product management specification at the time said that the average annual sales would be around 15. We really did not expect to exceed this target so massively.
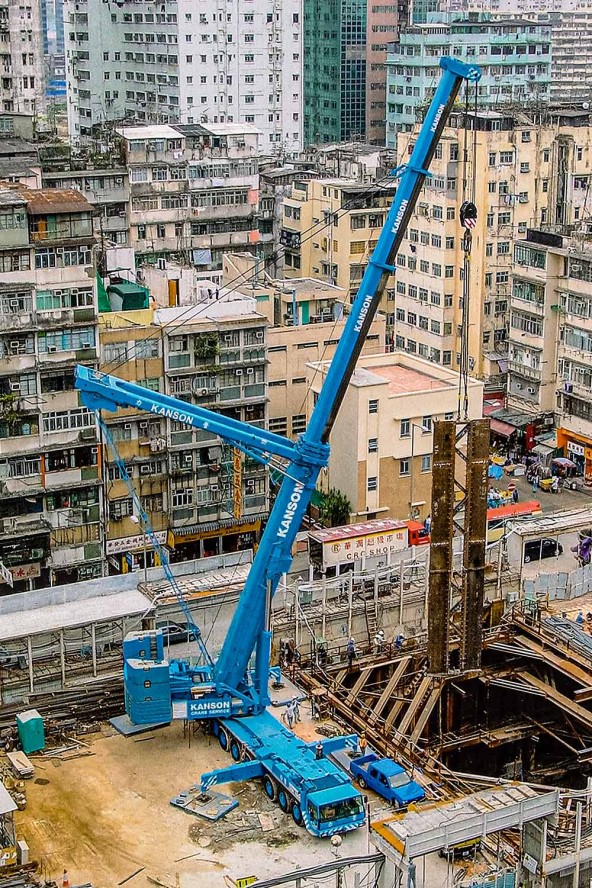
LTM 1500-8.1 with classic TA guying in Hong Kong
What were the challenges for the new 8-axle crane at the time?
Joachim Henkel: As I mentioned above, the two telescopic boom lengths were something special – 50 and 84 metres. And 84 metres at the time was a world record for a telescopic mobile crane! However, it was only possible because of the development of the new ovaloid boom concept. The predecessor LTM 1400 had a conventional rectangular cross-section with all sorts of buckling stiffeners in the boom to provide extra rigidity.
But buckling stiffeners require space and therefore prevent being able to retract lots of telescopic sections of adequate width into each other. The cross-sections of the telescopic sections in the LTM 1500 then required almost no buckling stiffeners. And it was this that meant we could build a 6-section boom with this enormous boom length, which also had good rigidity, particularly sideways.
However, we had no practical experience with this new type of telescopic boom. At the time we conducted an enormous number of FEM simulations to enable us to assess the boom’s strength. One FEM strength calculation for one telescopic boom section with one load case took around 18 hours, nowadays the computer does the same thing in 5 minutes.
Hans-Joachim Wenger: For the control system, too, the option of installing two different booms presented a whole new challenge. It meant that the control system, depending on which boom was installed, had to extend the 4 or 7-section boom to the required telescope length as effectively as possible and in the shortest possible time. The control options and visualisation then had to be included in the existing LICCON monitor to act as an interface to the crane operator.
Yggve Richter: In addition to mastering the lifting capacity calculation using the Y guying, the development of a calculation method for the strength assessment for the various telescopic sections proved to be the biggest challenge. The 6-section boom would have enabled 4,096 theoretical extension state combinations. Even with the new software package, we quickly reached the limits of what we could do.
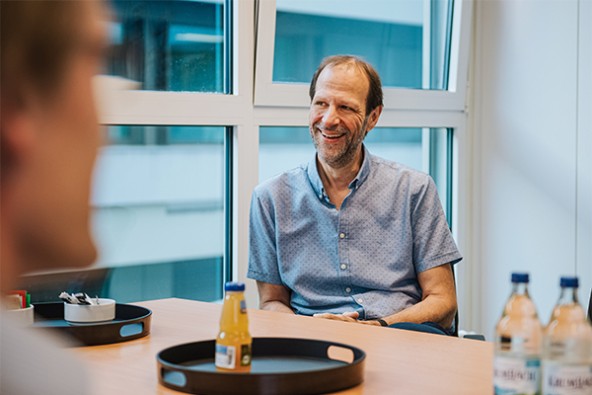
Hans-Joachim Wenger, Control Systems
Hans-Joachim Wenger: This enormous number of possible extension states, combined with the various possible accessories (luffing jib, fixed jib, hydraulic luffing fixed jib, guying with eccentric and spacer) meant that the number of tables required for the whole thing increased exponentially. This posed some major challenges to our colleagues at LML Development relating to storage capacity, management and processing for limiting the load moment.
Initially, we used the TA telescopic boom guying system which had been commonly used until then. Then came the spatial Y-guying. When exactly did that happen?
Yggve Richter: My first table is dated 27 September 2001.
Joachim Henkel: The LTM 1500 actually did not really take off until after we had developed the Y guying system. This enabled the lifting capacities to be increased dramatically even with high boom lengths, particularly when combined with lattice sections.
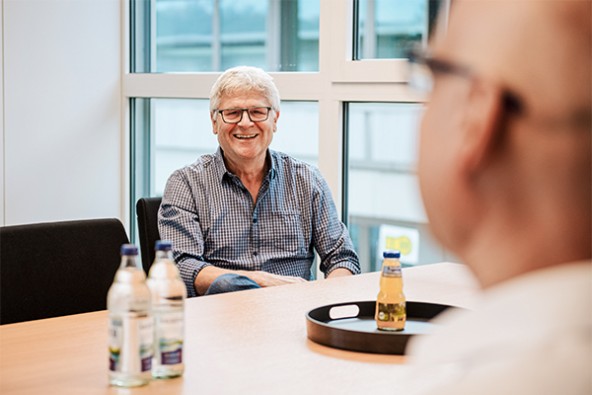
Norbert Leuze, Design
What was new about the Y-guying system?
Norbert Leuze: The TA guying system could only support loads in the longitudinal direction, so it prevented the boom buckling forwards. The Y-guying system also supports side loads, so it also prevents buckling to the side and can therefore hoist heavier loads. The lateral adjustment of the Y-guying supports enables the ideal guying angle to be achieved for the boom length and crane set-up.
What was the design challenge?
Norbert Leuze: Like TA-guying, it had to be possible to install the new system on the boom with as few hoists as possible. Furthermore, it must not exceed the vehicle width since in some countries the guying is carried on the crane when travelling on the road.
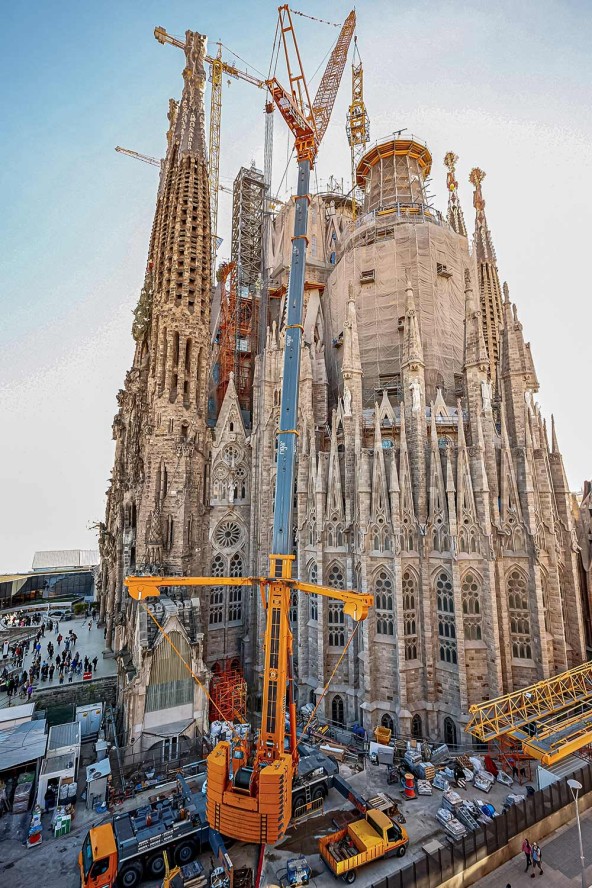
LTM 1500-8.1 erected tower cranes on the Sagrada Familia in Barcelona using Y-guying
And just like the old system, the guying had to be mechanically locked after it had been tensioned. This was achieved using teeth on the guard plate on the winch.
However, there was also the fact that it still had to be possible to slew the guying supports sideways. These studies took an immense amount of time. Since we had to check everything in spatial terms, it would have been almost impossible without 3-D CAD.
What does the new system mean for the control system and sensors?
Hans-Joachim Wenger: The new guying principle developed at the time, with a tensioning winch on each side of the boom and hydraulically controlled pawl and lowering cylinders required a massive number of sensors and actors. As automatic functions were now required for opening the pawl and for the actual lowering process, we had to place as many of the controls as possible in the LICCON. We managed to implement the controls and visualisation on the second LICCON monitor in the crane operator’s cab.
That was a really exciting time for me. In addition to the general crane controls, I was also responsible for programming the displays and controls in the LICCON monitor and PLC control system for the remote control lowering system. The collaboration between departments was absolutely fantastic.
This guying system also provided the basis for future, ever more refined guying methods for our current large telescopic cranes.
How complicated were the new structural calculations?
Yggve Richter: We first had to gain some experience with the new guying system. That meant that we conducted an enormous number of measurements on the test site. The preload forces with specific loads were measured and compared to the forces that we had calculated. It quickly became apparent that some of the differences were significant. As a result of this, we had to introduce tolerances, which meant that we had to calculate the boom strength four times. That took four times as long.
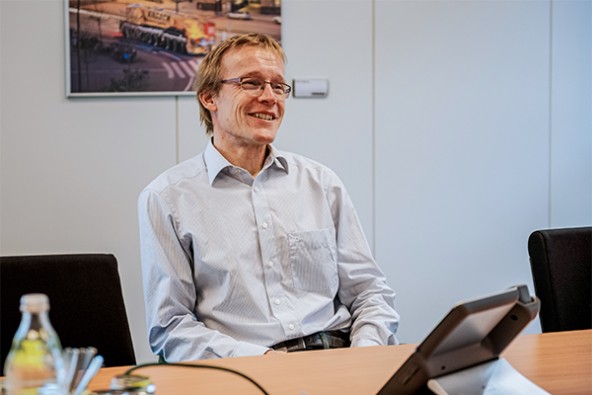
Yggve Richter, Structural Engineering
What other new features were created during the crane’s service life which related to the structural engineering?
Yggve Richter: The launch of the Spacer from 2002 gave the Y guying in TYN mode, in other words with a luffing jib and lowered boom, a real boost!
Norbert Leuze: In 2004 we also developed an Eccentric specially for TYF mode, in other words with a fixed jib and guying, to increase the lifting capacities even further.
Joachim Henkel: A combination of both systems has been standard on all Liebherr cranes with Y guying ever since. That meant the LTM 1500-8.1 was a real technology pioneer and we learnt an enormous amount.
Mr Richter, can you estimate how many hours of your life you spent working on the LTM 1500?
Yggve Richter laughs: No, I can’t. There were other projects as well of course. But every so often I found myself creating special tables for the 1500. That meant I was working on it fulltime for five or six years.
Are you currently still working on the LTM 1500-8.1?
Yes, I am still doing between two and three hours a week on it. That mainly involves “wind enquiries”. Customers want to hoist loads with large areas exposed to the wind, which would result in very low maximum wind speeds being possible on the basis of the standard conversion which customers can do for themselves. If we enter the special cases into our program, we can generally enable them to operate in significantly higher maximum wind speeds. I have answered more than 1,200 enquiries of this type since 2000.
After more than 20 years, the LTM 1500-8.1 is to be replaced by the new LTM 1650-8.1. Why do you believe the LTM 1500-8.1 was so successful and what goes through your head at the end of the life of such a successful crane?
Joachim Henkel: The first thing, of course, is the crane’s performance data and also its flexibility and mobility. But the very important thing is that we were constantly developing it, driven in particular by the boom in the wind industry. And we also managed to satisfy some exotic customer wishes, which over time became selling points for other customers. We did almost nothing wrong with this crane.
This article was published in the UpLoad magazine 01 | 2020.